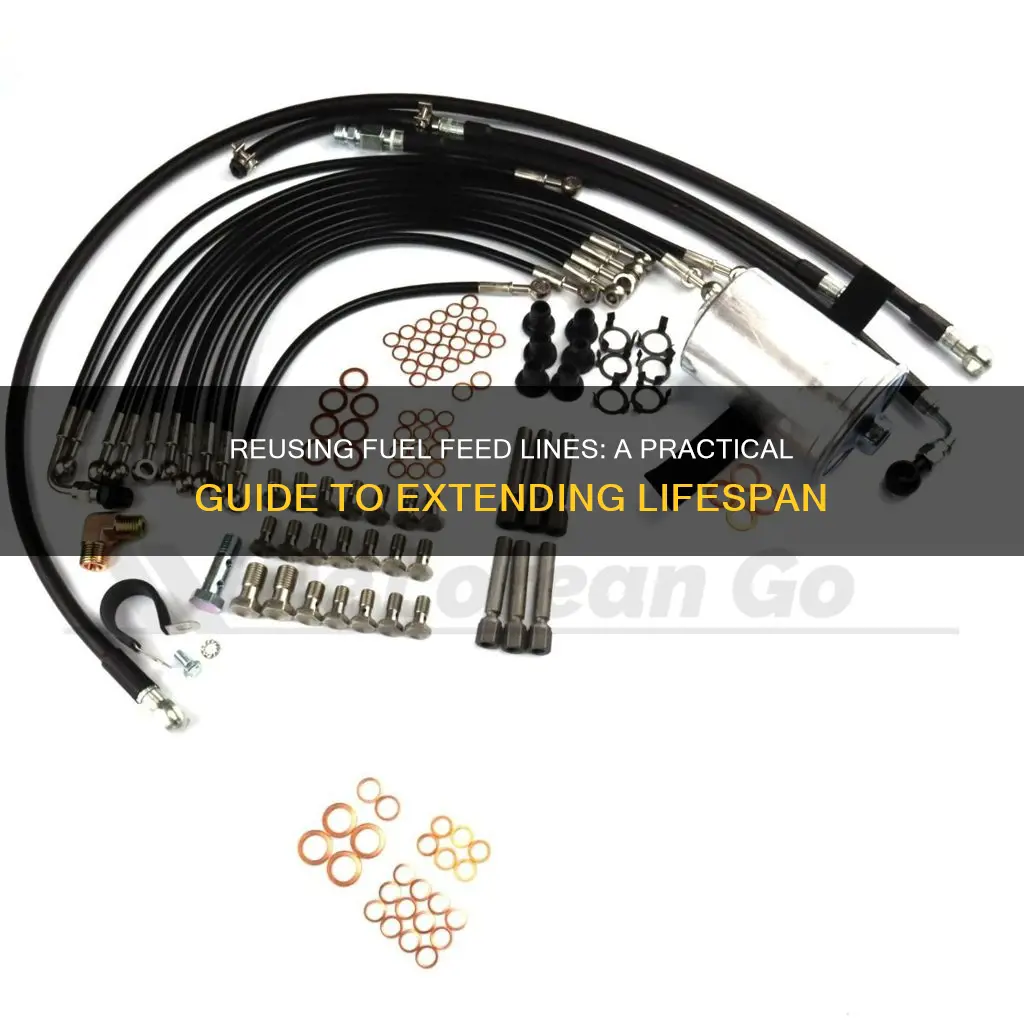
The question of whether a fuel feed line can be reused is an important consideration for vehicle maintenance and safety. Fuel feed lines, which deliver fuel from the tank to the engine, are crucial components that can wear out over time due to factors like fuel contamination, age, and environmental conditions. Reusing a fuel feed line without proper inspection and replacement can lead to potential issues such as fuel leaks, engine performance problems, and even safety hazards. This paragraph will explore the factors to consider when deciding whether to reuse or replace a fuel feed line, including the condition of the existing line, the type of fuel used, and the overall maintenance history of the vehicle.
Characteristics | Values |
---|---|
Reuse Potential | Yes, fuel feed lines can be reused under certain conditions. |
Material Compatibility | The material of the feed line should be compatible with the fuel type to avoid corrosion or degradation. |
Condition of Feed Line | Inspect for any signs of damage, cracks, or leaks before reusing. |
Fuel Type | Different fuels may require specific feed lines; e.g., ethanol blends might need lines designed to handle higher ethanol concentrations. |
System Design | The overall fuel system design should accommodate reused components to ensure proper functionality. |
Maintenance | Regular maintenance and cleaning can extend the life of the feed line and ensure optimal performance. |
Regulations | Adhere to local and industry regulations regarding the reuse of fuel system components. |
Expert Consultation | Consult with experts or manufacturers for specific guidelines and recommendations. |
What You'll Learn
- Material Compatibility: Reusing fuel feed lines requires checking material compatibility with new fuel
- Pressure Testing: Reusable lines must pass pressure tests to ensure integrity
- Corrosion Resistance: Lines should be resistant to corrosion from fuel to prevent degradation
- Flexibility: Flexibility is crucial for feed lines to withstand engine vibrations and movement
- Maintenance: Regular maintenance is essential to ensure the line's longevity and performance
Material Compatibility: Reusing fuel feed lines requires checking material compatibility with new fuel
When considering reusing fuel feed lines, material compatibility is a critical factor that should not be overlooked. The original fuel feed line may have been designed and manufactured with specific fuel types in mind, and reusing it with a different fuel can lead to potential issues. The compatibility of the materials used in the feed line with the new fuel is essential to ensure the system's safety and performance.
Different fuels have varying chemical compositions and properties, which can cause reactions with the materials in the feed line. For example, some fuels may contain corrosive substances that can deteriorate the inner lining of the feed line over time, leading to leaks or contamination. Additionally, the temperature and pressure conditions of the fuel system can also impact material compatibility. Higher temperatures and pressures may accelerate the degradation of certain materials, making them unsuitable for long-term reuse.
To ensure material compatibility, it is crucial to consult the manufacturer's guidelines and specifications for the original fuel feed line. These guidelines often provide information on the recommended fuels and any specific requirements for maintenance and replacement. By understanding the original design's intent and the materials used, you can make an informed decision about reusing the feed line.
If reusing the feed line is deemed acceptable, it is essential to perform thorough inspections and testing. This includes checking for any signs of wear, corrosion, or damage that may have occurred during the initial use. Visual inspections, pressure tests, and material analysis can help identify any potential issues. Furthermore, it is advisable to consult with experts or engineers who can provide guidance on the compatibility of the new fuel with the existing feed line materials.
In summary, reusing fuel feed lines requires a careful assessment of material compatibility to ensure the system's integrity and performance. By considering the chemical properties of the fuel, consulting manufacturer guidelines, and conducting thorough inspections, one can make an informed decision about the feasibility of reusing the feed line while maintaining safety standards.
Unleash the Power: Breaking Fuel Lines: A Quarry Decision
You may want to see also
Pressure Testing: Reusable lines must pass pressure tests to ensure integrity
When considering the reuse of fuel feed lines, it is crucial to understand the importance of pressure testing as a critical quality control measure. Reusable lines, often made from durable materials like stainless steel or aluminum, must undergo rigorous testing to ensure their structural integrity and reliability. This process is essential to guarantee that the lines can withstand the pressures associated with fuel delivery systems without compromising performance or safety.
Pressure testing involves subjecting the fuel feed lines to specific pressure levels, typically simulating the conditions they would experience in a vehicle's fuel system. The primary goal is to identify any potential weaknesses, leaks, or structural failures that might occur over time. By applying controlled pressure, technicians can assess the line's ability to maintain a tight seal and prevent fuel leakage. This is particularly important as fuel feed lines are responsible for transporting fuel from the tank to the engine, and any failure could lead to engine misfires, reduced performance, or even dangerous fuel leaks.
The testing process typically involves the use of specialized equipment, such as pressure gauges and test fixtures, to measure and control the pressure applied to the lines. Technicians will gradually increase the pressure and monitor for any signs of stress or failure. Common methods include hydrostatic testing, where water is used to simulate fuel pressure, or pneumatic testing, utilizing compressed air. These tests should be conducted at various pressure levels to cover a range of potential real-world scenarios.
For reusable fuel feed lines to be considered safe and reliable, they must pass these pressure tests with flying colors. Any signs of damage, such as cracks, bends, or leaks, indicate that the line has failed the test and should not be reused. It is essential to document the test results and any defects found to ensure proper maintenance and replacement of faulty lines. Regular pressure testing can also help identify wear and tear over time, allowing for proactive maintenance and extending the lifespan of the fuel feed lines.
In summary, pressure testing is a vital step in the process of reusing fuel feed lines. It ensures that the lines can handle the demands of fuel delivery systems, providing peace of mind to vehicle owners and operators. By adhering to strict testing protocols, technicians can maintain the integrity of the fuel system, optimize engine performance, and ultimately enhance the overall reliability of the vehicle.
In-Line Fuel Pump Installation: Engine Bay or Fuel Tank?
You may want to see also
Corrosion Resistance: Lines should be resistant to corrosion from fuel to prevent degradation
When considering the reuse of fuel feed lines, one critical aspect to evaluate is the material's corrosion resistance. Fuel feed lines are exposed to harsh environments, and the fuel itself can be corrosive over time. Therefore, it is essential to choose materials that can withstand the corrosive effects of the fuel to ensure the longevity and reliability of the system.
Corrosion resistance is a key factor in determining the suitability of a fuel feed line for reuse. The fuel, often containing various additives and impurities, can lead to the degradation of the line's material. Common fuels, such as gasoline, diesel, and aviation fuel, contain acids and other corrosive substances that can attack the metal surface of the feed line. This corrosion can result in the formation of rust, pitting, or even cracking of the line, compromising its structural integrity.
To prevent degradation, it is recommended to use materials with excellent corrosion resistance. Stainless steel, for instance, is a popular choice for fuel feed lines due to its inherent corrosion-resistant properties. The stainless steel alloy contains chromium, which forms a protective oxide layer on the surface, preventing further corrosion. This protective layer ensures that the fuel feed line can withstand the corrosive nature of the fuel and maintain its structural integrity over time.
Additionally, the design and construction of the fuel feed line play a vital role in corrosion resistance. The line should be free from sharp bends or kinks, as these can create stress concentrations, making the material more susceptible to corrosion. Smooth, seamless construction is ideal to minimize the risk of fuel contact with the line's inner surface, reducing the potential for corrosion.
In summary, when reusing fuel feed lines, it is crucial to prioritize corrosion resistance. The chosen material should be able to withstand the corrosive effects of the fuel to prevent degradation and ensure the system's reliability. By selecting appropriate materials and considering the design aspects, engineers can make informed decisions to maximize the lifespan of fuel feed lines while maintaining the integrity of the fuel delivery system.
Fuel Line Fixes: A Step-by-Step Guide to Car Repairs
You may want to see also
Flexibility: Flexibility is crucial for feed lines to withstand engine vibrations and movement
Flexibility is a critical aspect of fuel feed lines, especially in the context of engine vibrations and movement. The fuel feed line is responsible for delivering fuel from the tank to the engine, and it must be able to accommodate the dynamic nature of the engine's operation. Engine vibrations, caused by the combustion process and the movement of the engine components, can exert significant stress on the feed line. If the line is not flexible enough, it may become damaged or kinked, leading to potential fuel leaks or reduced fuel flow.
The design of the feed line incorporates flexibility to ensure it can move with the engine without compromising its integrity. This flexibility is achieved through the use of materials and construction techniques that allow for a certain degree of bending and twisting. The line is typically made from durable, yet pliable materials such as rubber or flexible plastic compounds. These materials possess the necessary elasticity to absorb vibrations and maintain their shape under varying conditions.
In addition to the material properties, the construction of the feed line also plays a vital role in its flexibility. The line is often designed with a braided or spiral structure, which adds flexibility and reduces the risk of kinking. This design allows the line to bend and adjust to the engine's movement, ensuring a consistent and secure connection between the fuel tank and the engine. The flexibility of the feed line is further enhanced by the use of protective sleeves or coatings, which shield the line from potential damage caused by engine components or harsh environments.
Engineers and designers carefully consider the flexibility requirements during the feed line manufacturing process. They conduct rigorous testing to ensure the line can withstand the expected vibrations and movements without compromising its performance. This includes subjecting the feed line to simulated engine conditions and analyzing its behavior under stress. By meeting these flexibility standards, the fuel feed line can reliably deliver fuel to the engine, even in the presence of intense vibrations and movement.
In summary, flexibility is essential for fuel feed lines to endure the challenging conditions within an engine. The line's ability to flex and adapt to engine vibrations and movement ensures a secure and consistent fuel supply. Through careful material selection, construction techniques, and rigorous testing, engineers create feed lines that can withstand the rigors of engine operation, providing a reliable and efficient fuel delivery system.
Fuel Line Removal Guide: 2008 RMZ450
You may want to see also
Maintenance: Regular maintenance is essential to ensure the line's longevity and performance
Regular maintenance is a critical aspect of vehicle ownership and can significantly impact the longevity and performance of your fuel feed lines. These lines are responsible for delivering fuel from the tank to the engine, and over time, they can experience wear and tear due to various factors such as fuel contamination, temperature changes, and general degradation. Neglecting maintenance can lead to reduced engine performance, increased fuel consumption, and even potential engine damage.
One of the primary reasons for regular maintenance is to prevent fuel contamination. Over time, fuel can absorb moisture and other impurities from the air, leading to the formation of sludge and varnish. These contaminants can clog the fuel feed lines, reducing fuel flow and potentially causing engine misfires or stalling. Regular maintenance involves using fuel stabilizers and performing fuel system flushes to remove these impurities and ensure clean fuel delivery.
Another essential maintenance task is to inspect and replace worn-out components. Fuel feed lines, especially those with flexible materials, can degrade due to constant flexing and exposure to fuel chemicals. Cracks, leaks, or kinks in the lines can lead to fuel leaks, which are dangerous and can cause environmental damage. Regular inspections should include checking for any signs of damage, corrosion, or leaks. If any issues are found, the affected lines or components should be replaced promptly to maintain optimal performance.
Additionally, maintaining the correct fuel pressure is crucial for efficient engine operation. Fuel pressure regulators and pumps can wear out over time, leading to inconsistent fuel delivery. Regular maintenance involves checking and adjusting fuel pressure to ensure it meets the manufacturer's specifications. This can be done using specialized tools and equipment, and it is often recommended to consult a professional mechanic for accurate pressure readings.
In summary, regular maintenance of fuel feed lines is vital to guarantee their longevity and optimal performance. By implementing a comprehensive maintenance routine, including fuel contamination prevention, component inspection and replacement, and fuel pressure management, vehicle owners can ensure their engines run smoothly and efficiently. It is always advisable to follow the manufacturer's guidelines and consult automotive experts for specific maintenance requirements to keep vehicles in top condition.
Optimizing Performance: Choosing the Right Fuel Line for Your TMAXX
You may want to see also
Frequently asked questions
Yes, a fuel feed line can be reused if it has been previously replaced and is in good condition. It is common for fuel lines to be replaced due to wear and tear, damage, or corrosion, and if the original line was of good quality and properly installed, it can be reused. However, it is essential to inspect the line for any signs of deterioration, cracks, or leaks before reinstalling it.
Reusing a fuel feed line without proper inspection can pose several risks. Over time, fuel lines can develop cracks, especially in areas with high stress or vibration. These cracks may not be visible to the naked eye and can lead to fuel leaks, which can cause engine misfires, reduced performance, or even a fire hazard. It is crucial to ensure that the line is free from damage and has not exceeded its recommended service life to avoid potential issues.
To determine if a fuel feed line can be reused, you should inspect it thoroughly. Check for any visible signs of damage, such as cracks, brittleness, or corrosion. Ensure that the line is not bent or kinked, as this can affect its performance. Measure the line's length and compare it to the original specifications to ensure it matches. If the line passes the inspection and meets the required standards, it can be safely reused. Otherwise, it is advisable to replace it with a new one to maintain optimal engine performance and safety.