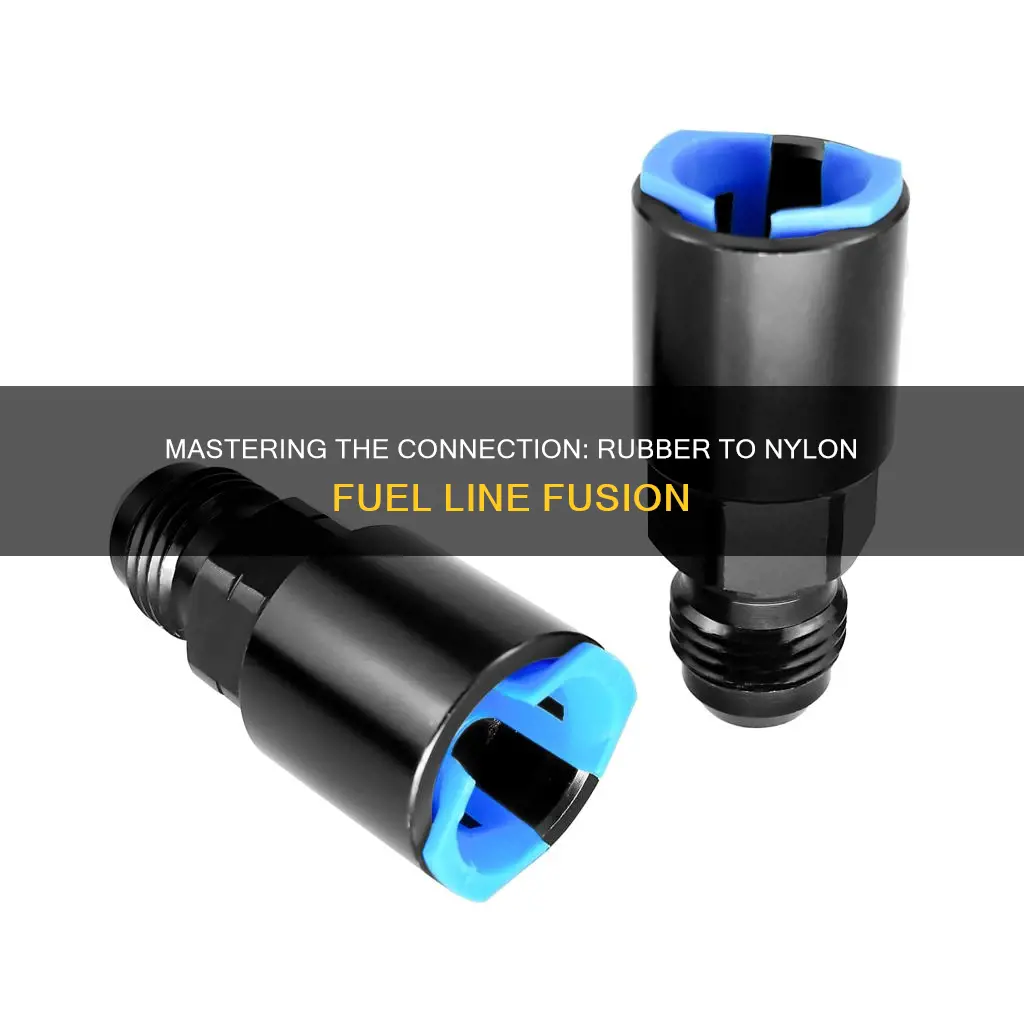
When working on a fuel system, it's important to know how to properly connect different types of fuel lines. In this guide, we'll focus on the specific task of hooking a rubber fuel line to a nylon fuel line. This process requires careful consideration of the materials and their compatibility to ensure a secure and leak-free connection. By following the steps outlined, you'll be able to make a reliable join that meets the demands of your fuel system.
Characteristics | Values |
---|---|
Material Compatibility | Rubber and nylon fuel lines can be connected using various methods, but it's important to ensure compatibility with the specific materials used. |
Temperature Resistance | Rubber fuel lines are generally more flexible and can withstand higher temperatures compared to nylon, which may have a lower temperature limit. |
Flexibility | Nylon fuel lines are known for their flexibility and ability to bend, making them suitable for tight spaces and complex fuel systems. Rubber lines might offer more rigidity. |
Durability | Nylon is often more durable and less prone to cracking or deterioration over time, especially in harsh environments. Rubber may require more frequent replacement. |
Cost | Nylon fuel lines can be more expensive than rubber alternatives, but the cost may vary depending on the brand and quality. |
Installation | Different methods like clamping, flaring, or using specialized adapters can be employed to connect rubber and nylon fuel lines. The chosen method should be suitable for the specific fuel system and application. |
Chemical Resistance | Consider the chemicals present in the fuel and choose a connection method that ensures compatibility to prevent fuel leakage or degradation. |
Availability | Both rubber and nylon fuel lines are widely available in various sizes and lengths, making it easier to find suitable connections. |
What You'll Learn
- Preparation: Ensure both lines are clean, dry, and free of debris
- Clamps: Use appropriate fuel line clamps for a secure connection
- Fitting Techniques: Tighten fittings gently to avoid damage
- Testing: Check for leaks before and after installation
- Maintenance: Regularly inspect and replace worn-out connections
Preparation: Ensure both lines are clean, dry, and free of debris
When preparing to connect a rubber fuel line to a nylon fuel line, it is crucial to ensure that both lines are in optimal condition to guarantee a secure and leak-free connection. The first step in this process is to thoroughly clean both lines. Over time, fuel lines can accumulate dirt, grime, and other contaminants from the fuel itself or the surrounding environment. These impurities can interfere with the connection, leading to potential leaks or reduced performance. Use a suitable cleaning agent, such as a fuel line cleaner, and a soft brush to scrub the interior of both lines, removing any built-up debris. Ensure that you pay attention to the threads and fittings, as these areas are particularly susceptible to contamination.
After cleaning, the lines must be dried to prevent any moisture-related issues. Moisture can cause the rubber and nylon materials to become brittle and less flexible, making the connection more prone to failure. Use a clean cloth or paper towel to wipe down the interior and exterior of both lines, removing any visible moisture. It is essential to work quickly, as leaving the lines wet could lead to the absorption of moisture, which may not be fully removable.
Additionally, inspect the lines for any signs of damage or wear. Small tears, cracks, or worn-out sections can compromise the integrity of the lines and affect the connection. If any damage is found, it is best to replace the affected sections before attempting the connection. This ensures that the lines are in the best possible condition, reducing the risk of leaks or other issues.
By taking the time to thoroughly clean, dry, and inspect the fuel lines, you are setting the foundation for a successful and secure connection. This preparation step is often overlooked but is critical to the overall performance and safety of the fuel system. It ensures that the lines are free from contaminants and potential sources of failure, providing a solid base for the upcoming connection process.
Toyota Tundra Fuel Line: Unsnapping the Process for Easy Access
You may want to see also
Clamps: Use appropriate fuel line clamps for a secure connection
When connecting rubber fuel lines to nylon fuel lines, using the right clamps is crucial for a secure and reliable join. Here's a detailed guide on how to achieve this:
Understanding the Clamps:
Fuel line clamps are designed to provide a tight seal and prevent fuel leakage. When dealing with rubber and nylon, you need clamps that offer flexibility and durability. Look for clamps specifically labeled for fuel lines or high-temperature applications. These clamps often feature a sturdy metal construction with a soft, rubberized inner layer to accommodate the different materials.
Preparation:
Before clamping, ensure both fuel lines are clean and free of any debris. Use a cloth or brush to wipe down the surfaces, removing any dirt or old adhesive residue. This step is essential for a proper connection.
Clamping Technique:
- Position the rubber fuel line and nylon fuel line alongside each other, ensuring they are aligned properly.
- Place the clamp over the joined fuel lines, making sure it covers the entire connection.
- Tighten the clamp securely by turning it clockwise. You should feel resistance as you tighten it, but be careful not to overtighten, as this can damage the fuel lines.
- Repeat this process for any additional fuel lines you are connecting.
Considerations:
- Always use the appropriate size clamp for the diameter of your fuel lines.
- Avoid using regular hose clamps, as they may not provide the necessary flexibility and strength.
- If the connection requires a more permanent solution, consider using a fuel line adhesive or sealant in addition to the clamps.
By following these steps and using the right clamps, you can ensure a secure and leak-free connection between rubber and nylon fuel lines. Remember, proper clamping is essential for maintaining the integrity of your fuel system.
US Fuel Lines to Mexico: Unraveling the Mystery
You may want to see also
Fitting Techniques: Tighten fittings gently to avoid damage
When connecting rubber and nylon fuel lines, it's crucial to employ the right fitting techniques to ensure a secure and damage-free assembly. The process involves several steps, and one of the most critical aspects is tightening the fittings gently. This approach is essential to prevent any potential harm to the fuel lines and the overall system.
Start by ensuring you have the appropriate fittings, such as barbed fittings with an inner diameter slightly larger than the fuel line's outer diameter. These fittings should be made of a durable material that can withstand the pressure and temperature changes associated with fuel. Before proceeding, inspect the fittings for any signs of damage or wear. Clean the fittings and the fuel lines to remove any dirt, debris, or old fuel residue, ensuring a clean and smooth connection.
Now, take the rubber fuel line and the nylon fuel line, and carefully insert the barbed fitting onto the nylon line. Ensure the fitting is positioned correctly, with the barbed end aligned with the fuel line's end. Gently push the fitting onto the line, feeling for a slight resistance when it is fully seated. This step requires precision and patience to avoid forcing the fitting, which could lead to damage. Once the fitting is in place, you'll need to tighten it using a wrench or spanner. The key here is to apply gentle, controlled force. Over-tightening can cause the fuel line to kink or the fitting to crack, leading to potential fuel leaks or system failures.
Instead, use a wrench to tighten the fitting securely but not excessively. You should feel the fitting make a firm connection without any excessive force. Check for any leaks around the fitting by applying a small amount of fuel to the connection and ensuring no fuel drips. If there are any leaks, carefully tighten the fitting further, being mindful of the gentle approach. After tightening, inspect the connection to ensure it is secure and free of any visible damage.
Remember, the goal is to create a tight, leak-free connection without causing any harm to the fuel lines. Gentle tightening techniques are essential to achieving this, ensuring the longevity and reliability of your fuel system. Always take your time and be cautious during the fitting process to avoid any unnecessary complications.
Chevy Fuel Line Disconnection: A Step-by-Step Guide
You may want to see also
Testing: Check for leaks before and after installation
Before and after the installation of the fuel lines, it is crucial to perform leak testing to ensure a secure and safe connection. Here's a step-by-step guide on how to test for leaks:
Before Installation:
- Prepare the Materials: Gather the necessary tools and materials, including the rubber fuel line, nylon fuel line, fuel, a leak detector or soapy water, and a spray bottle. Ensure you have the correct sizes and types of fuel lines that are compatible with each other.
- Set Up the Test: Find a suitable area where you can safely work and test the fuel lines. It is recommended to have a flat surface to facilitate the process.
- Connect the Lines Temporarily: Temporarily attach the rubber fuel line to the nylon fuel line using clamps or by wrapping the lines together. This step helps you visualize the connection and prepare for the permanent installation.
- Apply Fuel: Add a small amount of fuel to the temporary connection. You can use a syringe to inject the fuel into the system. Ensure you follow safety precautions and work in a well-ventilated area.
- Check for Leaks: Use your leak detector or spray soapy water around the temporary connection points. Look for any bubbles or foam forming, indicating a potential leak. Pay close attention to the threads, fittings, and bends where the lines meet. If you detect any leaks, carefully detach the lines and address the issue before proceeding.
After Installation:
- Reassemble and Secure: Once the fuel lines are installed, double-check the connections and ensure they are tight and secure. Use the appropriate tools to tighten any fittings or clamps.
- Test the System: Apply fuel to the newly installed system and repeat the leak detection process. Spray the soapy water or use the leak detector around all connection points, including the engine's fuel injectors or carburetor.
- Inspect for Any Signs of Leaks: Carefully examine the entire system for any bubbles, foam, or wet spots. Leaks can occur at the connections, inside the lines, or even at the engine's fuel intake. If you find any leaks, carefully detach the lines and inspect the damage. Make the necessary repairs or replacements to ensure a tight seal.
- Final Check: After addressing any leaks, reattach the lines and retest the system. Ensure that all connections are secure and that there are no further leaks.
Remember, proper leak testing is essential to prevent fuel leaks, which can lead to dangerous situations and potential engine damage. Always follow safety guidelines and consider seeking professional assistance if you are unsure about any step during the installation and testing process.
Fuel Line Splice: A Comprehensive Guide to Installation
You may want to see also
Maintenance: Regularly inspect and replace worn-out connections
Regular maintenance is crucial to ensure the longevity and safe operation of your fuel system, especially when dealing with different types of fuel lines like rubber and nylon. One critical aspect of this maintenance is the inspection and timely replacement of worn-out connections. Here's a detailed guide on why and how to approach this task:
Understanding the Risks of Worn Connections:
Over time, fuel lines, regardless of their material (rubber or nylon), can degrade due to various factors such as fuel contamination, temperature changes, and general wear and tear. Rubber fuel lines, in particular, may become brittle and crack, while nylon lines can develop small tears or splits. When these materials weaken, the connections between them and other components, such as fuel pumps, filters, and tanks, become vulnerable. Leaks can occur, leading to potential fuel spills, engine misfires, and even more severe issues like fire hazards.
Regular Inspection Protocol:
To prevent such problems, it's essential to establish a regular inspection routine. Here's a step-by-step guide:
- Visual Inspection: Start by visually examining all fuel line connections, including those between rubber and nylon lines. Look for any signs of damage, such as cracks, brittleness, or visible tears. Check for any discolored or softened rubber sections, as these could indicate degradation.
- Feel for Leaks: Use your sense of touch to identify potential leaks. Run your fingers along the connections and listen for any hissing or bubbling sounds, which might indicate a gas leak. Even a small drip can be a cause for concern.
- Check for Tightness: Ensure that all connections are secure. Loosen the fittings slightly and re-tighten them to ensure they are not too tight, which can cause damage over time.
- Document and Note: Keep a record of your inspections, noting the condition of each connection. This documentation will help you track the wear and tear pattern and identify areas that require immediate attention.
Replacing Worn-Out Connections:
If you identify any worn-out or damaged connections during your inspections, it's essential to take prompt action:
- Replace the Entire Line: If a rubber fuel line is significantly damaged, it's often more cost-effective and safer to replace the entire line rather than just the connection. This ensures that the new line meets the required specifications.
- Use the Right Adapters: When replacing or repairing connections, ensure you use the appropriate adapters or fittings designed for the specific materials. For example, use nylon-to-nylon or rubber-to-rubber adapters to ensure a secure and leak-free connection.
- Seek Professional Help: For complex fuel line systems, it's advisable to consult a professional mechanic. They can provide expert advice and ensure that the replacement is done correctly, adhering to manufacturer guidelines.
By incorporating regular inspections and prompt replacements, you can significantly reduce the risk of fuel-related issues and ensure that your vehicle's fuel system operates efficiently and safely. Remember, proper maintenance is key to avoiding costly repairs and potential hazards associated with fuel system malfunctions.
Winter Fuel Line Freeze: When to Act Fast
You may want to see also
Frequently asked questions
Connecting rubber and nylon fuel lines requires a few steps to ensure a secure and leak-free attachment. First, clean both lines to remove any dirt or debris. Then, use a fuel line adapter or a special solvent-based adhesive designed for fuel lines. Apply the adhesive or adapter according to the manufacturer's instructions, and ensure a tight fit. Heat the connection area slightly to help the adhesive set, and test the connection for leaks before use.
Yes, you'll need a few essential tools to make the connection. A fuel line crimping tool is commonly used to create a secure mechanical bond between the lines. You might also require a fuel line cutter to ensure precise lengths, and a cleaning brush or rag to prepare the lines. Additionally, have the appropriate adhesives or adapters readily available for the specific fuel line types you're working with.
One of the primary concerns is ensuring a tight and leak-free seal. If the connection is not properly secured, fuel could leak, leading to potential safety hazards and engine performance issues. It's crucial to follow the manufacturer's guidelines for the chosen adhesive or adapter. Another issue to watch out for is overheating the lines, as excessive heat can damage the materials and affect their performance.
Reusing a connection that has already leaked is not recommended. Over time, fuel lines can degrade, and the connection may become weaker, leading to more frequent leaks. If you encounter leaks, it's best to replace the affected lines and reconnect them using the appropriate methods. Regular maintenance and inspections can help identify potential issues before they become major problems.