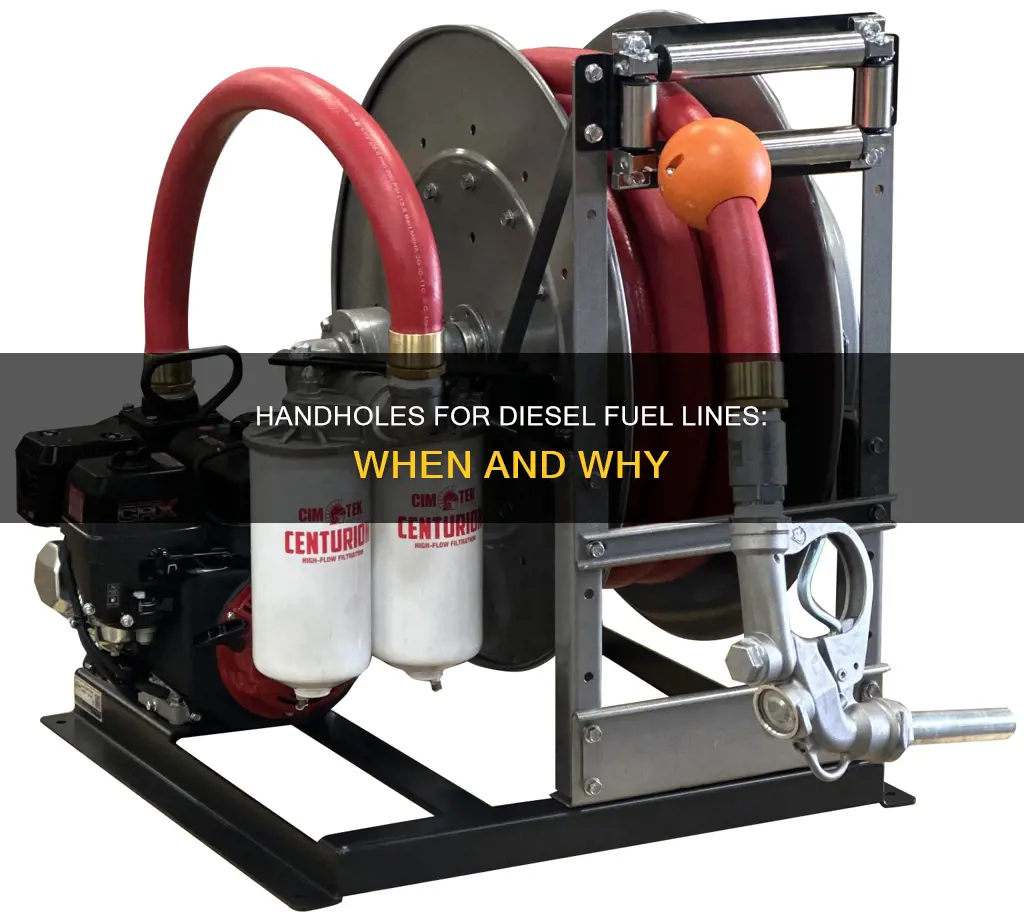
Handholes for diesel fuel lines are essential components in the design of fuel systems, especially in heavy-duty vehicles and marine applications. These handholes are strategically placed along the fuel lines to provide easy access for maintenance, repairs, and inspections. They are typically installed at regular intervals, allowing technicians to quickly locate and address any issues with the fuel lines, such as leaks, blockages, or damage. Understanding when and where to install handholes is crucial for ensuring the reliability and safety of diesel fuel systems, as it enables prompt maintenance and helps prevent potential failures.
What You'll Learn
- Handholes Placement: Strategically locate handholes for easy access to fuel lines
- Hose Routing: Ensure proper hose routing to prevent damage and maintain order
- Ventilation: Provide adequate ventilation to prevent fuel line overheating and potential hazards
- Insulation: Insulate fuel lines to protect against extreme temperatures and corrosion
- Maintenance Access: Design handholes with maintenance access points for regular inspections and repairs
Handholes Placement: Strategically locate handholes for easy access to fuel lines
When designing a fuel system for diesel engines, the strategic placement of handholes is crucial for maintenance and repair. Handholes are small openings in the fuel lines that provide access points for technicians to inspect, clean, or replace components. Proper placement ensures that these handholes are easily accessible, allowing for efficient and timely maintenance.
The location of handholes should be carefully considered to avoid interference with other components and to ensure they are visible and accessible during routine inspections. A common practice is to place handholes at regular intervals along the fuel lines, typically every 10 to 15 feet. This spacing allows for quick identification and access to specific sections of the fuel system, making it easier to locate potential issues.
In addition to spacing, the height and angle of handholes are essential factors. Handholes should be positioned at a comfortable working height, usually around 3 to 4 feet above the ground, to prevent strain on technicians' backs and necks. A slight downward angle is also recommended to allow any debris or contaminants to fall away from the handhole, keeping the work area clean and safe.
When designing the fuel system layout, it is important to consider the engine's orientation and the direction of fuel flow. Handholes should be placed in a way that aligns with the natural flow of the fuel lines, making it easier to navigate and access different sections of the system. This alignment also ensures that handholes are not obstructed by other components, providing a clear path for maintenance.
Furthermore, handholes should be clearly marked and labeled to prevent confusion. Each handhole should have a unique identifier, such as a color-coded cap or a small label, to indicate its specific location and purpose. This practice is especially important in large fuel systems with multiple handholes, ensuring that technicians can quickly identify the correct access point for their maintenance tasks. Proper handhole placement and labeling contribute to a well-organized and efficient fuel system, reducing downtime and improving overall maintenance productivity.
Understanding Fuel Tank Liners: Protection for Your Vehicle's Fuel System
You may want to see also
Hose Routing: Ensure proper hose routing to prevent damage and maintain order
When dealing with diesel fuel lines, proper hose routing is crucial to ensure the system's longevity and functionality. The fuel lines are often exposed to various environmental factors and potential hazards, so careful planning and execution of hose routing are essential. Here's a detailed guide on how to ensure proper hose routing:
- Identify Potential Hazards: Before starting the routing process, it's important to identify potential hazards that the fuel lines might encounter. These could include sharp edges, vibrations, heat sources, or areas with potential impact. Understanding these hazards will help you make informed decisions about the routing path. For example, if the fuel lines are near a moving part, you might need to route them away from the potential impact zone to prevent damage.
- Choose the Right Hose Material: Selecting the appropriate hose material is critical for durability and flexibility. Different materials offer varying levels of resistance to heat, chemicals, and abrasion. For diesel fuel lines, consider using hoses made from high-quality rubber or synthetic materials that can withstand the fuel's properties and environmental conditions. Ensure the hoses are compatible with the fuel type and temperature ranges you expect.
- Route the Hoses Away from Heat Sources: Diesel fuel lines should be routed away from any heat sources, such as exhaust systems, engines, or hot surfaces. Prolonged exposure to high temperatures can cause the hoses to degrade and potentially fail. Maintain a safe distance between the fuel lines and heat sources, and consider using heat shields or insulation if necessary. Proper spacing will help prevent damage and ensure the hoses remain in good condition.
- Secure the Hoses: Properly secure the hoses to prevent movement and potential damage. Use hose clips or ties to keep the hoses in place, ensuring they are not twisted or kinked. Avoid tightening the clips too much, as this can restrict flow and cause stress on the hose material. Allow for some flexibility in the routing to accommodate minor vibrations or temperature changes without causing strain.
- Maintain Order and Organization: Keep the fuel line routing neat and organized to facilitate maintenance and troubleshooting. Avoid crossing or intertwining hoses, as this can lead to confusion and potential damage during repairs or inspections. Use hose guides or sleeves to keep the lines straight and prevent tangling. A well-organized routing system will make it easier to identify issues and perform maintenance tasks efficiently.
- Regular Inspection: Implement a regular inspection schedule to check the hose routing and overall condition of the fuel lines. Look for signs of wear, cracks, or damage, especially in areas prone to impact or vibration. Promptly address any issues found during inspections to prevent further deterioration. Regular maintenance will help ensure the system's reliability and extend the lifespan of the fuel lines.
By following these guidelines, you can effectively manage hose routing for diesel fuel lines, minimizing the risk of damage and ensuring a well-organized system. Proper routing is a critical aspect of maintaining a reliable and safe fuel system, especially in heavy-duty applications where diesel fuel is commonly used.
Harley Sportster Fuel Line: Unveiling the Optimal Diameter
You may want to see also
Ventilation: Provide adequate ventilation to prevent fuel line overheating and potential hazards
Ventilation is a critical aspect of maintaining a safe and efficient fuel system, especially when dealing with diesel fuel lines. Proper ventilation ensures that any potential hazards associated with fuel line overheating are mitigated, preventing dangerous situations and costly repairs. Here's a detailed guide on why and how to provide adequate ventilation:
Understanding the Risks: Diesel fuel lines can overheat due to various factors, including high temperatures, prolonged operation, and improper installation. Overheating can lead to fuel line damage, reduced fuel efficiency, and even potential fire hazards. Additionally, the release of volatile organic compounds (VOCs) from diesel fuel can pose health risks if not properly managed.
Ventilation Techniques: To address these risks, it is essential to implement effective ventilation strategies. One common method is to use a ventilation fan or a dedicated ventilation system. These systems are designed to draw air through the fuel lines, carrying away heat and preventing the buildup of hot gases. It is crucial to ensure that the ventilation system is properly sized and positioned to cover the entire length of the fuel lines.
Location and Design: When installing handholes for diesel fuel lines, consider the ventilation requirements. Handholes should be strategically placed to allow for the passage of fresh air and the expulsion of heated air. Proper spacing and orientation of handholes can facilitate efficient ventilation. Additionally, the design of the fuel line routing should take into account the natural flow of air, ensuring that ventilation channels are not blocked or obstructed.
Regular Maintenance: Adequate ventilation is not a one-time task but requires regular maintenance. Over time, ventilation systems may become clogged or damaged, reducing their effectiveness. It is recommended to inspect and clean ventilation components periodically. This includes checking for debris, ensuring proper airflow, and replacing any worn-out parts to maintain optimal ventilation performance.
Safety Precautions: During the installation and maintenance of fuel lines, always prioritize safety. Wear appropriate personal protective equipment (PPE) to minimize exposure to potential hazards. Ensure that all personnel involved are trained in safety protocols and are aware of the risks associated with diesel fuel and ventilation systems. Regularly monitor the fuel system for any signs of overheating or malfunction, and take immediate action to address any issues.
By implementing these ventilation practices, you can effectively manage the temperature and air quality around diesel fuel lines, reducing the risk of overheating and potential hazards. Proper ventilation is a fundamental aspect of fuel system maintenance, ensuring the longevity and safety of your diesel engine.
Unveiling the Material Secrets of Micro Fuel Lines
You may want to see also
Insulation: Insulate fuel lines to protect against extreme temperatures and corrosion
Insulating fuel lines is a critical step in ensuring the longevity and reliability of diesel fuel systems. Proper insulation serves two primary purposes: protecting the fuel lines from extreme temperatures and preventing corrosion. These fuel lines are often exposed to harsh environments, making them susceptible to damage over time.
In terms of temperature protection, diesel fuel lines can experience significant thermal fluctuations. During operation, the fuel lines may become hot due to the combustion process, while in colder climates, they can freeze and crack. Insulation acts as a barrier, regulating the temperature and preventing sudden changes that could lead to material degradation. This is especially important in applications where fuel lines are routed through engine compartments or exposed to external elements.
Corrosion is another major concern, as diesel fuel contains water and acidic components that can accelerate the deterioration of metal and rubber components. Insulation, typically made from materials like fiberglass or mineral wool, provides a protective layer around the fuel lines. This insulation prevents direct contact between the fuel, moisture, and the metal or rubber, thus inhibiting corrosion. It is essential to choose insulation materials that are compatible with diesel fuel to avoid any adverse reactions.
When insulating fuel lines, it is crucial to ensure a proper fit and coverage. The insulation should be securely attached to the fuel lines, providing a continuous barrier without any gaps or overlaps that could compromise its effectiveness. Proper installation techniques, such as using adhesive tapes or mechanical fasteners, should be employed to maintain the insulation's integrity.
Additionally, regular inspection and maintenance of the insulated fuel lines are recommended. Over time, insulation may degrade or become dislodged, especially in areas with vibration or movement. Inspecting the insulation periodically allows for the early detection of any damage or wear, ensuring prompt repairs or replacements to maintain the fuel system's performance and safety.
Bundy Fuel Line Connector: A Comprehensive Guide
You may want to see also
Maintenance Access: Design handholes with maintenance access points for regular inspections and repairs
When designing fuel lines for diesel engines, it is crucial to incorporate handholes as maintenance access points to ensure easy and safe inspections and repairs. Handholes are small openings in the fuel line that provide direct access to the internal components, allowing technicians to work on the system without extensive disassembly. These access points are strategically placed to facilitate regular maintenance, which is essential for the longevity and reliability of the fuel system.
The placement of handholes should be carefully considered to ensure they are easily accessible and do not interfere with other components. Typically, these handholes are positioned at regular intervals along the fuel line, allowing for quick access to specific sections. This design approach enables technicians to identify and address issues promptly, preventing potential failures and costly downtime. For instance, handholes can be placed near the fuel tank, the engine bay, or at key junctions where the fuel line splits or joins with other components.
In addition to their strategic placement, handholes should be designed with a focus on durability and ease of use. The access points should be robust enough to withstand the rigors of regular maintenance but also user-friendly, ensuring that technicians can quickly and efficiently perform their tasks. This might involve using durable materials that can withstand fuel exposure and incorporating simple mechanisms for opening and closing the handholes.
Furthermore, the design of handholes should consider the specific needs of the fuel system. For instance, in systems with high-pressure fuel lines, handholes might need to be designed with additional safety features to prevent accidental fuel release during maintenance. This could include pressure-relief valves or specialized sealing mechanisms to ensure the handholes remain secure and leak-free.
In summary, incorporating handholes with maintenance access points in diesel fuel lines is a critical design consideration. These handholes should be strategically placed, durable, and user-friendly, allowing for regular inspections and repairs. By ensuring easy access to the fuel system, technicians can maintain the engine's performance, reliability, and safety over its operational life.
Optimizing Performance: Choosing the Right Fuel Line for Your Holley 650
You may want to see also
Frequently asked questions
Handholes are usually installed during the initial construction or renovation of a fuel system infrastructure. These handholes provide easy access points for maintenance, repairs, and inspections of the fuel lines. They are often placed at strategic locations, such as along the route of the fuel lines, to facilitate quick and efficient work.
Handholes offer several advantages. Firstly, they allow technicians to work on the fuel lines without having to dig up large sections of the ground or access confined spaces. This saves time and reduces the risk of damage to surrounding areas. Secondly, handholes provide a convenient way to monitor the condition of the fuel lines, identify potential issues, and perform routine maintenance tasks.
Handholes are not universally included in every diesel fuel line installation. The decision to install handholes depends on various factors, including the project's specific requirements, budget constraints, and the complexity of the fuel system design. In some cases, alternative access methods, such as buried access points or remote monitoring systems, might be utilized instead.