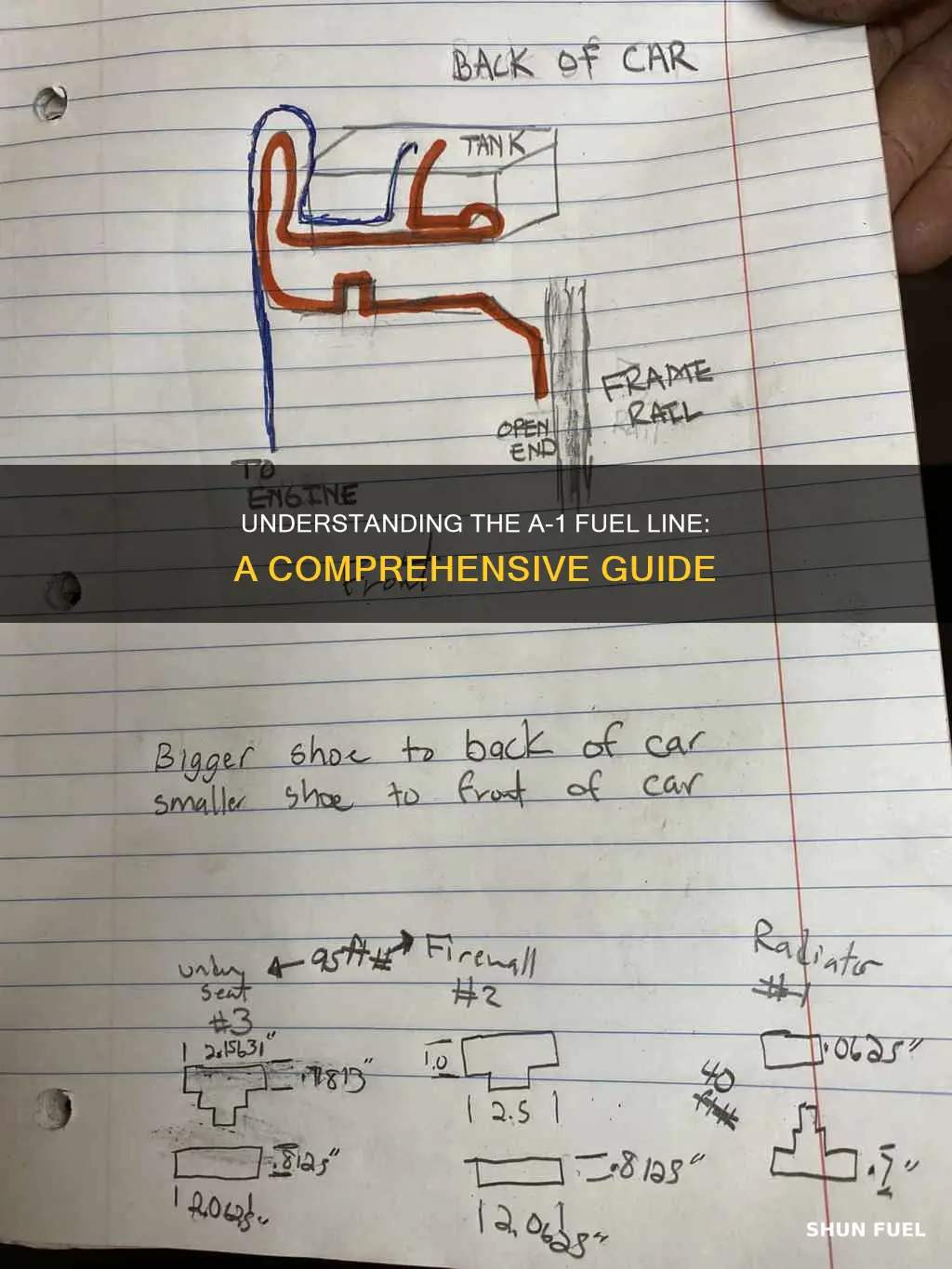
A-1 fuel lines are an essential component in the fuel delivery system of vehicles, particularly those with high-performance engines. These lines are designed to transport fuel from the tank to the engine, ensuring a steady and efficient supply of gasoline or diesel. The A-1 designation often refers to a specific type of fuel line known for its durability and ability to withstand high pressure and temperature, making it ideal for racing and high-performance applications. This paragraph introduces the topic by highlighting the critical role of fuel lines in vehicle performance and the specialized nature of A-1 fuel lines.
What You'll Learn
- Fuel Delivery: Focuses on the system that delivers fuel from the tank to the engine
- Fuel Injection: Explores the process of injecting fuel into the engine for combustion
- Fuel Filters: Discusses the role of filters in removing contaminants from the fuel
- Fuel Pumps: Details the function of pumps in pressurizing and circulating fuel
- Fuel Sensors: Examines sensors that monitor fuel levels and quality
Fuel Delivery: Focuses on the system that delivers fuel from the tank to the engine
The fuel delivery system is a critical component of any vehicle's engine, ensuring a steady and efficient supply of fuel to power the engine's operation. This system is responsible for transporting fuel from the fuel tank to the engine, where it is ignited to produce power. The process involves several key components working together to ensure optimal performance and reliability.
At the heart of the fuel delivery system is the fuel pump, which is typically located within the fuel tank or close to it. Its primary function is to draw fuel from the tank and increase its pressure to ensure a consistent flow. The pump is often an electric or mechanical device, with the latter being more common in older vehicles. Mechanical pumps are driven by the engine's camshaft, ensuring that the fuel delivery process is synchronized with the engine's operation.
Connected to the pump is the fuel line, a crucial component that acts as a conduit for the fuel. These lines are designed to withstand high pressure and temperature, ensuring the fuel's integrity during its journey to the engine. The fuel lines are typically made of durable materials such as steel, aluminum, or specialized plastics, depending on the vehicle's make and model. The lines are carefully routed to avoid damage and ensure a smooth flow, often following a path that minimizes bends and twists to maintain optimal pressure.
Another essential component is the fuel filter, which is usually positioned near the engine. Its role is to remove impurities and contaminants from the fuel, ensuring that only clean fuel reaches the engine. Over time, fuel can accumulate dirt, water, and other debris, which can lead to engine issues. The filter traps these particles, preventing them from entering the engine and causing potential damage. Regular maintenance, including replacing the filter at recommended intervals, is vital to keep the fuel delivery system in optimal condition.
In addition to these primary components, some vehicles may have additional features to enhance fuel delivery. For instance, a fuel pressure regulator is used to maintain the correct fuel pressure, ensuring the engine receives the precise amount of fuel required for efficient combustion. This regulator is especially important in engines with electronic fuel injection systems, where precise fuel-air mixture control is essential for optimal performance and fuel efficiency.
Understanding the fuel delivery system and its components is essential for vehicle owners and mechanics alike. Regular maintenance and timely replacements of parts can help ensure the engine operates efficiently and reliably. By focusing on the fuel delivery process, vehicle owners can contribute to the overall longevity and performance of their engines.
Fuel Filter's Role: Ensuring Supply Line Efficiency
You may want to see also
Fuel Injection: Explores the process of injecting fuel into the engine for combustion
Fuel injection is a critical process in modern engines, revolutionizing the way fuel is delivered to the combustion chamber. It involves the precise and efficient injection of fuel into the engine's cylinders, ensuring optimal performance and combustion. This technology has become a cornerstone of automotive engineering, offering numerous advantages over traditional carburetor systems.
The process begins with the fuel injection system, which is designed to meter and deliver fuel under high pressure. This system typically consists of an injection pump, injectors, and a fuel rail. The pump draws fuel from the tank and pressurizes it, ensuring a consistent and controlled flow. Injectors, often located near the intake valves, are responsible for the actual injection process. When the engine's computer sends a signal, the injectors rapidly open, spraying a fine mist of fuel into the combustion chamber. This high-pressure injection ensures that fuel is atomized to the perfect size, allowing for efficient combustion.
One of the key advantages of fuel injection is its ability to provide precise control over the fuel-air mixture. Unlike carburetors, which mix fuel and air mechanically, fuel injectors deliver fuel directly into the combustion chamber, where it mixes with air. This results in a more accurate and consistent mixture, leading to improved engine performance and efficiency. Modern fuel injection systems can adjust the fuel-air ratio in real-time, optimizing power output and fuel consumption. For instance, during high-load conditions, the system can inject more fuel to meet the engine's increased power demands, while still maintaining efficiency during lighter loads.
The process also enables advanced engine management strategies. Engine control units (ECUs) use sensors to monitor various parameters, such as engine speed, temperature, and load. Based on this data, the ECU calculates the ideal fuel injection timing and amount. This real-time adjustment ensures that the engine operates at its peak performance and efficiency, regardless of driving conditions. Additionally, fuel injection systems can implement strategies like knock control, where the fuel injection timing is adjusted to prevent engine knock, and idle control, which maintains a stable idle speed by precisely controlling the fuel flow.
In summary, fuel injection is a sophisticated process that plays a vital role in modern engine design. By injecting fuel directly into the combustion chamber, it ensures a precise and efficient fuel-air mixture, leading to improved performance, power, and fuel economy. The technology's ability to adapt to various driving conditions and implement advanced engine management strategies makes it a cornerstone of contemporary automotive engineering. Understanding the intricacies of fuel injection is essential for optimizing engine performance and maintaining the reliability of modern vehicles.
Understanding Fuel Line Sizes: Supply and Return Fuel Lines Explained
You may want to see also
Fuel Filters: Discusses the role of filters in removing contaminants from the fuel
Fuel filters are an essential component in any vehicle's fuel system, playing a critical role in maintaining engine performance and longevity. These filters are designed to remove contaminants from the fuel before it reaches the engine, ensuring a clean and efficient combustion process. The primary function of a fuel filter is to protect the engine from harmful substances that can cause damage over time.
Contaminants in fuel can include dirt, dust, water, and other impurities that may have entered the system during fuel storage, transportation, or even at the pump. These particles can lead to various issues, such as reduced engine power, poor fuel economy, and even engine damage. For instance, water in the fuel can cause corrosion in the fuel system, while dirt and debris can block fuel injectors, leading to misfires and reduced performance.
Fuel filters work by physically trapping these contaminants as the fuel passes through them. They are typically located in the fuel line, positioned between the fuel tank and the engine. When the engine is running, fuel is drawn from the tank, passes through the filter, and then continues its journey to the engine. The filter's design allows it to capture and hold contaminants, preventing them from entering the engine. This process ensures that only clean, contaminant-free fuel reaches the engine's fuel injectors or carburetor.
There are different types of fuel filters available, including in-line filters and sediment filters. In-line filters are commonly used in modern vehicles and are designed to handle high-pressure fuel systems. They are typically made of a woven metal or synthetic material that traps contaminants. Sediment filters, on the other hand, are often used in older vehicles and are more basic, consisting of a simple screen or mesh to capture larger particles.
Regular maintenance and replacement of fuel filters are crucial to ensure optimal engine performance. Over time, filters can become clogged with contaminants, reducing their effectiveness. It is recommended to check and replace fuel filters at regular intervals, especially if the vehicle is used in dusty or dirty environments. Proper maintenance of the fuel filter system can help prevent costly engine repairs and ensure the vehicle's overall reliability.
The Ultimate Guide to Pipe Thread Sealants for Aviation Fuel Lines
You may want to see also
Fuel Pumps: Details the function of pumps in pressurizing and circulating fuel
Fuel pumps play a critical role in the operation of internal combustion engines, ensuring a steady and efficient supply of fuel to the engine's combustion chambers. These pumps are designed to pressurize and circulate fuel, which is essential for optimal engine performance and reliability. The primary function of a fuel pump is to increase the pressure of the fuel to a level that allows it to overcome the engine's intake system resistance and reach the injectors or carburetor. This process is crucial, especially in high-performance engines, where fuel pressure needs to be precisely controlled to achieve the desired power output and fuel efficiency.
There are two main types of fuel pumps commonly used in automotive applications: mechanical and electric. Mechanical fuel pumps are typically driven by the engine's camshaft and are often used in older vehicles. These pumps use a diaphragm or a gear mechanism to pressurize the fuel. When the engine is running, the camshaft's rotation activates the pump, creating a vacuum that draws fuel from the tank and pressurizes it. This pressurized fuel is then directed to the engine's intake system. Mechanical pumps are known for their simplicity and reliability but may struggle to maintain consistent pressure at higher engine speeds.
Electric fuel pumps, on the other hand, are powered by an electric motor and are more commonly found in modern vehicles. These pumps offer several advantages, including the ability to maintain consistent fuel pressure across a wide range of engine speeds. Electric pumps are often smaller and more compact, allowing for better engine bay layout flexibility. They can be mounted in various locations, such as inside the fuel tank or near the engine, and are typically controlled by the engine control unit (ECU) to ensure precise fuel delivery.
The operation of a fuel pump involves several key components. Firstly, the pump body contains a chamber with an inlet and outlet port. The inlet port connects to the fuel tank, while the outlet port delivers pressurized fuel to the engine. Inside the pump, a diaphragm or a gear mechanism is used to create pressure. In diaphragm pumps, a flexible diaphragm moves in response to the engine's camshaft, creating a vacuum that draws fuel and pressurizes it. Gear pumps, as the name suggests, use gears to transfer power and increase fuel pressure.
Once the fuel is pressurized, it is directed to the engine's intake system, where it is injected or carbureted. The timing and pressure of fuel delivery are critical to engine performance. Modern fuel pumps are often equipped with pressure regulators to maintain the desired fuel pressure. These regulators ensure that the fuel pressure remains stable, even under varying engine loads and speeds. Additionally, some fuel pumps have built-in filters to remove contaminants from the fuel, ensuring clean and efficient combustion.
In summary, fuel pumps are essential components in the fuel delivery system of an engine. They pressurize and circulate fuel, ensuring a consistent and controlled supply to the engine's combustion chambers. Whether mechanical or electric, these pumps play a vital role in optimizing engine performance, fuel efficiency, and overall reliability. Understanding the function and components of fuel pumps is crucial for maintaining and troubleshooting fuel-related issues in various vehicle applications.
Honda 250 Fuel Line Size: Expert Guide to Choosing the Right Fit
You may want to see also
Fuel Sensors: Examines sensors that monitor fuel levels and quality
Fuel sensors play a critical role in modern vehicles, ensuring optimal performance and safety by monitoring fuel levels and quality. These sensors are designed to provide accurate and real-time data, allowing drivers and vehicle systems to make informed decisions. The primary function of fuel sensors is to detect the presence and quantity of fuel in the tank, enabling the vehicle's onboard computer to manage fuel-related operations efficiently. This includes fuel level indication, which is crucial for preventing fuel starvation and ensuring the vehicle doesn't run out of fuel unexpectedly.
There are various types of fuel sensors available, each with unique characteristics and applications. One common type is the float-style sensor, which is commonly found in traditional fuel tanks. This sensor operates by using a float that rises and falls with the fuel level, triggering electrical signals that correspond to the fuel's position. When the fuel level is low, the float moves closer to the sensor, sending a signal to the vehicle's computer, which then prompts the driver to refuel.
Another type is the resistive sensor, which measures the resistance of the fuel to determine its level. This sensor typically consists of a wire or rod that is partially submerged in the fuel. As the fuel level changes, the wire's exposure to the fuel varies, altering its resistance. This resistance is then converted into a fuel level reading by the vehicle's electronics. Resistive sensors are known for their accuracy and durability, making them a popular choice for many vehicle manufacturers.
Fuel quality sensors are also essential components of modern fuel systems. These sensors monitor the properties of the fuel, such as density, temperature, and acidity, to ensure it meets the required standards. For instance, density sensors measure the fuel's specific gravity, which indicates its concentration and purity. This is particularly important for diesel engines, where fuel quality directly impacts performance and emissions. Temperature sensors are also used to measure the fuel's temperature, which affects its density and volatility, thus influencing engine operation.
In addition to monitoring fuel levels and quality, some advanced fuel sensors can detect contaminants and provide early warnings. These sensors can identify the presence of water, sediment, or other impurities in the fuel, which could lead to engine damage if left unchecked. By continuously monitoring the fuel's condition, these sensors contribute to the overall reliability and longevity of the vehicle's fuel system. Modern fuel sensor technology has significantly improved vehicle efficiency, reduced emissions, and enhanced driver convenience by providing accurate and timely fuel-related information.
Locating the Fuel Line: A Guide to Finding the 2002 Pontiac GM Fuel Line
You may want to see also
Frequently asked questions
The A-1 fuel line is a specific type of fuel line used in aviation and automotive applications. It is designed to carry aviation fuel, such as jet fuel or aviation gasoline, and is commonly used in aircraft and some high-performance cars. This fuel line is known for its durability and ability to withstand high-pressure environments.
Compared to standard fuel lines, the A-1 fuel line is constructed with specialized materials and has a thicker wall thickness to handle the unique demands of aviation fuel. It is designed to resist corrosion, maintain flexibility over a wide temperature range, and ensure a reliable fuel supply even in challenging conditions.
While the A-1 fuel line is primarily designed for aviation fuel, it can be used for other types of fuel with similar properties. However, it's important to check the compatibility and specifications of the fuel line with the specific fuel type to ensure optimal performance and safety.
Yes, proper installation is crucial for the A-1 fuel line. It should be installed according to the manufacturer's guidelines, ensuring secure connections and proper routing to minimize the risk of fuel leaks. Regular inspections and maintenance are also recommended to ensure the fuel line's longevity and performance.