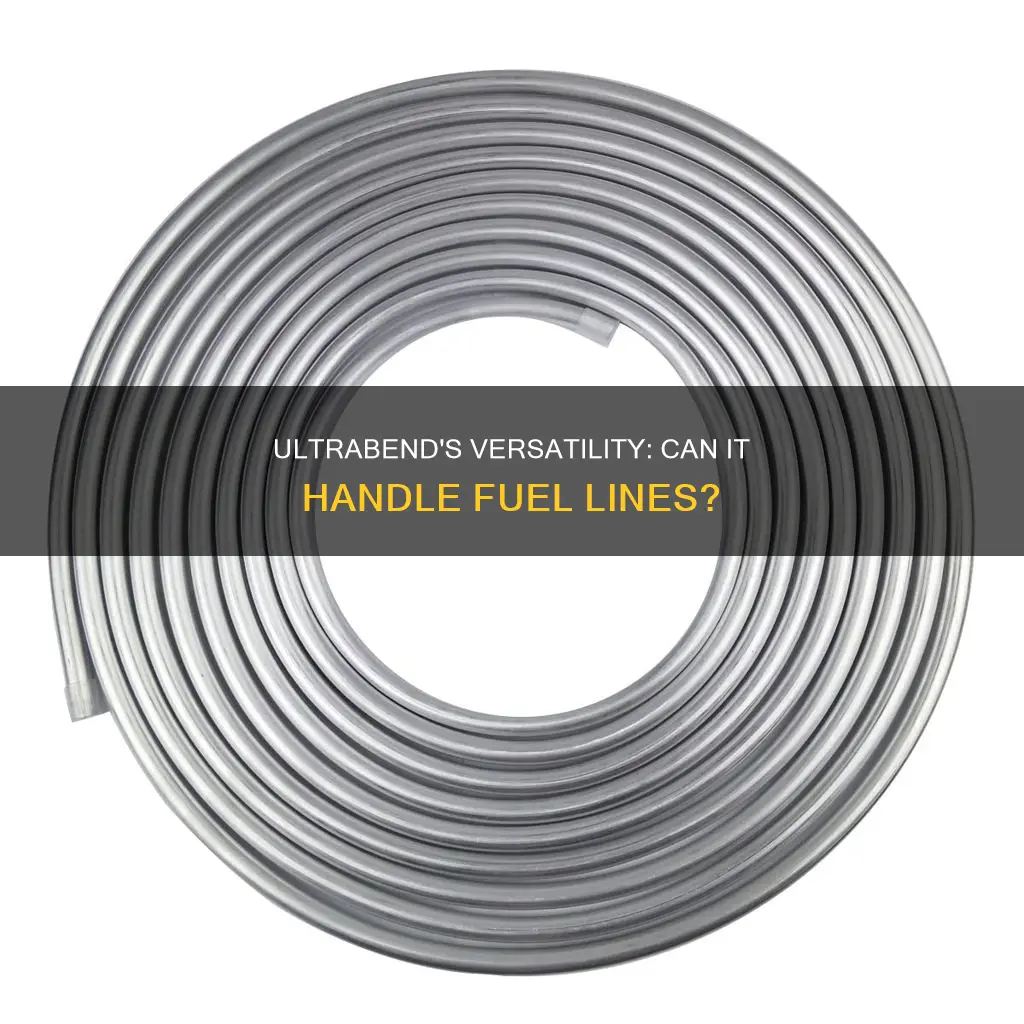
Ultrabend brake line tubing is a popular choice for automotive enthusiasts due to its durability and flexibility. However, when it comes to fuel lines, there are specific considerations to keep in mind. While Ultrabend can be used for fuel lines, it's important to note that it may not be the best option due to its potential for corrosion and the risk of fuel leaks over time. This paragraph introduces the topic by highlighting the suitability of Ultrabend for brake lines but also raises the need for careful evaluation when considering it for fuel lines.
What You'll Learn
- Compatibility: Check if ultrabend brake line tubing is compatible with fuel line requirements
- Material Strength: Assess if ultrabend can withstand fuel pressure and temperature
- Flexibility: Evaluate if ultrabend's flexibility meets fuel line bending needs
- Corrosion Resistance: Ensure ultrabend resists corrosion from fuel chemicals
- Installation: Verify if ultrabend can be easily installed as fuel lines
Compatibility: Check if ultrabend brake line tubing is compatible with fuel line requirements
When considering the use of ultrabend brake line tubing for fuel lines, it is crucial to evaluate its compatibility with the specific requirements of fuel systems. While ultrabend tubing is known for its durability and flexibility, ensuring its suitability for fuel lines is essential to prevent potential issues.
One critical aspect of compatibility is the material composition of the ultrabend tubing. Fuel lines often require materials that are resistant to fuel degradation, such as ozone and UV radiation. If the ultrabend tubing does not meet these criteria, it may degrade over time, leading to fuel leaks or contamination. Manufacturers typically provide detailed specifications regarding the tubing's resistance to various chemicals and environmental factors, including fuel compatibility. It is imperative to review these specifications to ensure the tubing can withstand the corrosive nature of fuels.
Another factor to consider is the pressure rating of the ultrabend tubing. Fuel lines operate under varying pressure conditions, and the tubing must be able to withstand these pressures without compromising its structural integrity. The pressure rating of ultrabend tubing should be compared against the minimum and maximum pressure requirements of the fuel system to ensure compatibility. Insufficient pressure rating could result in tubing failure, potentially causing fuel leaks or system malfunctions.
Additionally, the flexibility and bend radius of ultrabend tubing should be assessed. Fuel lines often require tubing that can navigate through tight spaces and bends in the vehicle's engine compartment. If the ultrabend tubing has a bend radius that is too stiff or a flexibility that is not adequate for the fuel line's route, it may lead to installation challenges or potential damage to the tubing. Therefore, it is essential to consider the physical constraints of the fuel line installation and choose tubing with suitable flexibility and bend characteristics.
Lastly, consulting the manufacturer's guidelines and industry standards is vital. Reputable manufacturers often provide comprehensive instructions and recommendations for using their products in specific applications. These guidelines can offer valuable insights into the compatibility of ultrabend tubing with fuel lines, ensuring proper installation and long-term performance. Adhering to these standards can help prevent potential issues and ensure the safety and reliability of the fuel system.
Nylon Fuel Line: Top Sources for Purchase
You may want to see also
Material Strength: Assess if ultrabend can withstand fuel pressure and temperature
The use of ultrabend brake line tubing for fuel lines is an interesting concept, especially given its reputation for durability and flexibility. However, when considering its application in fuel systems, the material's strength and ability to withstand specific conditions become crucial factors.
Ultrabend, known for its high-performance characteristics, is primarily designed for brake lines due to its exceptional tensile strength and resistance to abrasion. It is engineered to handle the rigorous demands of braking systems, including high-pressure environments and rapid temperature fluctuations. This makes it an ideal candidate for applications requiring robust and reliable performance.
In the context of fuel lines, the material's strength must be evaluated under the unique stresses of fuel pressure and temperature variations. Fuel systems operate at varying pressures, especially during acceleration and deceleration, and temperatures can fluctuate significantly, especially in high-performance vehicles. Ultrabend's ability to maintain its structural integrity under these conditions is essential to ensure the safety and efficiency of the fuel delivery system.
To assess its suitability, one must consider the material's yield strength and its resistance to deformation under pressure. Ultrabend's composition and manufacturing process should be examined to understand its ability to withstand the corrosive effects of fuels and the mechanical stresses associated with fuel line operation. Additionally, its temperature resistance, including its ability to retain flexibility and prevent cracking, is vital for long-term performance.
While ultrabend brake line tubing offers impressive characteristics, a comprehensive analysis of its material properties and performance in fuel line applications is necessary. This includes laboratory testing and real-world data to ensure it meets the specific requirements of fuel systems, providing both safety and reliability.
Optimizing Performance: Choosing the Right Fuel Line for Your 1992 Johnson 115 V4 Outboard
You may want to see also
Flexibility: Evaluate if ultrabend's flexibility meets fuel line bending needs
When considering the use of ultrabend brake line tubing for fuel lines, one of the critical factors to evaluate is flexibility. Fuel lines often require a certain level of flexibility to accommodate the natural movement and expansion of the engine components during operation. The tubing must be able to bend and twist without kinking or becoming rigid, which could lead to fuel flow issues and potential damage to the engine.
Ultrabend tubing is known for its exceptional flexibility, which is a result of its unique construction and material properties. The tubing is designed with a high degree of pliability, allowing it to conform to various shapes and angles. This flexibility is particularly advantageous in fuel line applications where the tubing needs to navigate through tight spaces, around engine components, and potentially under the vehicle's body.
To assess if ultrabend tubing meets the flexibility requirements for fuel lines, consider the following: First, examine the tubing's bend radius. Fuel lines often require tight bends to fit the engine's layout, so a smaller bend radius is essential. Ultrabend tubing should be able to bend sharply without compromising its structural integrity. Second, evaluate the tubing's ability to withstand repeated bending without becoming brittle or losing its flexibility over time. This is crucial for long-term performance and durability.
Additionally, the flexibility of ultrabend tubing should be tested under various temperatures and environmental conditions. Fuel lines are exposed to extreme temperatures, so the tubing must remain flexible and pliable even in sub-zero or scorching conditions. This ensures that the fuel lines can maintain their functionality and integrity throughout the vehicle's operating range.
In summary, the flexibility of ultrabend brake line tubing is a key consideration when determining its suitability for fuel lines. Its ability to bend, twist, and conform to different shapes is essential for accommodating the engine's movement and navigating through tight spaces. By evaluating the tubing's bend radius, durability, and temperature flexibility, you can ensure that it meets the specific requirements of fuel line applications, providing reliable and safe performance.
Foxbody Fuel Line Placement: A Step-by-Step Guide to Carburetor Fueling
You may want to see also
Corrosion Resistance: Ensure ultrabend resists corrosion from fuel chemicals
When considering the use of ultrabend brake line tubing for fuel lines, one crucial aspect to evaluate is its corrosion resistance, especially when exposed to the various chemicals present in fuel. Corrosion can lead to degradation of the material, potentially causing leaks, reduced performance, and even safety hazards. Therefore, it is essential to understand the material's ability to withstand the corrosive effects of fuel.
Ultrabend, known for its durability and versatility, is generally composed of high-quality materials that offer excellent resistance to corrosion. The specific composition of ultrabend can vary, but it often includes a combination of steel, copper, or aluminum alloys, which are inherently resistant to corrosion. These materials form a protective layer on the surface, known as a patina, which prevents further corrosion and protects the underlying metal.
In the context of fuel lines, the presence of various chemicals, such as ethanol, methanol, and additives, can pose a significant challenge. These chemicals can accelerate corrosion, leading to premature failure of the tubing. However, ultrabend's corrosion-resistant properties make it a suitable choice for this application. The material's ability to resist corrosion ensures that it can withstand the harsh environment of fuel systems, maintaining its structural integrity over time.
To ensure optimal performance and longevity, it is recommended to choose ultrabend tubing with a protective coating or plating. This additional layer can further enhance its corrosion resistance, especially in high-temperature and high-pressure environments. Common coatings include zinc plating or a specialized polymer coating, which act as barriers against corrosive elements.
In summary, when using ultrabend brake line tubing for fuel lines, its corrosion resistance is a critical factor to consider. The material's inherent properties, combined with additional protective measures, ensure that it can effectively resist the corrosive effects of fuel chemicals, providing a reliable and safe solution for fuel line applications. Proper selection and installation of ultrabend tubing will contribute to the overall performance and longevity of the fuel system.
Can Fuel Line Returns Use Plastic T-Fittings? Expert Insights Revealed
You may want to see also
Installation: Verify if ultrabend can be easily installed as fuel lines
When considering the use of Ultrabend brake line tubing for fuel lines, it's crucial to evaluate its installation process. Ultrabend is known for its flexibility and durability, making it a suitable candidate for fuel line applications. However, the ease of installation is a critical factor to ensure a successful and safe setup.
The installation process for Ultrabend brake line tubing is generally straightforward and user-friendly. It is designed with a smooth interior surface, allowing for easy bending and routing. This flexibility is advantageous when navigating through tight spaces or complex engine compartments. The tubing's durability also ensures that it can withstand the challenges of fuel line applications, including potential vibrations and temperature fluctuations.
To verify the ease of installation, one should consider the following steps. Firstly, ensure that the Ultrabend tubing is cut to the appropriate length, allowing for sufficient slack to work with. Then, use the appropriate tools, such as a tubing bender or a pair of pliers, to shape the tubing as needed. The smooth surface of Ultrabend makes it relatively simple to bend and manipulate, ensuring a secure fit. It is essential to follow the manufacturer's guidelines for bending angles and techniques to avoid damage to the tubing.
Additionally, the installation process should include the use of appropriate connectors and fittings. Ultrabend offers a range of compatible connectors designed specifically for fuel line applications. These connectors are typically easy to attach and provide a reliable seal, ensuring a secure connection. It is recommended to use high-quality fuel line connectors to guarantee the safety and longevity of the fuel system.
In summary, Ultrabend brake line tubing can be easily installed as fuel lines due to its flexibility and durability. The installation process involves cutting the tubing to size, using appropriate bending tools, and attaching compatible connectors. By following these steps and adhering to the manufacturer's instructions, one can ensure a successful and secure fuel line setup, taking advantage of Ultrabend's reliable performance in demanding automotive applications.
Can Fuel Lines Be Used as Vacuum Lines?
You may want to see also
Frequently asked questions
Yes, Ultrabend brake line tubing is an excellent choice for fuel lines due to its superior flexibility, durability, and resistance to fuel-related chemicals. It is designed to withstand the rigorous demands of automotive applications, making it a reliable option for fuel delivery systems.
Ultrabend tubing is crafted from high-quality materials, ensuring it can handle the unique challenges of fuel transportation. Its braiding pattern provides flexibility, allowing it to navigate through tight spaces in the engine compartment. Additionally, the tubing's inner diameter and wall thickness are optimized for efficient fuel flow while maintaining structural integrity.
Absolutely! Ultrabend is specifically engineered to perform in high-pressure environments, making it ideal for fuel lines that require precise control and efficient fuel delivery. Its ability to resist expansion and contraction under pressure ensures a reliable and safe fuel system.
The material used in Ultrabend tubing is carefully selected to resist fuel-related degradation. It is resistant to common fuels' chemicals, ensuring long-term reliability. This material also provides excellent flexibility, making it easy to install and route within the vehicle's confines.