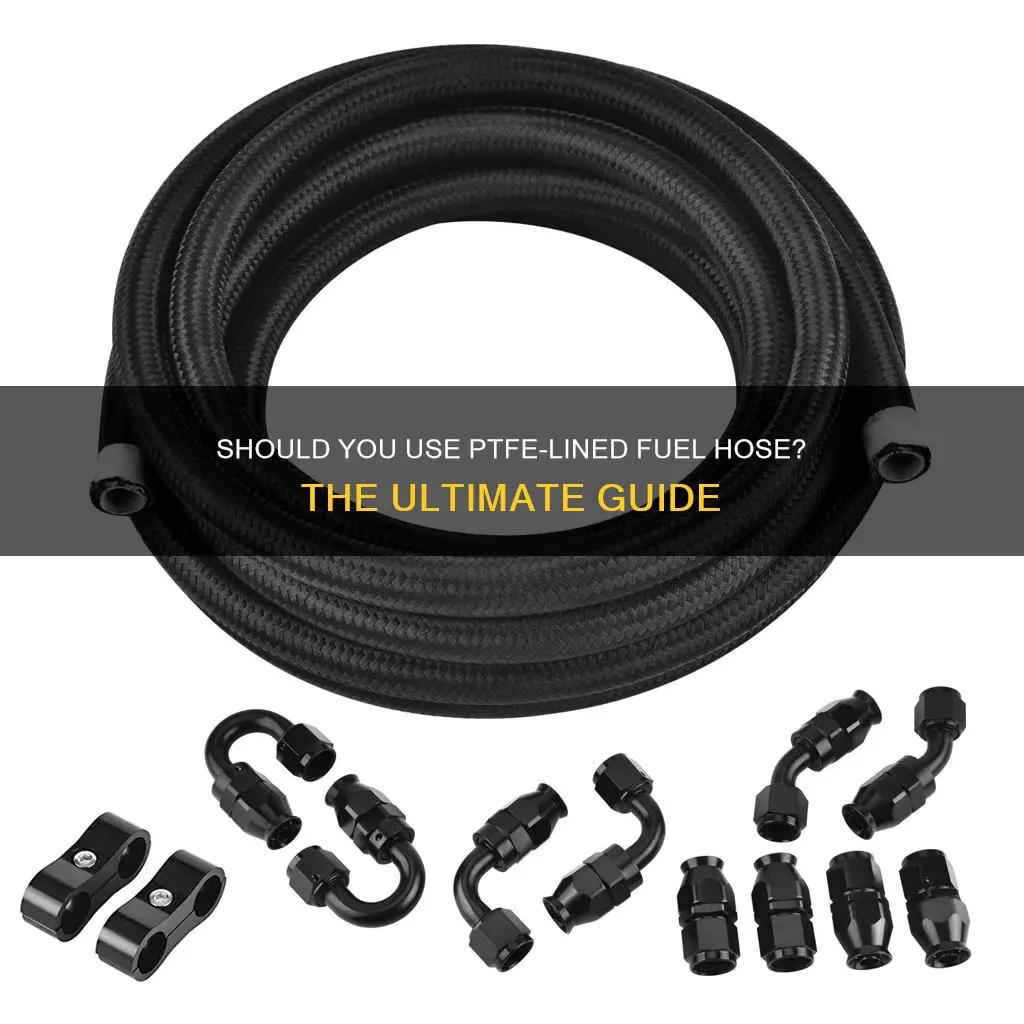
When it comes to fuel hoses, choosing the right material is crucial for optimal performance and safety. One popular option is PTFE-lined fuel hose, which offers several advantages over traditional rubber hoses. In this paragraph, we will explore the benefits of using PTFE-lined fuel hose and discuss whether it is necessary for your specific application. From its exceptional heat resistance to its ability to withstand harsh chemicals, PTFE-lined fuel hose provides a reliable and durable solution for fuel transfer and delivery systems.
Characteristics | Values |
---|---|
Material | PTFE (Polytetrafluoroethylene) |
Temperature Range | -60°C to 260°C (-76°F to 520°F) |
Pressure Rating | Up to 100 psi (6.9 bar) |
Flexibility | Excellent flexibility and durability |
Chemical Resistance | Resistant to most chemicals, including fuels |
Abrasion Resistance | High resistance to abrasion and wear |
Insulation | Provides electrical insulation |
Color | Typically black or white |
Compatibility | Compatible with most fuels and engine systems |
Installation | Easy to install and replace |
Cost | Generally more expensive than standard fuel hoses |
Maintenance | Low maintenance required |
Applications | Ideal for high-performance engines, racing cars, and marine applications |
What You'll Learn
- Fuel Compatibility: Check if the hose material is compatible with your fuel type
- Temperature Tolerance: Ensure the hose can withstand fuel temperature extremes
- Flexibility: Opt for a hose that's flexible enough for engine movement
- Durability: Choose a hose that's resistant to wear and tear
- Installation: Follow manufacturer guidelines for proper hose installation
Fuel Compatibility: Check if the hose material is compatible with your fuel type
When it comes to fuel systems, ensuring compatibility between the fuel type and the hose material is crucial to prevent leaks, contamination, and potential hazards. The compatibility of a fuel hose is determined by its ability to withstand the chemical properties of the fuel it will carry. Different fuels have varying compositions and characteristics, and using the wrong hose material can lead to degradation, cracking, or even failure of the hose over time.
One important factor to consider is the temperature range of the fuel. Some fuels, like aviation kerosene, can operate at extremely low temperatures, while others, such as gasoline, may have a wider temperature range. The hose material should be able to handle these temperature variations without becoming brittle or losing its flexibility. For instance, hoses made from natural rubber may not be suitable for fuels with a wide temperature range, as they can become stiff and crack at low temperatures or soften and become more susceptible to fuel degradation at high temperatures.
Another critical aspect is the chemical resistance of the hose material. Different fuels contain various additives and impurities that can react with certain hose materials. For example, ethanol-blended fuels can be more corrosive to some hose materials, such as certain types of rubber or plastic. It is essential to choose a hose that is specifically designed to withstand the chemical composition of the fuel it will carry. This ensures that the hose remains intact and does not leach any harmful substances into the fuel, which could lead to engine performance issues or even safety hazards.
To ensure compatibility, it is recommended to consult the manufacturer's guidelines or specifications for both the fuel and the hose. Manufacturers often provide detailed information on the recommended hose materials and their compatibility with specific fuels. This information can be found in fuel system manuals, technical data sheets, or by contacting the manufacturer directly. By following these guidelines, you can select the appropriate hose material that will ensure a safe and efficient fuel system.
In summary, when considering fuel compatibility, it is imperative to choose a hose material that is specifically designed for the type of fuel it will carry. This involves understanding the fuel's chemical properties, temperature range, and any potential additives or impurities. By selecting the right hose material, you can prevent leaks, maintain fuel quality, and ensure the longevity and reliability of your fuel system.
Fuel Line Removal: A Step-by-Step Guide for 2005 Chrysler PT Cruiser Owners
You may want to see also
Temperature Tolerance: Ensure the hose can withstand fuel temperature extremes
When considering the use of a fuel hose, temperature tolerance is a critical factor to ensure the safety and efficiency of your vehicle's fuel system. Fuel temperatures can vary significantly, especially in different climates and driving conditions. Extreme temperatures can cause the fuel to expand or contract, leading to potential issues with the hose's integrity and performance.
The ideal fuel hose should be designed to withstand a wide range of temperature extremes. This includes both high and low-temperature environments. For instance, in cold climates, fuel can freeze, and the hose must be able to handle the expansion of the fuel without cracking or leaking. Similarly, in hot climates or when the vehicle is exposed to direct sunlight, the fuel temperature can rise significantly, and the hose should not degrade or become brittle.
PTFE (Polytetrafluoroethylene) lined fuel hoses are often recommended for their excellent temperature tolerance. PTFE is a synthetic material known for its exceptional thermal stability. It can withstand a wide temperature range, typically from -200°C to 260°C (-328°F to 518°F). This makes it ideal for fuel hoses as it ensures the hose can handle the temperature fluctuations associated with different weather conditions and driving scenarios.
In addition to temperature resistance, PTFE-lined hoses also offer other benefits. They are known for their flexibility, making them easy to route and install. This material is also chemically inert, providing excellent resistance to corrosion and chemical attacks, which is crucial for maintaining the purity of the fuel. Furthermore, PTFE's low friction coefficient ensures smooth fuel flow, reducing the risk of fuel slippage and improving overall system efficiency.
When selecting a fuel hose, it is essential to consider the specific temperature extremes your vehicle will encounter. Ensure that the hose's temperature rating exceeds the expected fuel temperature range to guarantee long-term reliability and safety. Proper temperature tolerance will help prevent fuel leaks, maintain system efficiency, and ensure the overall longevity of your vehicle's fuel system.
Stihl BR600 Fuel Line Hose: Unlocking the Secrets
You may want to see also
Flexibility: Opt for a hose that's flexible enough for engine movement
When it comes to choosing the right fuel hose for your vehicle, flexibility is a crucial factor to consider, especially if your engine has any movement or vibration. A hose that is too rigid can become a source of frustration and potential damage over time. Here's why flexibility is essential and how to ensure you select the right hose.
The engine compartment in a vehicle is a dynamic environment, with various components moving and shifting during operation. This movement can cause stress on rigid hoses, leading to potential cracks, leaks, or even hose failure. Therefore, it is imperative to choose a fuel hose that can accommodate these movements without compromising its integrity. Opt for a hose made from materials that offer flexibility, such as rubber or certain types of synthetic compounds. These materials allow the hose to bend and flex without becoming brittle or prone to cracking.
Flexibility is particularly important if your vehicle has a high-performance engine or a modified setup. In such cases, the engine may have additional accessories or modifications that require the hose to move freely. A flexible hose will ensure that it can adapt to these changes without restricting fuel flow or causing unnecessary strain on the system. Look for hoses with a smooth interior lining and a flexible outer layer to allow for easy bending and movement.
Additionally, consider the length of the hose and its ability to reach all necessary connections without being overly rigid. A hose that is too stiff may require excessive force to connect or disconnect, which can be cumbersome and potentially damage the fittings. By choosing a flexible hose, you ensure a smooth installation process and easier maintenance.
In summary, when selecting a fuel hose, prioritize flexibility to accommodate engine movement and vibrations. This will help prevent potential issues and ensure the longevity of your fuel system. Remember, a flexible hose is not only practical but also contributes to a safer and more reliable vehicle performance.
Unclog Fuel Lines: The Ultimate Gas Additive Guide
You may want to see also
Durability: Choose a hose that's resistant to wear and tear
When it comes to choosing the right fuel hose for your vehicle, durability is a critical factor to consider. The fuel hose is a vital component in the fuel delivery system, and its primary function is to transport fuel from the tank to the engine while withstanding the constant pressure and potential hazards associated with fuel. Therefore, selecting a hose that is resistant to wear and tear is essential to ensure the longevity and reliability of your vehicle's performance.
One of the key aspects of durability is the hose's ability to withstand the corrosive nature of fuel. Gasoline and diesel contain various additives and impurities that can degrade certain materials over time. Therefore, it is crucial to choose a hose made from materials that are resistant to corrosion and degradation. For instance, hoses lined with polytetrafluoroethylene (PTFE) are an excellent choice as PTFE is known for its exceptional chemical resistance. This lining ensures that the hose can handle the harsh environment of fuel without compromising its structural integrity.
In addition to chemical resistance, the physical durability of the hose is another important consideration. Fuel hoses need to endure constant flexing, vibrations, and temperature fluctuations. A hose that is too flexible may wear out quickly due to excessive bending, while one that is too rigid might not accommodate the natural movement of the vehicle's components. The ideal hose should offer a balance between flexibility and rigidity, ensuring it can withstand the rigors of the road without excessive wear.
Furthermore, the construction and design of the hose play a significant role in its durability. Look for hoses with multiple layers or braids, as these provide added strength and protection against punctures and abrasion. Reinforced hoses, often used in high-performance applications, offer superior durability by incorporating additional layers or materials around the inner hose to enhance its resistance to wear and tear.
In summary, when selecting a fuel hose, prioritize durability by choosing a hose that is resistant to wear and tear. Consider the hose's ability to withstand the corrosive nature of fuel, its flexibility and rigidity, and the overall construction and design. By opting for a durable hose, you can ensure a reliable and long-lasting fuel delivery system for your vehicle.
Thawing Fuel Lines: A Step-by-Step Guide to Unfreezing
You may want to see also
Installation: Follow manufacturer guidelines for proper hose installation
When it comes to installing fuel hoses, it's crucial to follow the manufacturer's guidelines to ensure optimal performance and safety. These guidelines are designed to provide the best practices for a successful installation, taking into account the specific characteristics of the hose and the application it is intended for. Here's a step-by-step guide on how to properly install a PTFE-lined fuel hose:
Preparation: Before you begin, ensure you have the necessary tools and equipment, including the hose, fittings, and any additional components required. Check the hose for any visible damage or defects. If any issues are found, replace the hose to avoid potential leaks or performance problems. It is essential to work in a well-ventilated area and wear appropriate personal protective equipment, such as gloves and safety goggles, to protect yourself from any potential hazards.
Hose Routing: Plan the route for the fuel hose, ensuring it is free from sharp bends, tight turns, or any obstacles that could cause damage. The hose should be routed in a way that allows for easy access and inspection. Avoid routing it near heat sources or areas with excessive vibration, as this can compromise the hose's integrity.
Fitting Installation: Follow the manufacturer's instructions for installing the fittings. Typically, you will need to insert the hose into the fitting and secure it using the appropriate fasteners or clamps. Ensure a tight and secure connection to prevent any fuel leakage. Check for any signs of tightness or looseness and make adjustments as necessary. It is crucial to use the correct type of fittings for the specific hose and application to ensure compatibility and reliability.
Clamping and Support: Secure the hose with the recommended clamps or ties at regular intervals to prevent sagging or excessive movement. Proper support is essential to maintain the hose's shape and prevent damage. Ensure that the clamps are tightened securely but carefully, as excessive force can damage the hose. Allow the clamps to sit for a few minutes after tightening to ensure a firm grip.
Final Checks: Once the installation is complete, perform a thorough inspection. Check for any signs of fuel leakage at the connections and along the hose's length. Ensure that all fittings are tight and secure. Verify that the hose is properly supported and routed, avoiding any potential hazards. It is always a good practice to test the system under simulated conditions to ensure it functions as expected.
Remember, adhering to the manufacturer's guidelines is vital for a successful installation. These guidelines often include specific instructions tailored to the hose's design and intended use. By following these steps and guidelines, you can ensure a reliable and safe fuel hose installation.
Exploring the Feasibility of Using Any Line as a Fuel Line for Moped
You may want to see also
Frequently asked questions
PTFE (Polytetrafluoroethylene) is a synthetic fluoropolymer that offers several advantages for fuel hoses. It provides excellent resistance to chemicals, including fuels, and has a low coefficient of friction, allowing for smooth movement and flexibility. This material is often used in fuel systems to ensure a reliable and safe connection between the fuel tank and the engine.
While new vehicles often come with high-quality fuel systems, using a PTFE-lined hose can be a preventative measure. Over time, rubber hoses can degrade due to fuel exposure, leading to potential leaks and performance issues. Upgrading to a PTFE-lined hose can provide long-term reliability and peace of mind, especially for vehicles used in demanding conditions or those with high mileage.
Yes, you can replace your existing rubber hose with a PTFE-lined alternative. This upgrade is particularly beneficial for older vehicles or those with known fuel system issues. However, it's essential to ensure that the new hose has the correct dimensions and fittings to match your vehicle's fuel system. Consulting a mechanic or referring to your vehicle's manual will help you make an informed decision.