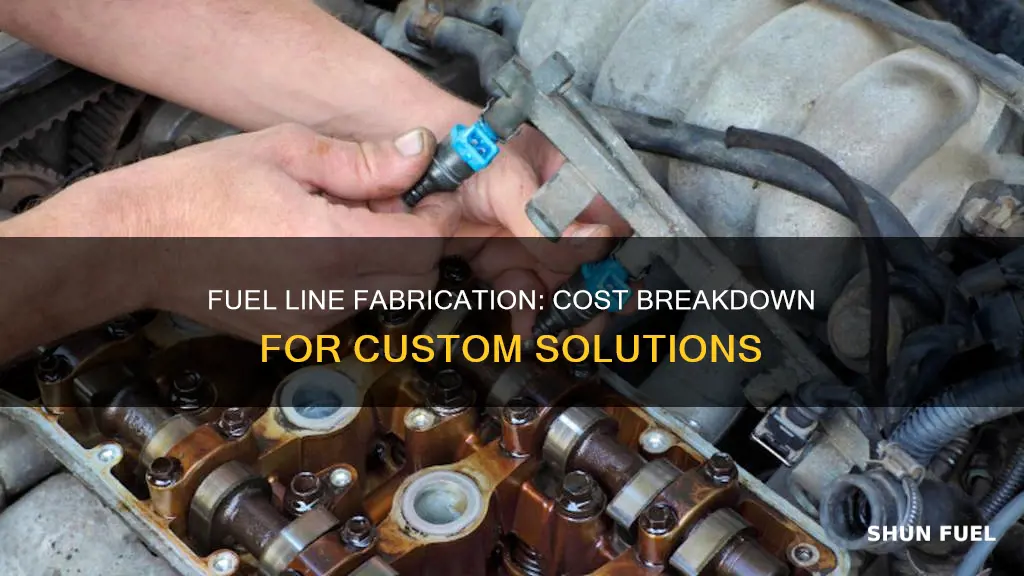
Fuel lines are an essential component of any vehicle's fuel system, and their manufacturing process can vary widely in terms of cost. The price of having fuel lines made depends on several factors, including the type of material used, the length and diameter of the lines, the complexity of the design, and the manufacturing method. For instance, stainless steel fuel lines might be more expensive due to their durability and resistance to corrosion, while aluminum lines could be lighter and less costly. Additionally, custom-made fuel lines for specialized vehicles or racing applications will typically incur higher costs compared to standard replacement lines. Understanding these variables is crucial for anyone looking to replace or upgrade their vehicle's fuel lines, ensuring they make an informed decision based on their budget and specific requirements.
What You'll Learn
- Material Costs: Compare prices of different materials for fuel lines
- Manufacturing Techniques: Explore various methods to estimate production costs
- Labor Expenses: Determine the cost of skilled labor for fuel line fabrication
- Overhead Expenses: Include rent, utilities, and other operational costs in the total
- Quality Control: Assess the impact of quality checks on fuel line production costs
Material Costs: Compare prices of different materials for fuel lines
When it comes to the cost of manufacturing fuel lines, the choice of material is a critical factor that significantly influences the overall expense. Different materials offer varying levels of durability, flexibility, and resistance to fuel-related chemicals, each with its own price tag. Here's a breakdown of the material costs associated with fuel lines:
- Rubber (Natural or Synthetic): Rubber is a traditional and widely used material for fuel lines due to its flexibility and resistance to most fuels. Natural rubber, sourced from rubber trees, is known for its superior flexibility and durability. However, it can be more expensive, especially when sourced from high-quality, sustainable plantations. Synthetic rubber, on the other hand, is often more cost-effective and offers similar performance characteristics. The price range for rubber fuel lines can vary, with natural rubber typically costing more, ranging from $2 to $5 per foot, depending on the thickness and quality. Synthetic rubber lines might be slightly more affordable, with prices around $1.50 to $3 per foot.
- PVC (Polyvinyl Chloride): PVC is a popular choice for fuel lines due to its affordability and ease of installation. It is lightweight, flexible, and resistant to most fuels, making it a cost-effective option. The cost of PVC fuel lines is generally lower compared to rubber. You can expect to pay around $1 to $2.50 per foot for PVC lines, with prices varying based on the gauge and thickness. This material is often used for smaller fuel lines and applications where flexibility is essential.
- Stainless Steel: For high-performance applications or in environments with extreme temperatures, stainless steel fuel lines are an excellent choice. This material offers superior durability, resistance to corrosion, and a long service life. While it is more expensive, the investment is justified in critical applications. Stainless steel fuel lines typically cost between $5 to $10 per foot, depending on the gauge and length. The higher cost is due to the material's premium properties and the manufacturing process involved.
- Braided Steel or Copper: Braided steel or copper fuel lines are often used for high-pressure applications or in racing environments. These materials provide excellent flexibility and resistance to fuel-related chemicals. Braided steel lines are known for their durability and can withstand extreme conditions. Copper lines, while less common, offer superior conductivity and corrosion resistance. The cost of these materials is higher, with braided steel lines ranging from $8 to $15 per foot, and copper lines being even more expensive, often costing $12 to $20 per foot or more.
When comparing prices, it's essential to consider the specific requirements of your fuel line project. Factors such as length, diameter, and the need for specialized coatings or reinforcements will impact the overall cost. Additionally, purchasing from reputable suppliers who offer high-quality materials can ensure better performance and longevity, even if it means a slightly higher initial investment.
Rubber Hose Fuel Line Lubrication: Essential Tips for Smooth Operation
You may want to see also
Manufacturing Techniques: Explore various methods to estimate production costs
When it comes to estimating the cost of manufacturing fuel lines, several manufacturing techniques and methods can be employed to ensure accuracy and efficiency. Here's an exploration of these techniques:
- Bill of Materials (BOM) Analysis: This is a fundamental step in any manufacturing process. Creating a detailed Bill of Materials involves listing all the components and raw materials required to produce the fuel lines. Each item should be specified, including its quantity, unit of measurement, and any unique identifiers. For instance, you might need to consider the type of fuel line material (such as stainless steel, aluminum, or plastic), the diameter and length of the fuel lines, fittings, connectors, and any specialized coatings or treatments. By breaking down the components, you can easily estimate the cost of each material and then calculate the total production cost.
- Process Mapping and Value Stream Analysis: Visualizing the manufacturing process is crucial. Create a process map that outlines the steps involved in producing the fuel lines, from raw material input to the final product. This map should include all operations, such as cutting, bending, welding, assembly, and quality control. Value Stream Analysis can then be applied to identify and eliminate waste in the process. By studying the flow of materials and information, you can optimize the production sequence, reduce unnecessary steps, and identify areas where costs can be minimized. This methodical approach ensures that every aspect of the manufacturing process is considered, allowing for a more accurate cost estimation.
- Direct Labor Cost Estimation: Labor costs are a significant portion of the overall production expense. To estimate direct labor costs, you need to consider the skills and experience of the workforce involved. Different manufacturing techniques may require specialized labor, such as experienced machinists for precision cutting or engineers for complex assembly. Calculate the labor hours required for each production step and multiply it by the hourly wage of the respective workers. Additionally, consider the overhead costs associated with labor, such as training, supervision, and employee benefits. This detailed breakdown will provide a realistic estimate of the labor-related expenses.
- Machine and Equipment Usage: Manufacturing fuel lines often involves the use of specialized machinery and equipment. To estimate production costs, you should account for the usage of these tools. Calculate the cost of operating and maintaining the machines, including energy consumption, wear and tear, and any required service contracts. Consider the time each machine takes to complete its respective tasks and the overall production time. By allocating costs to the specific equipment used, you can accurately reflect the expenses associated with the manufacturing process.
- Quality Control and Inspection: Ensuring product quality is essential, and it often comes at a cost. Implement a quality control system that includes inspections at various stages of production. This may involve purchasing specialized testing equipment, hiring additional personnel for inspections, or conducting third-party audits. By estimating the costs related to quality assurance, you can factor in the expenses associated with maintaining high-quality standards. This approach ensures that the final product meets the required specifications and reduces potential costs associated with product recalls or customer dissatisfaction.
Chevy Fuel Tank: Understanding the Lines and Connections
You may want to see also
Labor Expenses: Determine the cost of skilled labor for fuel line fabrication
When it comes to the cost of having fuel lines made, labor expenses are a significant factor. Skilled labor is essential for the precise and safe fabrication of fuel lines, ensuring they meet industry standards and regulations. The cost of labor can vary depending on several factors, including the complexity of the design, the materials used, and the location of the fabrication facility.
Labor costs typically include the wages of experienced technicians or engineers who specialize in fuel system design and manufacturing. These professionals possess the necessary skills to handle the intricate work involved in fabricating fuel lines, ensuring they are free of defects and meet the required specifications. Their expertise is crucial in maintaining the integrity of the fuel system, especially in critical applications such as automotive or aviation industries.
The process of fuel line fabrication involves several steps, each requiring specific skills and attention to detail. These steps may include cutting, bending, soldering, and welding the fuel lines to the desired specifications. Skilled labor is required to ensure accurate measurements, precise connections, and the ability to identify and rectify any potential issues during the fabrication process. This level of expertise is often more costly but is essential to guarantee the quality and safety of the final product.
In addition to wages, labor expenses may also encompass other costs associated with skilled labor. This can include training and development programs to keep technicians and engineers up-to-date with the latest industry standards and techniques. Providing a safe and efficient working environment, along with the necessary tools and equipment, is also a part of the labor cost. These factors contribute to the overall expense of skilled labor, which is a critical component in determining the total cost of fuel line fabrication.
Determining the exact labor costs can be complex and may require input from industry experts or consultants. It is essential to consider the specific requirements of the project, the complexity of the fuel lines, and the labor market conditions in your region. Obtaining quotes from multiple fabrication facilities and comparing their labor rates can provide a more accurate estimate of the overall cost. This approach ensures that you receive a detailed breakdown of labor expenses, allowing for better financial planning and decision-making regarding the fabrication of fuel lines.
The Materials Behind the Fuel Lines: A Deep Dive
You may want to see also
Overhead Expenses: Include rent, utilities, and other operational costs in the total
When calculating the cost of manufacturing fuel lines, it's crucial to consider the overhead expenses that contribute to the overall financial burden of the production process. Overhead expenses encompass various fixed costs that are incurred regardless of the volume of fuel lines produced. These expenses are essential to account for when determining the profitability and sustainability of the manufacturing operation.
Rent is a significant overhead expense, as it represents the cost of leasing or occupying the space where the fuel lines are produced. This includes the rent for the factory or workshop, as well as any additional costs associated with the facility, such as property taxes and maintenance fees. The size of the production space, the number of employees, and the specific requirements of the manufacturing process will influence the rent expense. For instance, a larger facility with specialized equipment may require a higher rent to accommodate the production needs.
Utilities, such as electricity, water, and gas, are another critical component of overhead expenses. These costs are necessary to power the machinery, provide water for cleaning and cooling processes, and maintain the overall functionality of the production facility. The utility expenses can vary depending on the energy consumption of the equipment, the duration of production hours, and the efficiency of the machinery. It is essential to factor in these costs to ensure that the production operation remains viable and cost-effective.
In addition to rent and utilities, other operational costs should be considered. These may include salaries and wages for the workforce, including both skilled and unskilled labor. The cost of hiring and retaining employees, providing training, and ensuring their well-being is an essential aspect of overhead expenses. Furthermore, expenses related to maintenance and repairs of machinery, tools, and equipment should be accounted for. This includes regular servicing, replacements, and any unexpected breakdowns that may occur during the production process.
By including these overhead expenses in the total cost calculation, manufacturers can gain a comprehensive understanding of the financial implications of producing fuel lines. It allows for better financial planning, budgeting, and decision-making. Moreover, it ensures that the production process remains sustainable and profitable, even when considering the fixed costs associated with the operation.
Fuel Line Clog Symptoms: Engine Issues Revealed
You may want to see also
Quality Control: Assess the impact of quality checks on fuel line production costs
Quality control is an essential aspect of fuel line manufacturing, as it directly impacts the cost and reliability of the final product. The process involves rigorous inspections and tests to ensure that the fuel lines meet the required standards and specifications. By implementing effective quality control measures, manufacturers can minimize the risk of defects, reduce waste, and ultimately lower production costs.
One of the key elements of quality control is the selection of appropriate testing methods. Manufacturers should employ a combination of visual inspections, dimensional measurements, and material testing to assess the integrity of the fuel lines. Visual inspections can identify surface defects, such as scratches or bends, while dimensional measurements ensure that the lines conform to the specified dimensions. Material testing, including hardness and tensile strength tests, verifies the quality and suitability of the materials used. These tests should be conducted at various stages of production to catch any issues early on.
The frequency and scope of quality checks should be determined based on industry standards and the specific requirements of the fuel line application. For critical components or high-risk applications, more frequent and comprehensive inspections may be necessary. For instance, in the aerospace industry, where fuel lines are subject to extreme conditions, quality control protocols might include non-destructive testing methods like ultrasonic or radiographic inspections to detect internal flaws. By investing in thorough quality checks, manufacturers can identify potential issues before they become costly problems, reducing the need for expensive rework or product recalls.
Additionally, implementing a robust quality control system can help streamline the production process. Automated inspection systems and computer-aided design (CAD) software can enhance accuracy and efficiency. These tools enable manufacturers to quickly identify deviations from the design specifications and make necessary adjustments. By minimizing human error and maximizing process efficiency, production costs can be optimized without compromising quality.
In summary, quality control plays a vital role in fuel line production by ensuring that the final product meets the required standards and specifications. Through the use of appropriate testing methods, frequent inspections, and advanced technologies, manufacturers can minimize defects, reduce waste, and ultimately lower production costs. Effective quality control not only ensures the reliability of fuel lines but also contributes to the overall success and competitiveness of the manufacturing process.
Unveiling the Car Fuel Line: Visual Guide
You may want to see also
Frequently asked questions
The cost of custom fuel lines can vary significantly depending on several factors. Firstly, the material used plays a crucial role; common choices include stainless steel, aluminum, or brass, each with different price points. Stainless steel, for instance, is more expensive but highly durable and resistant to corrosion. The length and complexity of the fuel lines also impact the price; longer lines or those with intricate bends and fittings will generally be more costly. Additionally, the manufacturing process and the supplier's location can influence the final cost. It's recommended to get quotes from multiple manufacturers to find the best value for your specific requirements.
Yes, installation costs can vary depending on the complexity of the job and the expertise required. Simple fuel line replacements might be manageable for DIY enthusiasts, but more intricate installations, especially in high-performance vehicles or custom builds, often require professional help. Labor costs can range from $50 to $100 per hour, and for complex projects, multiple hours might be needed. It's essential to consider these installation fees when budgeting to ensure a proper and safe fuel system setup.
Providing specific details is essential for an accurate quote. However, you can request a general estimate by describing your project. For example, you could mention the type of vehicle, the desired material, and any unique requirements. Manufacturers often use these details to provide a preliminary quote, which can then be refined with more specific information. This approach allows you to get an idea of the potential costs without revealing all your project's secrets.
Turnaround times can vary widely depending on the manufacturer's capacity, the complexity of the design, and the quantity required. For simple, standard fuel lines, production might take a few days to a week. However, custom-made lines with intricate designs or specialized materials could take several weeks. Some manufacturers offer expedited services for an additional fee, which can significantly reduce the waiting time. It's advisable to inquire about lead times when requesting quotes to plan your project accordingly.