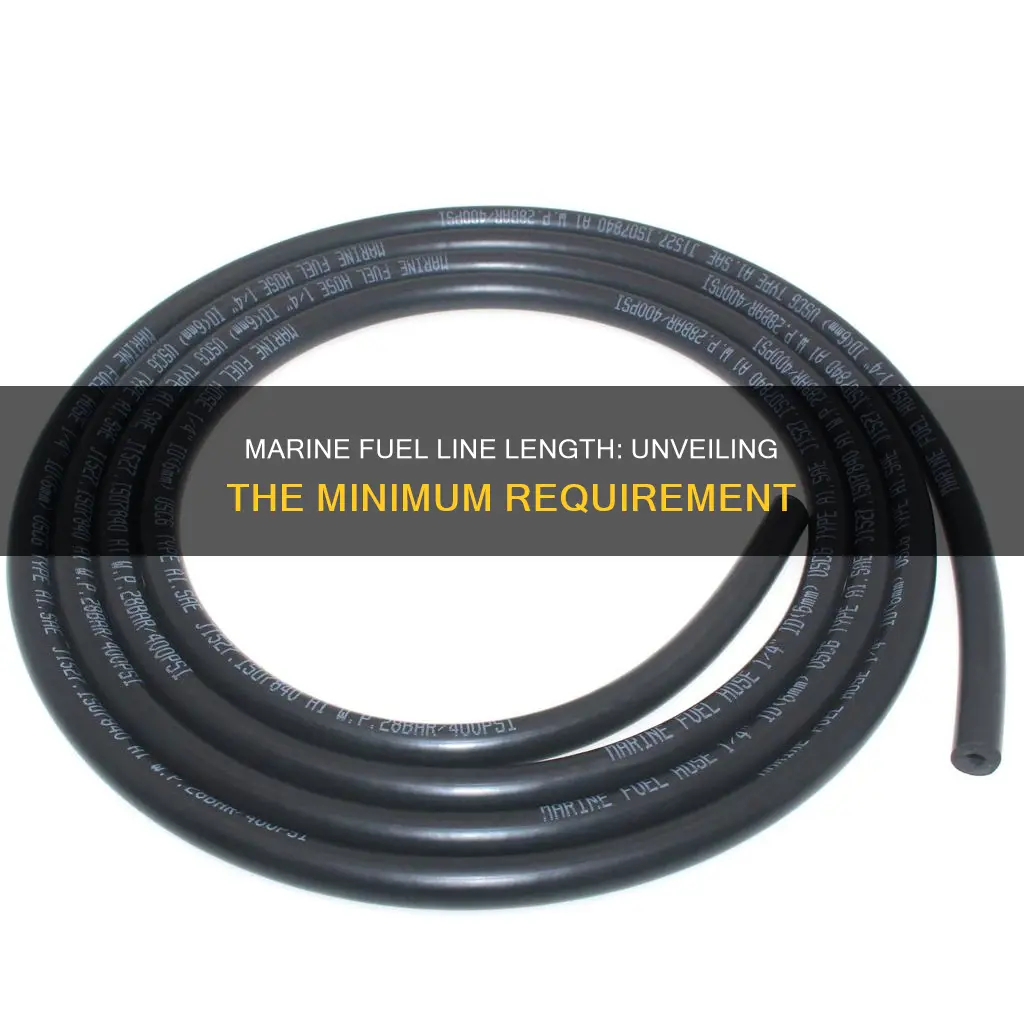
When it comes to marine fuel lines, a common question arises: is there a minimum length requirement? This is an important consideration for boat owners and marine engineers, as fuel lines that are too short can lead to performance issues and potential safety hazards. Understanding the minimum length requirements for marine fuel lines is crucial to ensure optimal fuel delivery and prevent fuel-related problems. In this discussion, we will explore the factors that determine the appropriate length of fuel lines and the benefits of adhering to these guidelines.
What You'll Learn
- Material and Construction: Fuel lines must be made from durable materials like stainless steel or high-density polyethylene
- Diameter and Flow Rate: Line diameter should be chosen based on the required flow rate and pressure
- Flexibility and Bend Radius: Lines need to be flexible enough to bend around obstacles without kinking
- Pressure Rating: Lines must be rated to handle the maximum pressure expected in the marine environment
- Compliance and Standards: Fuel lines should meet industry standards and regulations for marine applications
Material and Construction: Fuel lines must be made from durable materials like stainless steel or high-density polyethylene
When it comes to marine fuel lines, the choice of material is critical to ensure durability and reliability in harsh marine environments. The primary requirement is to select materials that can withstand the corrosive effects of saltwater, UV radiation, and temperature fluctuations. Stainless steel and high-density polyethylene (HDPE) are the preferred choices for fuel lines in marine applications.
Stainless steel is renowned for its exceptional strength and corrosion resistance. It is an ideal material for fuel lines as it can handle the challenges posed by marine environments. The stainless steel used in fuel lines is often 316L, which offers superior resistance to chloride-induced stress corrosion, making it perfect for saltwater applications. This material is also known for its ability to withstand high temperatures and pressure, ensuring the safe and efficient transfer of fuel.
High-density polyethylene, or HDPE, is another excellent option for marine fuel lines. HDPE is a lightweight, flexible, and durable plastic that provides excellent resistance to chemicals and UV radiation. Its ability to withstand temperature variations makes it suitable for a wide range of marine conditions. HDPE fuel lines are often used in recreational boats and smaller vessels where weight and flexibility are essential considerations.
The construction of these fuel lines should also be carefully considered. Stainless steel fuel lines are typically made with a braided design, providing excellent flexibility and kink resistance. The braiding also helps distribute the material's inherent stiffness, allowing for easy installation and routing. HDPE fuel lines, on the other hand, are often flexible and can be more easily bent, making them ideal for tight spaces and complex layouts.
In summary, when designing or selecting fuel lines for marine applications, the focus should be on using durable materials like stainless steel or HDPE. These materials ensure the fuel lines can withstand the demanding conditions of marine environments, providing long-lasting performance and safety. The choice of material and construction directly impacts the overall reliability and efficiency of the fuel system, making it a critical aspect of marine vessel design and maintenance.
Stihl FS80 Fuel Line Size: Expert Guide
You may want to see also
Diameter and Flow Rate: Line diameter should be chosen based on the required flow rate and pressure
When designing a marine fuel line system, one of the critical factors to consider is the diameter of the fuel line. The diameter is a fundamental aspect that directly influences the flow rate and pressure characteristics of the system. Here's a detailed explanation of how diameter and flow rate are related and why it matters:
The flow rate of a fluid, in this case, marine fuel, through a pipe or line is directly proportional to the cross-sectional area of the pipe. Mathematically, this relationship can be expressed as Q = A * v, where Q is the flow rate, A is the cross-sectional area, and v is the velocity of the fluid. The cross-sectional area (A) is calculated as the square of the diameter (d) of the pipe, A = π * (d/2)^2. Therefore, to achieve a higher flow rate, a larger diameter is required. This is particularly important in marine applications where fuel lines need to supply fuel efficiently to engines, especially in high-pressure environments.
The pressure drop across a pipe or line is another critical consideration. As fuel flows through the line, it experiences friction and other resistances, leading to a pressure drop. The pressure drop is inversely proportional to the diameter of the pipe. This means that a larger diameter will result in a lower pressure drop for the same flow rate. In marine fuel systems, maintaining adequate pressure is essential to ensure proper engine operation. A smaller diameter line may lead to excessive pressure drop, especially over longer distances, which can result in reduced fuel pressure at the engine, potentially causing performance issues.
To determine the appropriate diameter, engineers and designers must consider the required flow rate and the desired pressure at the engine. For instance, if a marine vessel requires a high-pressure fuel supply to its engines, a larger diameter line is necessary to minimize pressure drop and ensure the required pressure is maintained. Similarly, for applications with lower pressure requirements, a smaller diameter may be sufficient. It's important to note that the flow rate and pressure requirements can vary depending on the specific engine, vessel type, and operating conditions.
In summary, the diameter of a marine fuel line should be carefully selected based on the required flow rate and pressure. A larger diameter line provides a larger cross-sectional area, allowing for higher flow rates and lower pressure drops. This ensures that the fuel supply system can meet the demands of the engines and maintain optimal performance. Properly sizing the fuel line diameter is a critical aspect of marine engineering to guarantee efficient and reliable fuel distribution.
Mastering the Art of Unhooking LML Fuel Tank Lines: A Step-by-Step Guide
You may want to see also
Flexibility and Bend Radius: Lines need to be flexible enough to bend around obstacles without kinking
When it comes to marine fuel lines, flexibility and bend radius are crucial considerations, especially when navigating through tight spaces and around various obstacles on a vessel. The lines must be designed to withstand the natural movement and shifting of the boat while also accommodating the physical constraints of the vessel's structure. One of the primary reasons for this requirement is to prevent kinking, which can lead to fuel leaks, damage to the line, or even a complete failure of the system.
Flexibility is a measure of a material's ability to deform without breaking. In the context of marine fuel lines, this means the line should be able to twist, turn, and bend without becoming rigid or breaking. The key factor here is the material's durometer, which is a measure of its hardness. Lines with a lower durometer are more flexible and can easily conform to the shape of the surrounding environment. For marine applications, materials like rubber or flexible PVC are commonly used due to their inherent flexibility.
The bend radius is another critical factor. It refers to the radius of the smallest arc that the fuel line can follow without kinking. A smaller bend radius means the line must be able to make tighter turns, which can be challenging in confined spaces. To ensure the line doesn't kink, it should be able to bend around obstacles with a radius that is at least twice the diameter of the line. For example, a 2-inch diameter fuel line should have a minimum bend radius of 4 inches to avoid kinking.
To achieve the required flexibility and bend radius, manufacturers often employ various techniques. One common method is to incorporate flexible materials and add reinforcing layers to provide strength without compromising flexibility. Additionally, the construction of the line, such as the number of layers and the arrangement of the materials, can significantly impact its flexibility. For instance, a braided construction with multiple layers of flexible material can offer excellent bend radius capabilities.
In summary, marine fuel lines must be flexible enough to navigate around obstacles without kinking, ensuring the safety and efficiency of the fuel supply system. This is achieved through careful material selection, considering the line's durometer and bend radius, and employing construction techniques that balance flexibility and strength. By adhering to these principles, marine fuel lines can effectively operate in various environments, providing reliable fuel distribution.
Kartech Arrow Fuel Line: The Ultimate Size Guide
You may want to see also
Pressure Rating: Lines must be rated to handle the maximum pressure expected in the marine environment
When it comes to marine fuel lines, ensuring they can withstand the pressures of the marine environment is crucial. The pressure rating of these lines is a critical factor in their design and installation. Marine fuel lines are exposed to various pressures, including the force of fuel being pumped, the weight of the vessel, and the dynamic nature of the sea. Therefore, these lines must be rated to handle the maximum pressure expected in their specific application.
The pressure rating is typically determined by the manufacturer based on extensive testing and engineering calculations. It takes into account factors such as the material's strength, the diameter of the line, and the expected flow rate of the fuel. For instance, a fuel line supplying high-pressure fuel to an engine will require a higher pressure rating compared to a line used for low-pressure fuel transfer.
In the marine industry, it is common to use pressure-rated hoses and fittings specifically designed for fuel transfer applications. These components are often made from materials like rubber, PVC, or synthetic compounds, carefully selected for their ability to withstand the corrosive effects of fuel and the harsh marine environment. The pressure rating is usually indicated on the product specifications, ensuring that the installer can choose the appropriate size and type for the job.
During installation, it is essential to consider the route the fuel line will take. The line should be routed in a way that avoids sharp bends or kinks, as these can cause stress on the material and potentially reduce its pressure-handling capacity. Proper support and protection of the fuel lines are also necessary to prevent damage from abrasion, impact, or corrosion.
Regular maintenance and inspections are vital to ensure the long-term performance and safety of marine fuel lines. Over time, the lines may degrade due to UV exposure, oxidation, or other environmental factors. Therefore, it is recommended to periodically check the pressure rating and overall condition of the fuel lines to identify any signs of wear or damage that could compromise their ability to handle pressure effectively.
Mastering the Art: A Guide to Removing Fuel Lines on Your 1999 Chevy Envoy
You may want to see also
Compliance and Standards: Fuel lines should meet industry standards and regulations for marine applications
When it comes to marine fuel lines, compliance with industry standards and regulations is of utmost importance to ensure the safety and efficiency of any vessel. These standards are in place to guarantee that fuel lines are designed, manufactured, and installed to withstand the unique challenges of marine environments. One critical aspect of these standards is the requirement for a minimum length of fuel lines to prevent potential issues during operation.
The minimum length of marine fuel lines is a crucial consideration to ensure optimal performance and safety. Industry regulations often specify a minimum length to account for various factors. Firstly, it ensures that the fuel lines have sufficient length to reach the fuel tanks without excessive bending or stress, which could lead to leaks or damage over time. Secondly, it allows for proper routing, ensuring that the fuel lines are not obstructed or damaged by other components or structures within the vessel.
Compliance with standards is essential as it ensures that fuel lines are made from materials that can withstand the corrosive effects of marine environments. Marine fuel lines must be resistant to saltwater, UV radiation, and temperature fluctuations. Materials like stainless steel, brass, or specialized polymers are commonly used to meet these requirements. Additionally, the construction and design of the fuel lines should adhere to industry standards to prevent leaks and ensure a reliable fuel supply.
Regulations also dictate the installation process to maintain safety and functionality. Fuel lines must be securely fastened and protected from abrasion to prevent damage during vessel movement or operation. Proper support and insulation may be required to protect against temperature extremes and mechanical stress. Adhering to these installation standards is vital to avoid fuel leaks, which can be hazardous and environmentally detrimental.
In summary, marine fuel lines must comply with industry standards and regulations to ensure they meet the specific demands of marine environments. The minimum length requirement, along with material and installation standards, is essential for the safe and efficient operation of vessels. By adhering to these guidelines, marine engineers and operators can ensure the reliability and longevity of fuel systems, contributing to the overall safety and performance of marine vessels.
Air in Fuel Line: Impact on Diesel Engine Performance
You may want to see also
Frequently asked questions
The minimum length of marine fuel lines is typically 6 inches (152 mm) for inboard engines and 8 inches (203 mm) for outboard engines. This ensures sufficient length to reach the fuel tank from the engine without causing unnecessary strain or damage.
It is not recommended to use shorter fuel lines as it can lead to various issues. Insufficient length may result in fuel line damage due to engine vibrations, reduced fuel flow, and potential fuel leaks. Always refer to the manufacturer's guidelines for the appropriate fuel line length for your specific marine engine and vessel.
Yes, several factors can influence the minimum length of marine fuel lines. These include the engine's location, the type of fuel used, and the vessel's design. For instance, inboard engines often require longer lines to reach the fuel tank, while outboard engines may have different mounting considerations.
To ensure you have the correct length, measure the distance from the engine's fuel inlet to the fuel tank. Consider the engine's orientation and any potential obstructions. If needed, consult a marine mechanic or refer to the vessel's manual for specific recommendations. Custom-made fuel lines can also be ordered to fit unique engine configurations.