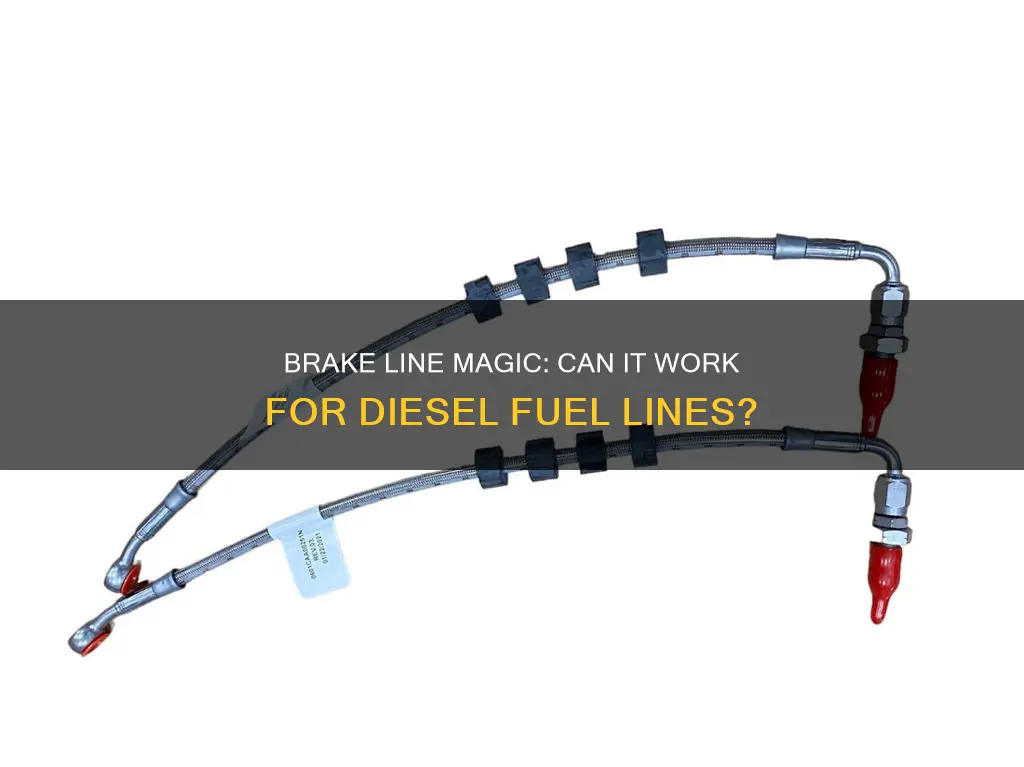
Brake lines and diesel fuel lines serve distinct purposes in a vehicle's system. While brake lines are responsible for transmitting hydraulic pressure to the brakes, ensuring safe and efficient stopping, diesel fuel lines are designed to transport fuel from the tank to the engine. Despite their different functions, both systems rely on similar principles of fluid transmission and require careful installation and maintenance to ensure optimal performance. This introduction sets the stage for a discussion on the compatibility and considerations of using brake lines for diesel fuel lines, highlighting the importance of understanding the unique requirements of each system.
Characteristics | Values |
---|---|
Compatibility | Brake lines are generally not compatible with diesel fuel lines due to differences in material, pressure, and temperature requirements. |
Material | Brake lines typically use steel or aluminum, which may not withstand the corrosive nature of diesel fuel. |
Pressure Rating | Brake lines are designed for lower pressure systems, while diesel fuel lines require higher pressure ratings. |
Temperature Tolerance | Brake lines may not handle the extreme temperatures that diesel fuel can experience, especially during engine operation. |
Flexibility | The rigid nature of brake lines might not allow for the necessary flexibility required in fuel lines to accommodate engine movement. |
Corrosion Resistance | Diesel fuel can corrode certain materials used in brake lines, leading to potential leaks and performance issues. |
Availability | Specialized fuel lines designed for diesel engines are more readily available and recommended for use. |
What You'll Learn
- Material Compatibility: Ensure brake lines are made from materials that can withstand diesel fuel's corrosive properties
- Pressure Rating: Verify brake lines can handle the pressure of diesel fuel at various temperatures
- Flexibility: Check for flexibility to accommodate engine movement and potential vibrations
- Durability: Assess the durability against diesel fuel's potential degradation effects over time
- Routing: Design a route that avoids sharp bends and potential stress points
Material Compatibility: Ensure brake lines are made from materials that can withstand diesel fuel's corrosive properties
When it comes to using brake lines for diesel fuel lines, material compatibility is a critical factor to consider. The corrosive nature of diesel fuel can lead to premature degradation of the brake line materials, resulting in potential safety hazards. Therefore, it is essential to choose brake lines made from materials that can withstand the harsh environment of diesel fuel.
One of the primary concerns with diesel fuel is its tendency to cause oxidation and corrosion of metal components. To combat this, brake lines should be constructed using materials that are resistant to oxidation and corrosion. Stainless steel is an excellent choice for brake lines in diesel applications. It is known for its superior corrosion resistance, making it ideal for withstanding the corrosive properties of diesel fuel. The use of stainless steel ensures that the brake lines remain durable and reliable over an extended period.
In addition to stainless steel, some manufacturers also utilize specialized coatings or treatments to enhance the material's compatibility with diesel fuel. These coatings can provide an extra layer of protection against corrosion, ensuring that the brake lines maintain their structural integrity. It is crucial to look for brake lines that have been specifically engineered to meet the demands of diesel fuel systems.
Another consideration is the flexibility and durability of the brake lines. Diesel fuel lines often experience vibrations and movements due to engine operation. Therefore, the brake lines should be flexible enough to accommodate these movements without compromising their structural integrity. Materials like braided stainless steel or synthetic composites can offer the necessary flexibility while maintaining the required strength.
Furthermore, it is essential to ensure that the brake lines are properly sealed and protected from any direct contact with diesel fuel. This can be achieved by using high-quality fittings and seals that are compatible with the chosen material. By combining the right materials and construction techniques, brake lines can effectively withstand the corrosive nature of diesel fuel, ensuring safe and reliable operation of the vehicle's braking system.
Optimizing Performance: Choosing the Right Fuel Line for Your 326 LX
You may want to see also
Pressure Rating: Verify brake lines can handle the pressure of diesel fuel at various temperatures
When considering the use of brake lines for diesel fuel lines, it is crucial to evaluate their pressure-handling capabilities, especially in the context of diesel fuel's unique properties. Diesel fuel operates under higher pressure compared to gasoline, and its temperature variations can significantly impact the system's integrity. Therefore, ensuring that the brake lines can withstand these conditions is essential for safe and efficient operation.
The pressure rating of brake lines is a critical factor in this assessment. Brake lines are designed to transmit hydraulic pressure from the master cylinder to the calipers or wheel cylinders, enabling braking action. However, diesel fuel systems operate at much higher pressures, often exceeding 1000 psi, depending on the engine and fuel system design. Therefore, the brake lines must be rated to handle these elevated pressures to prevent failures and ensure the safety of the vehicle.
To verify the pressure rating, it is essential to consult the vehicle's manufacturer specifications or technical manuals. These resources provide detailed information on the recommended brake line materials, diameters, and pressure ratings suitable for the specific diesel fuel system in question. Using brake lines with inadequate pressure ratings can lead to premature failure, fuel leaks, or even catastrophic system failures, posing significant risks to the vehicle and its occupants.
Additionally, temperature variations in diesel fuel systems should be considered. Diesel fuel can experience wide temperature fluctuations, from extremely cold conditions during winter to high temperatures when the engine is running. These temperature changes can affect the pressure within the fuel system and, consequently, the brake lines. It is crucial to select brake lines that can accommodate these temperature variations without compromising their structural integrity or pressure-bearing capacity.
In summary, when adapting brake lines for diesel fuel lines, a thorough examination of the pressure rating is imperative. This ensures that the brake lines can effectively manage the higher pressures associated with diesel fuel while also accounting for temperature variations. By adhering to manufacturer guidelines and selecting suitable brake line materials, vehicle owners can ensure the reliability and safety of their diesel fuel systems, ultimately contributing to a more robust and efficient vehicle performance.
Dissolving Fuel Line: Uncover the Mystery Behind Your Chainsaw's Malfunction
You may want to see also
Flexibility: Check for flexibility to accommodate engine movement and potential vibrations
When considering the use of brake lines for diesel fuel lines, it's crucial to evaluate the flexibility of the system. Diesel engines are known for their robust and powerful performance, but they also generate significant vibrations and experience substantial movement during operation. Therefore, the fuel lines must be able to accommodate these factors to ensure optimal performance and longevity.
One way to assess flexibility is by physically inspecting the lines. Look for any kinks or sharp bends that could restrict movement. Flexibility is essential to allow the lines to move freely with the engine's natural vibrations. Overly rigid lines may lead to stress points, potential leaks, and even damage to the engine or fuel system components over time.
You can also perform a simple test by gently moving the engine and observing how the fuel lines respond. A flexible system should allow for smooth, unrestricted movement without any visible strain or stress on the lines. This test can help identify any potential issues before they become major problems.
Additionally, consider the material of the brake lines. Some materials, like rubber or flexible plastic, offer better flexibility compared to rigid metal. For diesel fuel lines, a material that can withstand the corrosive nature of diesel fuel while maintaining flexibility is ideal. This ensures that the lines can adapt to the engine's movement without compromising their integrity.
In summary, when using brake lines for diesel fuel lines, flexibility is a critical aspect to consider. It allows the system to accommodate engine vibrations and movement, reducing the risk of damage and ensuring a reliable fuel supply. Regular inspection and the use of appropriate, flexible materials can contribute to the overall performance and longevity of the diesel fuel system.
Understanding Jeep's Dual Action Fuel Pump: The Double Line Advantage
You may want to see also
Durability: Assess the durability against diesel fuel's potential degradation effects over time
When considering the use of brake lines for diesel fuel lines, it is crucial to evaluate the durability of these components in the context of diesel fuel's unique properties and potential degradation effects over time. Diesel fuel, known for its higher sulfur content and different chemical composition compared to gasoline, can have a more significant impact on the materials used in fuel lines.
Brake lines, typically made from various types of rubber, plastic, or metal, are designed to withstand the forces and pressures associated with braking systems. However, when exposed to diesel fuel, certain factors come into play that may affect their long-term performance. One key consideration is the potential for fuel-related degradation, which can lead to reduced flexibility, cracking, or even material failure over time.
The higher sulfur content in diesel fuel can accelerate the aging process of materials, causing them to become brittle and more susceptible to damage. This is particularly relevant for rubber components, as sulfur can promote cross-linking, making the rubber harder and less flexible. As a result, brake lines used for diesel fuel lines might not maintain their original pliability, potentially leading to leaks or reduced performance.
To ensure durability, it is essential to select brake lines made from materials specifically designed to withstand the challenges posed by diesel fuel. Some manufacturers offer fuel-resistant brake lines that incorporate specialized rubbers or plastics with improved resistance to sulfur compounds. These materials can help prevent degradation and maintain the integrity of the fuel lines over extended periods.
Additionally, regular inspections and maintenance are vital to identify any signs of degradation or damage early on. This includes checking for cracks, leaks, or changes in the material's appearance, especially in areas where the brake lines are most susceptible to fuel exposure. By implementing proper maintenance practices, you can ensure that the brake lines remain effective and reliable, even when used for diesel fuel lines.
Dirt Bike Fuel Line Attachment: A Comprehensive Guide
You may want to see also
Routing: Design a route that avoids sharp bends and potential stress points
When designing a route for brake lines in a diesel fuel system, it is crucial to prioritize safety and reliability. The primary goal is to ensure that the brake lines are not subjected to excessive stress or sharp bends, as these can compromise their integrity and performance. Here's a detailed approach to achieving this:
Smooth and Gradual Bends: One of the key principles is to minimize sharp bends in the routing. Brake lines should be routed in a way that allows for smooth, gradual curves. This can be achieved by following the natural contours of the vehicle's frame and using gentle bends whenever possible. Avoid abrupt changes in direction, as these can create stress points and potentially lead to line damage over time. For example, when routing the brake lines from the fuel tank to the engine bay, aim for a gradual curve rather than a sharp angle, ensuring the line's flexibility and reducing the risk of damage.
Avoid High-Stress Areas: Identify and steer clear of high-stress areas within the vehicle's structure. These areas often include sharp corners, engine compartments, and areas near suspension components. When routing brake lines, try to keep them away from these regions to prevent potential interference with moving parts or excessive strain on the lines. For instance, routing the lines near the suspension arms or under the engine could lead to damage during normal vehicle operation.
Use Appropriate Support: To further enhance the integrity of the brake lines, consider using appropriate support structures. This might include mounting the lines on brackets or using protective sleeves to guide them around sharp corners. These supports can help maintain the lines' shape and prevent them from being pinched or damaged by other components. Ensure that the chosen support system allows for some flexibility to accommodate the lines' natural movement during vehicle operation.
Consider Vehicle Dynamics: Take into account the vehicle's dynamics and potential movement during operation. The brake lines should be routed in a way that accounts for the vehicle's natural sway and movement, especially during acceleration and braking. This ensures that the lines remain taut and secure, reducing the chances of damage or disconnection.
Regular Inspection and Maintenance: Finally, establish a routine inspection and maintenance schedule for the brake lines. Regularly check for any signs of wear, damage, or stress points. This proactive approach will help identify potential issues before they become major problems. By addressing any concerns promptly, you can ensure the long-term reliability of the brake lines in the diesel fuel system.
Air Bubbles in Diesel Fuel Lines: A Cause for Concern?
You may want to see also
Frequently asked questions
While brake lines and diesel fuel lines serve similar purposes in terms of containing fluid, they are not interchangeable. Brake lines are designed to withstand the heat and pressure generated by braking systems, which involves high temperatures and varying levels of vacuum. In contrast, diesel fuel lines need to handle the pressure and temperature changes associated with fuel injection systems, which can be more extreme. Therefore, using brake lines for diesel fuel lines may not provide the necessary protection and could lead to potential issues.
One potential advantage is the cost-effectiveness of using brake lines, as they are generally more affordable than specialized diesel fuel lines. Additionally, brake lines might be more readily available in certain regions or from specific suppliers. However, it's crucial to consider the potential risks and limitations mentioned in the previous answer.
Yes, there are a few important factors to keep in mind. Firstly, the brake lines should be compatible with the fuel type, as diesel fuel has different properties than gasoline. Secondly, the lines should be able to withstand the pressure and temperature fluctuations in the diesel system. It is recommended to consult the vehicle's manual or seek professional advice to ensure the chosen brake lines meet the specific requirements of the diesel fuel system.