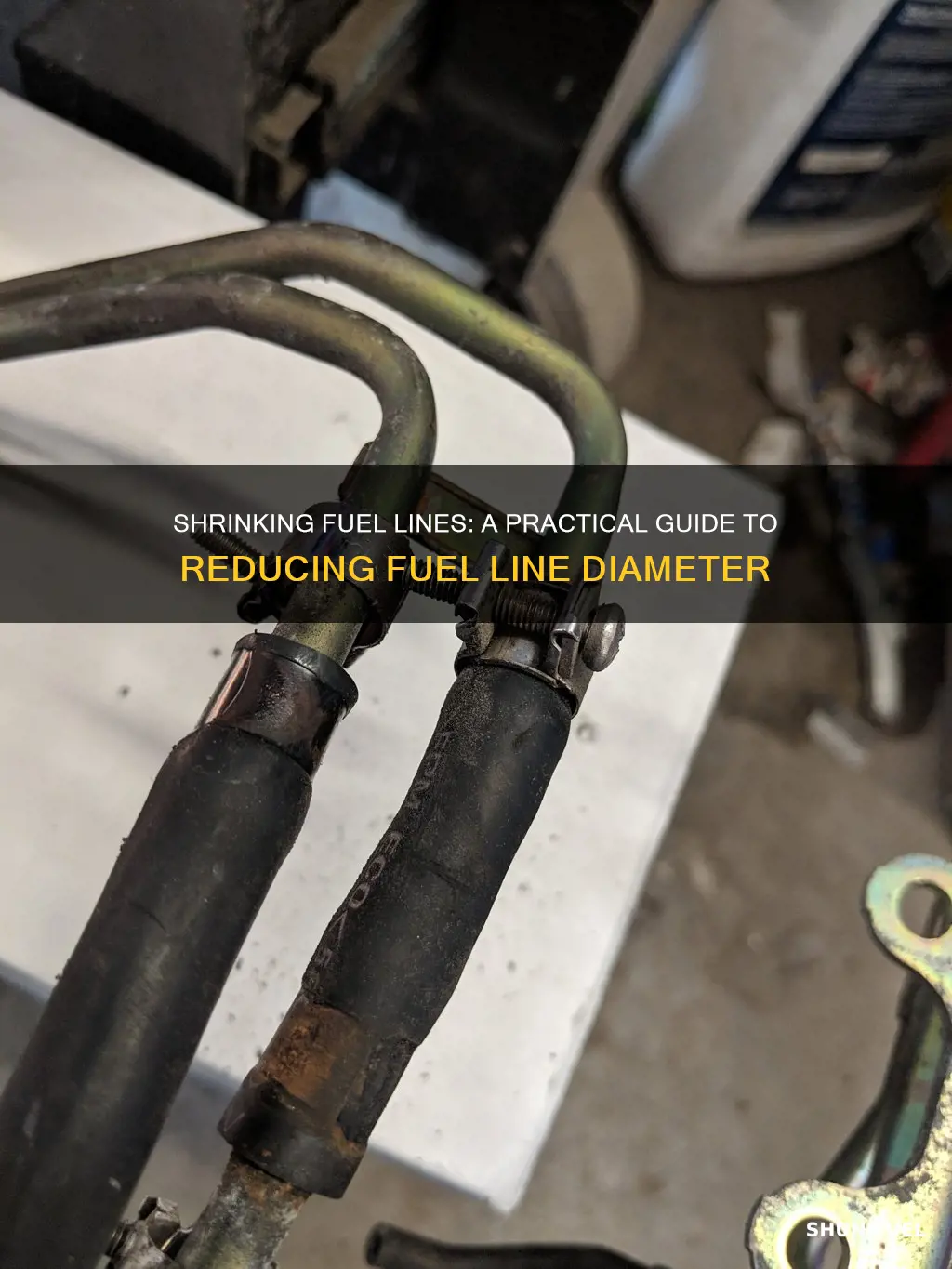
Fuel lines play a crucial role in delivering fuel from the tank to the engine, but sometimes they can become damaged or worn over time. One common question that arises is whether it's possible to shrink a fuel line to fix any leaks or fit it into a tighter space. While it's not a typical or recommended solution, some enthusiasts and DIYers might consider shrinking a fuel line as a temporary fix. However, it's important to note that attempting to shrink a fuel line can be dangerous and may lead to reduced performance, fuel leaks, or even engine damage. Proper maintenance and professional repairs are generally the best approach to ensure the safety and efficiency of your vehicle's fuel system.
What You'll Learn
- Materials and Design: Exploring materials and design choices to reduce fuel line size
- Flow Rate and Pressure: Analyzing the impact of flow rate and pressure on fuel line diameter
- Flexibility and Durability: Evaluating the need for flexibility and durability in smaller fuel lines
- Vacuum and Suction: Understanding the role of vacuum and suction in fuel line shrinking
- Safety and Regulations: Discussing safety standards and regulations for fuel line size reduction
Materials and Design: Exploring materials and design choices to reduce fuel line size
The concept of shrinking fuel lines is an intriguing approach to optimizing fuel delivery systems, especially in the context of automotive engineering and performance enhancements. This exploration delves into the materials and design considerations that can contribute to achieving smaller fuel lines without compromising efficiency and reliability.
One key aspect is the utilization of advanced materials. Modern fuel lines can be crafted from high-performance polymers, such as fluoropolymers or specialized polyolefins. These materials offer excellent chemical resistance, ensuring they can withstand various fuels and operating temperatures. For instance, perfluoroalkoxy (PFA) or polytetrafluoroethylene (PTFE) can provide superior durability and flexibility, allowing for the creation of smaller-diameter fuel lines without sacrificing performance. The reduced size can be achieved by optimizing the material's properties, such as adjusting the durometer (hardness) to balance flexibility and strength.
Design optimization plays a crucial role in minimizing fuel line dimensions. Engineers can employ computer-aided design (CAD) software to model and simulate fuel line configurations. By analyzing fluid flow characteristics, pressure differentials, and potential stress points, designers can identify areas for improvement. One strategy is to incorporate braided or spiral-wound structures, which provide enhanced flexibility and reduced diameter. These designs can efficiently manage fuel flow while maintaining structural integrity, even in tight spaces. Additionally, considering the fuel line's routing and placement within the vehicle can further contribute to space optimization.
Another design consideration is the integration of fuel injectors or pumps directly into the fuel line. This approach, known as in-line fuel injection, eliminates the need for separate fuel rails or distribution systems, thereby reducing overall system complexity and size. By minimizing connections and interfaces, the risk of leaks and pressure drops is decreased, ensuring efficient fuel delivery. Furthermore, the use of precision-engineered components, such as micro-pumps or injectors, can further contribute to the overall compactness of the fuel system.
In summary, shrinking fuel lines requires a meticulous approach to materials and design. By employing advanced polymers and innovative structural designs, engineers can achieve smaller fuel lines without compromising performance. This exploration highlights the potential for significant space savings in fuel delivery systems, contributing to more compact vehicle designs and improved overall efficiency.
Air Filter Clog: A Hidden Fuel Line Filter Problem
You may want to see also
Flow Rate and Pressure: Analyzing the impact of flow rate and pressure on fuel line diameter
The relationship between flow rate, pressure, and fuel line diameter is a critical aspect of fuel system design and optimization. When considering the 'can you shrink a fuel line' question, it's essential to understand how these factors interact to ensure efficient and reliable fuel delivery.
Flow rate, essentially the volume of fuel passing through a line per unit of time, directly influences the required diameter of the fuel line. Higher flow rates necessitate larger diameters to accommodate the increased volume of fuel without causing excessive pressure drops. This is because a smaller diameter would lead to higher velocities, potentially causing turbulence and reduced efficiency. The optimal diameter is determined by the specific flow rate requirements of the engine and the desired pressure maintenance throughout the fuel system.
Pressure plays a pivotal role in this context as well. Fuel lines must be designed to withstand the pressure generated by the fuel pump and the engine's operation. If the line's diameter is too small, the pressure drop across it can become significant, leading to inadequate fuel supply and potential performance issues. Engineers aim to minimize pressure losses by selecting an appropriate diameter that balances flow rate requirements and pressure considerations.
To analyze the impact of flow rate and pressure, engineers employ various calculations and simulations. These methods help determine the minimum diameter required for a fuel line to handle a specific flow rate while maintaining acceptable pressure levels. By considering factors such as fuel viscosity, temperature, and pump characteristics, designers can optimize the fuel line's diameter to ensure efficient and reliable fuel delivery.
In summary, when addressing the 'can you shrink a fuel line' query, it is crucial to recognize that the diameter of the fuel line is intricately linked to flow rate and pressure. Engineers must carefully consider these factors to design fuel systems that meet performance requirements while ensuring optimal fuel delivery and system efficiency. This analysis is fundamental in the design process to guarantee the reliability and safety of fuel-powered systems.
Unclogging a VW Bug's Fuel Line: A Step-by-Step Guide
You may want to see also
Flexibility and Durability: Evaluating the need for flexibility and durability in smaller fuel lines
When considering the design and installation of smaller fuel lines, flexibility and durability are crucial factors that cannot be overlooked. These lines are often used in tight spaces and may need to accommodate various movements and vibrations, especially in high-performance vehicles or applications with limited engine compartments. The need for flexibility arises from the requirement to navigate around obstacles and maintain a secure connection without restricting the engine's performance.
Flexibility is essential to ensure that the fuel lines can adapt to the vehicle's natural movements during operation. Engines experience thermal expansion and contraction, and the fuel lines must be able to move with the engine block without causing excessive stress or damage. This is particularly important in high-performance applications where engines operate at extreme temperatures and pressures. By allowing the fuel lines to flex, you can prevent cracks, leaks, and potential engine damage caused by rigid lines that cannot accommodate these changes.
Durability is another critical aspect, as fuel lines must withstand the harsh conditions within an engine bay. These lines are exposed to high temperatures, fuel pressure, and mechanical stress. The materials used should be able to resist corrosion, abrasion, and the degradation caused by fuel additives. High-quality, reinforced rubber or synthetic materials are often employed to ensure the lines can handle the demanding environment. Additionally, the construction of the fuel lines, including the reinforcement of critical areas, is vital to their longevity.
In smaller fuel lines, achieving the right balance between flexibility and durability is essential. While flexibility ensures the lines can navigate through tight spaces and move with the engine, durability prevents premature failure and potential fuel leaks. Designers and engineers must carefully select materials and construction methods that provide the necessary flexibility without compromising strength. This evaluation process involves considering the specific requirements of the application, including the type of fuel, operating temperatures, and the overall design of the fuel system.
In summary, when dealing with smaller fuel lines, it is imperative to prioritize flexibility and durability. These lines must be able to navigate through confined spaces while withstanding the extreme conditions within an engine bay. By carefully selecting materials and construction techniques, engineers can create fuel lines that offer the required flexibility without sacrificing the necessary durability, ensuring reliable and safe fuel delivery in various automotive applications.
Supercharge Your Chainsaw: Exploring Enhanced Fuel Line Options
You may want to see also
Vacuum and Suction: Understanding the role of vacuum and suction in fuel line shrinking
The concept of shrinking fuel lines is an intriguing one, especially in the context of automotive repairs and modifications. While it might seem counterintuitive to reduce the size of a fuel line, there are specific scenarios where this technique can be beneficial. One such method involves the use of vacuum and suction, which plays a crucial role in this process.
When attempting to shrink a fuel line, creating a vacuum or applying suction is a strategic approach. This technique is particularly useful when dealing with fuel lines that have expanded or become loose over time due to temperature changes or wear and tear. By generating a vacuum, you essentially pull the fuel line's walls inward, reducing its diameter. This process can be achieved using specialized equipment, such as a vacuum pump or a suction device designed for this purpose. The vacuum creates a force that draws the fuel line's material together, effectively shrinking it.
The key to success with this method lies in understanding the fuel line's material properties. Different materials have varying levels of flexibility and elasticity. For instance, rubber fuel lines might respond better to suction compared to rigid metal lines. It's essential to consider the fuel line's composition to determine the most effective shrinking technique. Additionally, the application of suction should be gentle and controlled to avoid causing damage to the fuel line or the surrounding components.
In practice, a mechanic or enthusiast might use a vacuum pump to create a controlled environment, slowly reducing the fuel line's size. This process requires precision and patience, ensuring that the fuel line is not damaged during the shrinking process. Once the desired reduction is achieved, the fuel line can be carefully secured in its new, shrunk state. This technique is often employed in fuel system upgrades or repairs, allowing for improved fuel flow and potentially enhancing engine performance.
Mastering the art of shrinking fuel lines using vacuum and suction requires practice and a keen understanding of the fuel system's intricacies. It is a specialized skill that can be invaluable for those working on high-performance engines or unique vehicle modifications. By harnessing the power of suction, one can effectively reshape fuel lines, ensuring optimal performance and a professional finish.
Upgrade Your Ride: A Guide to Swapping Steel Fuel Lines for Nylon
You may want to see also
Safety and Regulations: Discussing safety standards and regulations for fuel line size reduction
When considering the reduction of fuel line size, it is crucial to prioritize safety and adhere to established regulations. Fuel lines play a critical role in the transportation of flammable substances, and any modifications or reductions in size must be approached with caution to ensure compliance with industry standards.
Safety standards for fuel lines are stringent and are designed to mitigate the risks associated with fuel handling. These standards often specify minimum diameter requirements for fuel lines to ensure adequate flow rates and pressure capacity. Reducing the size of a fuel line below these minimum standards can lead to several safety concerns. Firstly, it may result in a decrease in the line's ability to handle the intended fuel volume, potentially causing pressure buildup and an increased risk of fuel line failure. This could lead to fuel leaks, which, in the presence of ignition sources, pose a significant fire hazard.
Regulations governing fuel line dimensions are typically outlined in industry guidelines and standards, such as those set by the Society of Automotive Engineers (SAE) or the American Petroleum Institute (API). These standards provide specific requirements for fuel line materials, construction, and testing to ensure reliability and safety. For instance, the SAE J1728 standard offers guidelines for fuel line sizing, taking into account factors like fuel type, operating temperature, and pressure. Adhering to these regulations is essential to guarantee that the fuel system functions safely and efficiently.
In some cases, fuel line reduction might be necessary due to space constraints or design modifications. However, any such changes must be carefully evaluated and justified. It is imperative to consult with experts and ensure that alternative solutions, such as using higher-pressure fuel systems or implementing additional safety measures, are considered to maintain the required performance and safety levels.
Furthermore, when working with fuel lines, it is essential to follow proper installation and maintenance procedures. This includes using appropriate tools, ensuring secure connections, and regularly inspecting the lines for any signs of wear or damage. Proper training and adherence to manufacturer guidelines are vital to minimizing the risks associated with fuel line reduction and ensuring the overall safety of the fuel system.
2005 Nissan Murano Fuel Line: Location and Access
You may want to see also
Frequently asked questions
While it is possible to shrink a fuel line to a certain extent, it is not a recommended or reliable method for ensuring a proper fit. Fuel lines are designed to withstand specific dimensions and pressure, and attempting to shrink them may lead to reduced performance, potential leaks, or even damage to the engine. It is best to use the correct size fuel line specified for your engine to ensure optimal functionality and safety.
Adjusting the size of a fuel line without shrinking it involves considering alternative solutions. One approach is to use a fuel line with a larger diameter that can be cut to the desired length. This method allows for a more precise fit and ensures the line can handle the required fuel flow. Another option is to explore fuel line adapters or fittings that can accommodate different sizes, providing a flexible solution for engine modifications.
No, it is not advisable to permanently reduce the size of a fuel line. Fuel lines are typically made of materials that can be temporarily compressed or reshaped but will not retain their new shape permanently. Attempting to permanently shrink a fuel line may result in a loss of flexibility, reduced fuel flow, and potential engine performance issues. It is always best to consult a professional or refer to the manufacturer's guidelines for proper fuel line installation and sizing.