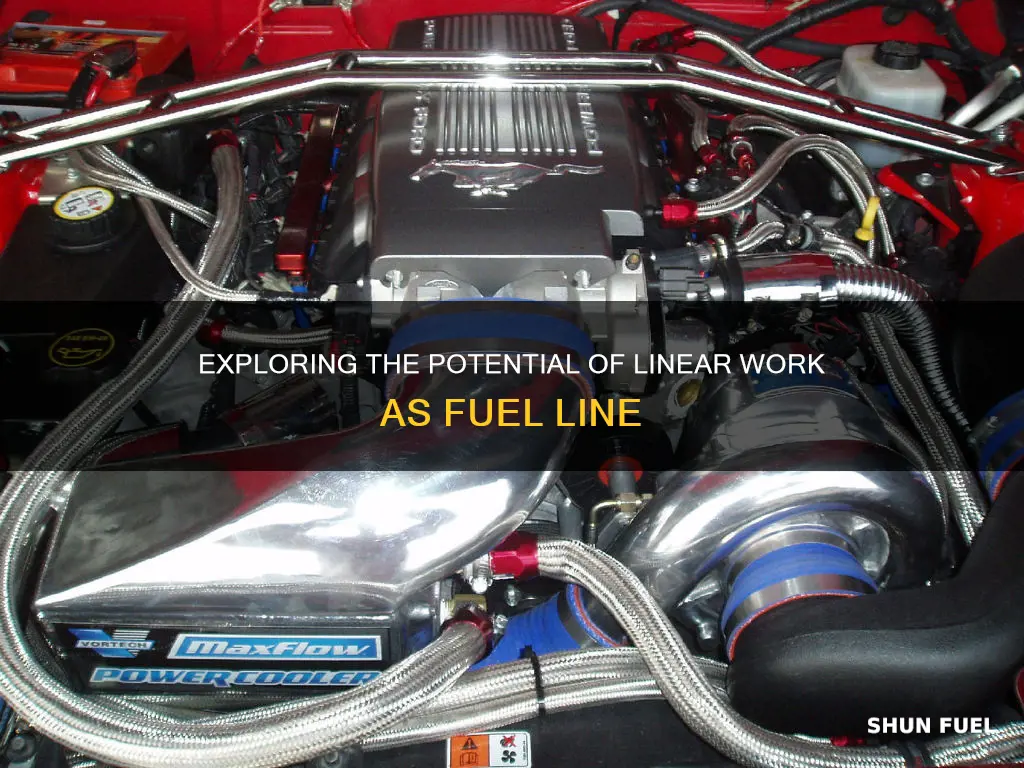
Can any linear structure serve as a fuel line? This question delves into the adaptability of various linear elements for fuel transportation. While traditional fuel lines are typically made of specific materials like rubber or plastic, the concept of utilizing linear structures for this purpose is intriguing. This exploration opens up possibilities for innovative fuel delivery systems, considering factors such as material compatibility, structural integrity, and efficiency. By examining these aspects, we can determine the feasibility and potential benefits of employing linear structures as fuel lines in various applications.
What You'll Learn
- Fuel Line Materials: Different materials like rubber, plastic, or metal can be used for fuel lines
- Fuel Line Diameter: The diameter of the fuel line affects flow rate and pressure
- Fuel Line Length: Longer fuel lines may require additional support or reinforcement
- Fuel Line Routing: Proper routing prevents damage and ensures optimal fuel flow
- Fuel Line Compatibility: Fuel lines must be compatible with the fuel type and vehicle system
Fuel Line Materials: Different materials like rubber, plastic, or metal can be used for fuel lines
Fuel lines are an essential component of any vehicle's fuel system, responsible for transporting fuel from the tank to the engine. The choice of material for these lines is crucial, as it directly impacts performance, durability, and safety. Different materials offer unique advantages and are chosen based on the specific requirements of the fuel system.
One of the most common materials used for fuel lines is rubber. Rubber is a versatile and cost-effective option, known for its flexibility and resistance to heat and chemicals. It can withstand the harsh conditions of fuel, including its volatility and potential corrosive properties. Rubber fuel lines are often used in older vehicles or those with less demanding fuel systems. They provide a good balance of flexibility and strength, allowing for easy installation and routing within the engine compartment. However, rubber can degrade over time, especially when exposed to sunlight and extreme temperatures, which may lead to cracking or leaks.
Plastic is another popular choice for fuel lines, particularly in modern vehicles. Plastic fuel lines offer excellent resistance to corrosion and chemical degradation, making them ideal for fuel systems that use ethanol or other additives. They are lightweight, flexible, and can be produced in various colors, making them aesthetically pleasing. Plastic lines are often used in high-performance vehicles or those with more complex fuel systems. The material's durability and resistance to fuel-related issues make it a reliable choice. However, plastic can become brittle over time, especially when exposed to low temperatures, which may result in cracking or failure.
Metal fuel lines, typically made from stainless steel or aluminum, are often used in high-performance or racing applications. Metal offers superior strength and durability, ensuring that the fuel lines can withstand high pressure and extreme conditions. It is an excellent choice for vehicles that require precise fuel delivery or those operating in harsh environments. Metal lines are rigid but can be flexible when needed, allowing for easy installation. They are less susceptible to corrosion and provide excellent heat resistance, making them suitable for engines with high-temperature outputs. However, metal fuel lines can be more expensive and less flexible than rubber or plastic, requiring careful consideration during installation.
In summary, the choice of material for fuel lines depends on the specific needs of the vehicle and its fuel system. Rubber provides flexibility and cost-effectiveness, plastic offers corrosion resistance and durability, while metal ensures strength and heat resistance. Each material has its advantages and considerations, allowing for a tailored approach to fuel line selection and installation. It is essential to consider the vehicle's age, performance requirements, and environmental factors when deciding on the appropriate fuel line material.
Fuel Line Placement: Expert Tips for Optimal Performance
You may want to see also
Fuel Line Diameter: The diameter of the fuel line affects flow rate and pressure
The diameter of the fuel line is a critical factor in determining the performance and efficiency of fuel delivery systems, especially in high-performance vehicles or applications where precise fuel management is essential. This parameter directly influences the flow rate and pressure of the fuel, which are crucial for optimal engine operation.
In the context of fuel lines, the diameter refers to the cross-sectional area of the pipe or hose. A larger diameter means more space for the fuel to flow, allowing for higher flow rates. When designing or selecting a fuel line, engineers and enthusiasts must consider the required flow rate to ensure the engine receives the necessary amount of fuel for efficient combustion. For instance, a high-performance engine might demand a larger flow rate to meet its power output needs, thus requiring a fuel line with a more substantial diameter.
On the other hand, the pressure within the fuel line is also significantly impacted by its diameter. A narrower diameter restricts the flow, increasing pressure. This relationship is described by the principle of continuity in fluid dynamics, which states that the product of the flow rate and the cross-sectional area is constant for an incompressible fluid. Therefore, a smaller diameter fuel line will result in higher pressure, which can be beneficial in certain scenarios but may also lead to issues like fuel pump strain or even fuel line failure if not properly managed.
The choice of fuel line diameter should be made with consideration of the engine's requirements and the overall system design. A fuel line that is too small might not provide sufficient flow, leading to engine performance issues, while an overly large diameter could result in unnecessary fuel wastage and increased system complexity. Finding the right balance ensures that the fuel system operates efficiently, delivering the required fuel volume and pressure to the engine while maintaining system integrity.
In summary, the diameter of the fuel line is a critical design consideration, impacting both the flow rate and pressure of the fuel. Engineers and enthusiasts must carefully select the appropriate diameter to optimize engine performance and ensure the longevity of the fuel delivery system. Understanding this relationship is essential for anyone working with fuel lines, whether in a professional capacity or as a hobbyist, to make informed decisions and avoid potential issues related to fuel management.
Where to Find Red Kote Fuel Tank Liners: Your Ultimate Guide
You may want to see also
Fuel Line Length: Longer fuel lines may require additional support or reinforcement
When considering the use of alternative materials as fuel lines, it's important to address the potential challenges that longer fuel lines may present. One significant concern is the structural integrity and stability of the fuel line itself. Longer fuel lines, especially those made from non-traditional materials, might require additional support or reinforcement to ensure they can withstand the stresses and strains encountered during vehicle operation. This is particularly crucial in high-performance or heavy-duty applications where fuel lines are subjected to increased pressure and movement.
The length of a fuel line can impact its performance and longevity. Longer lines may be more susceptible to vibration, especially during acceleration and deceleration, which can lead to potential issues over time. To mitigate these risks, engineers often design fuel lines with specific flexing points and incorporate flexible materials that can absorb and distribute the vibrations effectively. This ensures that the fuel line remains intact and continues to function optimally without compromising the overall performance of the vehicle.
In some cases, longer fuel lines might also require additional protective measures. For instance, if the fuel line is routed through areas with potential impact hazards or extreme temperatures, it may need to be encased in protective sleeves or shields. These protective measures are essential to prevent damage from external factors, ensuring the fuel line's integrity and the safety of the vehicle's fuel system.
Furthermore, the installation process for longer fuel lines should be carefully executed. Proper routing and securement are critical to avoid excessive stress on the fuel line. Technicians must follow manufacturer guidelines and best practices to ensure that the fuel line is installed correctly, providing adequate support and minimizing the risk of damage or failure.
In summary, while exploring alternative materials for fuel lines, it is essential to consider the implications of longer fuel lines. Additional support, reinforcement, and protective measures may be necessary to ensure the fuel line's durability and performance. By addressing these considerations, engineers can design fuel systems that are both innovative and reliable, catering to the diverse needs of various vehicle applications.
Choosing the Right Hose for Your Diesel Fuel Return Line
You may want to see also
Fuel Line Routing: Proper routing prevents damage and ensures optimal fuel flow
Fuel lines are an essential component of any vehicle's fuel system, and proper routing is crucial to ensure optimal performance and prevent potential issues. The primary purpose of these lines is to transport fuel from the tank to the engine, and their placement can significantly impact the overall efficiency and longevity of the vehicle. When considering the routing of fuel lines, it's important to understand the potential risks and benefits associated with different placement options.
One critical aspect of fuel line routing is avoiding sharp bends or kinks. Fuel lines should be routed in a straight line as much as possible to minimize the risk of damage. Sharp bends can lead to fuel line wear and tear, especially at the bend points, which may result in fuel leaks or reduced fuel flow. It is recommended to use flexible fuel lines with a suitable diameter to accommodate gentle curves and bends without restricting flow. Proper support and protection are also essential; fuel lines should be secured using appropriate clamps or brackets to prevent them from being pinched or damaged by other vehicle components.
Additionally, fuel lines should be kept away from high-temperature areas, such as the exhaust manifold or engine block, as excessive heat can cause the fuel lines to degrade over time. This can lead to fuel leaks and potential engine misfires. It is advisable to route the fuel lines parallel to the ground or in a way that keeps them at a safe distance from heat sources. Furthermore, fuel lines should be protected from mechanical damage, such as impacts from suspension components or road debris. Using protective sleeves or routing the lines away from potential impact zones can help prevent damage.
In some cases, fuel lines may need to be routed through tight spaces or under specific vehicle components. In such scenarios, it is crucial to ensure that the lines are not subjected to excessive pressure or stress. Proper padding or insulation can be used to protect the fuel lines in these areas. Regular inspections are also recommended to identify any signs of wear, damage, or potential issues. By following these guidelines, vehicle owners and mechanics can ensure that fuel lines are properly routed, minimizing the risk of damage and optimizing fuel flow for efficient engine operation.
In summary, proper fuel line routing is a critical aspect of vehicle maintenance. It involves avoiding sharp bends, keeping lines away from heat sources, providing adequate protection, and ensuring the lines are not subjected to excessive stress. By following these practices, you can prevent damage, maintain optimal fuel flow, and ensure the long-term reliability of your vehicle's fuel system. Remember, regular inspections and maintenance are key to identifying and addressing any potential issues with fuel line routing.
Fuel Line Returns: Uncovering Hidden Costs and Benefits
You may want to see also
Fuel Line Compatibility: Fuel lines must be compatible with the fuel type and vehicle system
When it comes to fuel lines, compatibility is key to ensuring optimal performance and safety. The fuel line is a critical component in any vehicle's fuel system, responsible for transporting fuel from the tank to the engine. Using the wrong type of fuel line can lead to a range of issues, from reduced engine performance to potential safety hazards. Therefore, it is essential to understand the compatibility requirements for fuel lines.
The primary factor in determining fuel line compatibility is the type of fuel used in the vehicle. Different fuels have varying properties, such as volatility and chemical composition, which can affect the performance and longevity of the fuel line. For example, gasoline fuel lines are designed to withstand the volatility of gasoline, which can evaporate and potentially damage other components if not compatible. On the other hand, diesel fuel lines are engineered to handle the higher pressure and lubricating properties of diesel fuel. Using a fuel line designed for one type of fuel in a vehicle intended for another can lead to fuel leaks, engine misfires, or even more severe consequences.
Additionally, fuel lines must be compatible with the specific vehicle system they are intended for. Different vehicle manufacturers use various fuel system designs, such as electronic fuel injection or carbureted systems. These systems have unique requirements for fuel line materials, diameters, and routing. For instance, a fuel line designed for a high-pressure electronic fuel injection system may have a different inner diameter and wall thickness compared to a line for a carbureted engine. Using a fuel line that doesn't match the vehicle's system can result in improper fuel delivery, reduced power, or even engine damage.
To ensure compatibility, it is crucial to consult the vehicle's manual or seek professional advice when selecting fuel lines. Automotive experts can provide guidance on the specific fuel line requirements for a particular make and model. They can also offer recommendations on the best materials and brands to ensure a proper fit and optimal performance. Using high-quality, compatible fuel lines is an investment in the vehicle's longevity and reliability, ensuring that the fuel system operates efficiently and safely.
In summary, fuel line compatibility is essential for maintaining a vehicle's performance and safety. The type of fuel used and the specific vehicle system must be considered when choosing fuel lines. By selecting the right fuel lines, vehicle owners can ensure efficient fuel delivery, optimal engine performance, and peace of mind, knowing their fuel system is operating as intended.
Mastering the Art of Fitech Fuel Line Routing: A Comprehensive Guide
You may want to see also
Frequently asked questions
No, not all metals are suitable for fuel lines. The material used for fuel lines must be compatible with the type of fuel it will carry and resistant to corrosion and degradation over time. Common materials include stainless steel, aluminum, and copper alloys, which are known for their durability and ability to withstand the corrosive effects of fuels.
While some plastics can be used for fuel lines, they are generally not recommended for high-performance or high-temperature applications. High-performance vehicles often require materials that can withstand rapid acceleration, extreme temperatures, and potential fuel additives. Rubber or specialized synthetic materials like fluoropolymers are more commonly used in such cases.
Yes, fuel lines can often be repaired or replaced individually without the need to replace the entire fuel system. It is important to use compatible replacement parts and ensure proper installation to maintain the integrity of the fuel system. Regular inspection and maintenance can help identify and fix issues before they cause major problems.
Yes, regular maintenance is crucial for fuel lines. This includes checking for any signs of damage, cracks, or leaks, especially after accidents or extreme weather conditions. It is also recommended to use fuel line protectants to prevent degradation and to ensure that the fuel lines are properly secured to avoid damage from vibrations.