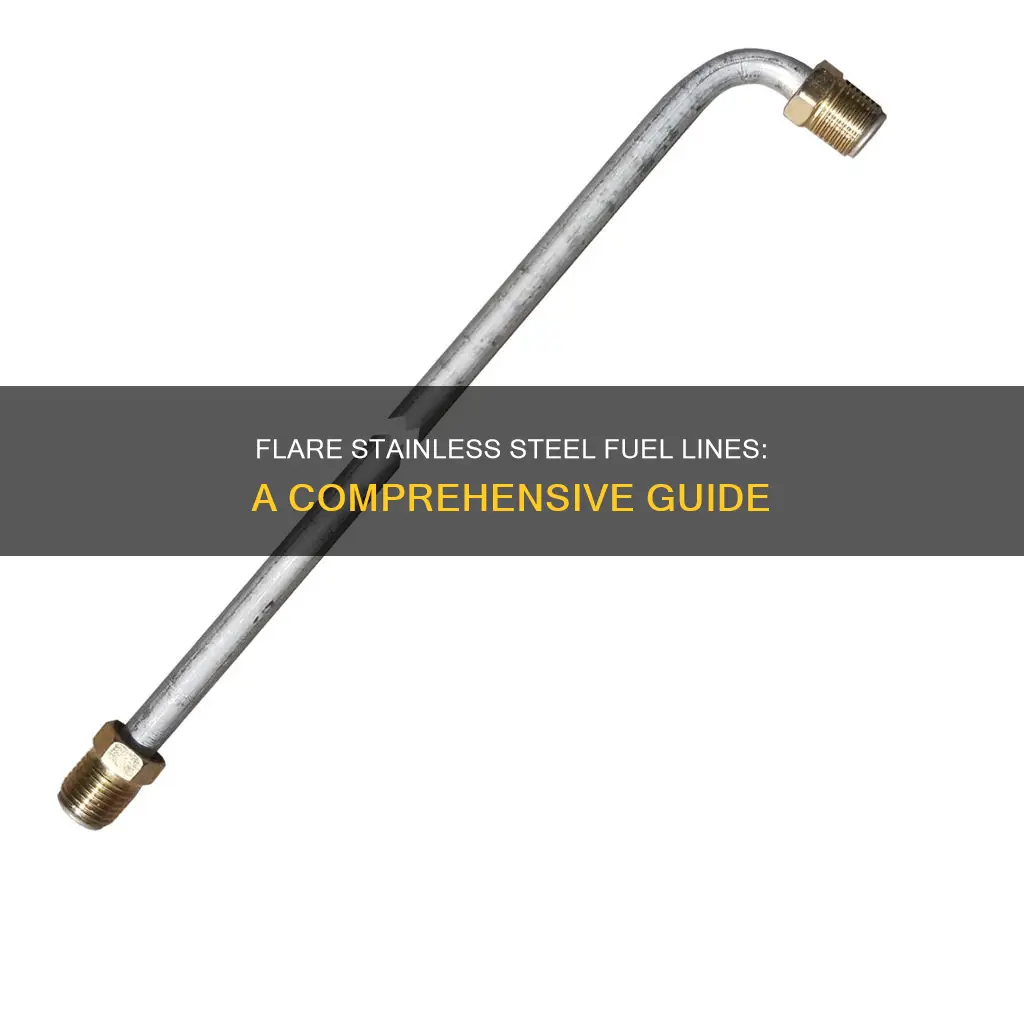
When it comes to working with fuel systems, understanding the properties of different materials is crucial. One common question that arises is whether stainless steel fuel lines can be flared. Flaring is a process used to create a smooth, rounded end on a pipe or tube, which is essential for proper connections and fittings. In this paragraph, we will explore the feasibility and considerations of flaring stainless steel fuel lines, providing insights into the process and its implications for fuel system maintenance and performance.
What You'll Learn
- Materials Compatibility: Flare stainless steel fuel lines require compatible materials to ensure safety and performance
- Flaring Techniques: Different methods for flaring stainless steel lines, such as hand-bending or using specialized tools
- Pressure Testing: Ensuring flare connections are leak-tight through pressure testing is crucial for fuel line safety
- Corrosion Resistance: Stainless steel's corrosion resistance makes it ideal for fuel lines in harsh environments
- Installation Guidelines: Proper installation procedures for flaring stainless steel fuel lines to ensure a secure fit
Materials Compatibility: Flare stainless steel fuel lines require compatible materials to ensure safety and performance
When working with flare stainless steel fuel lines, understanding the compatibility of materials is crucial for ensuring the safety and optimal performance of your fuel system. The primary concern is to prevent any adverse reactions between the fuel, the fuel line, and any other components in the system. Here's a detailed breakdown of the materials compatibility considerations:
Fuel Compatibility: The fuel you are using should be compatible with the stainless steel material. While stainless steel is generally resistant to corrosion, certain fuels, especially those containing ethanol or other additives, can still cause degradation over time. It's essential to use fuel that is specifically designed for the application and is compatible with the stainless steel fuel lines. Always refer to the manufacturer's guidelines for fuel recommendations.
Gaskets and Seals: The gaskets and seals used in the flare connections must be compatible with both the fuel and the stainless steel material. Rubber or silicone gaskets are commonly used and are generally compatible with most fuels. However, it's important to choose the correct size and type of gasket to ensure a tight seal without compromising the integrity of the connection.
Fittings and Connections: The fittings and connections used to join the fuel lines should also be compatible with the stainless steel material. Brass, copper, or stainless steel fittings are often used and can be joined using various methods such as compression, flare, or welded connections. Ensure that the fittings are designed to withstand the pressure and temperature requirements of your fuel system.
System Design and Maintenance: Proper system design and regular maintenance are essential to maintain materials compatibility. This includes using the correct size and length of fuel lines, avoiding sharp bends that could cause stress on the material, and implementing a regular inspection and maintenance schedule. Regularly check for any signs of corrosion, cracks, or leaks, and address any issues promptly to ensure the safety and performance of your fuel system.
By carefully considering these materials compatibility factors, you can ensure that your flare stainless steel fuel lines are installed and maintained correctly, providing a safe and efficient fuel supply for your application. Always refer to manufacturer guidelines and seek expert advice when necessary to ensure the best results.
Unveiling the Mystery: Where Fuel Lines Originate from the Internal Pump
You may want to see also
Flaring Techniques: Different methods for flaring stainless steel lines, such as hand-bending or using specialized tools
Flaring stainless steel fuel lines is a crucial process in plumbing and automotive applications, ensuring a secure and leak-free connection. When dealing with stainless steel, it's essential to employ the right techniques to achieve a precise flare that can withstand the demands of the fuel system. Here, we explore various flaring methods to ensure a successful outcome.
One traditional approach is hand-bending, a manual process that requires skill and precision. This method involves carefully bending the stainless steel line using pliers or a pipe bending tool. The key is to apply controlled pressure and maintain a consistent radius to create a smooth flare. Hand-bending is particularly useful for smaller-diameter lines and allows for more flexibility in terms of flare angles. It demands a steady hand and a keen eye for detail to ensure the flare is uniform and free from sharp edges.
For more complex or larger-scale projects, specialized tools are often employed. One such tool is the flare gun, which is designed to create flares with consistent and accurate dimensions. This tool typically consists of a handle and a mandrel that guides the bending process. The operator applies force to the handle, which, in turn, bends the line to the desired flare shape. Flare guns are available in various sizes and configurations to accommodate different pipe diameters and flare angles. This method is efficient and ensures repeatability, making it a popular choice for professionals.
Another technique is the use of a flare press, which is a mechanical device that applies pressure to the stainless steel line, forming a flare. This method is highly precise and can be automated, making it suitable for high-volume production. The flare press typically has adjustable settings to control the force and angle of the flare, ensuring consistency. Flare presses are often used in manufacturing and automotive industries where precision and speed are essential.
Additionally, some flaring tools utilize a combination of hand-bending and mechanical assistance. For instance, a flare mandrel can be used in conjunction with a hand tool to create a flare. The mandrel provides guidance and support during the bending process, ensuring a consistent shape. This hybrid approach offers the best of both worlds, combining the precision of mechanical tools with the control of manual techniques.
In summary, flaring stainless steel fuel lines can be achieved through various methods, each with its advantages. Hand-bending is a traditional and flexible approach, while specialized tools like flare guns and presses offer precision and efficiency. The choice of method depends on the specific requirements of the project, the size of the line, and the desired flare angle. Proper training and the use of appropriate tools are essential to ensure a successful and secure flare connection.
Cub Cadet Fuel Line: Size Guide for Optimal Performance
You may want to see also
Pressure Testing: Ensuring flare connections are leak-tight through pressure testing is crucial for fuel line safety
Pressure testing is an essential step in ensuring the safety and reliability of flare connections in fuel lines, especially when working with stainless steel materials. This process involves applying controlled pressure to the system to identify and address any potential leaks or weaknesses in the connections. By subjecting the flare connections to this test, you can verify their integrity and ensure they can withstand the demands of the fuel line environment.
When flaring stainless steel fuel lines, the connections must be meticulously prepared to ensure a secure and leak-tight seal. The process begins with carefully cleaning and preparing the ends of the fuel lines. This involves removing any debris or contaminants that could interfere with the flaring process and the subsequent connection. Proper preparation is critical to achieving a tight and reliable bond between the flared ends.
The flaring process itself is a precise technique that requires skill and attention to detail. It involves shaping the ends of the fuel lines to create a smooth, tapered surface that can be easily connected. The flared ends should be free of any sharp edges or burrs, as these can compromise the integrity of the connection. Once flared, the connections are typically aligned and secured using specialized fittings or clamps.
Pressure testing is then conducted to ensure the flare connections are leak-tight. This test involves applying a measured amount of pressure to the system and monitoring for any signs of leakage. The pressure is gradually increased, and the system is inspected for any visual indications of leaks, such as bubbles or moisture. If any leaks are detected, the connections must be re-examined and re-flared to ensure a proper seal.
It is crucial to follow standardized procedures and guidelines during pressure testing to ensure accuracy and consistency. This includes using calibrated equipment and documenting the test results. By adhering to these practices, you can confidently verify the effectiveness of the flare connections and ensure that the fuel lines are safe and ready for operation. Regular maintenance and periodic re-testing are also recommended to maintain the integrity of the flare connections over time.
Fuel Line Removal: Quick Tips for Tool-Free Access
You may want to see also
Corrosion Resistance: Stainless steel's corrosion resistance makes it ideal for fuel lines in harsh environments
The use of stainless steel for fuel lines is a popular choice in various industries, especially where harsh environments and corrosive elements are present. One of the key advantages of stainless steel is its exceptional corrosion resistance, which makes it an ideal material for fuel lines. Corrosion, a natural process that degrades materials over time, can be a significant concern in fuel systems, especially when exposed to certain chemicals, moisture, or extreme temperatures.
Stainless steel, as the name suggests, contains a significant amount of chromium, which forms a protective oxide layer on the surface when exposed to oxygen. This layer, known as the 'passivation layer,' acts as a barrier, preventing further corrosion and protecting the underlying material. When used for fuel lines, this corrosion resistance is crucial as it ensures the structural integrity of the line, even in the presence of corrosive substances. For instance, in marine environments, where saltwater and chlorinated water can accelerate corrosion, stainless steel fuel lines can withstand the harsh conditions without compromising their performance.
The resistance to corrosion is not limited to chemical attacks; it also applies to electrochemical corrosion, which is a significant concern in fuel systems. Stainless steel's ability to resist pitting and crevice corrosion makes it highly suitable for fuel lines that are often subjected to these forms of corrosion. These types of corrosion can lead to localized damage, compromising the fuel line's integrity, but stainless steel's passive nature ensures that such issues are minimized.
Furthermore, the corrosion resistance of stainless steel is not just about protection against external factors. It also ensures the longevity of the fuel lines by preventing internal degradation. Over time, fuel lines can be exposed to fuel contaminants, such as water or acidic compounds, which can corrode the inner surface. Stainless steel's resistance to these internal corrosive agents ensures that the fuel lines remain intact and functional for extended periods.
In summary, the corrosion resistance of stainless steel is a critical factor in its application for fuel lines, especially in challenging environments. This property ensures the durability and reliability of fuel systems, making stainless steel an excellent choice for engineers and designers in various industries. By choosing stainless steel, they can be confident that the fuel lines will perform optimally, even in the most demanding conditions.
Mastering Fuel Cell Efficiency: The Art of Running Return Lines
You may want to see also
Installation Guidelines: Proper installation procedures for flaring stainless steel fuel lines to ensure a secure fit
When working with stainless steel fuel lines, proper flaring techniques are crucial to ensure a secure and leak-free connection. Here are the installation guidelines to achieve a precise and reliable flare:
Preparation: Begin by ensuring you have the necessary tools and materials, including the stainless steel fuel line, flare nuts, and dies specific to your application. Clean the ends of the fuel lines to remove any debris or contaminants that could affect the flare quality. It is essential to work with cool lines to avoid any heat-related issues during the flaring process.
Flaring Process: Start by inserting the fuel line into the flare nut, ensuring it is centered. Use the appropriate flare die for the size of the line and apply firm, even pressure while rotating the die in a clockwise direction. The goal is to create a uniform and consistent flare. Continue the process until the desired flare depth is achieved, typically a few turns of the die. Avoid over-tightening to prevent damage to the line.
Inspection and Tightening: After flaring, inspect the joint for any imperfections or uneven flares. If necessary, use a file or sandpaper to smooth the flare and ensure a clean, even surface. Once satisfied with the flare quality, tighten the flare nut securely using the appropriate torque specifications for your application. This step ensures a tight seal and prevents any potential leaks.
Testing and Final Adjustments: Before completing the installation, perform a thorough test to check for any leaks. Use a soapy water solution or a specialized leak detection spray around the flared joint. If a leak is detected, carefully inspect the flare and make any necessary adjustments. Re-flare the joint if needed, ensuring the process is repeated correctly.
Safety and Maintenance: Always prioritize safety during the installation process. Wear appropriate personal protective equipment, such as gloves and safety goggles. Regularly maintain your tools and equipment to ensure optimal performance. Properly dispose of any waste materials, and follow all manufacturer guidelines for the specific fuel line and flare nut system you are using.
Mastering the Art of Small Engine Fuel Line Removal: A Step-by-Step Guide
You may want to see also
Frequently asked questions
Flaring stainless steel fuel lines is a process used in plumbing and automotive applications to create a smooth, rounded end on the fuel line, which helps prevent damage and ensures a secure connection. This technique is particularly useful when connecting fuel lines to fuel injectors or other components, as it provides a clean and precise fit, reducing the risk of fuel leaks and improving overall system efficiency.
Flaring a stainless steel fuel line typically involves using a flaring tool or a mandrel bending process. The process begins by cutting the fuel line to the desired length and then using a flaring tool to shape the end into a smooth, conical shape. This is done by applying pressure to the line, which causes the material to bend and form a flare. The flare is then carefully trimmed and deburred to ensure a clean and precise connection.
Yes, specialized tools are necessary for flaring stainless steel fuel lines. These include flaring tools, such as flaring dies or mandrels, which are designed to apply the required force and shape the material. Additionally, a good quality fuel line cutter, deburring tools, and a mandrel bending machine (for more complex applications) are essential. It is important to use the correct tools and techniques to ensure a professional and reliable flare.