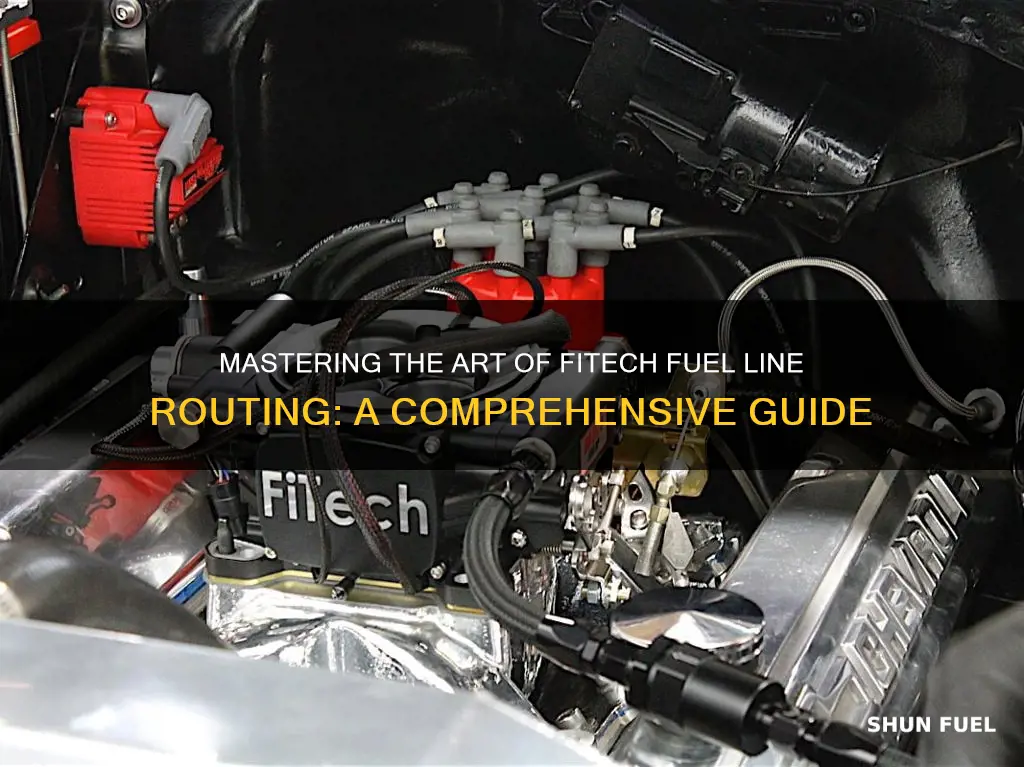
Routing FITECH fuel lines requires careful planning and adherence to specific guidelines to ensure optimal performance and safety. This process involves several key steps, including selecting the appropriate fuel line material, considering the vehicle's layout and engine configuration, and implementing secure mounting techniques. Understanding the unique characteristics of FITECH fuel lines, such as their flexibility and resistance to heat and fuel degradation, is essential for successful installation. By following a systematic approach, including proper preparation, precise measurement, and secure attachment, you can effectively route FITECH fuel lines to meet the demands of your vehicle's fuel system.
What You'll Learn
- Fuel Line Material Selection: Choose the right material for your fuel lines, considering factors like temperature resistance and flexibility
- Routing Techniques: Explore different methods for routing fuel lines, such as using bends, loops, and straight runs
- Clamping and Securing: Learn proper clamping techniques to ensure a secure and leak-free connection for fuel lines
- Grounding and Shielding: Understand the importance of grounding and shielding fuel lines to prevent electromagnetic interference
- Testing and Inspection: Discover methods for testing and inspecting fuel lines for leaks, blockages, and proper functionality
Fuel Line Material Selection: Choose the right material for your fuel lines, considering factors like temperature resistance and flexibility
When it comes to selecting the appropriate material for your fuel lines, especially when using Fitech fuel systems, it's crucial to consider the specific requirements of your vehicle and the fuel system's operating conditions. The material choice directly impacts the performance, longevity, and safety of your fuel delivery system. Here's a comprehensive guide to help you make an informed decision:
Temperature Resistance: One of the most critical factors in fuel line material selection is temperature resistance. Fuel lines must withstand the extreme temperature variations that engines experience. For most automotive applications, rubber-based materials are commonly used due to their flexibility and durability. Natural rubber can handle a wide temperature range, typically from -40°F to 250°F. However, for higher-performance vehicles or those operating in more extreme conditions, you might consider synthetic rubber compounds like SBR (Styrene-Butadiene Rubber) or EPDM (Ethylene Propylene Diene Monomer). These synthetic rubbers offer improved temperature resistance, often up to 250°F or higher, making them suitable for high-performance engines.
Flexibility and Durability: Fuel lines need to be flexible to accommodate engine movement and vibrations during operation. The material should also be durable to resist wear and tear from engine components, road debris, and other potential hazards. As mentioned earlier, rubber is an excellent choice for flexibility. Natural rubber provides a good balance of flexibility and strength, ensuring the fuel lines can move with the engine without becoming brittle or cracking. For added durability, consider fuel lines made from braided rubber, which offers enhanced resistance to abrasion and kinking.
Chemical Compatibility: Ensure that the chosen material is compatible with the fuel type your vehicle uses. Different fuels have varying chemical compositions, and some materials may degrade or become brittle when exposed to certain fuels over time. For example, ethanol-blended fuels may require materials with better resistance to ethanol's corrosive effects. Always refer to the manufacturer's guidelines and consult with experts if needed to select the most compatible material.
Size and Routing: The size and routing of fuel lines are essential considerations. Fitech fuel systems often offer various line sizes to accommodate different fuel flow requirements. Select the appropriate diameter to ensure optimal fuel delivery without excessive pressure drop. Additionally, plan the fuel line routing carefully to avoid tight bends, sharp corners, or routes that could interfere with engine components or other systems. Proper routing ensures easy access for maintenance and minimizes the risk of damage.
Installation and Maintenance: Proper installation techniques are vital to ensure the longevity of your fuel lines. Follow the manufacturer's instructions for installation, including any specific requirements for sealing and securing the lines. Regular maintenance, such as checking for cracks, leaks, or signs of degradation, is also essential. Inspect the fuel lines periodically, especially after extended use or exposure to harsh conditions, to identify any potential issues early on.
Thawing Diesel Fuel Lines: Optimal Temperature for Winter
You may want to see also
Routing Techniques: Explore different methods for routing fuel lines, such as using bends, loops, and straight runs
When it comes to routing FITECH fuel lines, there are several techniques to ensure optimal performance and aesthetics. One common approach is to utilize bends, which allow for the necessary curvature to accommodate the layout of your engine bay. Bends can be made from various materials, such as metal or flexible plastic, and should be chosen based on the desired flexibility and durability. It's important to measure and mark the desired bend angles before cutting to ensure a precise fit. Start by identifying the starting point of the fuel line and measure the required angle of the bend. Then, carefully cut the line at the marked point and shape it accordingly. Remember to avoid sharp bends that could restrict flow or cause damage over time.
Loops are another effective routing method, especially when dealing with longer fuel lines. Creating loops helps to reduce stress on the line and prevents sharp bends that could lead to potential issues. To create a loop, identify a suitable location near the fuel source or tank. Measure and mark the desired length of the loop, ensuring it is long enough to provide easy access and not interfere with other components. Carefully cut the fuel line to the marked length and then fold it into a loop, securing it temporarily with tape or a clamp. This technique allows for better organization and makes it easier to maintain the fuel line's integrity.
Straight runs are essential to maintain optimal fuel flow and pressure. When implementing straight sections, ensure that the fuel line is securely attached to the fittings and that there are no kinks or obstructions. Measure the length required for the straight run and cut the fuel line accordingly. Use appropriate connectors or clamps to attach the straight section to the fittings, ensuring a tight and leak-free connection. Straight runs should be kept as short as possible to minimize the risk of fuel pressure drops or flow restrictions.
Additionally, consider the use of fuel line sleeves or protective covers to safeguard the routing process. These sleeves provide insulation and protection against potential damage from sharp edges or high temperatures. They can be especially useful when running fuel lines alongside other components or in areas with limited space. Ensure that the sleeves are properly installed, allowing for easy movement of the fuel lines while maintaining their integrity.
In summary, routing FITECH fuel lines effectively involves a combination of bends, loops, and straight runs. Bends should be carefully measured and shaped, loops should be created to reduce stress, and straight sections should be kept short and securely attached. By employing these techniques and considering the use of protective sleeves, you can ensure a well-organized and efficient fuel line setup, contributing to the overall performance and longevity of your vehicle's fuel system.
Peacock Fuel Line Woes: What to Do?
You may want to see also
Clamping and Securing: Learn proper clamping techniques to ensure a secure and leak-free connection for fuel lines
When it comes to routing FITECH fuel lines, proper clamping and securing techniques are essential to ensure a reliable and leak-free fuel system. Clamps play a critical role in maintaining the integrity of the fuel lines, preventing leaks, and ensuring optimal performance. Here's a detailed guide on how to clamp and secure your FITECH fuel lines effectively:
Understanding the Clamping System: Familiarize yourself with the type of clamps used in FITECH fuel line installations. Typically, these clamps are designed to provide a tight and secure grip around the fuel lines. They often feature a robust construction with a smooth interior surface to avoid damaging the fuel lines. Understanding the specific clamp design will enable you to apply the correct clamping techniques.
Preparation and Placement: Before clamping, ensure that the fuel lines are clean and free of any debris or contaminants. Use a suitable cleaner to remove any dirt or old clamp residue. Measure and mark the desired clamping points along the fuel lines, ensuring they are spaced appropriately according to the manufacturer's guidelines. Proper placement is crucial to maintaining the fuel line's integrity and preventing excessive stress on the lines.
Clamping Technique: When clamping, apply firm pressure to create a secure hold. Start by positioning the clamp around the fuel line, ensuring it is centered and aligned with the marked spot. Use a wrench or a specialized clamp tool to tighten the clamp, but be cautious not to overtighten, as this can damage the fuel line. The goal is to achieve a snug fit without causing any bends or kinks in the line. Repeat this process for each clamping point, ensuring an even and consistent clamp throughout the fuel line route.
Leak-Proof Connections: To ensure a leak-free connection, pay close attention to the joints and intersections of the fuel lines. Use pipe dope or fuel line tape on the threads of any fittings or connections before tightening. This additional layer of protection creates a barrier against fuel leakage. Regularly inspect the clamped areas for any signs of wear or damage, especially in high-stress areas, and replace any worn-out clamps promptly.
Final Adjustments and Testing: After clamping and securing all the fuel lines, give the system a thorough inspection. Check for any visible signs of damage, such as cracks or bends in the lines. Ensure that all clamps are tight and secure. Consider using a fuel pressure tester to verify the integrity of the fuel system. This step is crucial to identify any potential issues before the final installation, ensuring a safe and efficient fuel supply.
Sonoma Fuel Lines: Uncovering Hidden Intake Secrets
You may want to see also
Grounding and Shielding: Understand the importance of grounding and shielding fuel lines to prevent electromagnetic interference
Grounding and shielding are critical aspects of fuel line installation, especially when dealing with high-performance fuel systems like those used in racing or modified vehicles. These techniques help prevent electromagnetic interference (EMI) from affecting the performance and reliability of your fuel system. Here's a detailed look at why grounding and shielding are essential and how to implement them effectively:
Understanding Electromagnetic Interference:
Electromagnetic interference can disrupt the smooth flow of fuel within your engine's system. It can cause erratic behavior, such as fuel pump failures, incorrect fuel pressure readings, and even engine misfires. EMI is generated by various sources, including electrical components, ignition systems, and even other electronic devices in your vehicle. When these electromagnetic waves interact with the fuel lines, they can induce voltage and currents, leading to interference.
The Role of Grounding:
Grounding serves as a direct path for electrical charges to flow into the earth. In the context of fuel lines, grounding helps to dissipate any induced currents or voltages caused by EMI. By grounding the fuel lines, you create a stable reference point, ensuring that any electromagnetic interference is safely directed to the ground rather than causing disruptions within the fuel system. This is particularly important in high-performance applications where fuel pressure and flow rates are critical.
Shielding Techniques:
Shielding involves creating a conductive barrier around the fuel lines to block electromagnetic waves. This can be achieved using various materials, such as braided copper wire, copper tubing, or even specialized shielding tape. The shielding material should be connected to the vehicle's ground point to ensure proper grounding. Wrapping the fuel lines with shielding material and securing it in place is essential to maintain a continuous conductive path. This technique is especially useful when running fuel lines alongside electrical cables or near other sources of EMI.
Implementing Grounding and Shielding:
- Route Fuel Lines Strategically: Plan the fuel line route to minimize exposure to potential EMI sources. Keep them away from electrical components and high-voltage areas.
- Grounding Connections: Ensure all grounding points are secure and properly connected to the vehicle's chassis or a dedicated ground strap. Use high-quality grounding clips or straps to establish a reliable connection.
- Shielding Installation: Wrap the fuel lines with shielding material, ensuring it is tightly secured and free of any kinks or sharp bends that could compromise its effectiveness. Connect the shielding to the ground point to create a continuous conductive path.
- Regular Maintenance: Periodically inspect the grounded and shielded fuel lines for any signs of damage or disconnection. Tighten connections and replace any compromised shielding to maintain optimal performance.
By implementing proper grounding and shielding techniques, you can ensure that your FITECH fuel system operates reliably and efficiently, even in high-performance or modified vehicle applications. This attention to detail will contribute to a smoother driving experience and enhanced overall engine performance.
Understanding the Significance of the 3 Lines on Your Fuel Pump
You may want to see also
Testing and Inspection: Discover methods for testing and inspecting fuel lines for leaks, blockages, and proper functionality
When it comes to testing and inspecting FITECH fuel lines, there are several methods to ensure they are functioning correctly and free from leaks or blockages. One of the most common techniques is the use of a fuel pressure gauge. This tool measures the pressure of the fuel in the system and can help identify potential issues. Start by connecting the gauge to the fuel line, ensuring a tight seal. Then, with the engine off, measure the pressure. A healthy fuel system should have a specific pressure range, typically between 40-60 psi. If the pressure is significantly higher or lower than this range, it may indicate a blockage or leak.
Another effective method is the use of a smoke machine or a fog machine. These devices produce a fine mist that can be injected into the fuel lines. By introducing smoke or fog, you can visually inspect the lines for any leaks. Start by disconnecting the fuel lines from the fuel tank and engine. Then, carefully inject the smoke or fog into the system, ensuring it reaches all parts of the fuel lines. Leaks will be visible as small clouds or droplets, allowing you to pinpoint the exact location of the issue.
Visual inspection is also a crucial step in the testing process. Carefully examine the fuel lines for any signs of damage, cracks, or corrosion. Look for any discolored or softened areas, as these could indicate leaks or blockages. Pay close attention to bends and fittings, as these areas are prone to wear and tear. If any issues are found, it is essential to address them promptly to prevent further damage.
In addition to visual checks, you can use a fuel line inspection tool, often referred to as a fuel line tester. This tool typically consists of a small, flexible probe that can be inserted into the fuel line. By applying a small amount of pressure, the tester can detect leaks and measure the flow rate. It is a quick and efficient way to identify issues, especially in hard-to-reach areas.
Lastly, it is recommended to test the fuel lines under different operating conditions. Start the engine and listen for any unusual noises, such as hissing or roaring, which could indicate a leak. Also, check for any changes in engine performance, as a blocked or leaking fuel line can cause reduced power and efficiency. By following these testing and inspection methods, you can ensure that your FITECH fuel lines are in optimal condition, providing reliable performance.
Understanding Fuel Line Flaring: A Comprehensive Guide
You may want to see also
Frequently asked questions
When routing FITECH fuel lines, it's important to prioritize safety and functionality. Start by identifying the fuel tank, pump, and various fuel injectors or carburetor locations. Route the lines away from moving parts and high-heat sources to prevent damage. Use flexible fuel lines with appropriate fittings and ensure they are securely attached to the fuel components. Consider using a fuel line protector or shield to safeguard against potential impacts or damage during installation.
While regular automotive fuel lines may seem like a cost-effective alternative, it's generally recommended to use FITECH fuel lines for optimal performance and safety. FITECH lines are specifically designed to withstand high pressure, temperature fluctuations, and resistance to fuel contamination. They offer better flexibility and durability, reducing the risk of leaks or damage over time. Always refer to the vehicle's manual or consult a professional for the recommended fuel line specifications.
To achieve a secure connection, start by cleaning the fuel injectors and fuel line ends with a suitable solvent to remove any contaminants. Apply a thin layer of fuel line sealant or thread seal tape to the male end of the fuel line. Then, thread it onto the fuel injector, ensuring a tight fit. Use a fuel line crimping tool to create a secure crimp, following the manufacturer's instructions. This process ensures a reliable and leak-free connection.
Yes, a few specialized tools are necessary for a successful installation. You'll need a fuel line crimping tool to create secure connections, as mentioned earlier. Additionally, a fuel line cutter or a pair of sharp scissors can be useful for trimming the lines to the desired length. It's also a good idea to have a fuel line brush or a small brush to clean the fuel injectors and lines before assembly. These tools will help ensure a professional and leak-free installation.
When dealing with tight spaces or complex fuel systems, careful planning is essential. Consider using flexible fuel lines with a slightly larger diameter to allow for easier routing. Take your time to measure and mark the desired line paths, ensuring they are free from obstructions. If necessary, consult a professional mechanic or refer to detailed vehicle diagrams to navigate the fuel system layout. Patience and precision are key to a successful and safe fuel line installation.