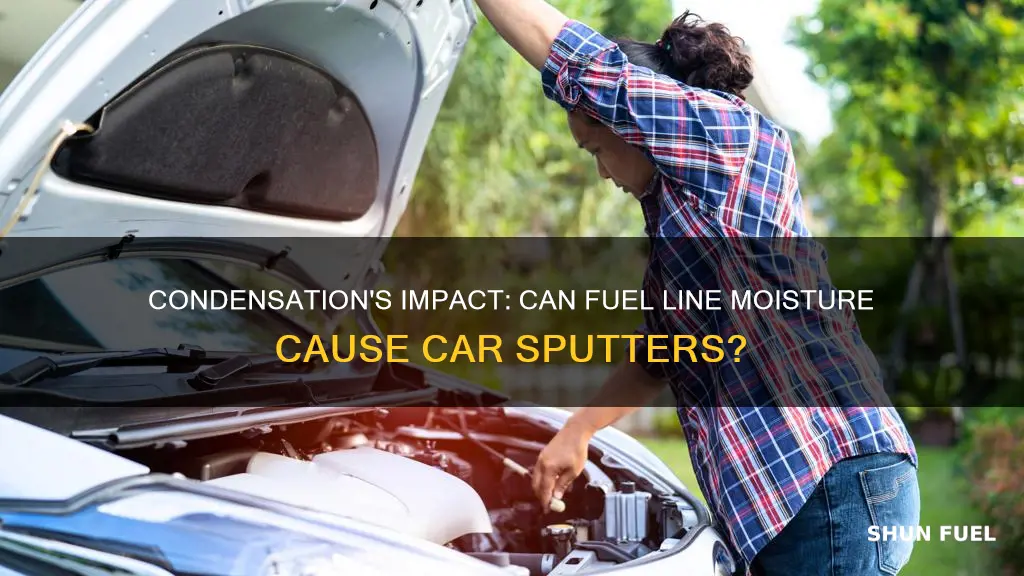
Condensation in the fuel line can be a common issue for car owners, especially during colder months. When water vapor in the air condenses into liquid water inside the fuel line, it can lead to a variety of problems, including engine sputtering. This occurs because the condensed water can block the flow of fuel to the engine, causing it to run poorly or even stall. Understanding the causes and effects of condensation in the fuel line is crucial for maintaining a reliable vehicle and ensuring a smooth driving experience.
Characteristics | Values |
---|---|
Condensation in Fuel Line | Yes |
Car Sputtering | Yes |
Possible Causes | Condensation can form in the fuel line due to temperature changes, especially when the engine is turned off and the fuel cools down. |
Symptoms | Engine misfires, poor fuel efficiency, stalling, and reduced power. |
Solutions | Remove the fuel line and replace it with a new one, or use a fuel line heater to prevent condensation. Regularly check for and address any fuel system issues. |
Precaution | Driving in humid conditions or during winter can increase the risk of condensation. |
What You'll Learn
- Condensation and Fuel Line Clogging: Moisture buildup can block fuel flow, leading to engine sputtering
- Fuel Line Material: Different materials react differently to condensation, affecting performance
- Engine Temperature: Higher temperatures can reduce condensation, but extreme heat may damage fuel lines
- Fuel Pump Impact: Condensation can affect fuel pump operation, causing sputtering and reduced power
- Maintenance and Inspection: Regular checks can prevent condensation-related issues and ensure engine reliability
Condensation and Fuel Line Clogging: Moisture buildup can block fuel flow, leading to engine sputtering
The presence of condensation in the fuel lines of a vehicle can indeed lead to engine sputtering, a common issue that many car owners face. This phenomenon occurs due to the accumulation of moisture within the fuel system, which can cause a range of performance problems. When condensation forms in the fuel lines, it often results from temperature changes, especially during the transition from cold to warm weather or when driving through varying altitudes. As the engine warms up, the fuel lines expand, and any moisture present begins to condense, forming small droplets that can block the flow of fuel to the engine.
Moisture in the fuel system is a significant concern because it can lead to fuel line clogging. Over time, the condensed water can accumulate and create a blockage, restricting the smooth flow of fuel. This disruption in fuel supply directly impacts the engine's performance, causing it to sputter and stall. The engine may lose power, and the vehicle might hesitate or decelerate unexpectedly, posing a potential safety hazard.
Several factors contribute to the development of condensation and subsequent clogging in fuel lines. Firstly, the design of the fuel system plays a role; older vehicles with less sophisticated fuel systems may be more susceptible. Additionally, the quality of the fuel itself can impact moisture content. Poor-quality fuel or fuel that has been stored for extended periods can contain higher levels of water, increasing the likelihood of condensation. Regular maintenance, including fuel system inspections and the use of fuel stabilizers, can help mitigate these issues.
To address condensation and fuel line clogging, several solutions are available. One effective method is to use a fuel additive designed to reduce moisture content. These additives can help prevent condensation by maintaining a dry environment within the fuel system. Regularly checking and replacing the fuel filter is also crucial, as it can trap moisture and contaminants, ensuring cleaner fuel delivery. In some cases, a professional fuel system flush may be necessary to remove accumulated moisture and debris.
In summary, condensation in fuel lines, often caused by temperature changes, can lead to engine sputtering and performance issues. Moisture buildup blocks fuel flow, resulting in potential safety hazards. Understanding the causes and implementing preventive measures, such as using fuel additives and regular maintenance, can help car owners avoid this common problem. Being proactive in managing fuel system moisture will contribute to a more reliable and efficient vehicle.
Metal Fuel Tank Rust: Liner's Role Revealed
You may want to see also
Fuel Line Material: Different materials react differently to condensation, affecting performance
The presence of condensation in fuel lines can indeed have a significant impact on a vehicle's performance, and the material of the fuel line plays a crucial role in this phenomenon. Different materials exhibit varying levels of susceptibility to condensation, which can lead to sputtering and other engine issues.
One common material used in fuel lines is rubber. Rubber is a flexible and durable option, often chosen for its ability to withstand the harsh conditions inside an engine compartment. However, rubber fuel lines can be prone to absorbing moisture from the air. When condensation forms in the fuel line, the rubber material may swell and restrict the flow of fuel, leading to reduced performance. This can result in a sputtering engine, especially during acceleration or when the engine is under load. To mitigate this issue, rubber fuel lines are often designed with a protective coating or a braided reinforcement to minimize the absorption of moisture.
In contrast, fuel lines made from materials like steel or aluminum are generally more resistant to condensation-related problems. These metals have lower permeability to moisture, meaning they are less likely to absorb water from the fuel or the surrounding environment. As a result, steel or aluminum fuel lines are less susceptible to swelling or distortion when exposed to condensation. This property makes them a preferred choice for high-performance vehicles or applications where fuel line durability is critical.
Another factor to consider is the design and construction of the fuel line. Some fuel lines are designed with a double-walled or braided structure, which helps to reduce the risk of condensation-related issues. These designs often use a flexible inner tube surrounded by a protective layer, ensuring that the fuel remains isolated from the moisture in the air. By minimizing direct contact between the fuel and the surrounding environment, these designs can effectively prevent condensation-induced performance problems.
In summary, the material and construction of fuel lines are essential considerations when addressing the impact of condensation. Rubber fuel lines may require additional measures to prevent swelling and subsequent performance issues, while metal or specially designed fuel lines offer better resistance to condensation. Understanding these material properties and design considerations is vital for maintaining a vehicle's optimal performance and ensuring a reliable driving experience.
Engine's Strange Noises: When Fuel Line Issues Speak
You may want to see also
Engine Temperature: Higher temperatures can reduce condensation, but extreme heat may damage fuel lines
The relationship between engine temperature and condensation in fuel lines is a critical aspect of vehicle maintenance. Higher temperatures play a significant role in mitigating condensation-related issues. When the engine operates at elevated temperatures, the fuel lines are less prone to condensation formation. This is because heat helps to vaporize any moisture that might have entered the fuel system, preventing it from condensing into liquid droplets. As a result, the risk of fuel line blockages and subsequent engine sputtering is significantly reduced.
However, it's essential to strike a balance. While higher temperatures are beneficial, extreme heat can also have detrimental effects on the fuel system. Prolonged exposure to excessive temperatures may lead to fuel line damage. The fuel lines, often made of rubber or similar flexible materials, can degrade over time when subjected to high heat. This degradation can result in cracks, leaks, or even the failure of the fuel lines, causing fuel to leak and potentially leading to engine performance issues.
To ensure optimal engine performance, it is recommended to maintain a moderate operating temperature. This can be achieved by monitoring the engine's temperature gauge and taking appropriate measures to cool it down if it becomes too hot. Regularly checking for any signs of fuel line damage, such as leaks or cracks, is also crucial. If any issues are detected, prompt action should be taken to repair or replace the affected fuel lines.
In colder climates, where temperatures drop significantly, condensation becomes a more prominent concern. During these conditions, it is advisable to use fuel line inhibitors or fuel system treatments that can help prevent condensation and ice formation in the fuel lines. These products can be added to the fuel tank to provide an extra layer of protection, ensuring that the fuel system remains in optimal condition.
In summary, engine temperature plays a crucial role in managing condensation in fuel lines. Higher temperatures help reduce condensation, but extreme heat should be avoided to prevent potential damage. By maintaining a balanced engine temperature and taking preventive measures, vehicle owners can minimize the risk of fuel line issues and ensure their cars run smoothly and efficiently.
Fuel Line Break: Engine Chaos Unveiled
You may want to see also
Fuel Pump Impact: Condensation can affect fuel pump operation, causing sputtering and reduced power
Condensation in the fuel line is a common issue that can have a significant impact on a vehicle's performance, particularly in relation to the fuel pump. When water vapor condenses within the fuel lines, it can lead to a variety of problems, with one of the most noticeable being engine sputtering and reduced power output. This phenomenon is often overlooked, but understanding its causes and effects is crucial for maintaining a vehicle's optimal performance.
The fuel pump is a critical component in the fuel delivery system, responsible for pumping fuel from the tank to the engine at the required pressure. When condensation occurs in the fuel lines, it can introduce water into the fuel stream, which then reaches the fuel pump. Water is not an ideal medium for the efficient operation of the fuel pump, as it can cause several issues. Firstly, water has a higher specific gravity than fuel, which means it will settle at the bottom of the fuel tank, potentially blocking the fuel pump's intake and causing it to run dry. This can result in the pump overheating and, in severe cases, permanent damage.
Moreover, the presence of water in the fuel can lead to the formation of ice crystals during cold weather, which can further block the fuel lines and pump. This is especially problematic as it can cause the engine to stall or sputter when starting, especially in colder climates. The water can also cause corrosion within the fuel system, including the pump, over time, leading to a decline in its performance and efficiency.
The impact of condensation on the fuel pump is twofold. Firstly, the water can cause mechanical issues, such as internal damage to the pump's components due to the corrosive nature of water. This can lead to a decrease in the pump's lifespan and, in some cases, complete failure, requiring expensive repairs or a replacement. Secondly, the water can affect the pump's ability to deliver fuel efficiently, resulting in reduced power output from the engine. This is because the water can cause air bubbles in the fuel, leading to inconsistent fuel-air mixture delivery, which is a common cause of engine sputtering.
To mitigate these issues, regular maintenance is essential. This includes checking the fuel tank for any signs of water accumulation and ensuring that the fuel system is properly sealed to prevent condensation. Using fuel additives that help separate water from the fuel can also be beneficial. In cases where condensation is already causing problems, a professional mechanic can advise on the best course of action, which may include replacing the fuel pump or addressing any corrosion issues. Understanding the relationship between condensation, fuel pumps, and engine performance is vital for vehicle owners to ensure their cars run smoothly and efficiently.
Snowmobile Fuel Line Sizing: A Comprehensive Guide
You may want to see also
Maintenance and Inspection: Regular checks can prevent condensation-related issues and ensure engine reliability
Condensation in the fuel line can indeed lead to various performance issues, including sputtering, and it's a problem that requires proactive maintenance and regular inspections to prevent. This is especially crucial for vehicles with fuel injection systems, where the fuel is directly injected into the engine's cylinders, and any disruption in the fuel supply can have immediate effects on the engine's operation.
Regular maintenance and inspections are key to identifying and addressing condensation-related problems before they cause significant damage. One of the primary steps is to ensure that the fuel system is properly sealed to prevent moisture from entering. This includes checking and replacing any damaged or worn-out gaskets, seals, and hoses that could allow condensation to form. Over time, fuel lines can develop small cracks or leaks, especially in older vehicles, and these issues can go unnoticed until they cause performance problems.
During routine maintenance, it's essential to inspect the fuel tank and lines for any signs of moisture. Condensation often appears as a white or milky substance inside the fuel tank or along the fuel lines. If you notice any such signs, it's crucial to address the issue promptly. One effective method is to use a fuel line drier, which can be installed in the fuel system to absorb moisture. These devices are particularly useful in preventing condensation, especially in climates with high humidity.
Additionally, regular engine maintenance, such as oil changes and filter replacements, can indirectly help prevent condensation-related issues. Keeping the engine in good condition ensures that it operates efficiently, reducing the likelihood of fuel-related problems. It's also beneficial to use a fuel stabilizer in the tank, especially for older vehicles or those stored for extended periods, to minimize the risk of condensation and fuel degradation.
In summary, regular maintenance and inspections are vital to preventing condensation-related issues in the fuel line. By ensuring the fuel system is properly sealed, inspecting for moisture, and implementing preventative measures, vehicle owners can maintain engine reliability and avoid costly repairs caused by condensation. Staying proactive with maintenance is the best way to keep these issues at bay.
The Ultimate Guide to Choosing the Right Hose Clamp for Your 3/8" Outboard Fuel Line
You may want to see also
Frequently asked questions
Yes, condensation in the fuel line can lead to engine issues, including sputtering. When water enters the fuel system, it can cause problems due to its corrosive nature and the potential for phase changes. Condensation often occurs when the fuel line is exposed to cooler temperatures, and the water vapor in the fuel can condense, leading to a mixture of water and fuel. This mixture can cause blockages, corrosion, and contamination, which may result in engine misfires, reduced performance, and sputtering.
Preventing condensation involves maintaining a consistent temperature in the fuel system. Here are some measures you can take:
- Use a fuel line insulator: Insulating the fuel line, especially if it's exposed to cold temperatures, can help maintain a steady temperature and reduce the chances of condensation.
- Keep the fuel tank full: When the tank is full, there's less air space, which can minimize the formation of condensation.
- Use a fuel additive: Certain fuel additives can help prevent water accumulation and keep the fuel system dry.
- Regularly check for leaks: Ensure your fuel system is intact and free from any leaks that could allow moisture to enter.
Identifying condensation in the fuel line early can help prevent further issues. Here are some indicators:
- Engine misfires or rough idling: Sputtering or inconsistent engine performance could be a sign of water in the fuel.
- Reduced fuel efficiency: Condensation can lead to poor fuel combustion, resulting in decreased fuel efficiency.
- Engine knocking or pinging: These sounds may indicate water in the cylinders, causing engine damage.
- Check the fuel filter: If the filter becomes clogged or dirty, it might be due to water contamination, indicating a potential issue with condensation.