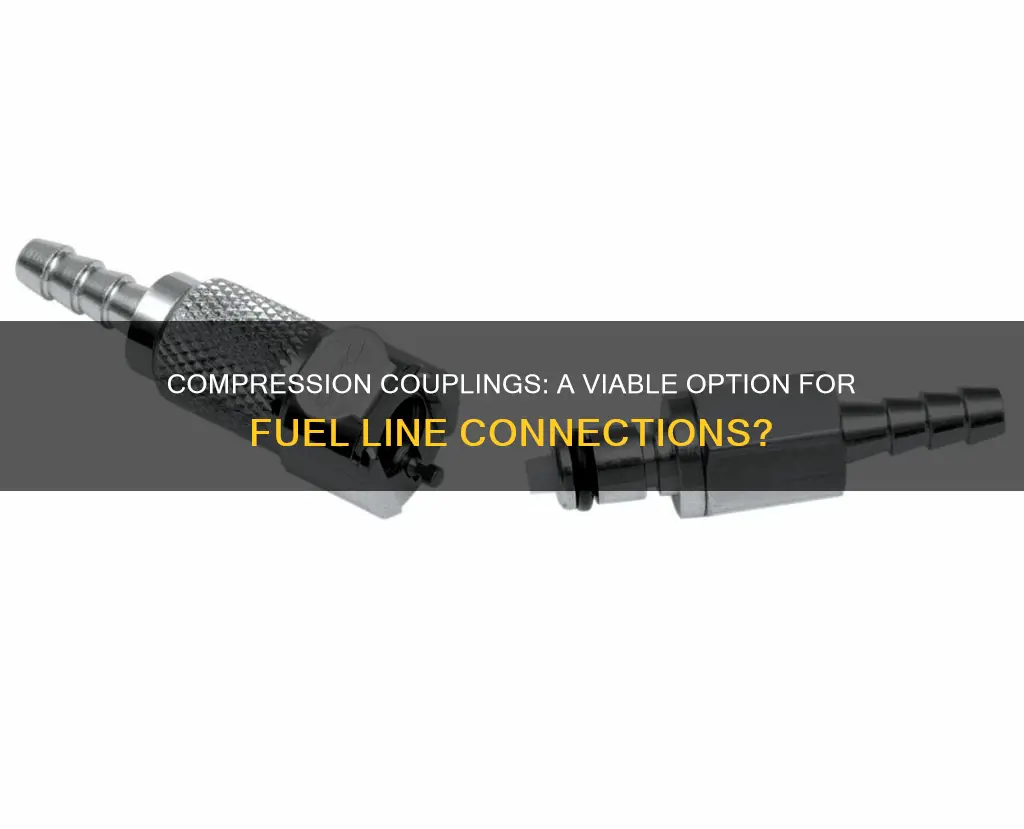
Compression couplings are a type of coupling mechanism commonly used in various automotive applications, including fuel lines. These couplings are designed to securely connect two components while allowing for a certain degree of movement or misalignment. When it comes to fuel lines, the use of compression couplings can be beneficial as they provide a reliable and flexible connection point. This is particularly useful in vehicles where fuel lines may need to accommodate vibrations, temperature changes, or slight misalignments without compromising the integrity of the fuel supply. The couplings are typically made from durable materials, ensuring they can withstand the harsh conditions of an engine bay while maintaining a tight seal. This makes them a popular choice for fuel line installations, offering both functionality and protection against potential leaks.
What You'll Learn
- Material Compatibility: Ensure the coupling material is compatible with fuel line fluids
- Pressure Rating: Check if the coupling can withstand fuel line pressure
- Flexibility: Assess the coupling's flexibility to accommodate fuel line movement
- Temperature Tolerance: Verify the coupling's performance within fuel line temperature ranges
- Installation Ease: Evaluate the ease of installing the coupling on fuel lines
Material Compatibility: Ensure the coupling material is compatible with fuel line fluids
When considering the use of compression couplings for fuel lines in vehicles, material compatibility is a critical factor that cannot be overlooked. The primary concern is ensuring that the coupling material does not react with or degrade the fuel line fluids, which could lead to potential issues such as fuel contamination, reduced performance, or even safety hazards.
Fuel lines in vehicles typically carry gasoline, diesel, or other petroleum-based fuels, which can vary in composition and volatility. These fuels often contain additives to enhance performance and protect the engine, such as detergents, antioxidants, and lubricants. Therefore, the coupling material must be carefully selected to withstand these fuel components without adverse reactions.
One of the key properties to consider is the material's resistance to fuel degradation. Some materials, when exposed to fuel, may undergo chemical changes, leading to the formation of harmful byproducts or the degradation of the material's structural integrity. For instance, certain plastics or rubbers might absorb fuel, causing swelling and potential cracking over time. This could result in fuel leaks, reduced coupling performance, and potential engine damage.
To ensure compatibility, manufacturers often specify the use of materials that are resistant to fuel degradation. These materials are typically engineered to maintain their structural and chemical properties when exposed to fuel. For example, high-quality rubber compounds with fuel-resistant additives or specific types of plastics with excellent chemical stability can be used. These materials can provide a reliable and long-lasting connection between the fuel lines and the coupling.
Additionally, it is essential to consider the temperature range and operating conditions of the vehicle. Fuel lines may experience varying temperatures, especially in different climates, and the coupling material should be able to withstand these conditions without compromising its compatibility with the fuel. Some materials might be more suitable for high-temperature environments, while others excel in low-temperature applications.
In summary, when using compression couplings for fuel lines, material compatibility is vital to guarantee the longevity and reliability of the fuel system. Choosing materials that are resistant to fuel degradation and can withstand the specific operating conditions of the vehicle is essential. This ensures that the coupling remains effective and safe, contributing to the overall performance and efficiency of the vehicle's fuel delivery system.
Protect Your Ride: A Guide to Securing Fuel Lines
You may want to see also
Pressure Rating: Check if the coupling can withstand fuel line pressure
When considering the use of compression couplings for fuel lines in vehicles, one critical aspect to evaluate is the pressure rating of the coupling. Fuel lines operate under varying pressure conditions, and it is essential to ensure that the chosen coupling can withstand these pressures to maintain the integrity of the fuel system.
The pressure rating of a coupling refers to the maximum pressure it can handle without failing or compromising its structural integrity. Fuel lines, especially in high-performance vehicles, can experience significant pressure fluctuations, especially during acceleration or when the engine is under load. Therefore, it is imperative to select a coupling with a pressure rating that exceeds the expected fuel line pressure to ensure safety and reliability.
To determine the pressure rating, manufacturers typically provide specifications for their couplings. These specifications should include the maximum pressure the coupling can withstand, often measured in pounds per square inch (PSI) or bar. It is crucial to consult the manufacturer's guidelines and choose a coupling with a pressure rating that meets or exceeds the fuel line pressure requirements. For instance, if the fuel line is expected to operate at 300 PSI, a coupling with a minimum pressure rating of 350 PSI or higher would be appropriate.
During the selection process, consider the specific fuel system design and the operating conditions of the vehicle. Different fuel systems may have unique pressure requirements, and the chosen coupling should align with these specifications. Additionally, it is advisable to opt for couplings with a proven track record of performance in similar applications to ensure reliability in real-world scenarios.
In summary, when using compression couplings for fuel lines, verifying the pressure rating is essential. By selecting a coupling that can withstand the expected fuel line pressure, you ensure the safety and functionality of the fuel system. Always refer to manufacturer guidelines and consider the specific needs of the vehicle to make an informed decision.
Choosing the Right U.S. Coast Guard-Approved Fuel Line for Ocean Outboards
You may want to see also
Flexibility: Assess the coupling's flexibility to accommodate fuel line movement
When considering the use of compression couplings for fuel lines in vehicles, one crucial aspect to evaluate is their flexibility. Fuel lines are subject to various movements and vibrations during the vehicle's operation, and the coupling must be able to accommodate these motions without compromising performance or safety.
Flexibility is a critical factor in ensuring the longevity and reliability of the fuel system. Compression couplings are designed to provide a secure connection between two components, but their ability to move and adjust is essential for maintaining a tight seal while allowing for the natural expansion and contraction of the fuel lines. This flexibility is particularly important in high-temperature environments, where fuel lines can expand and contract significantly.
To assess the flexibility of a compression coupling, one should consider the material and design of the coupling. Couplings made from flexible materials, such as rubber or certain types of plastics, can better adapt to the fuel line's movement. The design should also allow for a certain degree of angular and linear movement, ensuring that the coupling can accommodate the fuel line's natural fluctuations without excessive stress or strain.
During installation, it is crucial to ensure that the coupling is not overly tightened, as this can restrict flexibility. The coupling should be secured firmly but with enough play to allow for movement. Regular inspections and maintenance can also help identify any wear or damage that may affect the coupling's flexibility over time.
In summary, when using compression couplings on fuel lines, flexibility is key to ensuring a secure and reliable connection. The coupling should be chosen and installed with consideration for its ability to accommodate the fuel line's movement, ensuring the overall system's performance and safety. This assessment of flexibility is a critical step in the process of integrating compression couplings into vehicle fuel systems.
Unclogging the Miata: A Step-by-Step Guide to Removing the Fuel Line Filter
You may want to see also
Temperature Tolerance: Verify the coupling's performance within fuel line temperature ranges
When considering the use of compression couplings for fuel lines in vehicles, it is crucial to evaluate their performance within the specific temperature ranges encountered in automotive applications. Fuel lines are exposed to varying temperatures, which can significantly impact the functionality and longevity of the coupling. Therefore, thorough testing and verification are essential to ensure the couplings' reliability and safety.
The temperature tolerance of compression couplings is a critical factor in their suitability for fuel line applications. Fuel lines often operate within a wide temperature range, from extremely cold conditions during winter to high temperatures generated by the engine's heat. Couplings must be able to withstand these temperature fluctuations without compromising their structural integrity or performance. Manufacturers should conduct rigorous testing to simulate these extreme conditions and assess the coupling's behavior.
One common method to evaluate temperature tolerance is through thermal cycling tests. This involves subjecting the coupling to rapid temperature changes, mimicking the real-world temperature variations experienced by fuel lines. By exposing the coupling to these cycles, engineers can observe its performance over time. The coupling should maintain its sealing properties, prevent material degradation, and ensure that the connection remains secure even after repeated temperature fluctuations.
Additionally, manufacturers should consider the material properties of the coupling in relation to temperature. Different materials have varying levels of thermal stability. For instance, some couplings might use rubber or silicone, which can become brittle or lose flexibility at low temperatures, while others may employ more heat-resistant materials like certain plastics or metals. The chosen material should be compatible with the expected temperature range to ensure optimal performance and durability.
In summary, verifying the temperature tolerance of compression couplings for fuel lines is vital for their successful integration into vehicles. Through rigorous testing, including thermal cycling, and careful material selection, engineers can ensure that the couplings can withstand the temperature extremes encountered in automotive fuel systems, providing a reliable and safe connection.
Understanding the Dual Fuel Lines in Your Chainsaw: A Guide
You may want to see also
Installation Ease: Evaluate the ease of installing the coupling on fuel lines
When considering the use of compression couplings for fuel lines in vehicles, one crucial aspect to evaluate is the installation process. The ease of installation is a significant factor that can impact the overall efficiency and reliability of the fuel system. Here's an analysis of this aspect:
Compression couplings, as the name suggests, rely on compression to secure the connection between two pipes or hoses. This type of coupling is generally straightforward to install, especially when compared to other coupling methods like clamp-style or quick-connect couplings. The installation process typically involves the following steps: First, ensure that the fuel lines are properly prepared by cleaning and removing any debris or old couplings. Then, align the compression coupling with the fuel lines, ensuring that the coupling's internal threads match the fuel line's outer diameter. Next, apply a thin layer of thread sealant to the coupling and fuel line threads to prevent leaks. Finally, tighten the coupling by hand, followed by using a wrench to ensure a secure and tight connection. This process is relatively simple and can be completed with basic tools, making it accessible for DIY enthusiasts and professional mechanics alike.
The key advantage of compression couplings in terms of installation is their versatility. They can be easily adapted to various fuel line sizes and shapes, providing a customizable solution for different vehicle models. This adaptability simplifies the installation process, as technicians can quickly find the right coupling size without the need for extensive customization. Additionally, the simplicity of the installation process reduces the risk of human error, ensuring a more reliable connection.
However, it's important to note that the installation process may require some practice and skill to ensure a proper fit. The user must be cautious not to overtighten the coupling, as this can lead to damage to the fuel lines or the coupling itself. Proper torque specifications should be followed to achieve a secure connection without causing harm.
In summary, compression couplings offer a relatively simple and efficient installation process for fuel lines. Their versatility and ease of use make them a practical choice for connecting fuel lines in vehicles. With the right tools and a bit of practice, technicians can quickly master the installation technique, ensuring a reliable and leak-free fuel system.
Fuel Pump Line Removal: A Guide for 2005 Dodge Durango Owners
You may want to see also
Frequently asked questions
Yes, compression couplings can be used for fuel lines in vehicles, but it's important to consider specific requirements and compatibility. These couplings are designed to provide a secure and leak-free connection, which is crucial for fuel lines due to the potential hazards of fuel leaks.
Compression couplings offer several benefits for fuel line applications. They provide a tight seal by compressing the fuel line against the coupling, ensuring a secure connection. This design also allows for flexibility, accommodating slight movements and vibrations without compromising the seal. Additionally, they are easy to install and can be quickly disconnected for maintenance or repairs.
When using compression couplings for fuel lines, it's essential to choose the right size and material to match the fuel line diameter and ensure compatibility. The coupling should be made from a material that is compatible with the fuel type to prevent corrosion or degradation. Regular inspection and maintenance are also recommended to ensure the coupling remains leak-free over time.
While compression couplings can be used in fuel lines, they are generally more suitable for low-pressure applications. High-pressure fuel systems require specialized couplings designed to withstand the increased pressure and potential heat generated. It's crucial to consult the vehicle's manufacturer guidelines or seek expert advice for high-pressure fuel line installations.
Proper installation is critical to the performance and safety of compression couplings in fuel lines. Start by cleaning the fuel line and coupling surfaces to ensure a clean connection. Follow the manufacturer's instructions for the correct torque specifications when tightening the coupling. Ensure that the coupling is securely attached and cannot be easily loosened during vehicle operation. Regularly check for any signs of leakage or damage and replace the coupling if necessary.