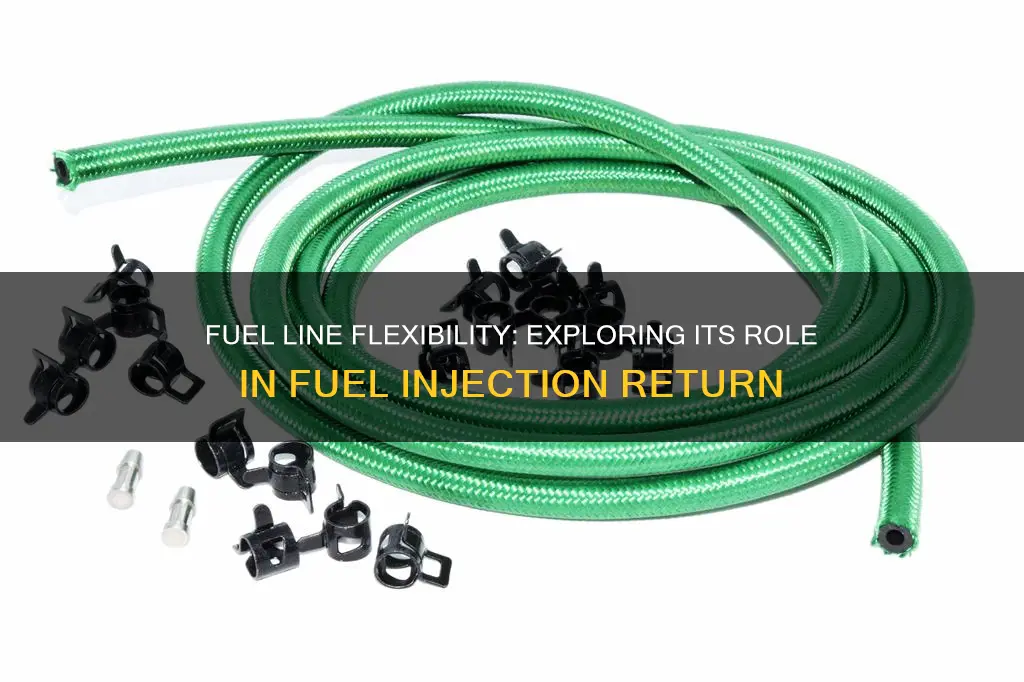
The fuel line and fuel injection return line are two distinct components in a vehicle's fuel system, and understanding their roles is crucial for proper maintenance. While the fuel line is responsible for transporting fuel from the tank to the engine, the fuel injection return line plays a different role. This line is designed to carry the unused fuel back to the fuel tank, ensuring that the engine receives only the required amount of fuel for optimal performance. This introduction sets the stage for further discussion on the compatibility and potential uses of these two lines in a vehicle's fuel system.
What You'll Learn
- Fuel Line Material: Plastic or rubber fuel lines can be used for fuel injection return lines
- Pressure Compatibility: Ensure fuel lines can withstand the pressure of the fuel injection system
- Flexibility: Flexible fuel lines are ideal for the return line's dynamic nature
- Compatibility with Fuel: Choose lines resistant to fuel degradation and contamination
- Installation and Routing: Proper installation and routing prevent damage and ensure optimal performance
Fuel Line Material: Plastic or rubber fuel lines can be used for fuel injection return lines
When it comes to fuel injection systems, the choice of materials for fuel lines is crucial to ensure optimal performance and longevity. While metal fuel lines are commonly used, plastic or rubber fuel lines can also be utilized for fuel injection return lines, offering certain advantages. These flexible materials can accommodate the dynamic nature of the fuel system, especially in high-performance engines where vibrations and movements are more pronounced.
Plastic fuel lines, often made from materials like nylon or polyetheretherketone (PEEK), provide excellent chemical resistance, ensuring that the fuel remains pure and free from contamination. This is particularly important in fuel injection systems, where any impurities can negatively impact engine performance. Additionally, plastic lines are lightweight, reducing the overall weight of the fuel system, which can be beneficial for high-performance applications. They also offer good flexibility, allowing them to follow the contours of the engine bay without restricting movement.
Rubber fuel lines, on the other hand, offer superior vibration damping properties. The natural elasticity of rubber absorbs engine vibrations, reducing the risk of fuel line damage and ensuring a more secure connection. This is especially important in high-performance vehicles where engine vibrations can be intense. Rubber lines are also known for their flexibility, making installation easier and providing a more adaptable solution for complex engine layouts.
Both plastic and rubber fuel lines can be an excellent choice for fuel injection return lines, especially in retrofits or custom builds. These materials offer a balance of performance, durability, and ease of installation. However, it is essential to consider the specific requirements of the engine and the fuel system. Factors such as temperature range, fuel type, and engine vibrations should be taken into account to ensure the chosen material can withstand the operating conditions.
In summary, while metal fuel lines are prevalent, plastic or rubber fuel lines can be effectively used for fuel injection return lines, providing flexibility, chemical resistance, and vibration damping. The choice between the two depends on the specific engine requirements and the desired performance characteristics. With the right material selection, fuel injection systems can operate efficiently and reliably, delivering the power and performance expected from modern engines.
Miata Fuel Line Sizes: A Comprehensive Guide
You may want to see also
Pressure Compatibility: Ensure fuel lines can withstand the pressure of the fuel injection system
When considering the use of fuel lines for fuel injection return lines, it is crucial to prioritize pressure compatibility to ensure optimal performance and safety. The fuel injection system generates significant pressure to deliver fuel to the engine, and the fuel lines must be able to withstand this pressure to prevent any potential issues.
The pressure in a fuel injection system can vary depending on the engine design and operating conditions. Typically, the system operates at relatively high pressures, often ranging from 100 to 300 psi (pounds per square inch) or even higher in some cases. These pressures are necessary to ensure efficient fuel atomization and proper engine operation. Therefore, the fuel lines used for the return line should be designed and selected with pressure compatibility in mind.
To ensure pressure compatibility, it is essential to choose fuel lines with a suitable pressure rating. The pressure rating of a fuel line indicates the maximum pressure it can withstand without failing or leaking. When selecting fuel lines, look for those specifically designed for fuel injection systems, as they are engineered to handle the expected pressure ranges. These lines often feature reinforced construction, such as braided or steel-reinforced hoses, to provide the necessary strength and flexibility while maintaining pressure integrity.
Additionally, consider the material of the fuel lines. Different materials offer varying levels of pressure resistance. For instance, high-pressure fuel lines often use materials like stainless steel or high-strength polymers that can withstand the demanding conditions of the fuel injection system. These materials provide excellent durability and resistance to pressure-related degradation over time.
In summary, when using fuel lines for fuel injection return lines, it is imperative to prioritize pressure compatibility. Selecting fuel lines with an appropriate pressure rating and choosing materials that can handle the system's pressure requirements are essential steps. By ensuring pressure compatibility, you can guarantee the reliable and safe operation of the fuel injection system, minimizing the risk of fuel leaks, system failures, or engine performance issues.
Poulin Chainsaw Fuel Line: Size Guide for Optimal Performance
You may want to see also
Flexibility: Flexible fuel lines are ideal for the return line's dynamic nature
The concept of using fuel lines for fuel injection return lines is an interesting one, especially when considering the dynamic nature of these systems. The return lines in a fuel injection system are responsible for transporting the fuel from the injectors back to the fuel tank or reservoir, often under varying pressure and flow conditions. This dynamic behavior can be challenging for traditional rigid fuel lines, which may become stiff and less flexible over time due to the constant movement and vibration within the engine bay.
Flexible fuel lines offer a solution to this problem. These lines are designed with a specific focus on flexibility, allowing them to move and bend more easily without compromising the integrity of the fuel flow. The dynamic nature of the return lines means that they need to accommodate changes in direction, engine movement, and varying pressure levels. Flexible fuel lines can easily conform to these changes, ensuring a consistent and reliable fuel supply to the injectors.
In the engine bay, where space is often limited and the environment can be harsh, flexibility becomes even more critical. The return lines may need to navigate around various engine components, such as the transmission, exhaust system, or even the air intake. Flexible fuel lines can easily bend and adjust to these obstacles, reducing the risk of damage and ensuring a smooth and efficient fuel return process.
Furthermore, the use of flexible fuel lines can improve the overall longevity of the fuel injection system. By allowing for more natural movement and reducing the stress on the lines, they are less likely to develop cracks, leaks, or other forms of damage over time. This is particularly important in high-performance applications or vehicles with rough terrain, where the engine and associated components experience more extreme conditions.
In summary, the flexibility of fuel lines is a key advantage when considering their use for fuel injection return lines. It allows for better adaptability to the dynamic nature of the system, ensuring consistent fuel delivery and potentially extending the lifespan of the fuel injection setup. This approach can be a valuable consideration for engineers and enthusiasts looking to optimize their vehicle's performance and reliability.
Fox Fuel Lines: Compatibility with Ford SN95 Models
You may want to see also
Compatibility with Fuel: Choose lines resistant to fuel degradation and contamination
When considering the use of a fuel line for a fuel injection return line, it is crucial to prioritize compatibility with the fuel being used. The choice of fuel line material and construction should be based on its ability to withstand the specific fuel's chemical properties and potential for degradation. Fuel lines play a critical role in the fuel system, and their compatibility with the fuel is essential to ensure optimal performance and longevity.
One of the primary concerns is the resistance of the fuel line to fuel degradation. Different fuels, such as gasoline, diesel, or alternative fuels like ethanol blends, have varying compositions and chemical properties. Over time, these fuels can degrade the materials used in fuel lines, leading to potential issues. For instance, gasoline contains volatile organic compounds (VOCs) that can dissolve certain plastics, causing them to deteriorate. Similarly, diesel fuel's higher sulfur content can accelerate the aging of rubber fuel lines. Therefore, selecting a fuel line material that is resistant to the specific fuel's degradation factors is vital.
Additionally, the choice of fuel line should consider its ability to prevent fuel contamination. Contaminants like water, dirt, and debris can enter the fuel system and cause performance issues. Some fuel lines are designed with features like integrated filters or anti-surge mechanisms to minimize contamination risks. These features help ensure that the fuel injected into the engine is clean and free from any harmful substances that could lead to engine damage.
To ensure compatibility, it is recommended to consult the vehicle's manual or seek expert advice. Different engines and fuel systems may require specific fuel line materials and specifications. Using the right fuel line can prevent fuel leaks, maintain engine performance, and extend the overall lifespan of the fuel system components.
In summary, when using a fuel line for a fuel injection return line, compatibility with the fuel is paramount. Choosing materials that resist fuel degradation and contamination is essential to ensure the fuel system's reliability and performance. Proper selection will contribute to a well-maintained and efficient engine, providing peace of mind to vehicle owners.
Fuel Line Removal: A Guide for 87 Crown Victoria Owners
You may want to see also
Installation and Routing: Proper installation and routing prevent damage and ensure optimal performance
When considering the use of a fuel line as a fuel injection return line, proper installation and routing are crucial to ensure the system's longevity and optimal performance. This is especially important given the high pressure and temperature variations that fuel lines and fuel injection systems experience. Here's a detailed guide on how to approach this installation:
Preparation and Tools: Before beginning the installation, ensure you have the necessary tools and materials, including the fuel line, fittings, clamps, and any required adapters. It is essential to use high-quality components that can withstand the demands of the fuel system. Additionally, have a workshop manual specific to your vehicle's make and model, as it will provide detailed diagrams and instructions tailored to your car.
Routing and Placement: Proper routing is critical to prevent damage and ensure the system's efficiency. The fuel line should be routed away from heat sources, such as exhaust manifolds and engine components, to avoid overheating. Keep the line as straight as possible to minimize stress on the material. Avoid sharp bends or kinks, as these can restrict fuel flow and lead to potential leaks. Route the line through the engine bay, ensuring it is not pinched or caught between moving parts.
Fitting and Clamping: When connecting the fuel line to the fuel injection system, use appropriate fittings and ensure they are tightened securely. The fittings should be compatible with the fuel line material to prevent corrosion or leaks. Apply a suitable clamp to secure the line, ensuring it is tight enough to prevent any movement but not so tight that it causes damage to the line or surrounding components.
Testing and Inspection: After installation, thoroughly test the system to ensure there are no leaks. Check for any signs of fuel leakage around connections and fittings. Inspect the route for any visible damage or wear, especially in areas where the line passes through tight spaces or under the vehicle. Regularly inspect the system, especially if you notice any changes in engine performance or fuel efficiency.
Maintenance and Care: Proper maintenance is key to the long-term success of this installation. Regularly check for any signs of deterioration, such as cracks, brittleness, or corrosion. Keep the fuel line clean and free of debris, especially if it passes through areas with high dust or contamination. Ensure that all connections remain tight and secure over time.
By following these installation and routing guidelines, you can effectively utilize a fuel line as a fuel injection return line, ensuring a reliable and efficient fuel system. Proper care and attention to detail will contribute to the overall performance and longevity of your vehicle's fuel injection system.
Fuel Line: Understanding the Difference Between ID and OD Measurements
You may want to see also
Frequently asked questions
Yes, a fuel line can be utilized for the fuel injection return line, but it's important to consider the specific requirements and compatibility with the vehicle's fuel system. Fuel lines are designed to handle fuel pressure and temperature changes, so using a suitable fuel line for the return line is essential to ensure proper functionality and prevent potential issues.
Using a fuel line for the return line can offer several benefits. It provides a dedicated path for the fuel to flow back to the fuel tank or the fuel pump, ensuring efficient and controlled fuel management. This setup can improve fuel delivery, enhance engine performance, and contribute to better fuel economy.
While using a fuel line for the return line can be advantageous, there are a few considerations. The fuel line should be compatible with the fuel type and temperature range of the vehicle. Inadequate sizing or material choice might lead to fuel leaks or reduced performance over time. Proper installation and regular maintenance are crucial to avoid these issues.
To find the right fuel line, you should consult the vehicle's manual or seek advice from a professional mechanic. They can guide you on the specific requirements, including fuel line diameter, material, and any unique features needed for your car's fuel system. Using the correct specifications will ensure a reliable and safe fuel injection return line setup.
Modifying an existing fuel line is possible, but it should be done with caution and expertise. Ensure that the fuel line is in good condition and compatible with the return line's requirements. Proper modifications might include resizing the fuel line, adding fittings, or making adjustments to the fuel system's layout. It is recommended to seek professional assistance to ensure the modifications are safe and effective.