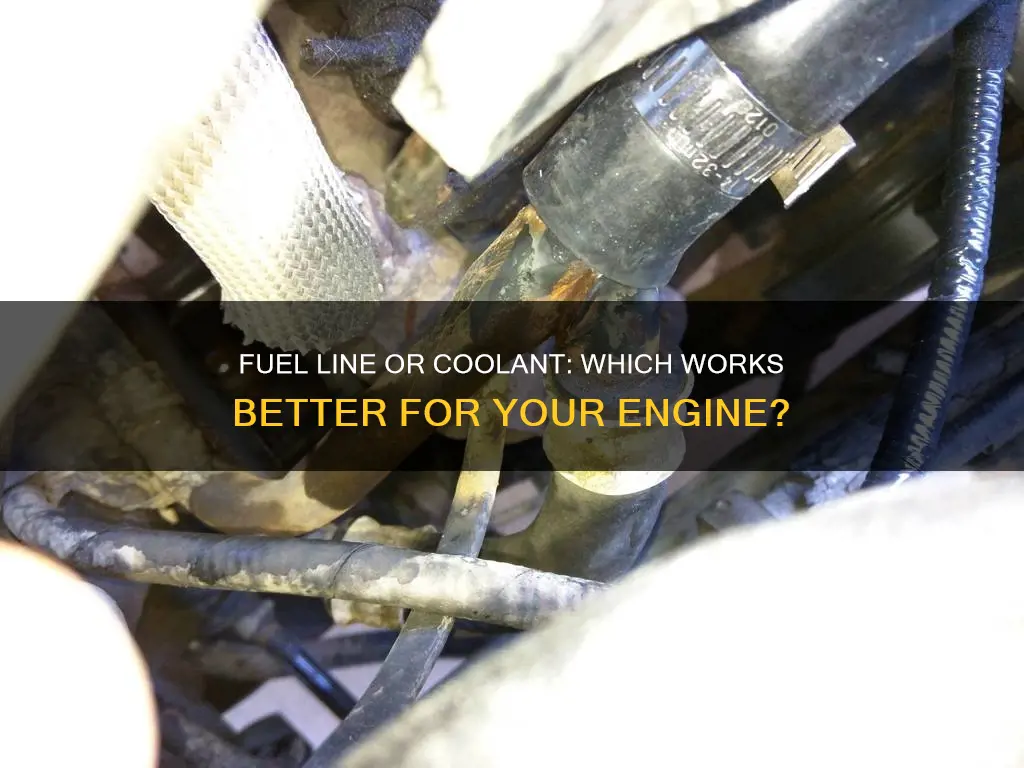
Fuel lines and coolant systems are two distinct components of a vehicle's engine, and they require different materials and maintenance. While fuel lines are designed to carry gasoline or diesel, coolant lines are specifically engineered to handle the engine's cooling fluid. Therefore, it is crucial to understand the differences between these systems to ensure proper maintenance and avoid potential issues. In this article, we will explore whether fuel line work can be applied to coolant systems and the potential risks and benefits of such an approach.
Characteristics | Values |
---|---|
Compatibility | Fuel lines are not designed for coolant and may not be compatible with its chemical composition. Coolant contains additives that can degrade fuel line materials over time. |
Pressure Rating | Fuel lines are typically rated for higher pressures compared to coolant systems. Coolant operates at lower pressures, and using a fuel line might not withstand the coolant's pressure. |
Temperature Range | Coolant systems operate within a specific temperature range, and fuel lines may not be suitable for these temperatures, especially in extreme climates. |
Material | Fuel lines are usually made of materials like rubber or plastic, which might not be resistant to coolant's corrosive properties. |
Flexibility | While fuel lines can be flexible, coolant systems often require more rigid lines to handle the fluid's flow and temperature changes. |
Installation | The installation process for fuel lines and coolant lines differs, and using a fuel line for coolant might require additional modifications. |
Maintenance | Coolant systems may have specific maintenance requirements that differ from fuel systems, making it challenging to use a fuel line for coolant. |
Longevity | Coolant exposure can reduce the lifespan of fuel lines, as the additives in coolant can accelerate material degradation. |
What You'll Learn
- Fuel Line Compatibility: Ensure fuel line material can withstand coolant temperatures and pressures
- Leak Prevention: Properly seal connections to prevent coolant leaks into the fuel system
- Material Selection: Choose fuel lines made from materials resistant to coolant corrosion
- Pressure Rating: Verify fuel lines meet or exceed system pressure requirements
- Installation Guidelines: Follow manufacturer instructions for correct installation and routing
Fuel Line Compatibility: Ensure fuel line material can withstand coolant temperatures and pressures
When considering the compatibility of fuel lines with coolant, it is crucial to understand the specific requirements and challenges that arise from this interaction. Coolants, particularly those used in engines, can operate under extreme conditions, including high temperatures and pressures. Therefore, the choice of fuel line material becomes a critical factor in ensuring the longevity and reliability of the fuel system.
The primary concern is the ability of the fuel line material to withstand the corrosive nature of coolants. Coolants often contain additives that can be aggressive towards certain materials, leading to degradation over time. For instance, ethylene glycol-based coolants, commonly used in automotive applications, can be particularly harsh on rubber and certain types of plastic fuel lines. These coolants can cause swelling, cracking, and eventual failure of the fuel line material, resulting in fuel leaks and potential engine damage.
To address this issue, it is essential to select fuel line materials that are specifically designed to resist coolant-related degradation. One effective approach is to use fuel lines made from materials like stainless steel or high-temperature-resistant polymers. Stainless steel fuel lines offer excellent corrosion resistance due to the protective oxide layer that forms on the surface, making it highly suitable for coolant-carrying applications. Similarly, specialized polymers, such as fluoropolymers or certain types of nylon, can provide the necessary durability to withstand coolant temperatures and pressures.
In addition to material selection, it is crucial to consider the design and construction of the fuel lines. Fuel lines should be designed to minimize stress concentrations and provide a smooth, flexible path for fuel flow. This is particularly important in high-temperature environments, where thermal expansion and contraction can exert significant stress on the fuel lines. Properly designed fuel lines with adequate reinforcement can help prevent cracking and ensure long-term reliability.
Furthermore, regular inspection and maintenance of the fuel system are essential to identify and replace any compromised fuel lines. Over time, even the most durable materials can show signs of wear and tear, especially in high-stress areas. Regular checks can help detect fuel line damage early on, allowing for prompt replacement and preventing potential engine issues. By understanding the specific requirements of coolant-fuel line compatibility, engineers and vehicle owners can ensure the optimal performance and longevity of the fuel system.
Understanding Hose Fuel Lines: A Comprehensive Guide
You may want to see also
Leak Prevention: Properly seal connections to prevent coolant leaks into the fuel system
When dealing with the integration of coolant and fuel systems in vehicles, it's crucial to understand the potential risks and take preventive measures. Coolant leaks into the fuel system can lead to a myriad of issues, including engine misfires, reduced performance, and even engine damage. One of the primary causes of such leaks is improper sealing of connections between the coolant and fuel lines. Here's a detailed guide on how to prevent these leaks:
Understanding the Risks: Before delving into the solutions, it's essential to recognize the potential consequences of coolant entering the fuel system. Coolant, designed to regulate engine temperature, contains additives that can be detrimental to the fuel system. These additives can cause corrosion, leading to the deterioration of fuel lines, injectors, and other fuel system components. Moreover, coolant can alter the combustion process, resulting in poor engine performance and potential engine damage over time.
Proper Sealing Techniques: To prevent coolant leaks, the following sealing methods should be employed:
- Thread Seal Tape: For connections involving threads, use thread seal tape specifically designed for fuel lines. Wrap the tape around the threads in a clockwise direction, ensuring full coverage. This creates a barrier that prevents coolant from seeping into the fuel system.
- Gaskets and O-Rings: When connecting components, always use gaskets or O-rings made from compatible materials. These seals provide a tight, leak-resistant connection. Ensure that the gaskets are properly sized and seated in the corresponding grooves to maintain an effective seal.
- Fuel Line Connectors: Utilize fuel line connectors that are designed to withstand the corrosive effects of coolant. These connectors often feature a durable, sealed design that prevents coolant from entering the fuel system.
Step-by-Step Connection Process: Properly sealing connections requires attention to detail:
- Clean the Connections: Before making any connections, ensure that all surfaces are clean and free from debris or old sealants. Use a solvent-based cleaner to remove any contaminants.
- Apply Sealant: If using thread seal tape, apply a thin layer around the threads. For gaskets and O-rings, ensure they are lubricated and properly positioned before assembly.
- Tighten Securely: When tightening connections, use the appropriate tools to achieve the recommended torque specifications. Over-tightening can damage components, while under-tightening may compromise the seal.
- Test for Leaks: After making the connections, start the engine and monitor for any leaks. If coolant is detected in the fuel system, immediately address the issue by re-sealing the connections.
Regular Maintenance: Preventive maintenance is key to long-term leak prevention. Regularly inspect all connections, especially those involving coolant and fuel lines. Look for signs of corrosion, cracks, or damage. Replacing worn-out components and tightening loose connections can help maintain a leak-free system.
By following these guidelines, you can effectively prevent coolant leaks into the fuel system, ensuring the longevity and optimal performance of your vehicle's engine. Remember, proper sealing techniques and regular maintenance are essential to mitigate the risks associated with coolant and fuel system integration.
Hose Clamps for 5/16 Fuel Lines: Size Matters
You may want to see also
Material Selection: Choose fuel lines made from materials resistant to coolant corrosion
When it comes to choosing the right fuel lines for your vehicle's cooling system, material selection is a critical aspect that often goes unnoticed. Coolant, also known as antifreeze, is a mixture of water and various additives designed to protect the engine from freezing and overheating. However, it can also be corrosive to certain materials, leading to premature wear and potential system failures. Therefore, selecting fuel lines made from materials resistant to coolant corrosion is essential for maintaining the longevity and reliability of your vehicle's cooling system.
One of the most commonly used materials for fuel lines in vehicles is rubber, which offers flexibility and durability. However, not all rubber compounds are created equal. Natural rubber, for instance, is susceptible to degradation when exposed to coolant over time. This degradation can lead to cracks, leaks, and ultimately, system failure. To combat this issue, manufacturers often use synthetic rubbers, such as neoprene or EPDM (ethylene propylene diene monomer), which provide better resistance to coolant corrosion. These synthetic rubbers are designed to withstand the chemical properties of coolant, ensuring that the fuel lines remain intact and functional.
Another material that has gained popularity in fuel line construction is polyurethane. This material offers superior resistance to coolant corrosion compared to rubber. Polyurethane fuel lines are known for their excellent flexibility, durability, and resistance to abrasion. They can withstand the harsh conditions of the engine bay, including exposure to high temperatures and various chemicals. Additionally, polyurethane fuel lines are less prone to cracking and leaking, making them a reliable choice for vehicles with high coolant exposure.
In some cases, fuel lines may also incorporate braided reinforcement to enhance their strength and flexibility. This braided layer, typically made from steel or stainless steel, provides additional protection against coolant corrosion. The braiding technique helps distribute stress evenly across the fuel line, preventing cracks and leaks. When selecting fuel lines, look for those with braided reinforcement, especially if your vehicle operates in extreme conditions or has a history of coolant-related issues.
In summary, when it comes to material selection for fuel lines working with coolant, opting for materials resistant to corrosion is paramount. Synthetic rubbers, such as neoprene and EPDM, offer improved resistance compared to natural rubber. Polyurethane fuel lines provide superior durability and flexibility, making them an excellent choice for long-lasting performance. Additionally, considering fuel lines with braided reinforcement can further enhance their strength and reliability. By choosing the right materials, you can ensure that your vehicle's cooling system remains efficient and dependable, even in the face of coolant exposure.
Flue Liner Sizing Guide: Choosing the Right Fit for Your Multi-Fuel Stove
You may want to see also
Pressure Rating: Verify fuel lines meet or exceed system pressure requirements
When it comes to ensuring the functionality and longevity of your fuel system, especially in relation to coolant, one critical aspect often overlooked is the pressure rating of fuel lines. This is a crucial factor that can significantly impact the performance and safety of your vehicle. Here's a detailed guide on why verifying the pressure rating of fuel lines is essential.
Fuel lines are responsible for transporting fuel from the tank to the engine, and in some cases, they also carry coolant to regulate engine temperature. The pressure within these lines can vary depending on the vehicle's operating conditions and the design of the fuel system. It is imperative to ensure that the fuel lines can withstand the pressure exerted by the system to prevent potential failures.
The pressure rating of a fuel line is typically specified by the manufacturer and is a critical design consideration. It indicates the maximum pressure the line can handle without compromising its structural integrity. When installing or replacing fuel lines, it is imperative to choose lines that meet or exceed the system's pressure requirements. This ensures that the fuel lines can handle the pressure fluctuations during engine operation, including acceleration, deceleration, and changes in altitude.
Verifying the pressure rating is a straightforward process. Start by consulting the vehicle's service manual or the manufacturer's specifications for the recommended pressure rating for your particular fuel system. Compare this with the pressure rating of the fuel lines you intend to use. Ensure that the lines have a higher or equal pressure rating to the system's requirements. This simple check can prevent potential issues such as fuel leaks, line rupture, or engine damage caused by pressure-related failures.
Additionally, it is worth noting that fuel lines may also carry coolant in some vehicles, especially in older models. Coolant pressure can vary, and ensuring that the fuel lines can handle this pressure is crucial. Regular maintenance and inspections can help identify any potential issues, allowing for timely replacements before pressure-related problems occur. By paying attention to the pressure rating, you can ensure the reliability and safety of your vehicle's fuel system, including its interaction with coolant.
Fuel Filter's Three Lines: Unraveling the Mystery in Ford Expedition
You may want to see also
Installation Guidelines: Follow manufacturer instructions for correct installation and routing
When it comes to installing a fuel line for coolant, it's crucial to follow the manufacturer's instructions to ensure a proper and safe setup. This is because different vehicles may have specific requirements and specifications for coolant systems, and using the correct parts and methods is essential for optimal performance and safety.
The first step is to gather all the necessary components, including the fuel line, coolant reservoir, and any additional fittings or adapters required. It's important to inspect these parts for any defects or damage before proceeding with the installation. Check for any bends, cracks, or leaks in the fuel line, as these issues can lead to potential problems during operation.
Next, locate the appropriate mounting points for the coolant reservoir and fuel line. These points are usually specified in the vehicle's manual or can be identified by their unique shapes or markings. Ensure that the reservoir is positioned in a convenient location for easy access and that the fuel line is routed correctly to connect the reservoir to the engine's coolant system. Proper routing is critical to prevent kinks and ensure a smooth flow of coolant.
During the installation process, pay close attention to the manufacturer's guidelines for routing the fuel line. The line should be secured and supported at regular intervals to prevent excessive strain or damage. Avoid routing the fuel line near hot surfaces or under the vehicle's body, as this can lead to potential hazards. Additionally, ensure that all connections are tightened securely to prevent leaks.
Once the installation is complete, it's essential to test the system for any leaks. Start the engine and check for any signs of coolant or fuel leakage. If any issues are found, carefully inspect the connections and make the necessary adjustments or tightenings. After ensuring the system is leak-free, fill the coolant reservoir to the recommended level and start the engine to verify that the coolant circulates properly. Always refer to the manufacturer's instructions for any specific testing procedures or maintenance requirements.
Unveiling the Fuel Line Mystery: Boeing 747's Fuel Line Size Explained
You may want to see also
Frequently asked questions
While fuel lines and coolant lines are both made of similar materials, they serve different purposes. Fuel lines are designed to withstand the pressure and temperature changes associated with fuel, which can be highly volatile. Coolant, on the other hand, is a liquid that circulates through the engine to regulate temperature and lubricate the engine components. Therefore, using fuel line as a replacement for coolant lines is not recommended as it may not provide the necessary protection and performance for the engine's cooling system.
In an emergency situation, it is understandable to make temporary fixes. However, it is crucial to understand the risks involved. Fuel lines are not designed to handle the corrosive nature of coolant, which can lead to internal engine damage over time. Additionally, fuel lines may not have the same level of flexibility and durability as coolant lines, potentially leading to leaks or damage to the engine components. It is always best to use the correct type of hose for the intended purpose to ensure the longevity and reliability of your vehicle.
Coolant lines are specifically engineered to withstand the corrosive properties of coolant, which helps prevent internal engine damage. They are also designed to handle the pressure and temperature changes associated with the engine's cooling system. Coolant lines often feature a more flexible material, allowing for easier installation and better adaptability to the engine's layout. Using the right type of hose for the specific application ensures optimal performance and protects your engine from potential issues.
Modifying fuel lines to function as coolant lines is not a recommended practice. The materials and construction of fuel lines are tailored to withstand fuel's unique properties, which may not align with the requirements of coolant. Modifying the lines could lead to reduced performance, potential leaks, and long-term damage to the engine. It is best to consult a professional mechanic or refer to the vehicle's manual for the appropriate hose specifications to ensure a safe and effective repair.