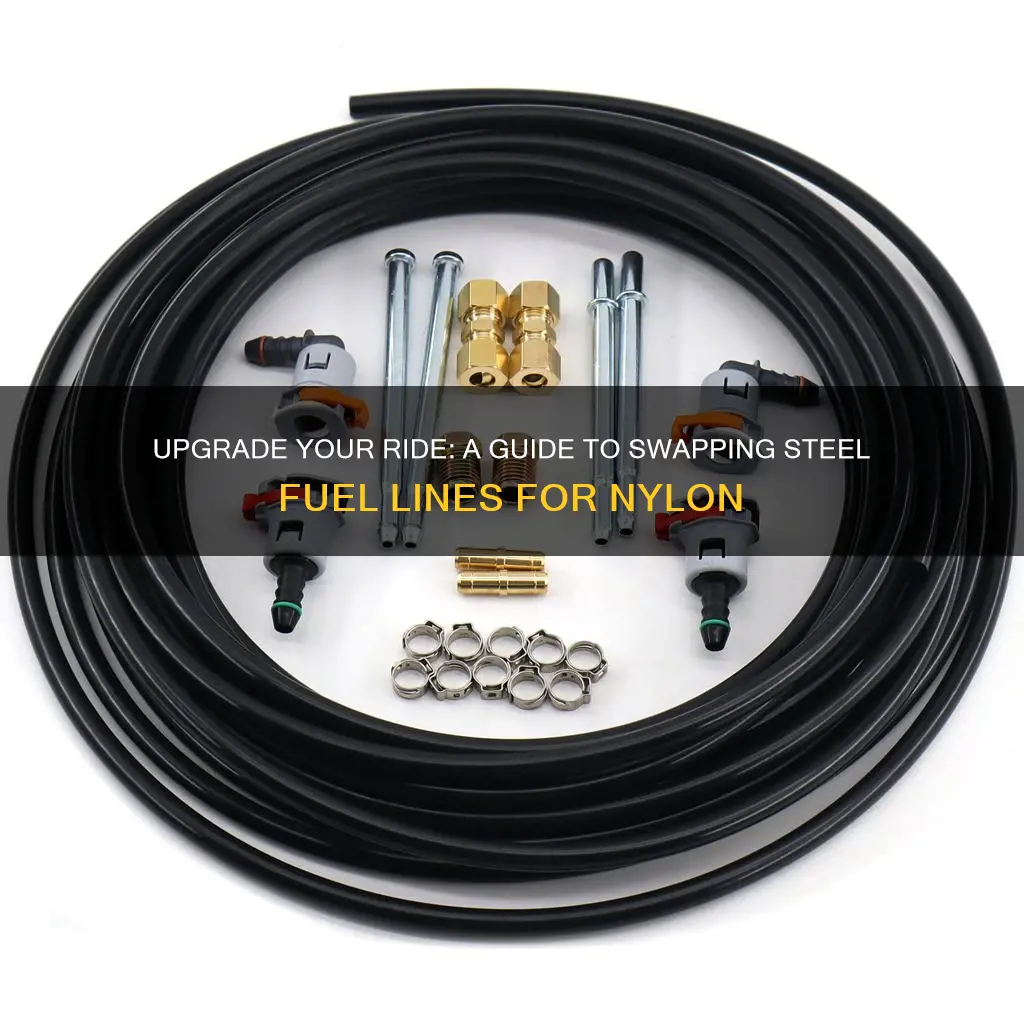
Replacing a steel fuel line with a nylon one is a common automotive repair that can improve the reliability and longevity of your vehicle's fuel system. Nylon fuel lines are known for their flexibility, resistance to heat and chemicals, and ability to withstand high pressure, making them an excellent alternative to steel. This guide will provide a step-by-step process for replacing the steel fuel line with a nylon replacement, ensuring a secure and efficient installation. By following these instructions, you can enhance the performance and safety of your vehicle's fuel delivery system.
Characteristics | Values |
---|---|
Material | Nylon |
Flexibility | High flexibility, allowing for easier installation and reduced risk of damage during vehicle movement |
Durability | Resistant to corrosion, abrasion, and temperature changes, ensuring long-lasting performance |
Temperature Range | Can withstand a wide range of temperatures, from -40°F to 250°F (-40°C to 121°C) |
Pressure Resistance | Capable of handling high fuel pressures commonly found in modern vehicles |
Compatibility | Compatible with various fuel types, including gasoline, diesel, and ethanol blends |
Installation | Often easier to install compared to steel lines due to its flexibility and reduced weight |
Cost | Generally more expensive than steel but offers long-term savings due to its durability and reduced maintenance needs |
Weight | Lighter than steel, contributing to improved fuel efficiency and reduced vehicle weight |
Noise | Less prone to rattling and noise generation, providing a quieter operation |
Availability | Widely available in various sizes and lengths, making it a popular choice for fuel line replacements |
What You'll Learn
- Preparation: Clean and inspect the fuel line, ensuring it's free of debris and damage
- Nylon Fuel Line: Choose a nylon fuel line with the correct diameter and length
- Clamps and Fittings: Select appropriate clamps and fittings for a secure connection
- Installation: Route the nylon line, connect to fuel source, and tighten clamps
- Testing: Check for leaks and ensure proper flow before final use
Preparation: Clean and inspect the fuel line, ensuring it's free of debris and damage
Before you begin the replacement process, it's crucial to ensure that the old fuel line is in optimal condition. Start by thoroughly cleaning the existing steel fuel line. This step is essential to remove any dirt, grime, or debris that might interfere with the installation of the new nylon line. Use a suitable cleaning agent, such as a fuel line cleaner, and a soft brush or cloth to scrub the line. Pay close attention to any bends or kinks in the line, as these areas may require extra cleaning to ensure a smooth transition for the new material. Rinse the line thoroughly with clean water to eliminate any cleaning agents and allow it to dry completely.
Once the cleaning is complete, inspect the fuel line for any signs of damage or wear. Look for cracks, corrosion, or any areas where the line has become brittle. Steel fuel lines can be susceptible to rust and degradation over time, especially in environments with high humidity or exposure to fuel contaminants. If you notice any damage, it's best to replace the entire line rather than just the section with the issue. Ensure that the fuel line is free from any sharp bends or kinks that could cause stress points for the new nylon replacement.
During the inspection, also check the connections and fittings. Make sure they are intact and secure. If there are any loose connections, tighten them appropriately. It's important to have a solid understanding of the fuel system's layout to ensure that the new nylon line is routed correctly and securely attached to the necessary components. This preparation step is vital to guarantee a successful and safe fuel line replacement.
Honda CH80 Fuel Line: Optimal Size for Peak Performance
You may want to see also
Nylon Fuel Line: Choose a nylon fuel line with the correct diameter and length
When replacing a steel fuel line with a nylon alternative, ensuring the correct specifications are met is crucial for a successful and safe installation. The first step is to carefully measure the existing fuel line to determine the necessary diameter and length. Nylon fuel lines are available in various sizes, so it's essential to choose the one that matches the original dimensions. Measure the inside diameter of the steel line, as this will dictate the size of the nylon replacement. Common diameters for fuel lines range from 3/8" to 1/2" inches, but always refer to the specific application's requirements.
Once you have the diameter, you can select the appropriate nylon fuel line. Nylon is known for its flexibility and durability, making it an excellent choice for fuel lines. Look for a nylon line with a similar wall thickness to the steel line to ensure it can withstand fuel pressure and temperature variations. The length of the nylon line should be slightly longer than the original steel line to allow for any adjustments during installation.
Consider the routing of the fuel line within the vehicle's engine bay. Nylon lines are generally more flexible than steel, so you might need to adjust the path to accommodate the new material. Ensure that the nylon line can reach the fuel source and the destination without being overly tight or restrictive.
It's important to note that nylon fuel lines may have different color-coding or marking systems compared to steel. Familiarize yourself with these markings to ensure you select the correct type of nylon line for your application. Always refer to the manufacturer's guidelines or consult a vehicle repair manual for specific recommendations regarding nylon fuel line replacements.
By carefully selecting the correct diameter and length of the nylon fuel line, you can ensure a proper fit and maintain the integrity of the fuel system. This process requires attention to detail and a good understanding of the vehicle's fuel line configuration. Proper installation will result in a reliable and efficient fuel supply system.
Finding the Perfect Fuel Line Fit for Your 2006 Scion TC
You may want to see also
Clamps and Fittings: Select appropriate clamps and fittings for a secure connection
When replacing a steel fuel line with a nylon alternative, ensuring a secure and reliable connection is crucial to maintain the integrity of your fuel system. The right clamps and fittings play a pivotal role in achieving this. Here's a comprehensive guide to selecting the appropriate components:
Understanding the Material: Nylon fuel lines offer enhanced flexibility and resistance to corrosion compared to steel. However, they may require specific fasteners to ensure a tight seal. Common types of clamps used for nylon lines include metal or plastic compression clamps, which apply pressure to the line and fitting, creating a secure bond. It's essential to choose clamps that match the diameter of your nylon fuel line to ensure a proper fit.
Clamp Types: There are various clamp styles available, each with unique advantages. For instance, a 'U' clamp is a popular choice, featuring a curved shape that wraps around the fuel line and fitting. These clamps are easy to install and provide a secure hold. Another option is the 'Slide-On' clamp, which slides over the fitting and line, offering a quick and efficient connection. Consider the ease of installation and the level of security provided by different clamp designs.
Fitting Selection: The choice of fittings is critical to the success of the replacement. Nylon fuel lines often require specialized fittings that are designed to work with this material. Look for fittings made from compatible materials, such as nylon or high-density polyethylene (HDPE), to ensure a seamless connection. Fittings should be designed to withstand fuel pressure and temperature fluctuations to guarantee long-term performance.
Consideration of Environment: The operating environment of your vehicle is a significant factor. If your vehicle is exposed to extreme temperatures or harsh conditions, select clamps and fittings with enhanced durability. For instance, in high-temperature environments, consider using clamps with a higher temperature rating to prevent degradation. Similarly, in corrosive environments, opt for clamps and fittings made from materials resistant to rust and corrosion.
Testing and Quality Assurance: Before finalizing your choice, ensure that the selected clamps and fittings undergo rigorous testing. Manufacturers often provide data sheets or specifications that detail the performance and compatibility of their products. Look for certifications or standards that guarantee the quality and reliability of the chosen fasteners. This step ensures that your fuel system meets the required safety and performance standards.
Outboard Fuel Line Clogs: Causes and Solutions
You may want to see also
Installation: Route the nylon line, connect to fuel source, and tighten clamps
When replacing a steel fuel line with a nylon one, the installation process requires careful planning and execution to ensure a secure and reliable connection. Here's a step-by-step guide to help you through the installation:
Routing the Nylon Line: Begin by carefully tracing the path of the old steel fuel line. This will help you determine the best route for the new nylon line. Nylon fuel lines are flexible and can be routed through the engine bay, but ensure you follow the manufacturer's guidelines for optimal placement. Consider the engine's layout, any obstructions, and the desired length of the line. Mark the starting and ending points, and measure the distance to ensure the nylon line is long enough for the replacement.
Preparation: Gather the necessary tools and materials, including the new nylon fuel line, fuel source adapter (if required), and appropriate clamps or fittings. Clean the area where the new line will be connected to remove any dirt or debris. Ensure the nylon line is free of any bends or kinks that could affect its performance.
Connection to Fuel Source: Locate the fuel source, which could be a fuel pump, tank, or another component. If an adapter is needed, attach it to the fuel source, ensuring a proper seal. Slide the nylon line through the adapter, if used, and connect it to the fuel source. Use a fuel line connector or clamp to secure the line, making sure it is tight and there is no play in the connection.
Tightening Clamps: Secure the nylon line with the appropriate clamps. Tighten the clamps firmly, but be careful not to overtighten, as this can damage the line. Ensure the clamps are positioned to provide a secure hold and prevent any movement or leakage. Check that the clamps are accessible for future maintenance and adjustments.
Final Checks: After completing the installation, start the engine and check for any leaks at the new nylon fuel line connections. Ensure that the line is functioning properly and that there is no fuel loss. Test the engine's performance and monitor for any unusual noises or vibrations. Properly dispose of the old steel fuel line and keep the installation area clean.
Remember, when working with fuel lines, it's crucial to follow safety guidelines and take necessary precautions to avoid fuel spills and ensure a successful replacement.
Mercury Outboard Fuel Line Removal: A Step-by-Step Guide
You may want to see also
Testing: Check for leaks and ensure proper flow before final use
Before finalizing the replacement of a steel fuel line with a nylon one, it is crucial to conduct thorough testing to ensure the system's integrity and functionality. This step is essential to prevent any potential issues and guarantee a safe and efficient fuel supply. Here's a detailed guide on how to approach this testing process:
Leak Detection: Start by inspecting the entire fuel line system for any signs of damage or imperfections. Use a soapy water solution as a leak detector. Apply a thin layer of this mixture along the length of the new nylon fuel line and the connections. Allow it to sit for a few minutes, then inspect the area. If there are any bubbles forming on the surface, it indicates a potential leak. If leaks are found, carefully re-evaluate the installation process and make the necessary adjustments to ensure a tight and secure fit. This step is critical to prevent fuel leakage, which can be dangerous and cause environmental damage.
Pressure Testing: Set up a pressure testing system to simulate real-world conditions. Attach a pressure gauge to the fuel line and gradually increase the pressure to a level that mimics the system's expected operating pressure. Monitor the gauge for any drops in pressure, which could indicate a leak. Ensure that the pressure is held stable for an extended period to confirm the integrity of the connection. This test is particularly important for fuel lines, as it helps identify any weak points that might fail under pressure, potentially causing fuel loss or system failure.
Flow Rate Assessment: Measure the flow rate of fuel through the new nylon line to ensure it meets the required specifications. Use a flow meter to accurately measure the volume of fuel passing through the line over a set period. Compare this with the expected flow rate for the specific fuel type and system design. Proper flow ensures that the engine receives the necessary fuel supply without wastage or performance issues. Adjustments might be necessary to optimize the flow, especially if the nylon line has a different diameter or internal surface characteristics compared to the steel line.
Visual Inspection: After the initial testing, perform a visual inspection of the entire system. Look for any signs of distortion, kinks, or unusual wear on the nylon fuel line. Ensure that all connections are secure and free from damage. This visual check is essential to identify any potential issues that might not be apparent during the leak or pressure tests. It provides a comprehensive assessment of the system's overall health and readiness for final use.
By following these testing procedures, you can confidently ensure that the replacement of the steel fuel line with nylon is secure, leak-free, and capable of handling the required fuel flow. This meticulous approach to testing is vital for maintaining the safety and performance of the fuel system in various applications.
Stihl BR600 Fuel Line Hose: Unlocking the Secrets
You may want to see also
Frequently asked questions
Nylon fuel lines offer several advantages over steel, including flexibility, durability, and resistance to corrosion and fuel degradation. They are often used in high-performance vehicles or classic car restoration projects where the original steel lines may be worn out or incompatible with modern fuels.
While it is possible to replace a fuel line as a DIY project, it is highly recommended to have some mechanical experience and knowledge. Working with fuel lines requires careful handling to avoid spills and potential fire hazards. It's best to follow detailed guides or seek professional assistance to ensure a safe and correct installation.
Selecting the appropriate nylon fuel line depends on various factors. Consider the vehicle's make and model, the original line's specifications, and the desired performance. Nylon lines come in different diameters and lengths, so measuring the existing line or consulting a vehicle-specific diagram is essential. Additionally, ensure the line is compatible with the fuel type and pressure requirements.
Yes, you'll require a few specialized tools for the job. These may include a fuel line cutter or shears, a fuel line adapter or reducer (if needed), crimping tools for the fittings, and possibly a fuel line cleaner or solvent. Having the right tools will ensure a clean and secure connection between the new nylon line and the fuel system components.
Steel fuel lines can become brittle over time, leading to cracks or leaks, especially when exposed to fuel vapors and temperature changes. This can result in fuel leaks, engine misfires, or even fire hazards. Replacing steel lines with nylon is a preventive measure to avoid potential engine damage and ensure the vehicle's safety and performance.