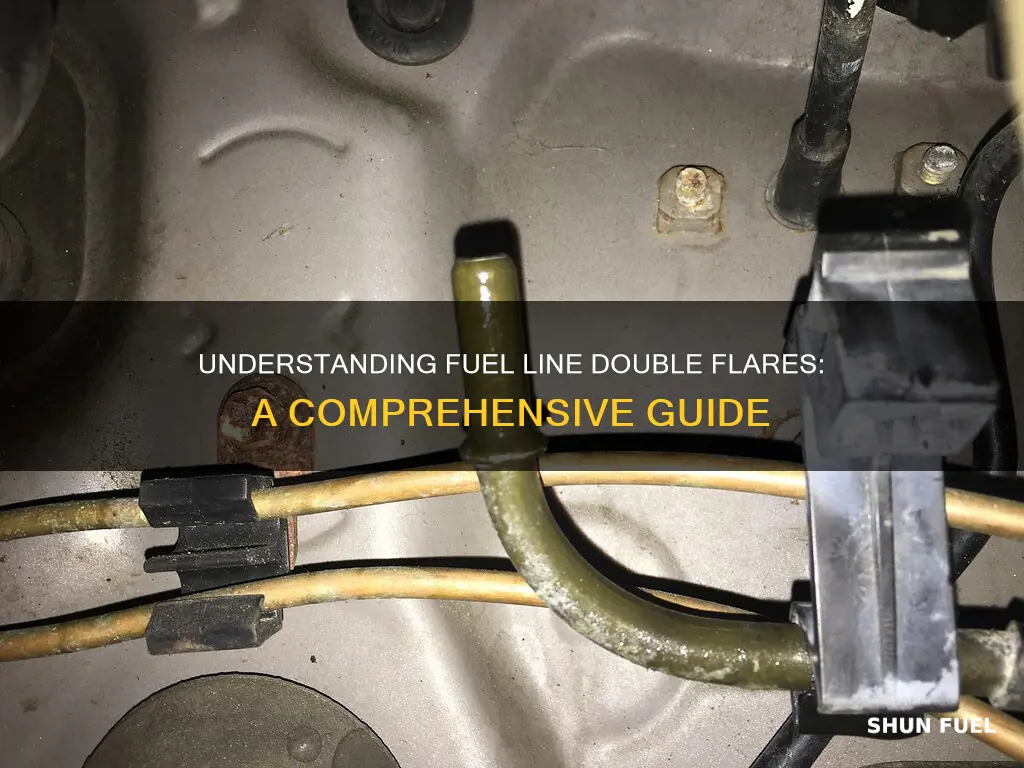
The fuel line double flare is a critical component in the automotive industry, specifically in the design and installation of fuel systems. This feature is an essential safety measure, ensuring a secure and reliable connection between the fuel tank and the engine. It involves a unique threading and sealing mechanism that provides a robust and leak-proof interface, allowing for the efficient transfer of fuel while maintaining structural integrity. Understanding the intricacies of this design is crucial for mechanics and engineers to ensure optimal performance and longevity of fuel systems in various vehicles.
Characteristics | Values |
---|---|
Material | Stainless steel, aluminum, brass |
Connection Type | Double flare |
Compatibility | Universal, fits various engine models |
Temperature Range | -40°F to 400°F (-40°C to 204°C) |
Pressure Rating | Up to 150 psi (pounds per square inch) |
Length | Varies, typically 1-6 feet |
Color | Silver, black, blue |
Brand | Various, including Bosch, Denso, NGK |
Package Includes | Single fuel line, fittings, and installation hardware |
Application | Fuel injection systems, carbureted engines |
Features | Corrosion-resistant, flexible, easy to install |
What You'll Learn
- Fuel Line Materials: Different materials like steel, brass, and plastic are used for fuel lines
- Double Flare Design: The double flare design provides a secure connection and prevents fuel leaks
- Fitting Compatibility: Ensure the double flare fits the specific fuel line and engine requirements
- Installation Process: Proper installation techniques are crucial for a tight and leak-free connection
- Maintenance and Inspection: Regular checks and maintenance can extend the life of the fuel line
Fuel Line Materials: Different materials like steel, brass, and plastic are used for fuel lines
Fuel lines are an essential component of any vehicle's fuel system, responsible for transporting fuel from the tank to the engine. The choice of material for these lines is crucial, as it directly impacts performance, durability, and safety. Over the years, various materials have been utilized for fuel lines, each offering unique advantages and disadvantages.
One of the most common materials used for fuel lines is steel. Steel fuel lines are known for their exceptional strength and durability. They can withstand high pressure and temperature, making them ideal for high-performance vehicles or those operating in extreme conditions. Steel lines are also less susceptible to corrosion, ensuring a longer lifespan. However, they can be heavier and more rigid compared to other materials, which might affect the overall flexibility of the fuel system.
Brass is another popular choice for fuel lines. This material offers excellent corrosion resistance, making it suitable for vehicles with aluminum or other non-ferrous metal bodies. Brass lines are also known for their smooth interior surface, which reduces the risk of fuel contamination and ensures a consistent fuel flow. Additionally, brass is lightweight and flexible, allowing for easier installation and routing within the engine compartment.
In contrast, plastic fuel lines have gained popularity due to their lightweight nature and cost-effectiveness. Plastic is highly resistant to corrosion and can withstand high temperatures, making it a safe choice for fuel transportation. It is also flexible, allowing for easy bending and installation. However, plastic lines may not be as durable as steel or brass, especially in extreme conditions, and they can be more susceptible to damage from sharp edges or high-pressure fuel.
The choice of material often depends on the specific requirements of the vehicle and the operating conditions. For high-performance applications, steel might be preferred for its strength, while brass could be ideal for its corrosion resistance and flexibility. Plastic, with its lightweight and cost-effectiveness, is a popular choice for everyday vehicles. It is essential to consider the advantages and disadvantages of each material to ensure the fuel system operates efficiently and safely.
Sonoma Fuel Lines: Uncovering Hidden Intake Secrets
You may want to see also
Double Flare Design: The double flare design provides a secure connection and prevents fuel leaks
The double flare design is an innovative feature in fuel lines that significantly enhances the safety and reliability of fuel systems. This design concept involves creating a unique connection point between the fuel line and the fuel tank or other components. The primary purpose of this design is to ensure a robust and leak-proof connection, which is crucial for maintaining the integrity of the fuel system and preventing potential hazards.
In traditional fuel lines, connections are often made using various types of fittings or clamps, which may not always provide a tight seal. Over time, these connections can loosen or become compromised due to factors like vibration, temperature changes, or corrosion. As a result, fuel leaks can occur, leading to potential engine damage, environmental contamination, and even safety risks.
The double flare design addresses these concerns by incorporating a double-flanged connection. This design involves creating a flared or expanded section at the end of the fuel line, which then mates with a corresponding flared section on the fuel tank or component. The flares are typically made of durable materials and are designed to create a mechanical lock, ensuring a secure and tight seal. This double-flare connection provides several advantages. Firstly, it offers a more robust and reliable seal compared to traditional connections, reducing the risk of fuel leaks. The mechanical lock created by the flares provides a physical barrier that resists movement and maintains the integrity of the connection.
Secondly, the double flare design is highly resistant to external factors that could compromise the connection. It can withstand vibrations and temperature fluctuations commonly experienced in vehicles, ensuring that the fuel system remains secure and leak-free over an extended period. This feature is particularly important in high-performance or heavy-duty applications where fuel systems are subjected to more demanding conditions.
Furthermore, the double flare design simplifies the installation process. The flared sections allow for easier alignment and connection, reducing the time and effort required for assembly. This simplicity in design also contributes to the overall reliability of the fuel system, as there are fewer potential points of failure. In summary, the double flare design is a valuable innovation in fuel line technology, offering a secure and leak-proof connection that enhances the safety and performance of fuel systems. Its ability to withstand various environmental factors and simplify installation makes it an excellent choice for both automotive and industrial applications where fuel efficiency and safety are paramount.
F150 Fuel Line Removal: A Step-by-Step Guide for 2010 Models
You may want to see also
Fitting Compatibility: Ensure the double flare fits the specific fuel line and engine requirements
When working with fuel lines, especially those featuring a double flare design, ensuring proper fitting compatibility is crucial for optimal performance and safety. The double flare, a specific type of connection, is designed to securely attach fuel lines to various components, such as fuel tanks, pumps, and engines. This connection method is essential for maintaining a reliable fuel supply and preventing leaks, which could lead to dangerous situations.
The process of ensuring fitting compatibility begins with understanding the specific requirements of your fuel line and engine system. Each engine model and fuel line configuration may have unique specifications, including the diameter, material, and length of the fuel line, as well as the dimensions and threading of the double flare connection. It is imperative to consult the manufacturer's guidelines or technical manuals to identify the precise dimensions and standards that your fuel line and double flare should meet.
Once you have gathered the necessary information, you can proceed with the fitting process. Start by inspecting the double flare for any signs of damage or wear. Ensure that the flare is intact and free from any bends or distortions that could affect its functionality. Then, carefully align the double flare with the corresponding port or connection point on the fuel line and engine. Pay close attention to the orientation and ensure that the flare is positioned correctly to provide a secure seal.
During the fitting process, it is essential to use the appropriate tools and techniques. This may include fuel line connectors, crimping tools, or specialized equipment designed for double flare connections. Follow the manufacturer's instructions for each tool and ensure that you apply the correct amount of force or pressure to create a tight and reliable connection. Over-tightening can damage the fuel line or double flare, while under-tightening may result in a weak connection.
After the fitting process, it is crucial to test the system for any leaks. This can be done by applying pressure to the connections and observing for any signs of fuel escaping. Additionally, consider running the engine and monitoring for any unusual noises or vibrations that could indicate a poorly fitted double flare. If any issues are detected, carefully inspect the connections and make the necessary adjustments or replacements to ensure a secure and compatible fit.
By carefully considering the specific requirements of your fuel line and engine, inspecting the double flare, using appropriate tools, and testing for leaks, you can ensure that the double flare fitting is compatible and reliable. This attention to detail will contribute to the overall performance and safety of your fuel system.
Aztek Fuel Disconnect: Step-by-Step Guide to Removing the Center Line
You may want to see also
Installation Process: Proper installation techniques are crucial for a tight and leak-free connection
The installation of a fuel line with a double flare connection requires precision and attention to detail to ensure a secure and leak-free system. This method is commonly used in automotive applications to connect fuel tanks, pumps, and injectors, providing a reliable and efficient fuel supply. Here's a step-by-step guide to achieving a proper installation:
Preparation: Begin by gathering the necessary tools and materials, including the double flare fuel line, flare nuts, wrenches, and a cleaning agent. Ensure that the fuel line is the correct size and length for your specific application. Inspect the line for any damage or defects before proceeding. Clean the male and female ends of the fuel line to remove any dirt or debris, ensuring a proper connection.
Assembly: Start by inserting the male end of the fuel line into the female end, aligning the threads. Apply a thin layer of thread seal tape or thread-locking compound to the male threads to prevent leaks. Tighten the flare nut onto the male end using a wrench, ensuring it is secure but not overtightened. The double flare design provides a double-sealing action, so make sure the flare nut is properly seated and locked in place. Repeat this process for the other end of the fuel line, connecting it to the desired component.
Flaring Technique: The key to a successful installation is the flaring process. Use a flaring tool to create a smooth, even flare on both ends of the fuel line. Apply firm pressure to the tool, ensuring the flare is formed without any sharp edges. The flare should be tight and secure, creating a reliable seal. Check for any gaps or imperfections in the flare and re-flare if necessary.
Leak Testing: After assembly, it is crucial to test for leaks. Fill the fuel line with a suitable fluid, such as diesel or engine oil, and check for any signs of leakage. Inspect the connections and flares carefully. If a leak is detected, carefully disassemble the connection, clean the surfaces, and re-install, ensuring all components are properly aligned and tightened.
Final Steps: Once the installation is complete and leak-free, secure the fuel line with clamps or brackets to prevent movement. Double-check all connections and ensure they are tight and aligned. Verify that the fuel line is free from any obstructions and that the flow of fuel is unrestricted. Proper installation and regular maintenance will contribute to a reliable and long-lasting fuel system.
Fix Clogged Fuel Lines: A Step-by-Step Guide to Getting Your Car Running Again
You may want to see also
Maintenance and Inspection: Regular checks and maintenance can extend the life of the fuel line
Fuel lines, especially those with a double flare design, are crucial components in any vehicle's fuel system. These lines are responsible for transporting fuel from the tank to the engine, and their integrity is vital for optimal engine performance and safety. Regular maintenance and inspections are essential to ensure the longevity and reliability of these fuel lines.
Over time, fuel lines can experience wear and tear due to various factors such as fuel contamination, temperature changes, and mechanical stress. The double flare connection, which provides a secure and leak-resistant seal, can also be susceptible to damage or degradation. Regular checks are therefore imperative to identify any potential issues before they escalate into major problems.
Maintenance routines should include visual inspections to look for any signs of damage, corrosion, or leaks. Check for cracks, brittleness, or any visible deterioration along the fuel line's length. Pay close attention to the double flare connections, ensuring they are tight and free from any signs of leakage. It is recommended to use a soapy water solution to test for leaks, as even small leaks can lead to engine misfires, reduced performance, and potential safety hazards.
In addition to visual inspections, it is beneficial to perform pressure tests on the fuel system. This can help identify any potential weaknesses or blockages in the fuel lines. By applying pressure and monitoring for any drops or abnormalities, you can ensure the system's integrity. Regular maintenance also involves checking the fuel filter, as a clogged filter can restrict fuel flow and cause engine issues.
Furthermore, keeping the fuel tank clean is essential. Over time, fuel can accumulate contaminants, such as water, sediment, or varnish. These contaminants can damage the fuel line and injectors, leading to performance issues. Regularly draining and cleaning the fuel tank can help prevent these problems and ensure the overall health of the fuel system. By following these maintenance practices, you can significantly extend the lifespan of your fuel lines and maintain a reliable and efficient vehicle.
Mopar Fuel Line Replacement: A Step-by-Step Guide for a Smooth Engine
You may want to see also
Frequently asked questions
A fuel line double flare is a type of connection used in fuel systems, typically for high-pressure applications. It involves a double-threaded flare, where the fuel line is crimped and flared twice, creating a secure and leak-resistant joint. This design provides extra strength and reliability, making it ideal for fuel systems in vehicles or aircraft.
Double flare connections are often used in fuel lines to ensure a tight and secure seal. The additional flare provides extra holding power, making it suitable for high-pressure fuel systems. This design helps prevent fuel leaks, which can be dangerous and cause engine performance issues. It is a common choice for professional mechanics and fuel system enthusiasts.
Installing a double flare fuel line requires careful preparation and the right tools. First, ensure the fuel line and flare nut are clean and free of debris. Then, thread the flare nut onto the fuel line, tightening it by hand. Use a flare tool to crimp and flare the nut, making sure to follow the manufacturer's instructions. Repeat this process for the second flare, and test the connection for leaks. Proper installation is crucial for the safety and efficiency of your fuel system.