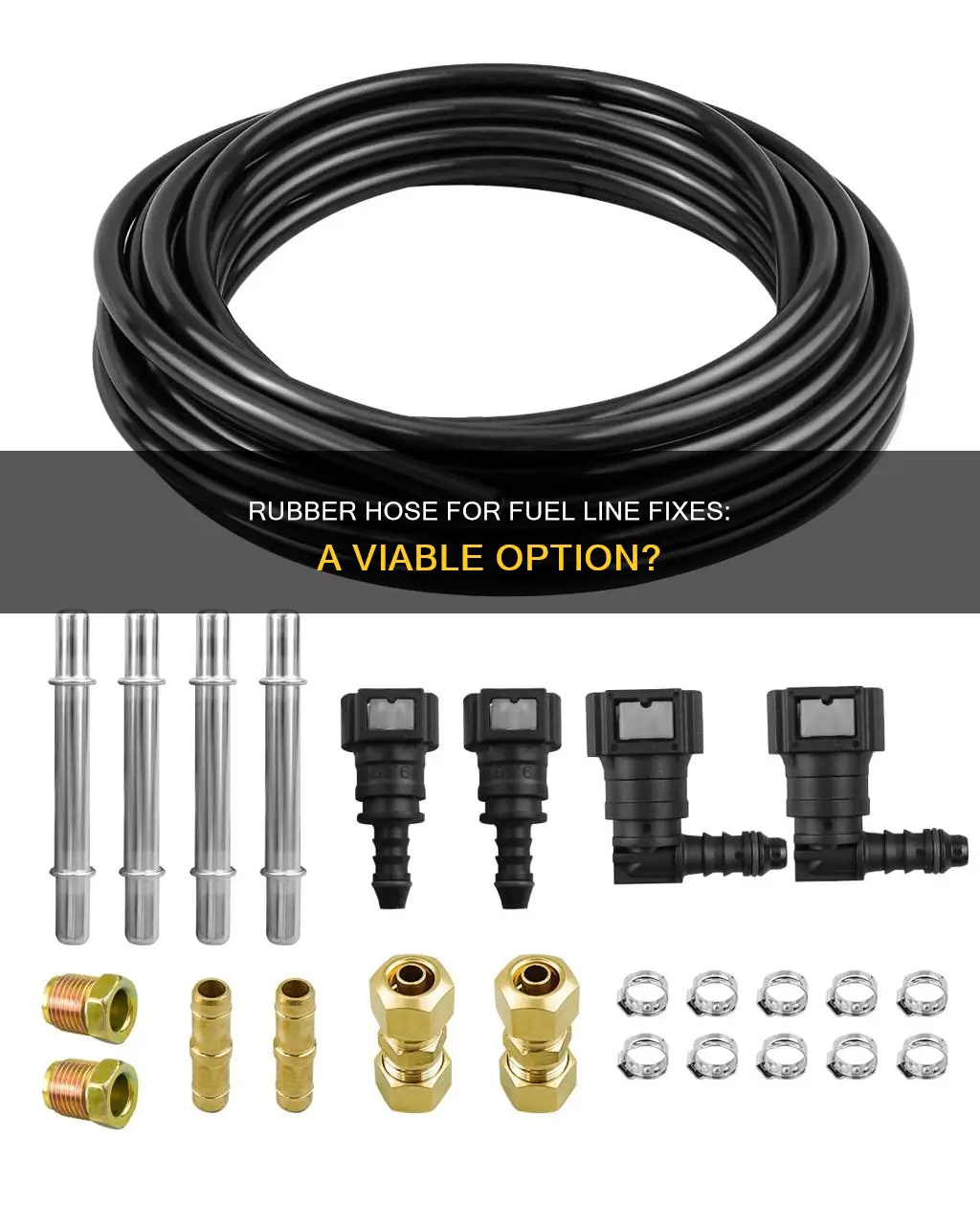
When it comes to repairing fuel lines, it's important to use the right materials to ensure a safe and effective fix. While rubber hoses might seem like a convenient option, they are not typically recommended for fuel line repairs due to their potential to crack or degrade over time, especially when exposed to fuel's harsh chemicals. This can lead to fuel leaks, which pose serious safety risks. Instead, specialized fuel line repair kits or professional services are often the best choice to ensure a reliable and safe repair.
Characteristics | Values |
---|---|
Material Compatibility | Rubber hoses are generally not suitable for fuel lines due to the risk of fuel permeation and degradation over time. |
Flexibility | Rubber hoses offer good flexibility, which can be beneficial for reaching tight spaces and bends in the fuel lines. |
Temperature Resistance | The temperature range of rubber hoses is typically limited, and they may not withstand extreme temperatures, which can cause cracking and failure. |
Chemical Resistance | Rubber hoses are not resistant to most fuels, especially those containing ethanol or blends with higher alcohol content. |
Longevity | Rubber hoses may not provide a long-term solution for fuel line repairs as they can deteriorate and become brittle over time. |
Cost | Using rubber hoses for fuel line repairs might be a temporary fix, but it is generally not recommended for a permanent solution due to the potential risks. |
Availability | Rubber hoses are widely available and relatively inexpensive, making them a common choice for temporary repairs. |
Ease of Installation | Rubber hoses can be easily connected and disconnected, providing a quick fix for temporary repairs. |
What You'll Learn
- Hose Material: Rubber's compatibility with fuel, its flexibility, and durability for fuel line repairs
- Hose Diameter: Ensuring proper fit for fuel lines, considering flow rate and pressure
- Hose Length: Determining the right length for fuel line replacement, considering accessibility and routing
- Hose Connections: Methods for securely attaching rubber hoses to fuel lines, ensuring leak-tight seals
- Hose Reinforcement: Techniques to reinforce rubber hoses for fuel lines, enhancing strength and longevity
Hose Material: Rubber's compatibility with fuel, its flexibility, and durability for fuel line repairs
The compatibility of rubber hoses with fuel is a critical factor to consider when deciding whether to use them for fuel line repairs. Rubber is a versatile material, but not all types of rubber are suitable for fuel applications. Natural rubber, for instance, is not ideal due to its sensitivity to fuel additives and its tendency to degrade over time when exposed to gasoline or diesel. On the other hand, synthetic rubbers, such as neoprene and butyl, offer better resistance to fuel chemicals and are more durable. These synthetic rubbers are often preferred for fuel-related applications due to their enhanced stability and longevity.
Flexibility is another essential attribute of rubber hoses for fuel line repairs. Fuel lines often require bends and twists to navigate around various engine components, so the hose must be flexible enough to accommodate these movements without kinking or cracking. Natural rubber hoses tend to be more flexible, but they may not last as long in fuel-rich environments. Synthetic rubbers, while less flexible than natural rubber, provide better long-term performance and are less prone to breaking under stress.
Durability is a key consideration for any fuel line repair, as the system must withstand the harsh conditions of an engine's environment. Rubber hoses should be able to resist abrasion, heat, and the constant vibration and movement within the engine bay. Reinforced rubber hoses, often featuring layers of fabric or steel wire, offer improved strength and durability. These reinforced hoses are less likely to develop leaks or failures over time, ensuring a more reliable fuel supply.
When choosing a rubber hose for fuel line repairs, it's essential to consider the specific fuel type and the operating conditions. For example, hoses used in high-performance engines or those exposed to extreme temperatures may require specialized materials with enhanced resistance to fuel degradation and heat. Additionally, the hose's inner diameter and wall thickness should be appropriate for the fuel flow rate and pressure to ensure efficient and safe operation.
In summary, while rubber hoses can be used for fuel line repairs, careful consideration of the hose material's compatibility with fuel, flexibility, and durability is necessary. Synthetic rubbers, such as neoprene and butyl, offer superior performance in fuel-rich environments due to their resistance to fuel chemicals and improved longevity. Reinforced hoses provide added strength, ensuring a more reliable fuel supply. By selecting the right rubber hose, you can ensure a safe and effective repair, maintaining the integrity of your fuel system.
Saito 180 Fuel Line: Size Guide for Optimal Performance
You may want to see also
Hose Diameter: Ensuring proper fit for fuel lines, considering flow rate and pressure
When considering using rubber hoses to repair fuel lines, one of the critical factors to evaluate is the hose diameter. The diameter of the hose plays a significant role in ensuring a proper fit and optimal performance for fuel lines. Here's a detailed guide on how to approach this:
Understanding Flow Rate and Pressure: Fuel lines require a specific flow rate and pressure to deliver fuel efficiently to the engine. The flow rate determines how much fuel can pass through the line per unit of time, while pressure ensures the fuel is delivered at the right force to overcome any potential vacuum or resistance. Rubber hoses have inherent flexibility, which can be advantageous for accommodating slight bends and vibrations. However, this flexibility must be balanced with the need for a secure fit.
Hose Diameter and Fuel Line Requirements: The diameter of the rubber hose should match or exceed the diameter of the fuel line it will replace. A smaller hose diameter can lead to reduced flow rate and pressure, potentially causing fuel starvation or inefficient operation. It is essential to consult the vehicle's manual or manufacturer specifications to determine the correct fuel line diameter. This information will guide you in selecting a hose that provides an adequate cross-sectional area for fuel flow.
Calculating Flow Rate: To ensure a proper fit, you can calculate the required flow rate based on the engine's power output and fuel consumption. Higher-performance engines may demand a more substantial flow rate to meet their fuel needs. By knowing the desired flow rate, you can estimate the minimum hose diameter required to handle the fuel volume effectively. This calculation involves considering factors like fuel pressure, line length, and any potential restrictions.
Pressure Considerations: Rubber hoses have a specific pressure rating, and it's crucial to choose a hose that can withstand the pressure of the fuel system. Fuel lines often operate under varying pressure conditions, especially during acceleration and deceleration. Selecting a hose with a pressure rating higher than the system's maximum pressure ensures a safe and reliable repair. This consideration is vital to prevent hose failure and potential fuel leaks.
In summary, when using rubber hoses to repair fuel lines, the hose diameter is a critical aspect that ensures a proper fit and optimal performance. By understanding the flow rate and pressure requirements, and matching the hose diameter accordingly, you can effectively repair fuel lines while maintaining the integrity and efficiency of the fuel delivery system. Always refer to manufacturer guidelines and specifications for the best results.
Flue Liner Sizing Guide: Choosing the Right Fit for Your Multi-Fuel Stove
You may want to see also
Hose Length: Determining the right length for fuel line replacement, considering accessibility and routing
When replacing fuel lines, determining the correct hose length is crucial for a successful and safe installation. The length of the hose should be carefully calculated to ensure it provides adequate coverage while also being easily accessible for maintenance and repairs. Here's a guide to help you determine the right hose length:
Assess the Current Setup: Start by carefully examining the existing fuel lines in your vehicle. Measure the length of the lines from the fuel tank to the engine, noting any bends or turns along the route. This will give you a baseline understanding of the distance the new hose needs to cover. Consider the position of the fuel tank, the engine's location, and any potential obstacles or constraints in the vehicle's interior.
Consider Accessibility: The hose should be long enough to allow easy access for maintenance and inspections. You want to ensure that the ends of the hose can be reached without removing any panels or accessing hard-to-reach areas. A good rule of thumb is to add a few extra inches to the measured length to account for any potential adjustments or movement during operation. This extra length will also provide some flexibility in case the hose needs to be adjusted over time.
Routing and Clearances: When planning the hose's route, consider the path it will take from the fuel tank to the engine. Ensure that the hose has sufficient clearance from the vehicle's frame, suspension components, and other moving parts. Proper routing will prevent damage to the hose and ensure its longevity. Allow for any necessary bends or turns while maintaining a smooth and continuous path to avoid stress points that could lead to leaks or damage.
Testing and Adjustment: After installing the new hose, test the system to ensure there are no leaks. If the hose is too short, you may need to adjust the routing or consider extending it. In some cases, you can use hose clips or ties to secure the hose in place and optimize its length. Remember that the goal is to achieve a secure and reliable connection without compromising accessibility for future maintenance.
By carefully measuring, considering accessibility, and planning the hose's route, you can ensure that the fuel line replacement is done correctly, providing a safe and efficient fuel supply to your engine.
Can Brake Lines Be Used for Fuel Lines? Exploring the Feasibility
You may want to see also
Hose Connections: Methods for securely attaching rubber hoses to fuel lines, ensuring leak-tight seals
When it comes to repairing fuel lines, using rubber hoses can be a practical solution, but ensuring a secure and leak-tight connection is crucial to prevent any potential hazards. Here are some methods to achieve reliable hose connections for your fuel lines:
- Compression Fittings: One of the most common and effective ways to connect rubber hoses to fuel lines is by using compression fittings. These fittings consist of a nut and a ferrule, which is a metal sleeve with a tapered inner surface. The process involves inserting the hose into the ferrule and then tightening the nut hand-tight. As you tighten the nut, the ferrule compresses the hose material, creating a tight seal. Ensure that the ferrule is the correct size for the hose diameter and made of a suitable material, often brass or bronze, to withstand fuel pressures. Always lubricate the hose and fitting threads to facilitate assembly and prevent damage to the hose.
- Clamps and Bands: Another method is to use hose clamps or bands, which provide a secure and adjustable connection. Hose clamps are typically made of metal and have a C-shaped design. You place the hose inside the clamp, ensuring it is centered, and then tighten the clamp by hand or with a tool. The clamp's pressure holds the hose in place, creating a leak-tight seal. For fuel lines, use hose clamps rated for fuel applications, as regular hose clamps may not withstand the corrosive nature of fuel. Ensure the hose is clean and free of debris before clamping to avoid damage.
- Crimping: Crimping is a process where a special tool is used to deform the end of the hose and create a seal. This method is often used for custom-made or specialized connections. The hose is inserted into a ferrule, and then the crimping tool is applied, deforming the ferrule and the hose material, creating a secure bond. Crimping requires precision and specialized tools, making it more suitable for professional mechanics.
- Adhesives and Sealants: While not a primary method for fuel line connections, using the right adhesives and sealants can provide additional security. Apply a suitable fuel-resistant adhesive or sealant to the hose and fuel line before making the connection. This can help bond the materials together and create a more robust seal. However, it should not be the sole method of connection, as mechanical fasteners like compression fittings or clamps are more reliable.
Remember, when working with fuel lines, it is essential to use the correct materials and techniques to ensure safety and prevent fuel leaks. Always refer to manufacturer guidelines and consider consulting a professional for complex fuel system repairs.
Fuel Line Cracks: A Hidden Hazard
You may want to see also
Hose Reinforcement: Techniques to reinforce rubber hoses for fuel lines, enhancing strength and longevity
When it comes to repairing fuel lines, one common question that arises is whether using a rubber hose is a viable solution. While rubber hoses can be used in certain scenarios, it's important to understand the limitations and potential risks associated with this approach. Rubber hoses are generally not designed for fuel line applications and may not provide the necessary strength and durability required for long-term use. However, there are techniques to reinforce rubber hoses, making them more suitable for fuel line repairs.
One effective method of reinforcement is the use of metal braiding or wire reinforcement. This technique involves wrapping a metal wire or braid around the rubber hose to provide additional strength and flexibility. The metal reinforcement helps to distribute the stress and pressure evenly along the hose, preventing it from cracking or leaking over time. This method is particularly useful for fuel lines that are subjected to high pressure or extreme temperatures. By incorporating metal reinforcement, the rubber hose can withstand the demanding conditions of a fuel system, ensuring a reliable and long-lasting repair.
Another approach to hose reinforcement is the application of specialized adhesives or bonding agents. These adhesives are designed to create a strong bond between the rubber hose and any surrounding components, such as fuel line fittings or metal pipes. By carefully adhering the hose to these surfaces, the risk of leakage is minimized, and the overall integrity of the fuel line is improved. It is crucial to choose the right adhesive for the specific rubber material and ensure proper application techniques for optimal results.
Additionally, considering the use of reinforced rubber hoses specifically designed for fuel line applications is essential. These hoses are engineered to meet the rigorous demands of fuel systems and often feature multiple layers of reinforcement, including fabric or steel wire. By opting for these specialized hoses, you can ensure a more reliable and long-lasting repair. However, it is important to consult the manufacturer's guidelines and specifications to ensure compatibility and proper installation.
In summary, while rubber hoses can be used in certain fuel line repair scenarios, reinforcement techniques are crucial to enhance their strength and longevity. Metal braiding, wire reinforcement, specialized adhesives, and the use of reinforced rubber hoses are all effective methods to ensure a successful and safe fuel line repair. By implementing these techniques, you can mitigate the risks associated with using rubber hoses and provide a more robust solution for your vehicle's fuel system.
Mastering the Quick Connect Swap: Nylon Fuel Line Guide
You may want to see also
Frequently asked questions
No, using a rubber hose for fuel line repairs is not recommended. Rubber hoses are not designed for fuel-carrying applications and may not provide a secure or reliable seal. They can degrade over time due to fuel exposure, leading to potential leaks and safety hazards.
Rubber hoses can become brittle and crack when exposed to fuel, causing leaks and potential engine damage. They may also fail to withstand the pressure and temperature changes in the fuel system, leading to system failure.
Yes, it is best to use specialized fuel line repair kits or replace the damaged section with new fuel line. These options provide a secure and reliable connection, ensuring the fuel system's integrity and safety.
While it might provide temporary relief, it is not a safe or effective long-term solution. The hose may not last, and any repairs made with it could be unreliable, potentially causing fuel leaks and engine issues.
In emergency situations, use a temporary clamp or a piece of fuel line from a spare part to secure the damaged area. However, this is only a temporary measure, and a professional repair or replacement should be done as soon as possible.