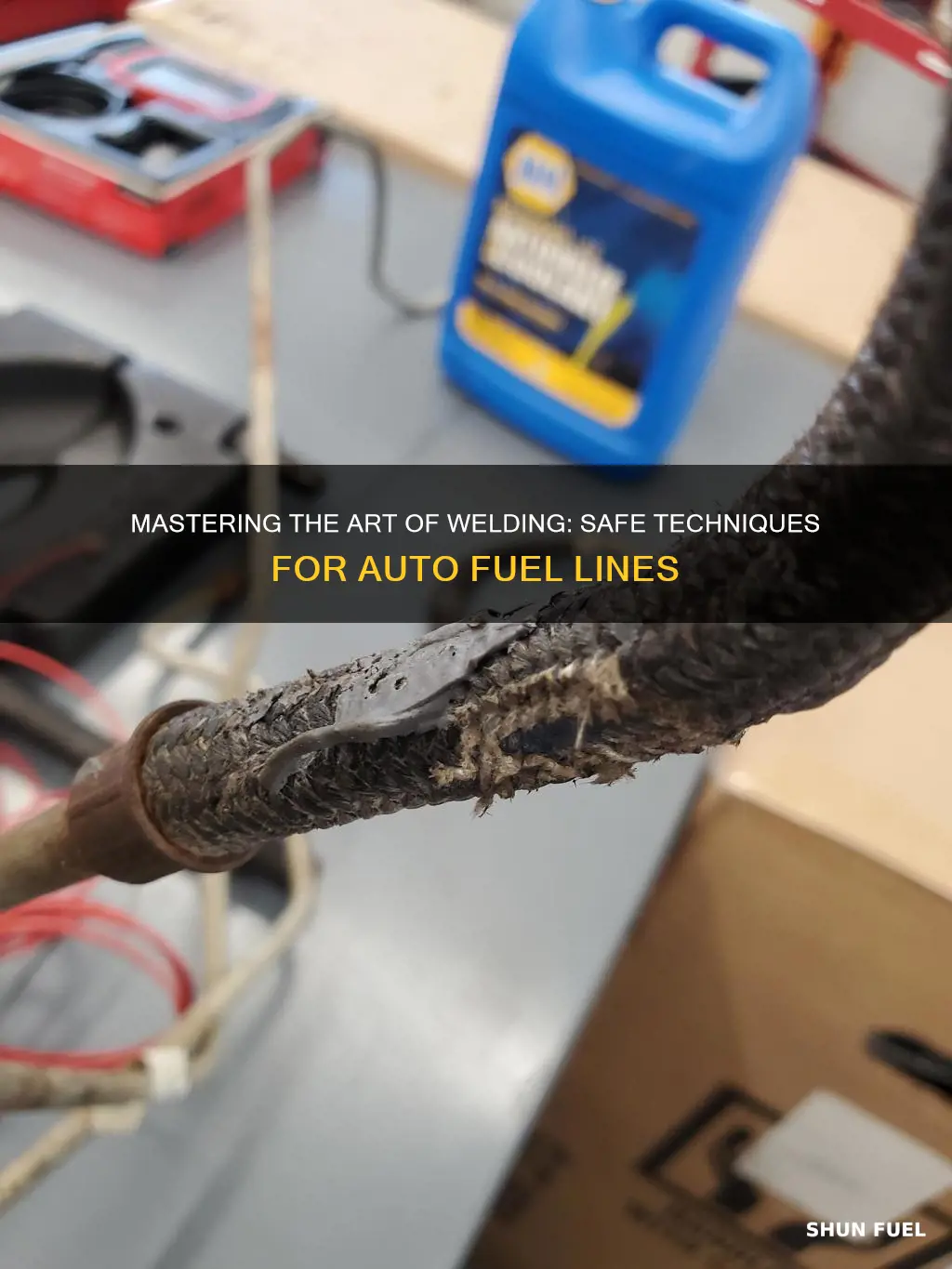
Welding near auto fuel lines requires extreme caution to prevent accidents. This guide will outline essential safety measures to ensure a secure welding process. It is crucial to understand the risks associated with fuel lines, which can cause fires or explosions if not handled properly. By following these steps, you can minimize hazards and ensure a safe working environment when welding in close proximity to fuel lines.
What You'll Learn
- Identify Fuel Lines: Locate and mark fuel lines before starting any welding to avoid accidental damage
- Use Protective Gear: Wear safety gear like gloves, goggles, and a respirator to protect against hazards
- Ventilate the Area: Ensure proper ventilation to prevent the buildup of flammable gases
- Use Non-Sparking Tools: Avoid sparks by using non-sparking tools and welding equipment
- Keep Distance: Maintain a safe distance from fuel lines and ensure no heat sources are nearby
Identify Fuel Lines: Locate and mark fuel lines before starting any welding to avoid accidental damage
Before you begin any welding or cutting operations near a vehicle's fuel system, it is crucial to identify and mark the fuel lines to prevent accidental damage. This process ensures the safety of both the vehicle and those working on it. Here's a step-by-step guide to help you locate and mark the fuel lines effectively:
- Consult the Vehicle's Manual: Start by referring to the vehicle's owner's manual or service documentation. These resources often provide detailed diagrams or illustrations of the fuel system, including the locations of fuel lines, tanks, and associated components. Understanding the layout will give you a head start in identifying the critical areas.
- Inspect the Vehicle's Exterior: Visually inspect the vehicle's exterior, paying close attention to the engine bay and any accessible areas under the hood or in the trunk. Look for visible fuel lines, hoses, and connections. In some cases, fuel lines may be routed through the engine compartment or along the vehicle's frame. Mark these locations with tape or chalk to ensure you don't accidentally cut or weld over them.
- Locate Hidden Fuel Lines: Some fuel lines may be concealed within the vehicle's interior or under panels. Carefully remove any accessible panels or trim to expose these areas. Use a bright flashlight to illuminate dark spaces and look for any signs of fuel lines or connections. Mark these spots with tape or small flags to indicate their presence.
- Use Temporary Markers: Once you've identified the fuel lines, use temporary markers to outline their paths. You can use colorful electrical tape, chalk, or even small pieces of tape with labels to indicate the start and end points of each fuel line. This visual representation will help you and your team members understand the layout and avoid any accidental damage during the welding process.
- Double-Check and Verify: Before proceeding with the welding, conduct a final inspection to ensure all fuel lines have been correctly identified and marked. Verify that no fuel lines are hidden beneath any welding or cutting points. This extra step is essential to prevent costly mistakes and potential hazards.
By following these steps, you can ensure that the fuel lines are safely identified and marked, reducing the risk of accidental damage during the welding process. Remember, safety should always be the top priority when working near a vehicle's fuel system.
Fuel Line Fixes: A Guide to Reviving Worn Hoses
You may want to see also
Use Protective Gear: Wear safety gear like gloves, goggles, and a respirator to protect against hazards
When performing any welding activity, especially near automotive fuel lines, it is crucial to prioritize safety and take the necessary precautions to minimize risks. One of the most essential aspects of ensuring a safe welding process is wearing appropriate protective gear. This gear acts as a barrier between the welder and potential hazards, providing much-needed protection.
Gloves are an essential item of protective gear for welding. They should be made of a heat-resistant material, such as leather or a specialized fabric designed for welding applications. These gloves offer protection against burns and thermal shock, which can occur when welding near fuel lines. They also provide a secure grip, allowing the welder to maintain control and precision during the process. It is important to choose gloves that fit well and allow for dexterity, ensuring that the welder can still perform tasks with ease.
Eye protection is another critical component of safety gear. Welding can produce intense light and sparks, which can cause severe eye damage. Goggles designed for welding provide a protective shield, blocking harmful radiation and debris. Look for goggles that offer UV protection and impact resistance to ensure optimal safety. Some goggles also feature a double-lens design, providing enhanced protection and a clear view of the welding area.
Respiratory protection is often overlooked but is equally vital. Welding can release fumes and gases, including hazardous ones, which can be inhaled and pose serious health risks. A respirator, specifically designed for welding environments, can filter out these harmful substances. It is important to select a respirator that fits comfortably and effectively, ensuring that the welder can breathe safely throughout the process. Modern respirators often feature advanced filtration systems and comfortable designs, making them a practical and essential part of welding safety.
In addition to these specific items, it is also advisable to wear a welding helmet with a dark shade lens to further protect the eyes and face from intense light and sparks. This additional layer of protection can significantly reduce the risk of injury. By wearing the appropriate protective gear, welders can minimize the chances of accidents, injuries, and long-term health issues associated with welding near fuel lines. It is a simple yet effective way to ensure a safer working environment.
Optimizing Fuel Delivery: Choosing the Right Fuel Line Size for 5/16 Nipple Applications
You may want to see also
Ventilate the Area: Ensure proper ventilation to prevent the buildup of flammable gases
When working near automotive fuel lines, proper ventilation is crucial to prevent dangerous situations. Welding and other heat-producing activities can release flammable gases, which, when combined with an ignition source, can lead to fires or explosions. Here's a detailed guide on how to ensure adequate ventilation in such scenarios:
Identify Potential Sources of Flammable Gases: Before starting any welding work, it's essential to understand the potential sources of flammable gases in the area. Automotive fuel lines, especially those containing gasoline or diesel, can release volatile organic compounds (VOCs) and other hazardous gases. These gases are released when fuel is pumped, spilled, or during the welding process itself if the fuel lines are damaged.
Use Industrial-Strength Ventilation Systems: To combat this issue, consider using industrial-strength ventilation systems designed for hazardous environments. These systems typically consist of powerful fans and filters that can extract and expel air, along with any accumulated flammable gases. Place the ventilation system near the welding area, ensuring it can effectively capture and remove the gases. Industrial-grade ventilation is particularly important in enclosed spaces or areas with limited natural airflow.
Implement Local Exhaust Ventilation (LEV): LEV systems are highly effective in controlling the release of hazardous substances. They involve a hood or enclosure that captures the gases at their source and directs them through a ducting system to a fume extractor. This method is especially useful for localized welding tasks, as it captures the gases before they can spread. Ensure that the LEV system is properly sized and positioned to cover the entire welding area.
Encourage Natural Airflow: In addition to mechanical ventilation, natural airflow can also help disperse flammable gases. Open windows and doors to allow fresh air to circulate, reducing the concentration of potential hazards. However, this method might not be sufficient on its own, especially in enclosed spaces, so it should be used in conjunction with more robust ventilation solutions.
Regular Maintenance and Inspection: Proper maintenance and regular inspections of the vehicle's fuel system are essential. Check for any signs of damage, leaks, or corrosion that could lead to gas releases during the welding process. Keep the work area clean and free of debris, as dust and dirt can also contribute to the buildup of flammable mixtures.
By implementing these ventilation strategies, you can significantly reduce the risks associated with welding near auto fuel lines, ensuring a safer working environment for both the welder and anyone nearby. Remember, when dealing with flammable substances, prevention is always better than cure.
Can Fuel Lines Withstand the Heat of Brake Fluid?
You may want to see also
Use Non-Sparking Tools: Avoid sparks by using non-sparking tools and welding equipment
When working near automotive fuel lines, it is crucial to prioritize safety to prevent any accidents or fires. One essential practice is to use non-sparking tools and equipment to eliminate the risk of sparks that could ignite flammable fuel. Here's a detailed guide on why and how to employ non-sparking tools for this specific task:
Understanding the Hazard: Automotive fuel systems are designed to be highly flammable. Even a small spark can ignite fuel vapor, leading to a dangerous explosion. Welding operations, by their very nature, generate sparks, making them a significant risk factor when working in close proximity to fuel lines. The potential consequences are severe, including fires, explosions, and severe injuries.
The Role of Non-Sparking Tools: Non-sparking tools are specifically designed to prevent the generation of sparks. These tools are made from materials that do not produce a spark when struck or rubbed against each other. By using such tools, you create a safer environment around fuel lines, ensuring that no accidental sparks can occur during the welding process.
Types of Non-Sparking Tools: There are various non-sparking tools available that can be utilized for welding near fuel lines. These include:
- Non-Sparking Pliers: These pliers are made from materials like bronze or copper alloys, ensuring they do not generate sparks when used for gripping or bending.
- Non-Sparking Wrenches: Similar to pliers, these wrenches are designed to avoid sparks, making them ideal for tightening or loosening nuts and bolts near fuel lines.
- Insulated Gloves: Wearing insulated gloves can provide an extra layer of protection, especially when handling hot metal or welding equipment.
- Spark-Free Welding Helmets: Specially designed welding helmets with non-sparking lenses can further enhance safety by preventing sparks from entering the welder's field of vision.
Implementing the Practice: When setting up for a welding job near fuel lines, ensure that all tools and equipment used are non-sparking. Inspect the tools regularly to check for any signs of damage or wear that might compromise their non-sparking properties. Additionally, educate your team on the importance of using these tools and the potential hazards of sparks in this environment.
By adopting the practice of using non-sparking tools and equipment, you create a safer working environment, significantly reducing the risks associated with welding near automotive fuel lines. This simple yet effective measure is a vital component of any comprehensive safety protocol for such delicate and potentially dangerous tasks.
Artic Cat 650 V2 Fuel Line Routing: A Step-by-Step Guide
You may want to see also
Keep Distance: Maintain a safe distance from fuel lines and ensure no heat sources are nearby
When performing any welding activity near a vehicle's fuel lines, maintaining a safe distance is crucial to prevent accidents and potential hazards. The primary goal is to avoid any direct contact or proximity that could lead to fuel line damage or ignition of flammable gases. Here's a detailed guide on why and how to keep a safe distance:
Understanding the Risks: Welding involves intense heat and sparks, which can be extremely dangerous when in close proximity to fuel lines. These lines are often made of thin metal and can be susceptible to damage from the intense heat generated during the welding process. Even a small puncture or cut can lead to fuel leaks, which, when combined with sparks or open flames, can result in explosions or fires. Additionally, the pressure and force of a welding torch can cause fuel lines to burst, leading to hazardous situations.
Safe Distance Protocol: It is recommended to maintain a distance of at least 10 feet between the welding equipment and any fuel lines or fuel-related components. This distance provides a buffer that minimizes the risk of accidental damage. If the vehicle has an underbody, ensure that the welding is conducted on the top side to avoid any potential heat or sparks reaching the fuel lines. For above-ground fuel tanks, the distance should be even more significant, considering the potential for fuel to spill or leak.
Heat Management: Keep in mind that heat sources can also pose a risk. Ensure that no other heat sources, such as soldering irons, heat guns, or even hot surfaces, are in the vicinity. These heat sources can cause localized damage to fuel lines, making them more susceptible to issues during the welding process. It is essential to create a safe work area by removing any potential heat-generating equipment and ensuring that the environment is clear of flammable materials.
Precautionary Measures: Before starting the welding, inspect the fuel lines for any signs of damage or wear. Look for cracks, punctures, or any other abnormalities that could make the lines more vulnerable. If any issues are found, address them promptly and ensure they are securely repaired or replaced before proceeding with the welding. Additionally, consider using protective gear, such as heat-resistant gloves and clothing, to minimize the risk of injury in case of any unexpected incidents.
By adhering to these guidelines and maintaining a safe distance, you can significantly reduce the risks associated with welding near auto fuel lines, ensuring a safer working environment and preventing potential disasters. Always prioritize safety and take the necessary precautions to protect yourself, those around you, and the vehicle's fuel system.
Flue Liner Sizing Guide: Choosing the Right Fit for Your Multi-Fuel Stove
You may want to see also
Frequently asked questions
Welding near fuel lines can pose significant dangers due to the risk of fuel leakage and ignition. Gasoline and diesel are highly flammable, and any spark or heat source, including welding, can cause a fire or explosion. Additionally, the pressure in fuel lines can cause them to rupture, leading to a dangerous release of fuel.
To ensure safety, it is crucial to follow these guidelines: first, ensure you have the necessary personal protective equipment (PPE), including heat-resistant gloves, safety goggles, and a respirator. Then, inspect the fuel lines for any signs of damage or corrosion. If possible, temporarily disconnect the fuel lines to eliminate the risk of fuel release. Always maintain a safe distance from the welding area and use a non-sparking tool to avoid any potential ignition sources.
Yes, a thorough preparation is essential. Before starting, ensure the vehicle's engine is off and the fuel system is isolated. Use a fuel leak detector or soapy water test to identify any potential leaks. If a leak is detected, do not proceed with welding. During the welding process, use a ground clamp to ensure a stable electrical connection, and keep the welding torch at a safe distance from the fuel lines. After welding, allow the area to cool down, and perform another leak test to ensure no damage was caused.