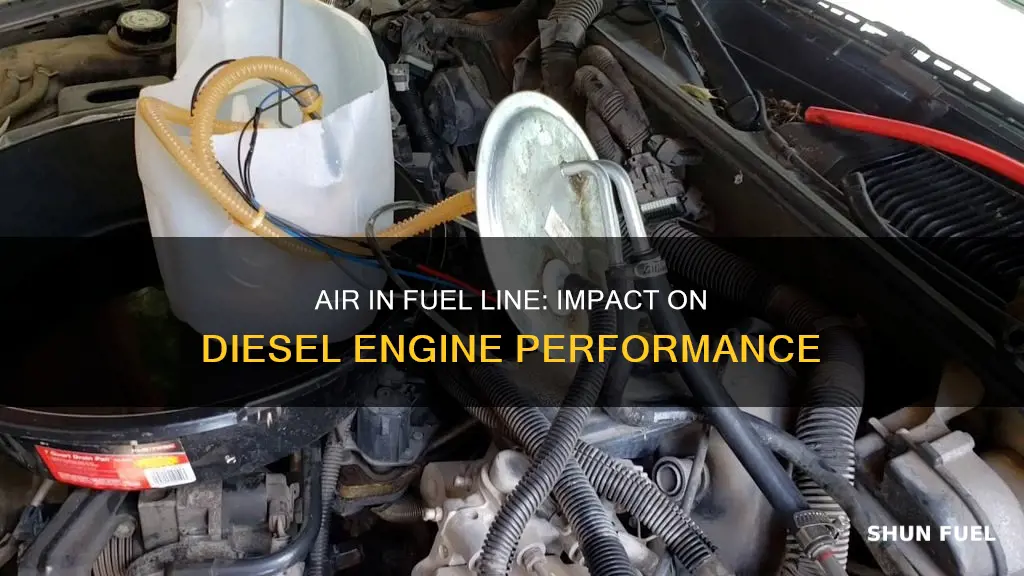
When it comes to diesel engines, air in the fuel line can be a significant issue. Air bubbles in the fuel system can lead to a variety of problems, including reduced engine performance, increased fuel consumption, and even engine damage. This is because air can cause the fuel to vaporize, leading to improper atomization and combustion, which can result in misfires, reduced power, and increased emissions. In severe cases, air in the fuel line can cause the engine to stall or even shut down completely. Understanding the causes and effects of air in the fuel line is crucial for maintaining the health and longevity of a diesel engine.
What You'll Learn
- Air Locks: Air bubbles in fuel lines can cause engine misfires and reduced performance
- Fuel Contamination: Air in fuel can lead to engine knocking and potential damage
- Engine Stall: Air bubbles may cause the engine to stall or lose power
- Fuel Pressure: Air in the line can affect fuel pressure, leading to poor performance
- Engine Overheating: Air in the fuel can cause overheating due to inefficient combustion
Air Locks: Air bubbles in fuel lines can cause engine misfires and reduced performance
Air locks in fuel lines are a common issue for diesel engines and can lead to a variety of performance problems. When air bubbles enter the fuel system, they can cause a range of symptoms, from misfires and reduced power to poor fuel economy and even engine stall. Understanding the causes and effects of air locks is essential for maintaining a diesel engine's optimal performance.
The primary cause of air locks is the introduction of air into the fuel system during the fueling process. This can happen for several reasons: improper fueling techniques, such as rapid fueling or leaving the fuel nozzle open for too long, can introduce air into the fuel tank. Additionally, fuel tanks with small openings or narrow necks may not allow for proper fuel flow, leading to the accumulation of air bubbles. Over time, these air bubbles can travel through the fuel lines and into the engine, causing issues.
When air bubbles reach the engine, they can disrupt the proper atomization of fuel, which is crucial for efficient combustion. The air bubbles may cause the fuel to spray unevenly, leading to incomplete combustion and misfires. Misfires occur when a cylinder fails to ignite the air-fuel mixture properly, resulting in a lack of power and potential damage to engine components over time. Furthermore, air bubbles can also reduce the engine's overall performance by decreasing the efficiency of the fuel injection system.
To address air locks, several solutions can be implemented. One effective method is to use a fuel filter with a built-in air separator, which can trap air bubbles before they reach the engine. Regularly checking and replacing the fuel filter is essential, especially after long periods of use or when the engine shows signs of air lock-related issues. Additionally, ensuring proper fueling techniques, such as using a steady fueling rate and avoiding rapid fueling, can help prevent air from entering the fuel system.
In summary, air locks in fuel lines are a significant concern for diesel engines, as they can lead to misfires, reduced performance, and other engine problems. By understanding the causes and implementing preventive measures, such as using air separators and proper fueling techniques, diesel engine owners can minimize the occurrence of air locks and maintain their engine's optimal functionality. Regular maintenance and attention to fueling practices are key to ensuring a healthy and efficient diesel engine.
Optimal Fuel Line Size for Efficient Beckett Oil Furnace Performance
You may want to see also
Fuel Contamination: Air in fuel can lead to engine knocking and potential damage
The presence of air in the fuel system of a diesel engine can have detrimental effects on its performance and longevity. When air enters the fuel lines, it can lead to several issues, primarily related to engine knocking and potential damage to critical components. This phenomenon is a common problem in diesel engines, often caused by improper fueling practices or system malfunctions.
One of the immediate consequences of air in the fuel is engine knocking, a condition where the air-fuel mixture in the combustion chamber ignites prematurely before the piston reaches the top of its compression stroke. This knocking sound is a clear indicator of fuel contamination with air. The excessive heat generated by this premature ignition can lead to rapid wear and tear of engine components, especially the piston rings and cylinder walls. Over time, this can result in increased engine operating temperatures, reduced power output, and even engine failure.
The entry of air into the fuel system can also cause the fuel to become less dense, leading to a leaner air-fuel mixture. This lean mixture may not provide sufficient energy for the engine to operate efficiently, resulting in reduced power and performance. In extreme cases, the engine may stall due to a lack of proper fuel-air mixture, especially during acceleration or when the engine is under load.
To mitigate these issues, it is crucial to ensure that the fuel system is properly maintained and that the fuel is free from air. Regularly checking and replacing fuel filters can help prevent air from entering the system. Additionally, using fuel additives designed to reduce air bubbles can be beneficial. However, it is essential to follow manufacturer guidelines when using such additives to avoid any adverse effects on engine performance.
In summary, air in the fuel line is a significant concern for diesel engines, as it can lead to engine knocking, reduced performance, and potential damage to critical engine components. Proper maintenance and attention to fueling practices are essential to prevent these issues and ensure the engine operates optimally.
Unveiling the Material Secrets of Micro Fuel Lines
You may want to see also
Engine Stall: Air bubbles may cause the engine to stall or lose power
Air bubbles in the fuel line can be a significant issue for diesel engines, often leading to engine stalls and reduced performance. This problem is more common in older diesel engines or those that have been modified or serviced improperly. When air bubbles enter the fuel system, they can cause a variety of symptoms, all of which can be detrimental to the engine's operation.
The primary concern with air bubbles is their ability to disrupt the fuel-air mixture, which is essential for combustion. In a diesel engine, the fuel is injected into the combustion chamber and mixes with air, which is then ignited to produce power. However, when air bubbles are present, they can separate the fuel from the air, leading to incomplete combustion. This results in a lack of power and can even cause the engine to stall.
One of the most noticeable signs of air bubbles in the fuel line is a sudden drop in engine power. The engine may lose its usual response to throttle inputs, becoming unresponsive or hesitating before responding. This is often accompanied by a noticeable change in the engine's sound, which may become quieter or more erratic. In some cases, the engine may even shut off completely, especially if the air bubbles are severe or persistent.
To address this issue, it is crucial to identify and eliminate the source of the air bubbles. This might involve checking the fuel filter for clogs or debris, as a dirty or damaged filter can allow air to enter the system. Ensuring that the fuel tank is properly vented and that there are no leaks in the fuel lines can also help prevent air bubbles. In some cases, a fuel system flush and inspection may be necessary to remove any accumulated air or contaminants.
Regular maintenance and proper fueling practices can significantly reduce the likelihood of air bubbles causing engine stalls. This includes using the correct fuel type and ensuring that the fuel system is clean and well-maintained. By addressing these issues, diesel engine owners can ensure reliable performance and avoid the inconvenience and potential damage caused by engine stalls due to air bubbles.
Understanding Jeep's Dual Action Fuel Pump: The Double Line Advantage
You may want to see also
Fuel Pressure: Air in the line can affect fuel pressure, leading to poor performance
The presence of air in the fuel line can have a significant impact on the performance of a diesel engine, primarily by affecting fuel pressure. When air is introduced into the fuel system, it can lead to a decrease in the overall pressure, which is crucial for proper engine operation. Fuel pressure is directly related to the engine's ability to atomize and inject the fuel effectively. In a diesel engine, the fuel is typically injected at high pressure into the combustion chamber, where it is rapidly heated and mixed with air to create a powerful explosion, driving the pistons and generating power.
As air enters the fuel line, it creates a mixture of air and fuel, diluting the fuel's concentration. This dilution results in a lower fuel pressure, as the air reduces the overall density of the fuel-air mixture. Lower fuel pressure can lead to a variety of performance issues. One of the most common problems is a decrease in power output. The engine may struggle to produce the required horsepower and torque, resulting in a loss of performance. This is because the engine's fuel injection system is designed to deliver a precise amount of fuel at a specific pressure to ensure optimal combustion. When the pressure is compromised, the engine may not receive the necessary fuel volume, leading to incomplete combustion and reduced power.
Additionally, air in the fuel line can cause erratic engine behavior. The engine may hesitate, stall, or even shut off unexpectedly. This is because the air bubbles can cause inconsistent fuel delivery, leading to misfires and a loss of control over the engine's operation. In some cases, the engine may start and run smoothly for a while, but as the air bubbles continue to circulate, the performance may deteriorate, causing the engine to become unstable.
To address this issue, it is essential to ensure that the fuel system is free from air bubbles. One common method is to use a fuel lift pump, which helps to maintain a consistent fuel pressure by drawing fuel from the tank and sending it to the engine at a controlled rate. This prevents air from entering the system and ensures a steady supply of fuel. Regularly checking and replacing the fuel filter is also crucial, as it can trap any contaminants, including air bubbles, that may have entered the system.
In summary, air in the fuel line can significantly impact diesel engine performance by affecting fuel pressure. It can lead to reduced power output, erratic behavior, and potential engine stalls. Proper maintenance, including the use of fuel lift pumps and regular filter changes, is essential to prevent air bubbles and ensure optimal engine operation. Understanding these effects is vital for diesel engine owners and operators to maintain reliable and efficient performance.
The Color of Oxyfuel: Unveiling the Oxy-Fuel Cutting Mystery
You may want to see also
Engine Overheating: Air in the fuel can cause overheating due to inefficient combustion
The presence of air in the fuel system of a diesel engine can lead to a range of performance issues, one of the most critical being engine overheating. This phenomenon occurs due to the inefficient combustion process that arises when air is introduced into the fuel.
When air is mixed with the fuel, it dilutes the concentration of the fuel-air mixture, which is essential for proper combustion. In diesel engines, the fuel is injected under high pressure into the combustion chamber, where it mixes with air and ignites, producing power. However, if air is present in the fuel, it can disrupt this process. The air-fuel mixture may not ignite completely, leading to incomplete combustion. This results in the production of excess heat, which can cause the engine to overheat.
Overheating can have severe consequences for the engine's performance and longevity. The excessive heat generated during incomplete combustion can cause the engine's components to expand and potentially warp or crack. This is particularly concerning for parts like the cylinder head and block, which are critical to the engine's operation. Moreover, the engine's cooling system may struggle to dissipate the additional heat, leading to a rapid rise in temperature.
To prevent engine overheating caused by air in the fuel, it is crucial to maintain a proper fuel-air mixture. This can be achieved by ensuring that the fuel injection system is calibrated correctly and that the fuel pressure is within the specified range. Regular maintenance, including fuel filter changes and system checks, can help identify and rectify any issues related to air intrusion in the fuel. Additionally, using a fuel additive designed to improve combustion efficiency can assist in maintaining optimal engine performance.
In summary, air in the fuel line can significantly impact a diesel engine's performance and health. The inefficient combustion resulting from air dilution can lead to overheating, causing potential damage to engine components. By understanding this relationship and implementing appropriate maintenance measures, diesel engine owners can ensure reliable operation and extend the lifespan of their vehicles.
Unleash Your Engine's Potential: Understanding the 8AM Fuel Line
You may want to see also
Frequently asked questions
Yes, air in the fuel line can definitely lead to engine stalling. When air enters the fuel system, it can cause the fuel to become less dense, leading to improper atomization and combustion. This results in a loss of power, reduced performance, and potential stalling, especially during acceleration or when the engine is under load.
Air bubbles in the fuel line can have several negative impacts. Firstly, it can lead to poor fuel-air mixture quality, resulting in misfires and reduced power output. Secondly, air can cause fuel to vaporize, leading to fuel pump cavitation, which can damage the pump over time. This issue is particularly common in older diesel engines with less sophisticated fuel injection systems.
Yes, air in the fuel line can contribute to engine knocking or pinging, especially when the engine is running at high speeds or under high load conditions. Knocking occurs when the air-fuel mixture ignites prematurely due to the high temperatures and pressures in the cylinder, causing a rapid and uncontrolled combustion process. This can lead to engine damage if not addressed promptly.
There are several reasons why air might enter the fuel line. One common cause is a faulty fuel lift pump, which fails to properly pressurize the fuel, allowing air to enter. Additionally, issues with the fuel filter, such as clogs or damage, can restrict fuel flow and create a vacuum that draws in air. Leaks in the fuel system, including the lines and injectors, can also introduce air into the fuel.