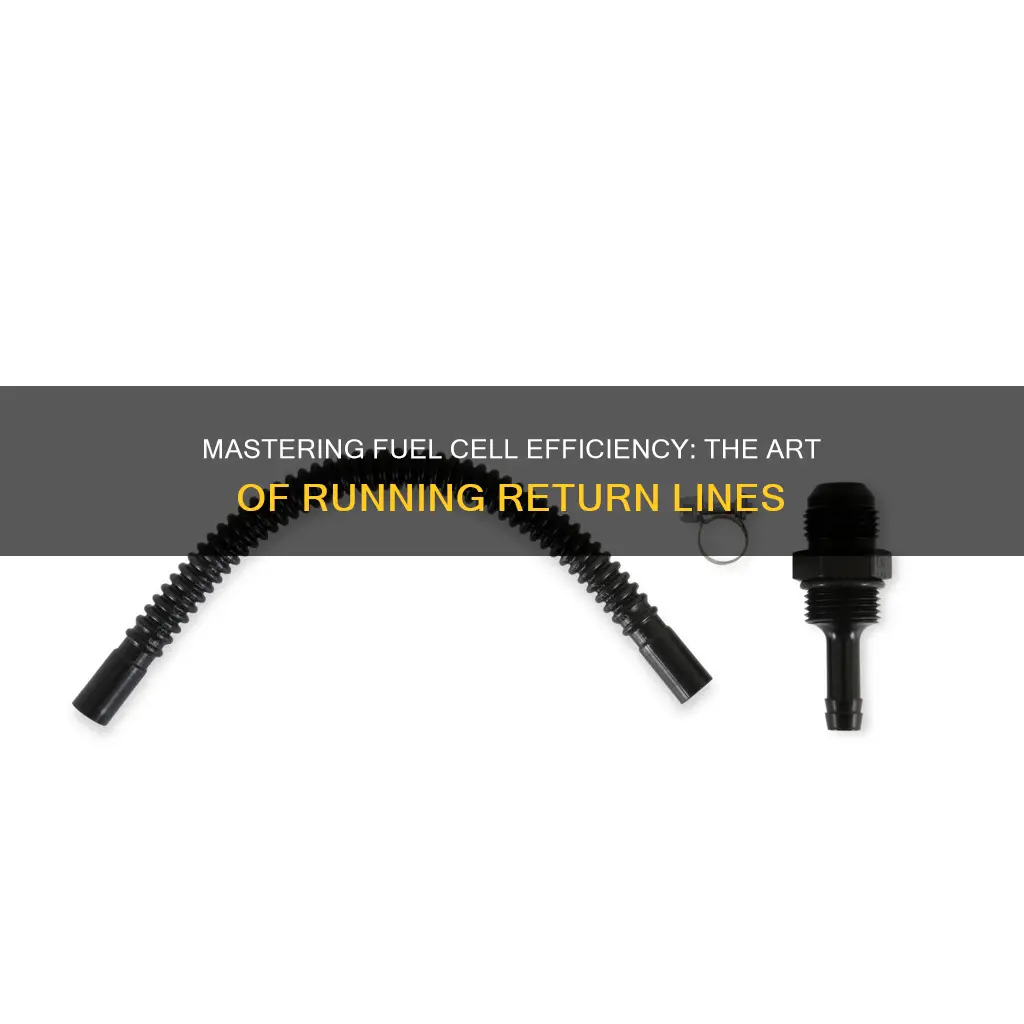
Running a return line to a fuel cell is a crucial step in ensuring efficient and effective operation of the fuel cell system. This process involves connecting the return line, which is responsible for transporting excess fuel and byproducts, to the fuel cell. By properly routing the return line, you can optimize the fuel cell's performance, enhance its longevity, and ensure a continuous and stable supply of fuel. This guide will provide a step-by-step overview of the process, including the necessary tools, safety precautions, and best practices to ensure a successful and safe installation.
What You'll Learn
- Fuel Cell Design: Optimize return line layout for efficient fuel gas recirculation
- Materials Selection: Choose corrosion-resistant materials for durability and reliability
- Flow Control: Implement precise flow control valves to regulate gas flow
- Pressure Management: Maintain optimal pressure to ensure proper fuel cell operation
- Maintenance: Regularly inspect and clean the return line for performance and safety
Fuel Cell Design: Optimize return line layout for efficient fuel gas recirculation
When designing a fuel cell system, optimizing the return line layout for efficient fuel gas recirculation is crucial to ensure optimal performance and longevity. The return line is responsible for transporting the unused fuel gas back to the fuel cell stack, where it can be recycled and utilized more efficiently. Here are some key considerations and steps to achieve this:
Firstly, it is essential to understand the fuel cell's operating principles. Fuel cells typically operate on the electrochemical reaction between a fuel (often hydrogen) and an oxidizing agent (usually oxygen from air). The reaction produces electricity, water, and heat. Efficient fuel gas recirculation ensures that the fuel cell receives a consistent supply of the reactants, maximizing power output and minimizing the formation of harmful byproducts.
The return line design should prioritize minimizing pressure drops and maintaining a steady flow. A well-designed return line should have a smooth, gradual curve to reduce turbulence and potential fuel gas stratification. This is especially important in systems where the fuel gas is under pressure, as sudden changes in flow direction can lead to pressure fluctuations, affecting the overall system performance. Consider using bends and elbows with gradual radii to ensure a smooth flow transition.
Another critical aspect is the placement of the return line. It should be positioned to avoid any obstructions or interference with other system components. Proper clearance is essential to prevent heat exchangers, catalysts, or other sensitive parts from being damaged by the flowing fuel gas. Additionally, the return line should be strategically placed to allow for easy maintenance and access during system operation.
Incorporating a fuel gas recirculation valve can further enhance the system's efficiency. This valve allows for precise control of the recirculation rate, ensuring that the fuel cell receives the optimal amount of fuel gas. By adjusting the valve, operators can fine-tune the system's performance, especially during changes in load or operating conditions. This level of control is vital for maintaining the fuel cell's efficiency and longevity.
Lastly, regular maintenance and monitoring of the return line are essential. Over time, the line may accumulate deposits or experience wear and tear, affecting its performance. Implementing a maintenance schedule that includes cleaning and inspection can help identify and address any issues promptly. This ensures that the fuel gas recirculation process remains efficient and contributes to the overall reliability of the fuel cell system.
Aluminum or Steel: Choosing the Right Fuel Line Material
You may want to see also
Materials Selection: Choose corrosion-resistant materials for durability and reliability
When designing and constructing a return line for a fuel cell system, the choice of materials is critical to ensure the long-term durability and reliability of the entire setup. The primary concern here is to select materials that can withstand the corrosive nature of the environment within a fuel cell system, which often involves high temperatures, various chemicals, and potentially aggressive atmospheres.
One of the key materials to consider is stainless steel, specifically types like 316 or 304 stainless steel. These grades are renowned for their excellent corrosion resistance, particularly in environments with high chloride content, which is common in fuel cell systems. Stainless steel's ability to form a protective oxide layer on its surface helps prevent corrosion, making it an ideal choice for the return line. For instance, the return line could be fabricated from 316 stainless steel, which is known for its superior resistance to pitting and crevice corrosion, ensuring the system's longevity.
In addition to stainless steel, certain alloys like Monel and Inconel can also be considered. These alloys offer exceptional resistance to a wide range of corrosive agents, including acids, alkalis, and salt solutions. For example, Monel, a nickel-based alloy, is highly resistant to pitting and crevice corrosion, making it suitable for applications where the return line might be exposed to harsh conditions. Similarly, Inconel, another nickel-based superalloy, provides excellent resistance to oxidation and corrosion at high temperatures, which is crucial for the efficient operation of a fuel cell system.
The choice of materials should also consider the compatibility with the fuels and electrolytes used in the fuel cell. For instance, if the fuel cell operates with hydrogen and uses an acidic electrolyte, materials like titanium or certain grades of stainless steel with low sulfur content might be preferred to avoid any potential reactions that could compromise the material's integrity.
Furthermore, the design and fabrication process should also incorporate measures to minimize stress concentrations and potential failure points. This includes careful welding techniques and the use of appropriate fasteners to ensure the structural integrity of the return line. By selecting the right materials and employing sound engineering practices, the return line can be designed to provide a reliable and efficient pathway for the fuel cell's operations.
Audi Fuel Line Sizes: A Comprehensive Guide
You may want to see also
Flow Control: Implement precise flow control valves to regulate gas flow
Flow control is a critical aspect of optimizing the performance and efficiency of a fuel cell system, especially when dealing with return lines. Precise flow control valves are essential components that enable engineers to manage the gas flow within the system, ensuring optimal operation and preventing potential issues.
The primary function of these valves is to regulate the movement of gases, such as hydrogen or air, to and from the fuel cell stack. By implementing flow control valves, engineers can fine-tune the gas composition and pressure, which is vital for maintaining the cell's power output and overall system stability. For instance, in a fuel cell vehicle, precise flow control ensures that the correct amount of hydrogen is supplied to the anode while managing the air flow to the cathode, maximizing energy conversion efficiency.
These valves operate based on various principles, such as pressure differentials, thermal expansion, or even electromagnetic actuation. For instance, a commonly used valve type is the solenoid-operated valve, which uses an electromagnetic coil to open or close the valve, allowing or restricting gas flow. The precision of these valves is crucial, as even small adjustments can significantly impact the fuel cell's performance.
To implement effective flow control, engineers must consider several factors. Firstly, the valve's response time is critical, especially in dynamic systems where gas flow rates need to be adjusted rapidly. Fast-acting valves ensure that the system can quickly adapt to changing conditions, maintaining optimal performance. Secondly, the valve's capacity and compatibility with the gas being controlled are essential. Engineers must select valves that can handle the expected gas flow rates and are compatible with the fuel cell's operating environment.
Additionally, advanced control systems can be integrated with these valves to provide automated flow regulation. These systems use sensors to monitor gas flow, pressure, and temperature, and then adjust the valves accordingly. By implementing such control algorithms, fuel cell systems can operate with minimal human intervention, ensuring consistent and efficient performance.
In summary, precise flow control valves are indispensable in managing gas flow within fuel cell systems. Their ability to regulate gas composition and pressure enables engineers to optimize power output and system stability. With careful consideration of valve types, response times, and control systems, fuel cell technology can be advanced, leading to more efficient and reliable energy production.
Fuel Line Tubing: Top Sources for Your Car's Needs
You may want to see also
Pressure Management: Maintain optimal pressure to ensure proper fuel cell operation
To ensure the efficient and safe operation of a fuel cell, maintaining the correct pressure is crucial. This is especially important when considering the return line, which is a critical component in the fuel cell's cooling and fuel management system. The return line is responsible for transporting excess fuel and water back to the fuel cell stack, and its pressure management is vital for several reasons.
Firstly, pressure regulation ensures the proper mixing and combustion of fuel and air within the fuel cell. Fuel cells operate on the principle of electrochemical reactions, where a fuel (often hydrogen) and an oxidant (usually oxygen from the air) react to produce electricity, water, and heat. The return line's pressure must be carefully controlled to facilitate the optimal flow of these reactants and products. If the pressure is too low, it can lead to inadequate mixing, resulting in incomplete reactions and reduced efficiency. Conversely, excessive pressure can cause issues such as fuel flooding, where excess fuel accumulates in the cell, potentially leading to catalyst poisoning and performance degradation.
The pressure management system in a fuel cell typically involves a series of valves and sensors. These components work together to monitor and adjust the pressure within the return line. For instance, pressure sensors can detect deviations from the optimal pressure setpoint and trigger valve adjustments to correct the issue. The valves can either restrict or release pressure as needed, ensuring that the fuel cell operates within the desired pressure range. This dynamic control is essential for maintaining the fuel cell's performance and longevity, especially in varying environmental conditions.
In addition to the technical aspects, pressure management also plays a role in the overall system design. Engineers must consider the layout and sizing of the return line to accommodate the required pressure differentials and flow rates. Proper design ensures that the fuel cell receives the necessary reactants while minimizing pressure losses, which can impact efficiency. Furthermore, the return line's pressure management system should be designed to handle potential faults, such as blockages or leaks, to prevent sudden pressure spikes or drops that could damage the fuel cell.
In summary, pressure management is a critical aspect of operating a return line to a fuel cell. It ensures the fuel cell's performance, efficiency, and longevity by maintaining the correct pressure for optimal fuel-air mixing and combustion. A well-designed pressure management system, incorporating sensors, valves, and thoughtful engineering, is essential to achieving reliable and sustainable fuel cell operation.
Understanding the Role of Fuel Vapor Lines in Your Vehicle
You may want to see also
Maintenance: Regularly inspect and clean the return line for performance and safety
The return line is a critical component in the operation of a fuel cell system, and regular maintenance is essential to ensure optimal performance and safety. Over time, this line can accumulate debris, contaminants, and scale, which can lead to reduced efficiency and potential system failures. Therefore, it is crucial to establish a routine inspection and cleaning process for the return line.
During the inspection, look for any signs of damage, corrosion, or blockages. The return line should be free from cracks, leaks, or any visible wear and tear. Inspect the connections and fittings to ensure they are tight and secure. Check for any signs of contamination, such as the presence of oil, grease, or other foreign matter, which could indicate a leak or system issue. It is also important to verify the line's flexibility and ensure it is not kinked or bent in a way that could restrict flow.
Cleaning the return line is a vital step in maintenance. Start by disconnecting the line from the fuel cell and the pump. Use a suitable cleaning agent recommended by the manufacturer to remove any built-up contaminants. This can often be done by running a cleaning solution through the line, ensuring it covers all internal surfaces. For more stubborn deposits, mechanical cleaning methods such as brushing or using a specialized cleaning tool may be required. After cleaning, rinse the line thoroughly to remove any residue and ensure it is free from contaminants.
Regularly scheduled maintenance checks should be performed to establish a baseline for the return line's condition. This will help identify any issues early on and allow for prompt action. Keep a record of the inspections and cleaning processes, including the dates and any observations made. This documentation will assist in tracking the line's performance and safety over time.
In summary, regular inspection and cleaning of the return line are essential practices to maintain the efficiency and reliability of a fuel cell system. By following these maintenance procedures, you can ensure the system operates safely and optimally, reducing the risk of unexpected failures and extending the lifespan of the fuel cell technology.
Ford Focus 2001 Fuel Line Breakdown: Essential Components Explained
You may want to see also
Frequently asked questions
The return line, also known as the exhaust line, is a crucial component in fuel cell technology. It serves the function of transporting the spent hydrogen-oxygen reaction products, primarily water vapor and carbon dioxide, away from the fuel cell stack. This line ensures that the system remains efficient and safe by managing the byproducts of the electrochemical reaction.
Connecting the return line requires careful consideration of the fuel cell's design and specifications. It is essential to follow the manufacturer's guidelines for installation. Typically, the return line is connected to the exhaust port of the fuel cell stack, where it collects the reaction gases. Proper sealing and secure fastening are critical to prevent leaks and ensure optimal performance.
Material selection for the return line depends on factors such as temperature, pressure, and compatibility with the fuel cell's components. Common materials include stainless steel, titanium, or specialized polymers. The size of the line is determined by the fuel cell's capacity and the desired flow rate of the reaction products. Engineers often calculate the required diameter based on the expected volume and velocity of the exhaust gases.
Modifying the return line should be approached with caution and a thorough understanding of the system's requirements. While some adjustments might be possible, such as adding a regulator to control pressure, significant alterations may impact the fuel cell's performance and longevity. It is generally recommended to consult the manufacturer's guidelines or seek professional advice before making any modifications to ensure the system's reliability and safety.