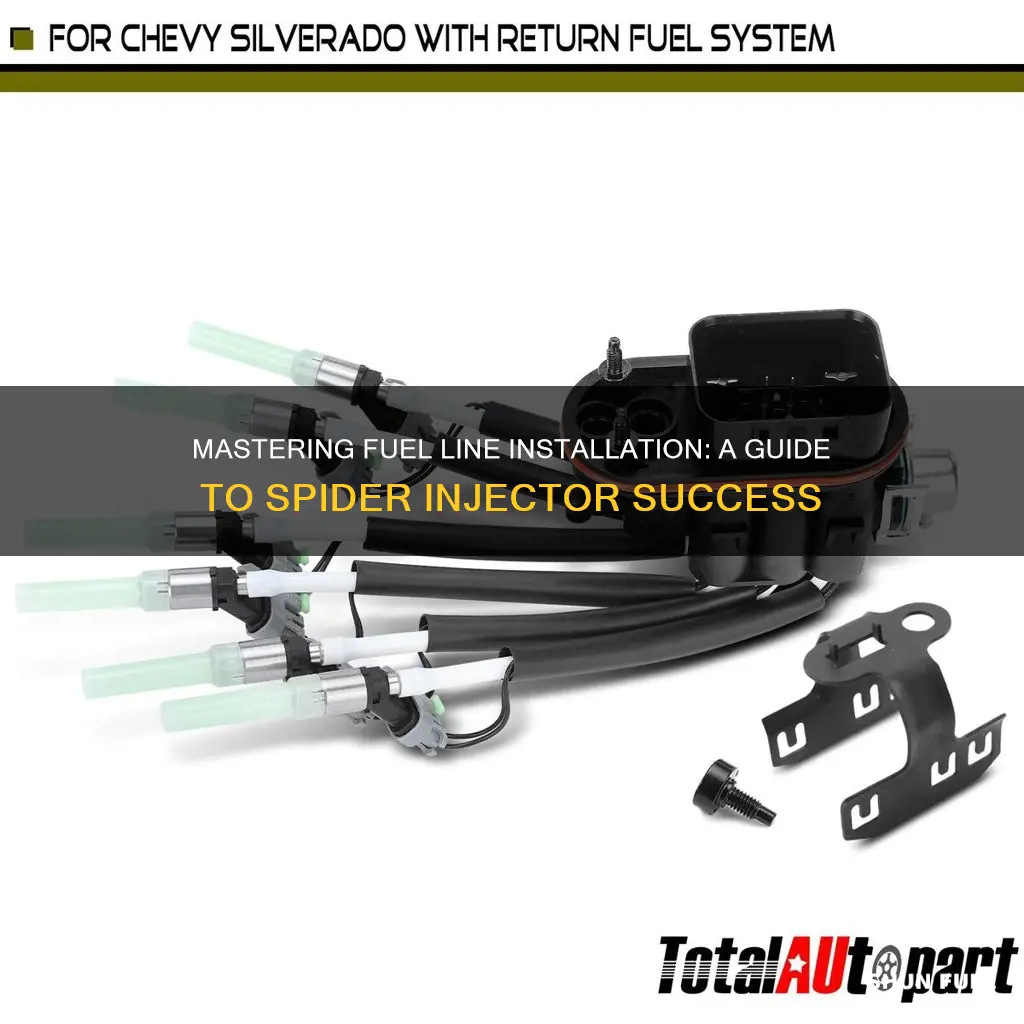
Installing fuel lines to a spider injector can seem daunting, but with the right tools and a systematic approach, it's a manageable task. This guide will walk you through the process step-by-step, ensuring you have the necessary knowledge to complete the job safely and effectively. From preparing the components to making secure connections, we'll cover everything you need to know to get your fuel lines in place and your engine running smoothly.
What You'll Learn
- Fuel Line Routing: Plan optimal paths for fuel lines, avoiding tight spaces and potential damage
- Fuel Line Material: Choose appropriate fuel-resistant materials for durability and compatibility
- Fuel Line Connections: Securely attach fuel lines to injectors using the correct fittings and torque specifications
- Fuel Line Testing: Conduct pressure tests to ensure fuel lines are leak-free and functional
- Fuel Line Maintenance: Regularly inspect and maintain fuel lines to prevent clogs and ensure optimal performance
Fuel Line Routing: Plan optimal paths for fuel lines, avoiding tight spaces and potential damage
When installing fuel lines for a spider injector, careful planning of the routing is crucial to ensure optimal performance and longevity of the system. The primary goal is to create a path that minimizes stress on the fuel lines while avoiding any potential damage from tight spaces or sharp bends. Here's a step-by-step guide to achieving this:
- Understand the Layout: Begin by studying the engine bay and the spider injector's position. Identify the available space and any obstacles that could hinder the fuel line installation. Visualize the path the fuel lines will take from the fuel tank to the injector.
- Route Planning: Design a route that is as straight as possible, reducing the number of bends and sharp turns. Fuel lines should be routed away from high-pressure areas, such as exhaust manifolds and engine components that could cause damage. Aim for a path that allows for easy access during maintenance and provides sufficient clearance.
- Consider Flexibility: Fuel lines should be flexible to accommodate engine movement during operation. Allow for slight bends and curves in the routing to ensure the lines can move freely without kinking or putting excessive strain on the connections.
- Avoid Tight Spaces: One of the critical aspects of routing is to steer clear of tight spaces like engine compartments, wheel arches, or areas with limited access. These spaces often have sharp corners or edges that can damage the fuel lines over time. Instead, opt for routes that provide ample space, ensuring the lines remain intact and secure.
- Securement and Support: Properly secure the fuel lines to prevent movement and potential damage. Use appropriate tie-downs, clips, or brackets to keep the lines in place. Ensure that the mounting points are chosen carefully to avoid putting strain on the lines, especially at bends or joints.
By following these guidelines, you can create a well-planned fuel line routing system that ensures efficient fuel delivery to the spider injector while minimizing the risk of damage and maintaining the overall health of the engine. Remember, the goal is to provide a smooth, protected path for the fuel lines, contributing to the engine's performance and reliability.
Aquarium Air Line: A Fuel Alternative?
You may want to see also
Fuel Line Material: Choose appropriate fuel-resistant materials for durability and compatibility
When it comes to installing fuel lines for a spider injector, choosing the right material is crucial for ensuring long-lasting performance and compatibility. The fuel lines must be able to withstand the corrosive nature of fuel, as well as the high temperatures and pressure it can exert. Here's a guide on selecting the appropriate fuel-resistant materials:
Consider the Fuel Type: Different types of fuel, such as gasoline, diesel, or ethanol blends, have varying properties. For instance, ethanol-blended fuels are more corrosive and can dissolve certain materials over time. Therefore, if you're working with an ethanol-blended fuel, opt for materials specifically designed to resist its corrosive effects. Look for fuel lines made from materials like stainless steel, which offers excellent corrosion resistance, or choose synthetic rubber compounds that are known to be compatible with ethanol-based fuels.
Evaluate Temperature and Pressure: The operating conditions of your engine play a significant role in material selection. If your engine operates at high temperatures or generates substantial pressure, you'll need fuel lines that can handle these extreme conditions. Materials like high-temperature rubber compounds or braided stainless steel hoses are ideal for such applications. These materials provide flexibility while maintaining structural integrity under heat and pressure.
Check Compatibility with Injectors: Spider injectors, in particular, may have specific requirements. Ensure that the fuel lines you choose are compatible with the injector's design and mounting points. Some injectors might require fuel lines with specific diameters or those that can accommodate particular mounting angles. Always refer to the manufacturer's guidelines or consult with an expert to ensure the chosen fuel lines fit the injector perfectly.
Durability and Flexibility: Fuel lines should be durable enough to withstand the rigors of daily use, including vibrations, temperature fluctuations, and mechanical stress. Look for materials that offer a balance between flexibility and strength. Braided stainless steel, for example, provides excellent durability while maintaining the necessary flexibility for easy installation and operation. Additionally, consider the overall length and routing of the fuel lines to ensure they can withstand the engine's mechanical movements without excessive wear or damage.
By carefully considering the fuel type, operating conditions, compatibility with the spider injector, and the durability requirements, you can select the most appropriate fuel-resistant materials for your fuel line installation. This ensures a reliable and long-lasting setup, minimizing the risk of fuel leaks or performance issues.
Log Book Fuel Line: A Guide to Filling Up
You may want to see also
Fuel Line Connections: Securely attach fuel lines to injectors using the correct fittings and torque specifications
When working on fuel line connections for a vehicle with a spider injector, it's crucial to ensure a secure and reliable setup to maintain optimal engine performance. Here's a step-by-step guide to achieving this:
Preparation and Tools: Begin by gathering the necessary tools and materials. You'll need the appropriate fuel line fittings, which should be compatible with your vehicle's fuel system. Common types include barbed fittings, compression fittings, or quick-connect fittings, each with its own advantages. Additionally, obtain the required torque specifications for the fuel lines and injectors to ensure proper tightening.
Fuel Line Installation: Start by locating the fuel injectors and identifying the fuel lines that need to be connected. Carefully remove any old or damaged fuel lines, ensuring you have a clear view of the injector ports. Clean the ports and fuel lines to remove any debris or contaminants. Then, cut the new fuel lines to the appropriate length, allowing for a slight overlap to facilitate a secure connection.
Fitting Connections: Slide the fuel line over the injector port, ensuring it is centered. Depending on the fitting type, you may need to crimp, clamp, or screw the fitting onto the fuel line. For barbed fittings, insert the fuel line into the barb and ensure a snug fit. Compression fittings require the fuel line to be inserted and then tightened with a tool to create a secure seal. Quick-connect fittings offer a convenient snap-on connection. Always refer to the manufacturer's instructions for the specific fitting you are using.
Torque and Security: Once the fittings are in place, it's essential to torque the connections according to the vehicle's specifications. Over-tightening can damage the fuel lines or injectors, while under-tightening may lead to leaks. Use a torque wrench to apply the correct amount of force, ensuring a tight and secure connection. Double-check all fittings to ensure they are tight and secure, especially at high-pressure points.
Testing and Final Checks: After completing the fuel line connections, start the engine and monitor for any leaks. Check all fittings for tightness and ensure there are no visible signs of damage. Test the fuel system's pressure to confirm the integrity of the connections. If everything is in order, your vehicle should now have a reliable fuel supply to the injectors, ensuring optimal performance and fuel efficiency. Remember, proper fuel line installation is vital for engine health and longevity.
Fixing Red Kote Fuel Tank Liner: A Step-by-Step Guide
You may want to see also
Fuel Line Testing: Conduct pressure tests to ensure fuel lines are leak-free and functional
Fuel line testing is a critical step in ensuring the proper functioning of your vehicle's fuel system, especially when dealing with intricate setups like the Spider Injector system. This testing process involves a series of checks to verify that the fuel lines are free from leaks and can withstand the pressure required for efficient fuel delivery. Here's a detailed guide on how to conduct these pressure tests:
Preparation: Before initiating the pressure test, ensure you have the necessary tools and equipment. This includes a fuel pressure gauge, a set of wrenches or tools for tightening connections, and a supply of clean, dry fuel. It is also essential to have a clear understanding of the vehicle's fuel system layout to identify the correct fuel lines and their respective connections.
Step-by-Step Process:
- Fuel Line Inspection: Start by visually inspecting the fuel lines for any signs of damage, cracks, or kinks. Look for any areas where the line might be pinched or damaged, as these can be potential leak points. Clean the fuel lines and connections to ensure no contaminants interfere with the test.
- Pressure Application: Locate the fuel pump and ensure it is operational. Apply pressure to the fuel system using the fuel pressure gauge. Start with a low pressure and gradually increase it while monitoring the gauge. The target pressure should be as specified in your vehicle's manual, typically around 45-60 psi for most vehicles. Hold the pressure for a few seconds to ensure stability.
- Leak Detection: During the pressure application, closely observe the fuel lines for any signs of fuel escaping. Leaks can occur at connections, fittings, or points where the line is bent or damaged. If a leak is detected, immediately release the pressure and identify the source of the leak. Tighten any loose connections or replace damaged sections of the fuel line.
- Repeat and Verify: After addressing any leaks, reapply the pressure and observe the fuel lines again. Ensure that no new leaks appear and that the pressure holds steady. It is recommended to perform this test multiple times to confirm the fuel lines' reliability.
- Post-Test Inspection: After the test, inspect the fuel lines once more for any signs of damage or wear. Check for any fuel residue or contamination that might have occurred during the test. Clean the fuel lines and connections if necessary to maintain optimal performance.
Safety Considerations: When conducting pressure tests, always prioritize safety. Ensure the engine is turned off and the vehicle is in a secure location. Wear appropriate personal protective equipment, such as gloves and safety goggles, to protect against potential fuel spills. Always follow the manufacturer's guidelines and recommendations for your specific vehicle.
By following these steps, you can effectively test and ensure the integrity of your fuel lines, guaranteeing a reliable fuel supply to the Spider Injector system. Regular maintenance and testing are essential to prevent fuel-related issues and maintain optimal vehicle performance.
Fuel Line Size for Your Yamaha KT100: What You Need to Know
You may want to see also
Fuel Line Maintenance: Regularly inspect and maintain fuel lines to prevent clogs and ensure optimal performance
Fuel lines are an essential component of any vehicle's fuel system, and proper maintenance is crucial to ensure optimal performance and longevity. Regular inspection and care can prevent clogs, leaks, and other issues that may arise from wear and tear or environmental factors. Here's a guide on how to maintain your fuel lines effectively:
Visual Inspection: Start by regularly examining the fuel lines for any signs of damage or deterioration. Look for cracks, brittleness, or any visible wear along the length of the lines. Check for any bends or kinks that might have occurred due to movement or impact. Pay close attention to the connections and fittings, as these areas are more susceptible to leaks and blockages. It's a good practice to inspect the fuel lines during routine vehicle maintenance checks or whenever there's an opportunity to access the engine bay.
Clearing Clogs: Over time, fuel lines can become clogged with debris, varnish, or fuel contaminants. This can restrict fuel flow and reduce engine performance. To address this, you can use a fuel line cleaner or a compressed air gun to blow through the lines and dislodge any blockages. Start at the fuel tank and work your way towards the injector, ensuring you clean all connections and fittings. This process helps to restore proper fuel delivery and maintain engine efficiency.
Replacing Worn Parts: If you notice any significant damage or persistent issues during your inspections, it's essential to replace the affected fuel lines or fittings promptly. Worn-out parts may lead to fuel leaks, which can be dangerous and cause engine misfires. When replacing parts, ensure you use high-quality replacements that are compatible with your vehicle's make and model. Properly secure all new components to maintain the integrity of the fuel system.
Regular Fluid Changes: Maintaining a regular schedule for fuel system flushes and changes can prevent the buildup of contaminants and ensure clean fuel lines. This is especially important if you use lower-quality fuels or notice any performance issues. Consult your vehicle's manual for recommended service intervals, and consider using fuel system cleaner during these changes to enhance the overall health of your engine.
By following these maintenance steps, you can ensure that your fuel lines remain in optimal condition, providing efficient fuel delivery to the engine. Regular care will help prevent costly repairs and keep your vehicle running smoothly. Remember, proper maintenance is key to extending the life of your vehicle's components and maintaining its overall performance.
Koler Command Fuel Line Sizes: A Comprehensive Guide
You may want to see also
Frequently asked questions
Fuel lines are an essential component in a spider injector system, which is commonly used in automotive applications. They serve as the conduit for delivering fuel from the fuel pump to the injector nozzles. By using fuel lines, the system ensures precise and controlled fuel delivery, allowing for efficient combustion and optimal engine performance.
Selecting the appropriate fuel lines is crucial for a successful installation. The size of the fuel line should match the flow rate requirements of your engine and the injector setup. Typically, fuel lines are made of materials like steel, aluminum, or flexible rubber hoses. Steel lines offer durability and are often used in high-pressure applications, while flexible hoses provide ease of installation and vibration dampening. Consider the engine's power output, fuel pressure, and environmental factors when choosing the material and size.
It is not recommended to use regular automotive fuel lines for a spider injector system. Spider injectors often require high-pressure fuel delivery, and standard fuel lines may not withstand the pressure and temperature fluctuations. Look for fuel lines specifically designed for high-pressure applications or custom-made lines that can handle the demands of your spider injector setup.
During the installation process, it's important to be mindful of potential issues. Ensure that the fuel lines are properly secured and routed to avoid damage or interference with other engine components. Check for any kinks or bends in the lines, as these can restrict fuel flow. Also, verify that all connections are tight and secure, using appropriate fuel line connectors to prevent leaks. Properly sealing the fuel lines at the injector and pump connections is vital to maintain system integrity.