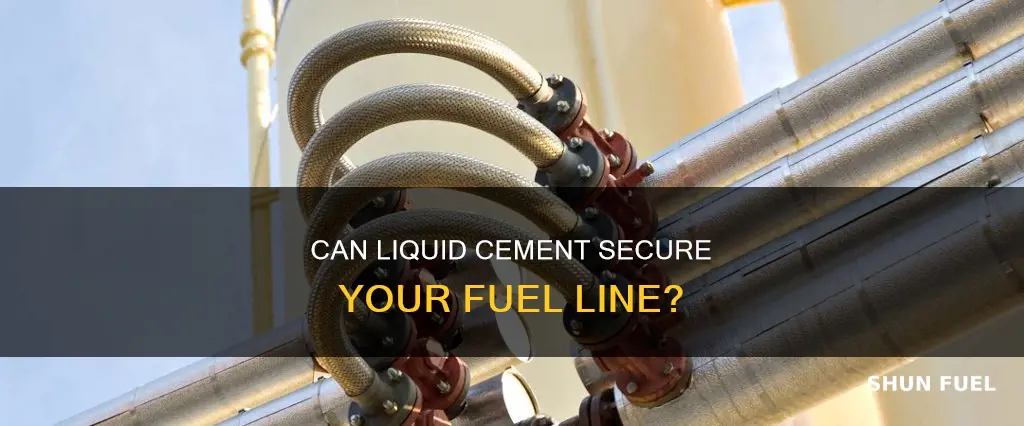
When it comes to repairing fuel lines, one might wonder if liquid cement is a viable option. While liquid cement can be used for various applications, it is crucial to consider its compatibility and effectiveness in the context of fuel lines. This paragraph will explore the potential benefits and drawbacks of using liquid cement for fuel line repairs, examining its ability to withstand the demands of a fuel-carrying system.
What You'll Learn
- Material Compatibility: Liquid cement must be compatible with the fuel line material to avoid corrosion or damage
- Temperature Resistance: It should withstand the temperature fluctuations of fuel lines without degrading
- Flexibility: The cement should be flexible to accommodate movement and prevent cracking
- Leak Prevention: Proper application ensures a strong, leak-free bond between fuel line components
- Regulatory Compliance: Using approved cements that meet industry standards for fuel systems is essential
Material Compatibility: Liquid cement must be compatible with the fuel line material to avoid corrosion or damage
When considering the use of liquid cement on fuel lines, material compatibility is a critical factor to ensure the integrity and safety of the fuel system. The primary concern is to prevent any adverse reactions that could lead to corrosion, degradation, or damage to the fuel line material. This is especially important as fuel lines are designed to withstand the corrosive effects of various substances, including the fuel itself, and any materials used in their construction should be able to resist these influences.
Liquid cement, typically a type of epoxy or polyurethane-based adhesive, can be a suitable option for bonding and sealing various materials. However, its compatibility with the specific fuel line material is essential. Different materials, such as rubber, plastic, or metal, may react differently to the cement's chemical composition. For instance, some cements might cause degradation or hardening of the fuel line material over time, leading to potential leaks or reduced flexibility.
To ensure compatibility, it is crucial to select a liquid cement that is specifically formulated for the intended fuel line material. Manufacturers often provide recommendations or technical data sheets that outline the compatible materials for their products. These guidelines should be followed to the letter to guarantee the long-term performance and reliability of the fuel system. For example, if the fuel line is made of a specific type of rubber, a cement designed for rubber bonding should be used to avoid any adverse reactions.
In addition to the cement's compatibility with the fuel line material, it is also essential to consider the environmental factors. The fuel line may be exposed to varying temperatures, UV radiation, and other external influences. Therefore, the chosen cement should be able to withstand these conditions without compromising its bond or the integrity of the fuel line. Testing and selecting cements that meet or exceed industry standards for fuel line applications can help ensure a reliable and safe fuel system.
In summary, material compatibility is a critical aspect when using liquid cement on fuel lines. The cement must be compatible with the specific fuel line material to prevent corrosion, damage, or performance issues. Following manufacturer guidelines and selecting cements designed for the intended application will help ensure a secure and reliable fuel system, contributing to the overall safety and efficiency of the vehicle or equipment.
Gas Line Leaks: Understanding the Causes and Solutions
You may want to see also
Temperature Resistance: It should withstand the temperature fluctuations of fuel lines without degrading
When considering the use of liquid cement on fuel lines, one of the critical factors to evaluate is its temperature resistance. Fuel lines are exposed to a wide range of temperatures, from extreme cold during winter to high heat generated by the engine. Therefore, the chosen cement must be able to withstand these temperature fluctuations without compromising its integrity or the performance of the fuel system.
The temperature resistance of a liquid cement is often determined by its ability to maintain its viscosity and chemical properties over a specific temperature range. In the context of fuel lines, the cement should not degrade or become brittle when exposed to cold temperatures, as this could lead to cracks or failures in the fuel system. Similarly, it should not soften or lose its bonding strength when subjected to high temperatures, which could result in fuel leaks or system malfunctions.
To ensure temperature resistance, it is essential to select a liquid cement specifically formulated for fuel line applications. These cements are designed to meet the unique challenges posed by the fuel environment, including resistance to fuel degradation and temperature extremes. They are typically made from materials that can withstand the volatile nature of fuels and the varying temperatures they encounter.
During the installation process, it is crucial to follow the manufacturer's guidelines for temperature control. Applying the cement at the recommended temperature range ensures optimal bonding and minimizes the risk of temperature-related issues. Proper temperature control also helps to avoid any potential damage to the fuel lines or the cement itself, ensuring a reliable and long-lasting connection.
In summary, when using liquid cement on fuel lines, temperature resistance is a critical consideration. The chosen cement should be able to withstand the temperature fluctuations associated with fuel lines without degrading, ensuring the integrity and reliability of the fuel system. By selecting the right cement and following proper installation practices, you can effectively address the temperature challenges posed by fuel lines.
Fuel Line Sizing for the Jeep TJ: A Guide
You may want to see also
Flexibility: The cement should be flexible to accommodate movement and prevent cracking
When considering the use of liquid cement on fuel lines, flexibility is a critical factor to ensure the integrity and longevity of the installation. Fuel lines are subject to various movements and vibrations, especially in automotive or industrial applications. The cement used for bonding and sealing these lines must be flexible enough to accommodate these movements without compromising its structural integrity.
Flexibility in this context refers to the material's ability to bend and stretch without breaking or cracking. Rigid cements, while strong, can become brittle and prone to failure when exposed to the dynamic nature of fuel lines. Over time, the repeated flexing of the line can lead to micro-cracks in the cement, which may not be visible but can significantly reduce the overall strength and reliability of the connection.
The ideal cement for fuel line applications should possess a certain degree of elasticity, allowing it to deform slightly under stress without permanent deformation. This property ensures that the cement can 'give' when the fuel line moves, thereby preventing the formation of cracks. It's important to note that flexibility does not mean the cement will be weak; instead, it should maintain its structural integrity while accommodating the fuel line's natural movement.
To achieve this level of flexibility, manufacturers often use specific polymers and additives in the cement formulation. These ingredients create a material that can bend and stretch without losing its bonding strength. When selecting a liquid cement for fuel lines, it is essential to choose a product specifically designed for this purpose, ensuring it meets the required flexibility standards.
In summary, flexibility is a key characteristic of liquid cement used on fuel lines, enabling it to withstand the dynamic environment of fuel transportation and usage. By choosing the right cement with the appropriate flexibility, engineers and technicians can ensure a reliable and long-lasting connection, minimizing the risk of leaks and other potential issues.
Mastering Fuel Line Antifreeze: A Comprehensive Guide to Winter Car Care
You may want to see also
Leak Prevention: Proper application ensures a strong, leak-free bond between fuel line components
When it comes to fuel line maintenance and repair, ensuring a leak-free bond between components is crucial to prevent potential hazards and costly repairs. Liquid cement, specifically designed for bonding rubber and plastic materials, can be an effective tool for achieving this goal. However, its application requires careful consideration and adherence to specific guidelines to ensure optimal results.
The proper use of liquid cement for fuel line applications involves several key steps. Firstly, it is essential to clean the surfaces of the fuel line components thoroughly. Any dirt, grease, or debris must be removed to ensure a strong bond. This can be achieved using a mild detergent or a specialized cleaner designed for this purpose. After cleaning, allow the surfaces to dry completely, ensuring there is no moisture present.
Once the surfaces are prepared, apply a thin and even layer of liquid cement to the fuel line components. It is important to follow the manufacturer's instructions regarding the appropriate amount and technique. Over-application can lead to excess cement oozing and potentially attracting dirt or causing blockages. Use a small brush or your finger (after wearing gloves) to spread the cement evenly, ensuring complete coverage of the mating surfaces.
After the cement has been applied, allow sufficient time for it to cure according to the product's guidelines. This curing process is critical to achieving a strong and durable bond. Avoid any pressure or stress on the bonded area during this period to ensure the integrity of the repair. Once cured, the cement will create a robust seal, preventing any fuel leaks and ensuring the fuel line functions optimally.
In summary, proper application of liquid cement is essential for leak prevention in fuel line systems. By following the manufacturer's instructions and adhering to the cleaning, application, and curing processes, you can ensure a strong, leak-free bond between fuel line components, promoting the overall reliability and safety of the vehicle's fuel system.
80 CB750 Fuel Line: Location and Connection Guide
You may want to see also
Regulatory Compliance: Using approved cements that meet industry standards for fuel systems is essential
When it comes to working with fuel lines, regulatory compliance is of utmost importance to ensure the safety and reliability of the entire system. One critical aspect of this compliance is the use of approved cements that meet industry standards specifically designed for fuel systems. These standards are in place to guarantee that the materials used in fuel lines and their connections are compatible, durable, and resistant to the corrosive effects of fuel.
The primary reason for this regulation is to prevent potential hazards associated with the use of improper cements. Fuel lines carry flammable substances, and any compromise in their integrity could lead to dangerous leaks or even fires. Approved cements are formulated to withstand the harsh conditions of fuel environments, including temperature fluctuations and the presence of various fuel types. They provide a secure and reliable bond between fuel lines, ensuring that the system remains leak-free and functional over time.
Industry standards, such as those set by organizations like the Society of Automotive Engineers (SAE) and the American Society for Testing and Materials (ASTM), provide specific guidelines for the materials and performance characteristics required for fuel system cements. These standards define the necessary properties, such as adhesion, flexibility, and resistance to fuel degradation, that the cement must possess. By adhering to these standards, manufacturers and technicians can ensure that the cements used in fuel line installations are of the highest quality and will perform as expected.
Using non-approved or substandard cements can have severe consequences. Such cements may lack the necessary resistance to fuel, leading to degradation over time, which can result in fuel leaks and potential safety hazards. Additionally, improper cements might not provide adequate bonding strength, causing connections to fail under pressure or vibration, further compromising the system's integrity. Therefore, it is crucial to always select cements that have been approved and tested to meet the specific requirements of fuel systems.
In summary, regulatory compliance in fuel system installations mandates the use of approved cements that adhere to industry standards. These standards ensure that the cements are compatible with fuel environments, providing a secure and reliable bond that prevents leaks and potential hazards. By following these guidelines, professionals can maintain the safety and performance of fuel systems, meeting the highest regulatory requirements.
Echo Carb Fuel Line: Location and Identification Tips
You may want to see also
Frequently asked questions
No, liquid cement should not be used on fuel lines. Fuel lines are designed to withstand high temperatures and pressures, and using cement can lead to a host of issues. Cement can cause the fuel line to become brittle and crack over time, leading to fuel leaks and potential fire hazards. It's crucial to use the correct materials and adhesives for fuel line installations and repairs.
The primary risk is the potential for fuel leaks and system failures. Cement can create a barrier that hinders the flow of fuel, leading to reduced performance or even engine stalls. Additionally, the heat generated during the cement curing process can cause the fuel line to expand and contract, further compromising its integrity. It's essential to follow manufacturer guidelines and use approved adhesives for fuel systems.
Absolutely! For fuel line repairs, it's recommended to use specialized fuel line adhesives or tape designed for this purpose. These products are flexible, heat-resistant, and can provide a secure bond without compromising the fuel line's performance. It's always best to consult the vehicle's manual or seek professional advice to ensure the right materials are used for a safe and effective repair.