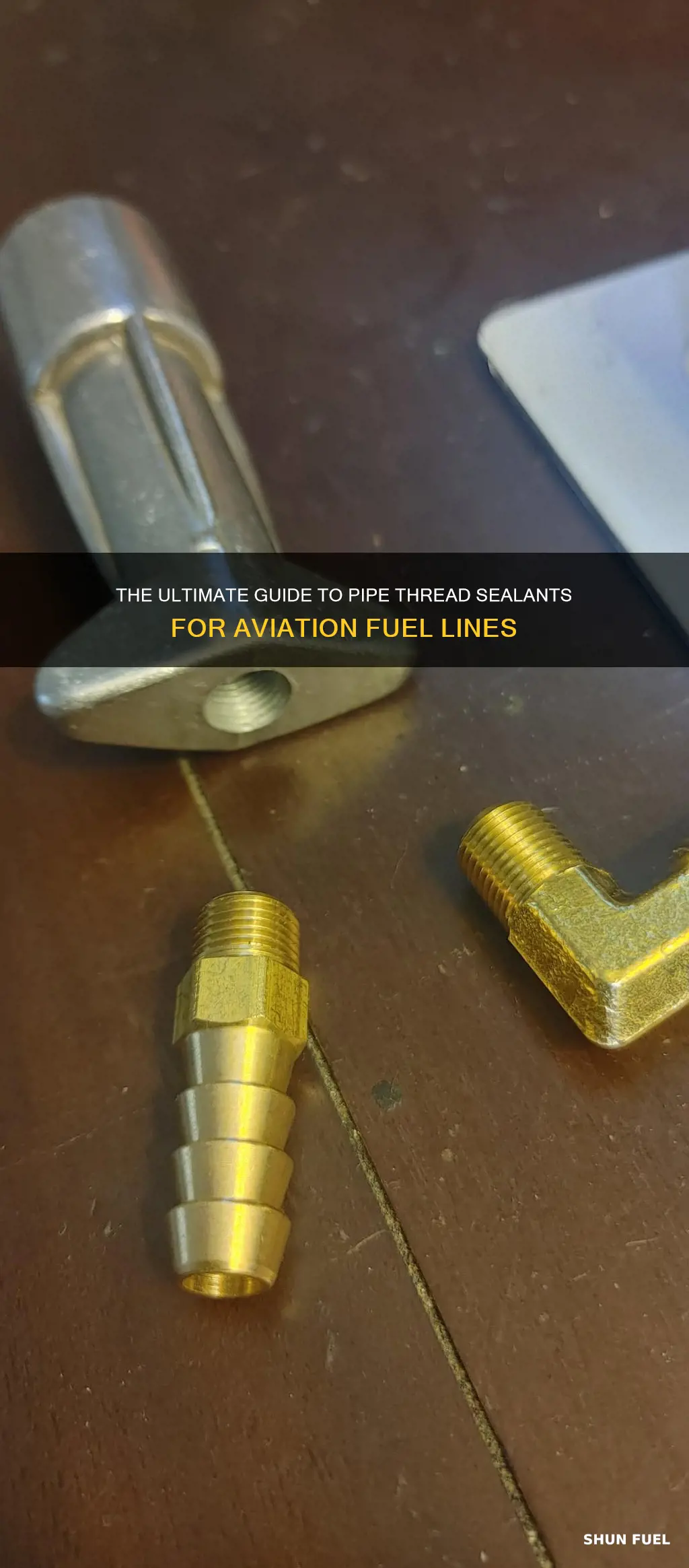
Pipe thread sealants play a critical role in the maintenance and assembly of aircraft fuel lines, ensuring a secure and leak-free connection. Specifically, aviation fuel lines require a specialized sealant that can withstand the extreme conditions of aviation environments, including high temperatures, pressure, and exposure to corrosive substances. The sealant must also be compatible with aviation fuels to prevent any adverse reactions that could compromise the integrity of the fuel system. This paragraph introduces the topic by highlighting the importance of selecting the right pipe thread sealant for aviation fuel lines, emphasizing the need for a product that meets the rigorous demands of aviation applications.
What You'll Learn
- Sealing Aviation Fuel Lines: Ensuring tight, leak-free connections for fuel efficiency and safety
- Resistance to Fuel Contaminants: Protecting against degradation and maintaining fuel quality
- High-Temperature Performance: Withstanding extreme temperatures for reliable fuel line operation
- Corrosion Inhibition: Preventing corrosion damage to fuel lines and components
- Compliance with Aviation Standards: Meeting industry regulations for quality and performance
Sealing Aviation Fuel Lines: Ensuring tight, leak-free connections for fuel efficiency and safety
The critical nature of aviation fuel systems demands the utmost attention to detail in their construction and maintenance. One of the most crucial aspects of these systems is ensuring that fuel lines are sealed properly to prevent leaks, which can lead to significant safety hazards and performance issues. The choice of sealant plays a pivotal role in achieving this goal.
When it comes to aviation fuel lines, the pipe thread sealant must be carefully selected to withstand the unique challenges posed by the operating environment. Aviation fuel lines are typically exposed to extreme temperatures, vibrations, and the corrosive effects of fuel itself. Therefore, the sealant must provide a robust and durable bond that can endure these conditions without compromising its integrity.
A commonly used sealant for aviation fuel lines is a special type of thread seal tape, often referred to as 'aviation thread seal tape' or 'fuel line tape'. This tape is designed specifically for the demanding conditions of aviation fuel systems. It is typically made from a combination of synthetic fibers and a high-performance adhesive, ensuring excellent resistance to fuel, temperature, and vibration. The tape is applied in a specific manner, wrapping it tightly around the pipe threads in an alternating pattern, creating a strong, leak-resistant seal.
In addition to thread seal tape, another effective sealant is a liquid sealant, often referred to as a 'thread seal compound' or 'pipe dope'. This type of sealant is applied directly to the pipe threads before assembly, forming a protective layer that prevents leaks. It is particularly useful for hard-to-reach areas and provides a strong, flexible bond. However, it requires careful application and curing time, making it less ideal for high-volume assembly processes.
The importance of proper sealing cannot be overstated. Leaks in aviation fuel lines can lead to fuel loss, reduced engine performance, and potential safety hazards. By using the appropriate sealant and following manufacturer guidelines, aviation professionals can ensure that fuel lines are sealed tightly, contributing to the overall efficiency and safety of the aircraft. Regular inspections and maintenance are also essential to identify and address any potential issues with the seals.
Optimizing Fuel Flow: Choosing the Right Line Size
You may want to see also
Resistance to Fuel Contaminants: Protecting against degradation and maintaining fuel quality
The integrity of aviation fuel systems is paramount to ensure optimal performance and safety. One critical aspect often overlooked is the role of pipe thread sealants in maintaining fuel quality and preventing degradation. When it comes to aviation fuel lines, the choice of sealant is crucial, as it directly impacts the resistance to fuel contaminants and the overall longevity of the fuel system.
Fuel contaminants can lead to a myriad of issues, including engine performance degradation, reduced fuel efficiency, and even potential engine failure. These contaminants can enter the fuel system through various means, such as improper sealing, corrosion, or external sources. Therefore, an effective sealant must provide robust protection against these harmful substances.
A high-quality pipe thread sealant designed for aviation fuel lines should offer excellent resistance to common fuel contaminants. These contaminants often include water, acids, bases, and various organic compounds that can accelerate corrosion and degradation of the fuel system components. The sealant acts as a barrier, preventing these contaminants from coming into direct contact with the fuel and the internal surfaces of the lines.
To achieve optimal resistance, the sealant should be compatible with aviation fuels and have a stable chemical composition that does not react with the fuel over time. It should also possess a low permeability to fuel, ensuring that contaminants cannot easily penetrate the sealant layer. Additionally, the sealant's ability to form a strong, durable bond with the pipe threads is essential to create a reliable seal that can withstand the pressures and vibrations encountered during flight.
Regular maintenance and inspection of the fuel lines and their sealants are vital. Over time, sealants may degrade or become compromised, especially in the harsh aviation environment. Therefore, periodic checks and replacements of the sealant are necessary to ensure continuous protection against fuel contaminants, ultimately contributing to the overall reliability and performance of the aircraft's fuel system.
Unveiling the Mystery: What Material Powers Your Lawn Mower's Fuel Lines?
You may want to see also
High-Temperature Performance: Withstanding extreme temperatures for reliable fuel line operation
The critical nature of aviation fuel lines demands a sealant that can endure the extreme temperatures encountered during flight. These fuel lines are exposed to a wide range of thermal conditions, from the intense heat of takeoff to the rapid cooling during descent. Therefore, the sealant must provide exceptional high-temperature performance to ensure the integrity and reliability of the fuel system.
One key aspect of high-temperature performance is the sealant's ability to maintain its structural integrity under extreme heat. This involves several factors. Firstly, the sealant should have a high melting point, ensuring it remains solid and functional even at elevated temperatures. This property is crucial to prevent fuel leaks and maintain the safety of the aircraft. Secondly, the sealant must exhibit excellent thermal stability, meaning it resists degradation and maintains its properties over a wide temperature range. This stability is essential to guarantee long-term reliability and performance.
In addition to melting point and thermal stability, the sealant's resistance to thermal expansion and contraction is vital. Aviation fuel lines experience significant temperature fluctuations, and the sealant must accommodate these changes without compromising its seal. This requires a material that can flex and adapt to the expanding and contracting fuel lines, ensuring a consistent and secure seal.
Furthermore, the high-temperature performance of the sealant is closely tied to its chemical composition. Aviation-grade sealants are typically formulated with specialized compounds that offer superior heat resistance. These compounds may include high-performance polymers, such as fluoropolymers or silicone-based materials, which are known for their exceptional thermal stability and resistance to fuel degradation. The choice of these materials is critical to ensuring the sealant's longevity and effectiveness.
Lastly, the high-temperature performance of the sealant is not just about its individual properties but also its compatibility with the fuel lines and the overall fuel system. The sealant should not react with the fuel or cause any adverse effects on the system's performance. This requires rigorous testing and adherence to aviation industry standards to ensure the sealant's suitability for the specific application.
Understanding Snowmobile Fuel Lines: Inside the Gas Tank
You may want to see also
Corrosion Inhibition: Preventing corrosion damage to fuel lines and components
Corrosion is a significant concern in aviation, especially when it comes to fuel systems. The harsh environments and varying temperatures experienced by aircraft can accelerate the degradation of materials, leading to costly repairs and potential safety hazards. One critical area where corrosion prevention is essential is in the fuel lines and components. These components are exposed to corrosive elements, including moisture, oxygen, and the inherent acidity of aviation fuels. Over time, corrosion can lead to pitting, cracking, and eventual failure of the fuel lines, which can result in fuel leaks, reduced performance, and even catastrophic failures.
To combat this issue, aviation professionals and engineers have developed specialized corrosion-inhibiting measures. One effective method is the use of corrosion inhibitors, which are additives designed to protect metal surfaces from corrosion. These inhibitors work by forming a protective layer on the metal, often through chemical reactions, which prevent the metal from coming into direct contact with corrosive substances. In the context of fuel lines, corrosion inhibitors are typically added to the fuel itself or applied directly to the internal surfaces of the lines.
The process of inhibiting corrosion in fuel lines involves several key steps. Firstly, the fuel lines must be thoroughly cleaned to remove any existing corrosion or contaminants. This is crucial as any remaining corrosion products or debris could interfere with the inhibitor's effectiveness. After cleaning, the lines are then prepared by applying a suitable primer or surface treatment to ensure optimal adhesion of the corrosion inhibitor. This step is vital to ensure the inhibitor forms a strong bond with the metal surface, providing maximum protection.
Once the preparation is complete, the corrosion inhibitor is applied. This can be done through various methods, including brushing, spraying, or immersion. The inhibitor is carefully selected based on the specific requirements of the fuel type and the environmental conditions the aircraft operates in. Some common types of corrosion inhibitors used in aviation include zinc dialkyl dithiophosphate (ZDDP) and silicate-based inhibitors. These compounds create a protective oxide layer on the metal surface, effectively preventing corrosion.
Regular maintenance and inspection are also essential to ensure the continued effectiveness of corrosion inhibition in aviation fuel lines. Periodic checks should be conducted to identify any signs of corrosion or degradation, allowing for prompt action to be taken. By implementing these corrosion-inhibiting measures, aviation professionals can significantly extend the lifespan of fuel lines and components, ensuring the reliability and safety of aircraft operations.
Houston Fuel Lines: Uncovering Hidden Issues and Solutions
You may want to see also
Compliance with Aviation Standards: Meeting industry regulations for quality and performance
The aviation industry demands the highest standards of reliability and safety, especially when it comes to fuel systems. When it comes to sealing pipe threads in aviation fuel lines, compliance with specific standards is crucial. The primary goal is to ensure that the sealant used is compatible with aviation fuel, provides an effective seal, and meets the stringent performance requirements set by aviation authorities.
One of the key standards that aviation manufacturers and maintenance facilities must adhere to is the Federal Aviation Regulations (FAR) Part 25, which outlines the airworthiness standards for aircraft. For fuel lines, the focus is on ensuring that the sealant used is compatible with the fuel type and does not compromise the structural integrity of the system. Aviation fuel lines are typically exposed to high-pressure environments and varying temperatures, so the sealant must be able to withstand these conditions without degradation.
The choice of sealant is critical to meeting these standards. Aviation-grade pipe thread sealants are specifically formulated to provide a reliable and durable seal in harsh environments. These sealants are designed to be compatible with aviation fuels, including jet fuel, which is known for its corrosive properties. A suitable sealant should offer excellent resistance to fuel-related chemicals, ensuring that it does not leach or dissolve over time, which could lead to fuel contamination and potential engine issues.
Furthermore, the sealant's mechanical properties are essential. It should provide a robust and permanent seal, capable of withstanding the internal pressures and vibrations experienced during flight. The sealant must also be resistant to aging and temperature changes, ensuring long-term performance and reliability. Regular testing and adherence to industry-specific guidelines are necessary to guarantee that the chosen sealant meets these demanding criteria.
In summary, compliance with aviation standards for fuel line sealants involves selecting a sealant that is specifically designed for aviation applications. It must be compatible with aviation fuels, offer excellent mechanical properties, and withstand the rigors of flight operations. By adhering to these regulations, aviation professionals can ensure the safety and reliability of fuel systems, contributing to the overall airworthiness of the aircraft.
The Ultimate Guide to Choosing the Best Fuel Line Cleaner
You may want to see also
Frequently asked questions
Aviation fuel lines require a specialized sealant, such as a pipe thread sealant, to ensure a secure and leak-free connection. This sealant is designed to withstand the extreme conditions of aviation environments, including high temperatures, pressure, and the corrosive effects of aviation fuels.
Regular pipe thread sealants may not provide the necessary durability and compatibility for aviation applications. They might not adhere well to the materials used in fuel lines, such as aluminum or brass, and could fail over time due to the harsh fuel environment. Specialized sealants are formulated to offer superior bonding, flexibility, and resistance to fuel degradation.
The sealant plays a critical role in maintaining the integrity of the fuel system. It prevents fuel leaks, which could lead to dangerous situations, especially during flight. By ensuring a tight seal, the sealant helps to maintain the structural integrity of the fuel lines, reducing the risk of failures that could result in fuel loss, engine damage, or even catastrophic failures.