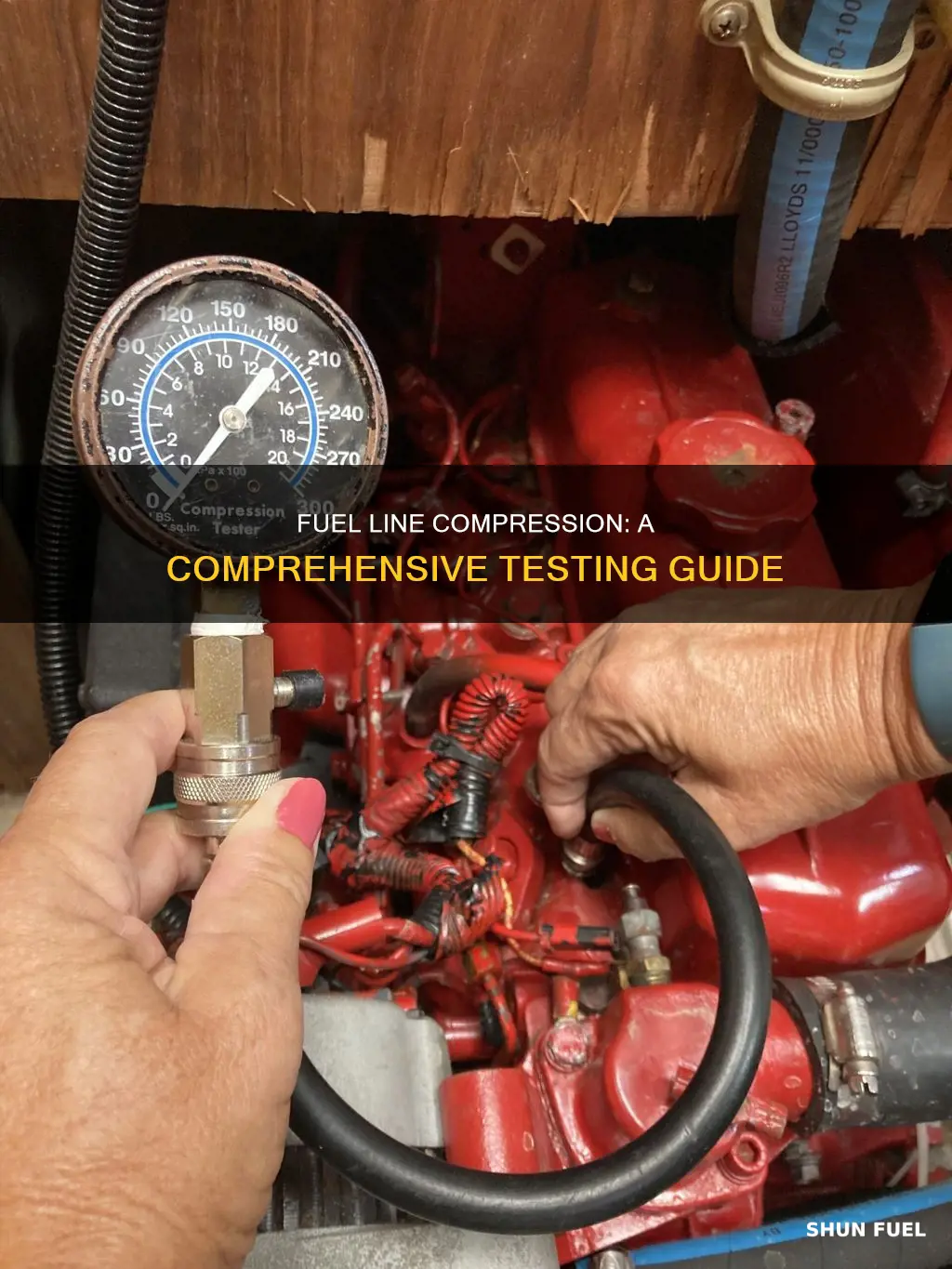
Fuel lines are a critical component of any vehicle's fuel system, and ensuring their integrity is essential for optimal performance and safety. One method to assess the condition and functionality of fuel lines is through a compression test. This test involves applying pressure to the fuel lines to check for leaks, blockages, or weaknesses that could compromise the fuel system's efficiency and reliability. By simulating real-world conditions, the compression test provides valuable insights into the fuel lines' ability to withstand pressure, helping identify potential issues before they cause significant problems. Understanding the role of compression testing in fuel line maintenance is crucial for vehicle owners and mechanics alike, as it ensures the longevity and safety of the vehicle's fuel system.
Characteristics | Values |
---|---|
Compression Test Purpose | To ensure the fuel lines can withstand pressure and prevent leaks |
Test Pressure | Typically 50-100 psi (pounds per square inch) |
Test Duration | Varies depending on the fuel line material and design |
Test Procedure | Apply pressure gradually and monitor for any signs of leakage or damage |
Common Issues Detected | Cracks, punctures, weakened connections, and material degradation |
Test Frequency | Recommended during vehicle maintenance and before long trips |
Test Equipment | Pressure gauge, manometer, and possibly a fuel leak detector |
Test Standards | May vary by region and vehicle manufacturer |
Pass/Fail Criteria | No visible damage or leaks, and pressure holds at the specified level |
What You'll Learn
- Fuel Line Material: Different materials have varying compressibility; some are more suitable for compression testing
- Fuel Line Diameter: Thicker lines may require different compression test parameters compared to thinner ones
- Fuel Line Length: Longer lines might exhibit different behavior under compression due to material properties and design
- Fuel Line Temperature: Temperature affects material elasticity; compression tests should consider ambient and operating temperatures
- Fuel Line Pressure: The pressure at which the compression test is conducted can impact the results and material behavior
Fuel Line Material: Different materials have varying compressibility; some are more suitable for compression testing
When considering the suitability of materials for fuel lines, it's important to understand the role of compressibility and how it relates to compression testing. Different materials exhibit varying degrees of compressibility, which can significantly impact the performance and longevity of fuel lines. This is particularly crucial in the automotive and aviation industries, where fuel lines are exposed to dynamic forces and varying pressure conditions.
The compressibility of a material refers to its ability to be compressed or reduced in size under external pressure. In the context of fuel lines, this property is essential because it determines how the material responds to the pressure changes that occur during fuel flow and engine operation. Materials with low compressibility are more rigid and less susceptible to deformation under pressure, ensuring a consistent and reliable fuel supply. On the other hand, materials with higher compressibility may be more flexible but could potentially lead to fuel leakage or reduced performance over time.
Compression testing is a critical process used to evaluate the compressibility characteristics of various materials. This test involves applying controlled pressure to a sample of the material and measuring its response. By analyzing the material's behavior during compression, engineers can determine its suitability for fuel line applications. For instance, materials with excellent compressive strength and minimal permanent deformation are ideal for fuel lines, as they can withstand the internal pressures and vibrations encountered during operation.
Various materials are commonly used in fuel line construction, each with its own unique compressibility properties. Rubber, for example, is a popular choice due to its flexibility and ability to absorb vibrations. However, natural rubber may not be as resistant to compression as synthetic rubbers, such as neoprene or butyl. These synthetic rubbers offer improved durability and resistance to fuel degradation. On the other hand, materials like steel or aluminum alloys are known for their high compressive strength and resistance to deformation, making them suitable for high-pressure fuel lines in heavy-duty applications.
In summary, the choice of material for fuel lines is closely tied to its compressibility and the results of compression testing. Engineers must consider the specific requirements of the fuel system, including pressure ratings, temperature ranges, and environmental conditions, to select the most appropriate material. By understanding the compressibility characteristics of different materials, manufacturers can ensure the reliability and performance of fuel lines, contributing to the overall efficiency and safety of vehicles and aircraft.
Finding the Perfect Fit: Where to Buy Molded Fuel Line for Kx65
You may want to see also
Fuel Line Diameter: Thicker lines may require different compression test parameters compared to thinner ones
When it comes to fuel lines, the diameter plays a crucial role in determining the appropriate compression test parameters. Thicker fuel lines, typically those with larger diameters, exhibit different characteristics and behaviors compared to thinner lines. These thicker lines often have a higher capacity to withstand increased pressure and are more resistant to bending or kinking. As a result, the compression test should reflect these unique properties.
In the context of compression testing, the diameter of the fuel line directly influences the force required to achieve a specific compression level. Thicker fuel lines generally need higher compression forces to reach the desired level of deformation. This is because thicker lines have more material to compress, and the increased cross-sectional area requires a greater applied force to achieve the same level of compression as thinner lines. Therefore, when designing the test, engineers must consider the diameter of the fuel line to ensure accurate and meaningful results.
The compression test parameters should be adjusted to accommodate the thicker fuel lines. This may involve increasing the compression speed, applying higher loads, or using specialized test equipment capable of handling larger diameters. By tailoring the test conditions to the fuel line's diameter, engineers can accurately assess the line's performance, including its ability to withstand pressure, resist kinking, and maintain a consistent flow rate.
Furthermore, the test should also consider the material properties of the thicker fuel lines. Different materials may exhibit varying behaviors under compression, and the test parameters should be optimized for the specific material being used. For instance, some materials might be more susceptible to permanent deformation, requiring a different approach to the compression test.
In summary, when conducting compression tests for fuel lines, it is essential to take into account the diameter of the lines. Thicker fuel lines demand unique test parameters, including higher compression forces and specialized equipment, to accurately evaluate their performance. By understanding the relationship between fuel line diameter and compression test requirements, engineers can ensure the safety and reliability of fuel systems in various applications.
Boat Fuel Line Vent Hose: Size Guide for Optimal Performance
You may want to see also
Fuel Line Length: Longer lines might exhibit different behavior under compression due to material properties and design
The length of a fuel line can significantly impact its performance and behavior under compression, especially in high-pressure applications. Longer fuel lines, while providing more flexibility, may present unique challenges when subjected to compression forces. This is primarily due to the inherent material properties and the design considerations involved in their construction.
In the context of compression testing, longer fuel lines can exhibit more pronounced effects of material elasticity and structural integrity. The material used in the construction of these lines, such as rubber or synthetic compounds, may have varying degrees of compressibility. When compressed, longer lines might experience increased stress on the material, potentially leading to deformation or even failure if the material properties are not optimized. For instance, a fuel line made from a highly elastic material might stretch more under compression, affecting its ability to maintain a consistent diameter and potentially causing issues in fuel delivery.
Design factors also play a crucial role in the behavior of longer fuel lines under compression. The wall thickness, diameter, and overall construction of the line can influence its resistance to compression. Thicker walls and a larger diameter can provide better structural integrity, allowing the line to withstand higher compression forces without significant deformation. However, this must be balanced with the need for flexibility to accommodate engine movement and temperature changes.
To ensure optimal performance, fuel lines, especially those with longer lengths, should undergo rigorous testing to assess their compression behavior. This includes subjecting the lines to controlled compression forces and measuring their response, such as diameter changes, material deformation, and overall structural integrity. By understanding the unique challenges posed by longer fuel lines, engineers can design and select materials that provide the necessary flexibility and strength, ensuring reliable fuel delivery in various automotive or industrial applications.
In summary, longer fuel lines require careful consideration of material properties and design to ensure they can handle compression forces effectively. The length of the line introduces additional factors that influence its behavior, making compression testing an essential aspect of fuel line design and selection.
Fuel Line Sizing for the Jeep TJ: A Guide
You may want to see also
Fuel Line Temperature: Temperature affects material elasticity; compression tests should consider ambient and operating temperatures
The performance and longevity of fuel lines in vehicles are significantly influenced by temperature variations, making temperature considerations crucial in compression testing. Fuel lines are subjected to a range of temperatures during operation, from cold starts in winter to prolonged exposure to high temperatures under the hood. This temperature fluctuation can impact the material's elasticity, which is a critical factor in ensuring the fuel lines maintain their structural integrity and functionality.
In compression testing, it is essential to account for both ambient and operating temperatures to accurately assess the fuel line's performance. Ambient temperature refers to the surrounding environmental conditions, while operating temperature pertains to the conditions the fuel lines experience during typical usage. By simulating these temperature extremes, engineers can evaluate how the fuel lines respond and ensure they meet the required standards.
When conducting compression tests, it is imperative to include temperature-controlled environments. This allows for the simulation of real-world conditions, ensuring that the fuel lines are tested under their expected operating temperatures. For instance, a test can be performed by exposing the fuel lines to sub-zero temperatures to mimic cold starts, and then rapidly increasing the temperature to simulate prolonged engine operation. This comprehensive approach helps identify any potential issues related to temperature-induced elasticity changes.
The effect of temperature on material elasticity is a critical consideration. Materials used in fuel lines, such as rubber or synthetic compounds, can become stiffer or more brittle when exposed to cold temperatures, reducing their ability to absorb pressure. Conversely, high temperatures can cause materials to expand and become more pliable, potentially leading to excessive compression or failure. Understanding these temperature-related changes is vital for designing fuel lines that can withstand the rigors of everyday use.
In summary, compression testing for fuel lines must incorporate temperature variations to ensure the reliability and safety of the vehicle's fuel system. By accounting for both ambient and operating temperatures, engineers can accurately assess the material's elasticity and its response to different thermal conditions. This comprehensive approach to testing helps guarantee that fuel lines meet the necessary performance criteria and contribute to the overall efficiency and longevity of the vehicle.
Ford Fuel Line Removal: A Step-by-Step Guide for 1990 Models
You may want to see also
Fuel Line Pressure: The pressure at which the compression test is conducted can impact the results and material behavior
The pressure at which a compression test is performed on fuel lines is a critical factor that can significantly influence the test results and the behavior of the materials being evaluated. This is because fuel lines are designed to withstand specific pressure conditions, and any deviation from these conditions can lead to inaccurate assessments of the material's performance.
In the context of fuel lines, compression testing typically involves applying a controlled amount of pressure to the line and measuring its response. The pressure at which this test is conducted should closely mimic the actual operating conditions of the fuel system. For instance, if the fuel lines are intended for use in a high-pressure environment, the test should be carried out at or near this pressure range. This ensures that the material's behavior under realistic conditions is accurately represented.
When the pressure is too low, the test may not fully reveal the material's strength and durability, especially for high-strength materials. Conversely, if the pressure is too high, it can lead to unrealistic results, potentially causing damage to the fuel lines or the testing equipment. Therefore, it is essential to select a pressure that is appropriate for the specific application and material properties.
The impact of pressure on the test results is twofold. Firstly, it affects the material's mechanical response, such as its ability to resist deformation or failure. Secondly, it influences the test's accuracy in predicting the material's performance in real-world scenarios. For instance, a material that performs well under low pressure might not exhibit the same level of strength when subjected to higher pressures, which is crucial information for engineers designing fuel systems.
In summary, the pressure at which a compression test is conducted is a critical parameter that must be carefully considered to ensure the reliability and accuracy of the test results. It directly impacts the material's behavior and the test's ability to predict real-world performance, making it a vital aspect of fuel line compression testing.
Fuel Line Size for 1977 Suzuki KZ650: Essential Guide
You may want to see also
Frequently asked questions
A compression test is a method used to assess the integrity and performance of fuel lines in vehicles. It involves applying pressure to the fuel lines to check for any leaks, blockages, or weaknesses in the material. This test is crucial for ensuring that the fuel system is functioning correctly and safely.
The process typically involves using a specialized tool called a fuel line compression tester. This device is connected to the fuel lines, and pressure is gradually increased while monitoring for any leaks or changes in pressure. The test can identify issues like cracked lines, blocked filters, or faulty fuel pump components.
Compression testing is essential as it helps identify potential problems with the fuel system before they become major issues. Fuel lines that are not functioning properly can lead to fuel leaks, reduced engine performance, or even engine failure. Regular testing ensures the safety and reliability of the vehicle's fuel supply, especially in high-pressure systems.