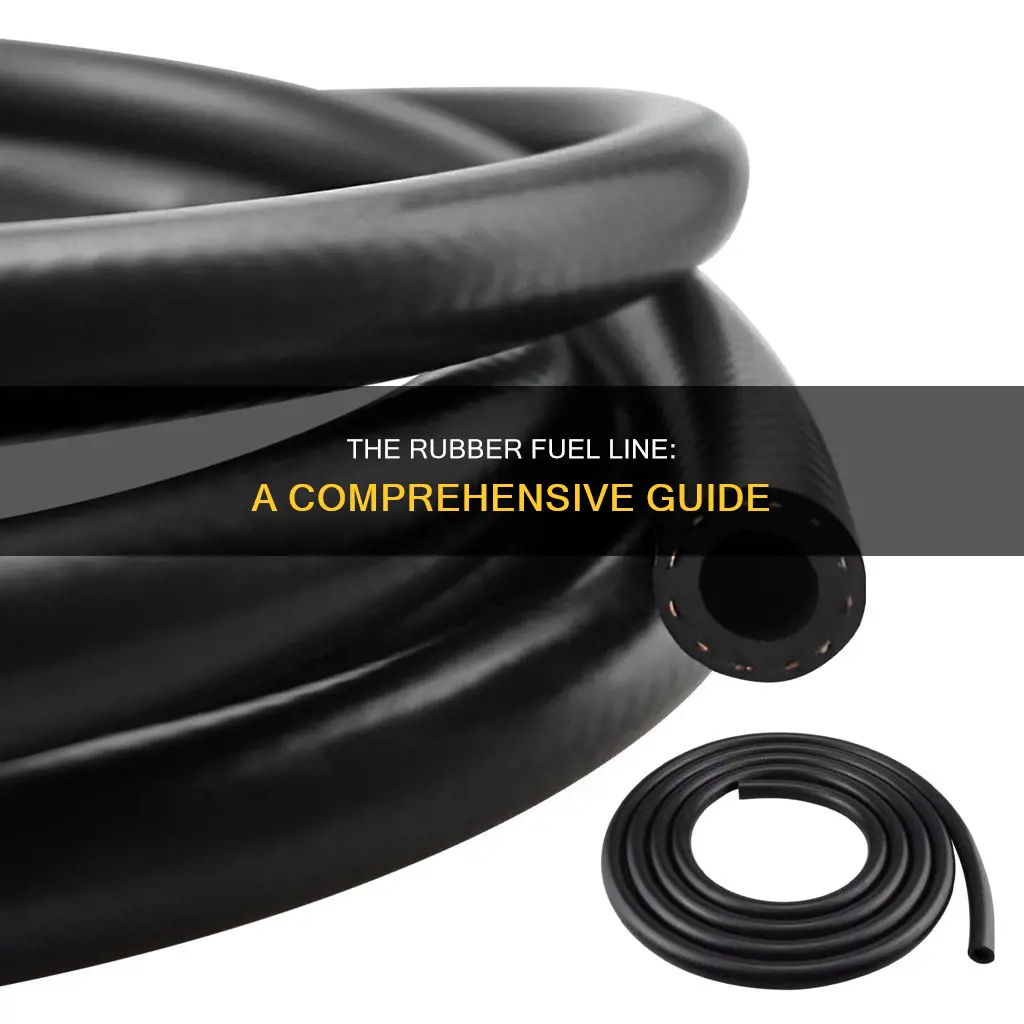
Fuel lines are an essential component of any vehicle's fuel system, responsible for transporting fuel from the tank to the engine. One of the most common materials used to make these lines is rubber, which offers several advantages over other materials. Rubber is flexible, durable, and resistant to heat and chemicals, making it ideal for withstanding the harsh conditions inside a vehicle's engine compartment. This material also helps to reduce noise and vibration, contributing to a smoother driving experience. However, the use of rubber in fuel lines has raised concerns about potential degradation over time, which can lead to fuel leaks and other issues. Despite these concerns, rubber remains a popular choice for fuel lines due to its cost-effectiveness and ease of installation.
Characteristics | Values |
---|---|
Material | Rubber (often synthetic) |
Flexibility | High flexibility to accommodate engine movement |
Durability | Resistant to heat, oil, and fuel chemicals |
Temperature Range | Operates well in a wide temperature range |
Vibration Resistance | Minimizes the risk of cracking or breaking due to engine vibrations |
Corrosion Resistance | Protects against corrosion from fuel and engine components |
Cost | Generally affordable and widely available |
Installation | Easy to install and replace |
Maintenance | Low maintenance requirements |
Compatibility | Compatible with various fuel types (gasoline, diesel, etc.) |
Longevity | Long-lasting performance over time |
What You'll Learn
- Material Science: Rubber's Flexibility and Durability for Fuel Lines
- Manufacturing Process: How Rubber Fuel Lines are Made
- Chemical Composition: Rubber's Chemical Structure for Fuel Resistance
- Environmental Impact: Rubber's Sustainability in Fuel Line Production
- Maintenance and Repair: Tips for Maintaining Rubber Fuel Lines
Material Science: Rubber's Flexibility and Durability for Fuel Lines
The use of rubber in fuel lines is a common practice in the automotive and industrial sectors, primarily due to its inherent flexibility and durability. These properties are crucial for ensuring the reliable and safe operation of fuel systems. Rubber's flexibility allows it to withstand the constant movement and vibration experienced in vehicles and machinery, preventing cracks and leaks that could lead to fuel leaks and potential fires. This material's ability to absorb and dampen vibrations is particularly important in high-stress environments, where rigid materials might fail over time.
From a material science perspective, the flexibility of rubber is attributed to its molecular structure. Rubber is a polymer, and its long, coiled polymer chains can easily stretch and deform under stress. This elasticity is a result of the disulfide bonds between sulfur atoms and the carbon-carbon double bonds in the polymer backbone. When force is applied, these bonds allow the chains to slide past each other, providing the material with its characteristic flexibility.
However, flexibility alone is not sufficient for fuel lines; durability is equally important. Rubber must be able to resist the corrosive effects of fuel, oils, and environmental factors over extended periods. This is achieved through the use of specialized rubber compounds, often containing additives like antioxidants, stabilizers, and reinforcing fillers. These additives enhance the material's resistance to degradation, ensuring it maintains its structural integrity and performance characteristics over time.
The process of manufacturing fuel lines involves careful selection and formulation of rubber compounds. Different types of rubber, such as natural rubber, neoprene, or butyl rubber, may be chosen based on their specific properties. For instance, neoprene is known for its excellent resistance to fuel and oil, making it ideal for high-temperature and high-pressure applications. Butyl rubber, on the other hand, offers superior flexibility and sealing properties, which are essential for maintaining a tight seal in fuel lines.
In conclusion, the use of rubber in fuel lines is a strategic choice, leveraging its flexibility and durability to ensure the safe and efficient operation of fuel systems. Through careful material selection and compounding, engineers can tailor rubber's properties to meet the specific demands of various applications, making it a reliable and cost-effective solution for fuel line construction. Understanding the science behind rubber's flexibility and durability is key to optimizing its performance in critical automotive and industrial roles.
Unraveling the Mystery: TBI Fuel Line 6AN Explained
You may want to see also
Manufacturing Process: How Rubber Fuel Lines are Made
The manufacturing process of rubber fuel lines involves several intricate steps to ensure the final product is durable, flexible, and capable of withstanding the harsh conditions within an engine compartment. Here's an overview of how these essential components are produced:
Raw Material Selection: The process begins with the careful selection of rubber compounds. Natural rubber or synthetic rubbers like neoprene or butyl are commonly used due to their excellent flexibility and resistance to heat and chemicals. The choice of rubber depends on the specific application and environmental factors. For instance, neoprene is ideal for high-temperature environments, while butyl offers superior flexibility.
Compound Mixing and Extrusion: Once the raw materials are sourced, they are carefully mixed and compounded in precise proportions. This mixture is then extruded through a die to create a continuous tube. The extrusion process involves feeding the rubber compound into a heated barrel, where it is melted and pushed through a die with a specific shape and size to form the desired fuel line profile. This step requires precision to ensure the fuel line's dimensions and wall thickness are accurate.
Reinforcement and Braiding: To enhance the structural integrity of the fuel line, reinforcement is often added. This can be done by inserting a layer of fabric or steel wire within the rubber tube. The reinforcement material is carefully selected to provide the necessary strength and flexibility. After reinforcement, the fuel line may be braided with metal or synthetic fibers to further reinforce the structure and prevent kinking or damage during installation.
Crimping and Fitting: The manufacturing process continues with the crimping of fittings onto the fuel line. Crimping involves applying pressure to create a secure connection between the fuel line and various components like fuel injectors, pumps, or tanks. This step ensures a reliable and leak-free connection. The fittings are typically made of metal and are carefully designed to match the fuel line's diameter.
Testing and Quality Control: Throughout the manufacturing process, rigorous testing and quality control measures are implemented. This includes pressure testing to ensure the fuel lines can withstand fuel pressure, flexibility tests to assess their durability, and visual inspections to identify any defects. These tests guarantee that the final product meets industry standards and performs reliably in real-world conditions.
The production of rubber fuel lines is a meticulous process, combining material science, engineering, and quality control to deliver a vital component of modern vehicles. Each step is crucial to ensuring the fuel lines' longevity and performance, contributing to the overall reliability of the automotive system.
Mercury Outboard Fuel Line Connector: Quick Guide to Finding the Right Fit
You may want to see also
Chemical Composition: Rubber's Chemical Structure for Fuel Resistance
The chemical composition of rubber plays a crucial role in determining its resistance to fuels, especially in the context of fuel lines. Rubber, a natural or synthetic polymer, is primarily composed of long-chain molecules known as polymers. These polymers are formed through a process called polymerization, where monomer units combine to create a network of interconnected chains. The specific type of rubber used in fuel lines is typically a synthetic variety, such as neoprene, butyl, or natural rubber, each with unique chemical structures that contribute to their fuel resistance properties.
One key aspect of rubber's chemical structure is its ability to form cross-links between the polymer chains. These cross-links create a three-dimensional network, making the rubber material more stable and resistant to deformation. In the context of fuel lines, this cross-linking is essential to ensure that the rubber remains flexible and maintains its shape even when exposed to the corrosive effects of fuels. The cross-links also contribute to the rubber's durability, preventing it from becoming brittle or cracking over time.
The molecular structure of rubber, particularly the presence of double bonds, is another critical factor. These double bonds, often found in the side chains of the polymer, can undergo chemical reactions with certain components of fuels. However, the specific chemical composition of the rubber, including the types of monomers and their arrangement, is carefully designed to minimize these reactions. This ensures that the rubber does not degrade or become susceptible to fuel-related damage.
Additionally, the additives used in rubber compounding can significantly impact its fuel resistance. These additives are carefully selected to enhance the material's properties without compromising its integrity. For instance, antioxidants are commonly added to prevent oxidation, which can lead to the breakdown of the rubber's molecular structure. Similarly, stabilizers are used to inhibit the degradation caused by heat, light, and other environmental factors, ensuring that the fuel lines remain effective over extended periods.
In summary, the chemical composition and structure of rubbers used in fuel lines are meticulously engineered to provide resistance to various fuels. The cross-linking, molecular arrangement, and strategic use of additives all contribute to the material's ability to withstand the corrosive nature of fuels. Understanding these chemical aspects is essential for engineers and manufacturers to select the appropriate rubber compounds, ensuring the longevity and reliability of fuel lines in various automotive and industrial applications.
Braided Fuel Line Installation: A Step-by-Step Guide
You may want to see also
Environmental Impact: Rubber's Sustainability in Fuel Line Production
The environmental implications of rubber's role in fuel line production are an important consideration in the automotive and manufacturing industries. Rubber, a natural or synthetic polymer, has been a traditional choice for fuel lines due to its flexibility, durability, and resistance to heat and chemicals. However, the sustainability of this material is a growing concern, especially as the industry aims to reduce its environmental footprint.
One significant environmental impact is the sourcing of raw materials. Natural rubber, derived from the latex of rubber trees, has a complex supply chain. The cultivation and processing of these trees can have ecological consequences, including deforestation, habitat destruction, and the use of harmful pesticides. Additionally, the energy-intensive process of transforming latex into rubber sheets contributes to the carbon footprint of the material. Synthetic rubbers, on the other hand, are derived from petroleum, a non-renewable resource, and their production process can also be energy-intensive and environmentally costly.
The manufacturing process of fuel lines itself presents challenges. Rubber compounding, a critical step, involves mixing various additives and fillers to enhance the material's properties. Some of these additives can be toxic or environmentally harmful if not properly managed. For instance, the use of lead or other heavy metals in compounding can have detrimental effects on ecosystems and human health if not disposed of or recycled correctly. Furthermore, the production of rubber fuel lines may require significant energy input, contributing to greenhouse gas emissions.
The end-of-life management of rubber fuel lines is another area of concern. While rubber is durable, it is not biodegradable, and improper disposal can lead to environmental pollution. Landfills are often the destination for discarded fuel lines, where they can take up space and potentially leach harmful chemicals into the soil and groundwater. Recycling and proper waste management strategies are essential to mitigate these impacts.
To address these sustainability challenges, the industry is exploring alternative materials and production methods. Bio-based rubbers, derived from renewable sources like plant oils and agricultural waste, offer a more sustainable option. These materials can reduce the reliance on fossil fuels and minimize the environmental impact of cultivation. Additionally, advancements in recycling technologies enable the recovery of rubber from end-of-life fuel lines, promoting a circular economy approach.
Choosing the Right Fuel Line for Spark Plug Success
You may want to see also
Maintenance and Repair: Tips for Maintaining Rubber Fuel Lines
Maintaining rubber fuel lines is crucial for ensuring the safe and efficient operation of your vehicle's fuel system. Rubber is a flexible and durable material, but it can degrade over time due to various factors such as age, temperature fluctuations, and exposure to chemicals. Here are some essential tips to help you keep your rubber fuel lines in top condition:
Regular Inspections: It is recommended to inspect your fuel lines at least once a year or whenever you notice any unusual symptoms. Look for cracks, brittleness, swelling, or any signs of deterioration. Pay close attention to areas where the lines connect to the fuel tank, pump, and engine, as these points are more susceptible to damage. Keep in mind that rubber fuel lines can become brittle and crack over time, especially if exposed to sunlight or extreme temperatures. Inspect the lines for any visible signs of damage and replace them if necessary.
Use of Fuel Line Cleaner: To maintain the flexibility and integrity of rubber fuel lines, consider using a specialized fuel line cleaner. These cleaners are designed to remove deposits, contaminants, and old fuel residue that can accumulate inside the lines. By regularly cleaning the fuel lines, you can prevent blockages and ensure that the fuel flows efficiently. When using a cleaner, follow the manufacturer's instructions carefully and allow sufficient time for the product to work before flushing it out.
Protection from Heat and Vibration: Rubber fuel lines can be susceptible to damage from heat and vibration. Park your vehicle in shaded areas to minimize direct sunlight exposure, as high temperatures can accelerate the aging process of rubber. Additionally, ensure that the fuel lines are securely fastened and protected from any potential sources of vibration, such as engine mounts or suspension components. Regularly check the mounting points to ensure the lines remain intact and firmly attached.
Regular Fuel System Maintenance: Maintaining your vehicle's overall fuel system is essential for the health of your rubber fuel lines. This includes regular fuel filter changes, keeping the fuel tank clean, and using the recommended fuel grade. Over time, fuel can degrade and contain contaminants that may damage the fuel lines. Using a fuel stabilizer can help preserve the fuel's quality and reduce the risk of line corrosion.
By following these maintenance tips, you can extend the lifespan of your rubber fuel lines and ensure optimal performance. Remember, regular care and attention can prevent costly repairs and potential safety hazards associated with fuel line failures.
Mastering Ford Fuel Line Connector Removal: A Step-by-Step Guide
You may want to see also
Frequently asked questions
Fuel lines are commonly made of rubber, specifically a type of synthetic rubber called neoprene or nitrile. This material is chosen for its flexibility, durability, and resistance to fuel-related chemicals, ensuring a reliable and safe fuel delivery system.
Rubber is an ideal choice for fuel lines due to its ability to withstand the harsh conditions within an engine bay. It can handle high temperatures, fuel pressure, and various fuel types without deteriorating or becoming brittle. Rubber's flexibility also allows it to accommodate engine movement and vibrations, ensuring a secure and leak-free connection.
Yes, while rubber is prevalent, other materials like stainless steel, braided steel, and high-temperature plastics are also used. Stainless steel offers excellent durability and corrosion resistance, making it suitable for long-term use. Braided steel provides flexibility and strength, while high-temperature plastics are lightweight and can handle extreme temperatures. The choice of material depends on the specific application and performance requirements.