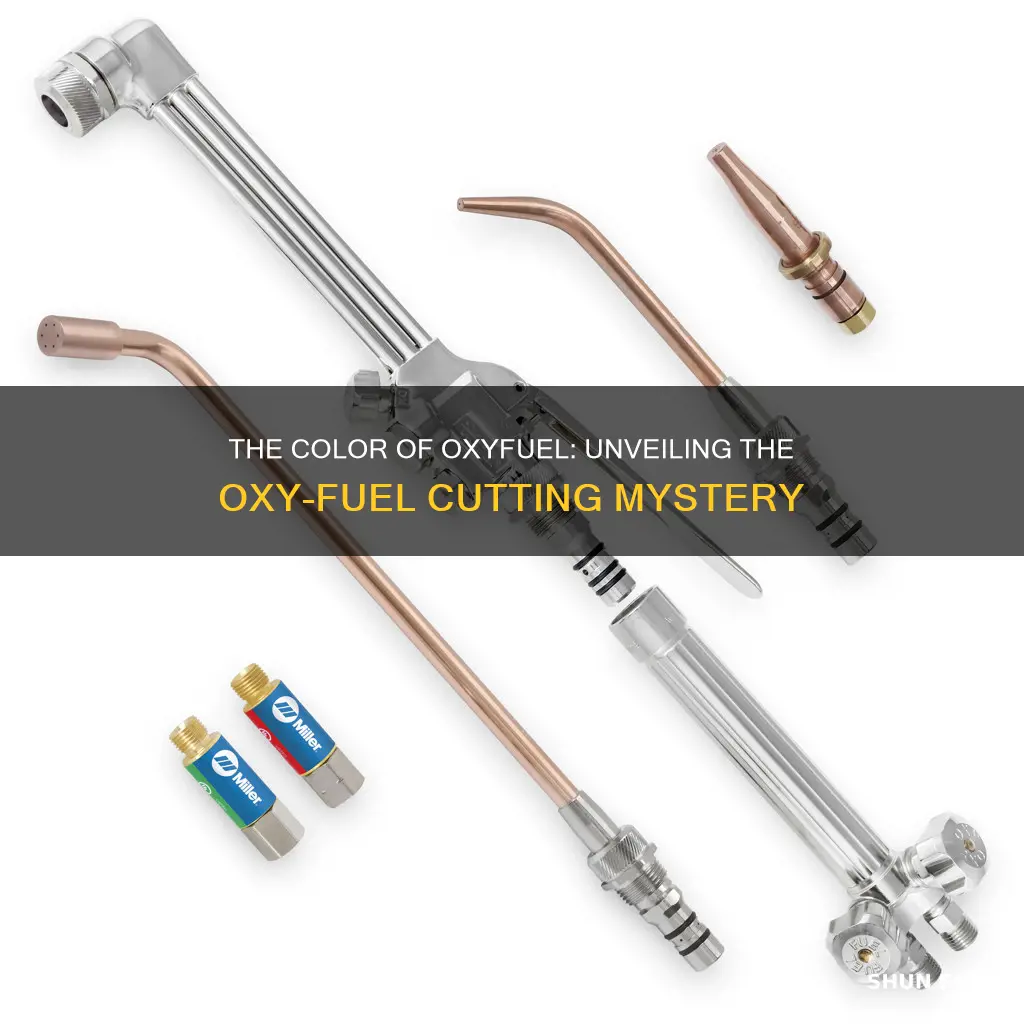
Oxy-fuel cutting is a process that utilizes a mixture of oxygen and fuel gases to produce a high-temperature flame, which is then used to cut through various materials. The color of the flame produced by an oxy-fuel cutting torch can vary depending on the specific gases used and the cutting conditions. When cutting with an oxy-fuel torch, the flame is typically a bright, blue-white color, which is a result of the combustion of the fuel gas (such as acetylene or propylene) with the oxygen. This flame is highly efficient and provides precise control over the cutting process, making it a popular choice for metal fabrication and welding applications.
What You'll Learn
- Oxy-fuel cutting gas color: typically blue or yellow depending on the fuel mix
- Gas color intensity: influenced by oxygen and fuel flow rates
- Flame color variations: affect cutting quality and material compatibility
- Safety precautions: wear protective gear to avoid burns from hot gas
- Gas color control: adjust oxygen and fuel to achieve desired flame color
Oxy-fuel cutting gas color: typically blue or yellow depending on the fuel mix
Oxy-fuel cutting is a process that utilizes a mixture of oxygen and fuel gases to produce a high-temperature flame for cutting or welding. The color of the flame produced by this method is a critical aspect of the process, as it indicates the temperature and efficiency of the cut. The color of the oxy-fuel cutting gas is typically blue or yellow, depending on the specific fuel mix used.
When using a mixture of oxygen and acetylene, the flame is usually a bright blue color. This blue flame is highly efficient and provides a clean, precise cut. The blue color is a result of the combustion of acetylene, which produces a high temperature and a stable flame. This type of flame is ideal for cutting a wide range of materials, including metals, plastics, and composites.
On the other hand, when using a mixture of oxygen and propylene, the flame color can vary. In some cases, it may appear as a bright yellow flame, which is less efficient than the blue flame produced by acetylene. The yellow color is due to the presence of carbon monoxide in the flame, which is a byproduct of the incomplete combustion of propylene. This type of flame is less stable and may not provide the same level of precision as the blue flame.
The color of the oxy-fuel cutting gas is an important indicator of the process's efficiency and the quality of the cut. A blue flame is generally preferred as it provides a more controlled and precise cut, resulting in a cleaner edge and reduced heat-affected zone. In contrast, a yellow flame may indicate a less efficient process, leading to a less precise cut and potential damage to the material being cut.
Understanding the color of the oxy-fuel cutting gas is essential for operators to ensure they are using the correct fuel mix and maintaining the desired flame temperature. By recognizing the color changes, operators can make adjustments to the fuel flow or oxygen supply to achieve the optimal cutting conditions. This knowledge is crucial for achieving high-quality cuts and maintaining the integrity of the materials being processed.
Troubleshooting Clogged Fuel Lines: Common Causes and Solutions
You may want to see also
Gas color intensity: influenced by oxygen and fuel flow rates
The color of the flame produced by oxy-fuel cutting is a fascinating phenomenon and a critical aspect of this welding process. The intensity and color of the flame are directly influenced by the flow rates of oxygen and fuel (acetylene or propylene) used in the cutting process. This relationship is fundamental to understanding the oxy-fuel cutting technique and its applications.
When oxy-fuel cutting, the flame color can vary significantly, ranging from a bright, blue-white flame to a more subdued, yellow-orange flame. The key factor determining this color variation is the ratio of oxygen to fuel in the gas mixture. A higher concentration of oxygen in the mixture will result in a brighter, more intense blue flame, while a lower oxygen concentration will produce a less brilliant, yellow-orange flame. This color change is a visual indicator of the combustion process and the efficiency of the cutting operation.
The intensity of the flame is also closely tied to the flow rates of the gases. Increasing the flow rate of oxygen will enhance the flame's brightness and heat, making it more suitable for cutting thicker materials. Conversely, reducing the oxygen flow rate will result in a less intense flame, which is often preferred for delicate or intricate cutting tasks. Similarly, adjusting the fuel flow rate allows for control over the flame's temperature and, consequently, the cutting speed and quality.
In oxy-fuel cutting, the color of the flame provides valuable feedback to the operator. A bright, blue-white flame indicates a balanced and efficient combustion process, ensuring optimal cutting performance. On the other hand, a yellow or orange flame may suggest an imbalance, with too much fuel and insufficient oxygen, leading to poor cutting quality and potential safety hazards. Therefore, precise control over oxygen and fuel flow rates is essential to achieving the desired flame color and, ultimately, the best cutting results.
Understanding the relationship between gas color intensity and flow rates is crucial for operators to fine-tune their oxy-fuel cutting processes. By adjusting these parameters, they can optimize the flame's characteristics, ensuring clean, precise cuts and efficient material removal. This knowledge also contributes to the safety and effectiveness of oxy-fuel cutting, making it a valuable skill for welders and fabricators.
Fuel Injector Line Maintenance: Is Cleaning Necessary?
You may want to see also
Flame color variations: affect cutting quality and material compatibility
The color of the flame in an oxy-fuel cutting process is a critical factor that significantly influences the quality of the cut and the compatibility of the materials being processed. This phenomenon is primarily due to the unique combustion characteristics of oxygen and fuel gases, which produce distinct flame colors and behaviors. Understanding these flame color variations is essential for operators to optimize their cutting processes and achieve the desired results.
In oxy-fuel cutting, the flame is typically a result of the combustion of acetylene or propylene as the fuel gas with oxygen. The color of the flame can range from a bright, blue-white to a more subdued yellow or orange, depending on the fuel-to-oxygen ratio and the flow rates of the gases. A blue-white flame is generally associated with a rich fuel-to-oxygen mixture, indicating that the flame is slightly fuel-rich. This type of flame is often used for cutting thicker materials and provides a more stable and controlled cutting action. On the other hand, a yellow or orange flame is produced when the mixture is more oxygen-rich, resulting in a more efficient combustion process. This flame color is suitable for thinner materials and offers a faster cutting speed.
The variation in flame color directly impacts the cutting quality. A blue-white flame provides a more precise and controlled cut, especially when dealing with delicate or intricate shapes. It allows for better edge definition and minimizes the risk of heat-affected zones, which can weaken the material. In contrast, a yellow or orange flame, while faster, may result in less precise cuts and can lead to more significant heat-affected zones, particularly on harder materials. The heat-affected zone is the area around the cut where the material has been exposed to elevated temperatures, potentially causing changes in its microstructure and properties.
Moreover, flame color variations play a crucial role in material compatibility. Different materials have varying sensitivities to heat and may react differently to the heat generated by the oxy-fuel flame. For instance, aluminum and magnesium alloys, which are commonly used in the aerospace industry, can undergo significant oxidation when exposed to high temperatures, leading to a loss of material strength. A blue-white flame, with its lower temperature, can help minimize this oxidation, ensuring better material compatibility. In contrast, a yellow or orange flame, while faster, may cause more rapid oxidation, making it less suitable for these materials.
In summary, the color of the flame in oxy-fuel cutting is a critical consideration for operators. Flame color variations directly impact cutting quality, with blue-white flames offering more precise cuts and yellow or orange flames providing faster cutting speeds. Additionally, understanding these flame color differences is essential for material compatibility, as it helps operators select the appropriate flame settings to minimize heat-related damage to the materials being processed. By optimizing flame color and gas flow rates, operators can achieve high-quality cuts while maintaining the integrity of the materials.
Unraveling the Mystery: Why Air Bubbles Form in Furnace Fuel Lines
You may want to see also
Safety precautions: wear protective gear to avoid burns from hot gas
When engaging in oxy-fuel cutting, it's crucial to prioritize safety to prevent accidents and injuries. One of the primary concerns is the intense heat generated by the cutting process, which can reach extremely high temperatures. This heat can cause severe burns if proper precautions are not taken.
To mitigate this risk, it is essential to wear appropriate protective gear. The most critical item is a heat-resistant jacket or apron made from materials like fire-resistant cotton or specialized fabrics designed to withstand high temperatures. These garments act as a barrier between your skin and the hot gas, preventing direct contact and potential burns. Ensure that the protective gear fits well and covers all exposed areas, including the arms, legs, and back.
Additionally, wearing heat-resistant gloves is highly recommended. These gloves should be made from materials that can withstand the extreme heat generated during oxy-fuel cutting. They provide insulation and protect your hands from any accidental splashes or contact with the hot gas. It is also advisable to wear closed-toe shoes to protect your feet from any falling debris or potential burns.
Furthermore, consider the use of safety goggles or a face shield to protect your eyes from sparks, flying debris, and the intense light produced during the cutting process. These eye protections are crucial to prevent eye injuries, which can be permanent if not treated promptly. Remember, the goal is to create a safe working environment by minimizing the risk of burns and other injuries associated with the high temperatures generated during oxy-fuel cutting.
In summary, when performing oxy-fuel cutting, always prioritize safety by wearing the appropriate protective gear. This includes heat-resistant clothing, gloves, and eye protection to safeguard against burns and other potential hazards. By taking these precautions, you can ensure a safer working environment and minimize the risk of accidents.
Unraveling the Mystery: Why Motorcycles Pop Pinholes in Fuel Lines
You may want to see also
Gas color control: adjust oxygen and fuel to achieve desired flame color
The color of the flame in oxy-fuel cutting is a critical aspect of the process, as it directly influences the quality and efficiency of the cut. The flame color is primarily determined by the ratio of oxygen to fuel, which can be adjusted to achieve the desired outcome. When using an oxy-fuel cutting torch, the flame is typically blue, indicating a precise and controlled environment. This blue flame is the result of a balanced mixture of oxygen and fuel, which creates a stable and efficient combustion process.
To control the flame color, one must understand the role of oxygen and fuel. Oxygen, when introduced in excess, tends to create a more intense, brilliant blue flame. This is because a higher concentration of oxygen in the mixture increases the combustion temperature, leading to a brighter and whiter flame. Conversely, reducing the oxygen flow will result in a more subdued flame color, often leaning towards yellow or orange. These colors indicate a lower combustion temperature and a less efficient cut.
The fuel, usually acetylene or propylene, plays a complementary role in this process. Acetylene, for instance, produces a bright blue flame when combined with a sufficient amount of oxygen. Propylene, on the other hand, may result in a slightly different flame color, often with a hint of yellow or orange, depending on the specific application and the cutting parameters. Adjusting the fuel flow can also influence the flame's intensity and color, providing further control over the cutting process.
Achieving the desired flame color is essential for optimal cutting performance. A blue flame is generally associated with a clean and precise cut, especially in delicate or intricate work. It ensures that the heat is concentrated at the tip of the torch, allowing for a smooth and accurate cut. However, in some cases, a yellow or orange flame might be preferred for specific applications, such as when cutting thicker materials or when a more aggressive cut is required.
In summary, gas color control in oxy-fuel cutting is a precise art, where the balance of oxygen and fuel determines the flame's color and, consequently, the quality of the cut. By understanding and manipulating these variables, operators can achieve the desired flame color, ensuring efficient and effective cutting operations. This level of control is a testament to the versatility and precision of oxy-fuel cutting technology.
Unveiling the Mystery: Small Lines Behind Fuel Filter in Cadillac SRX
You may want to see also
Frequently asked questions
The oxygen line in an oxy-fuel cutting process is typically blue. This is because the oxygen gas, when ignited, produces a distinct blue flame due to the presence of nitrogen in the air.
The blue color is a result of the combustion process and the chemical reaction between oxygen and nitrogen in the air. When oxygen is supplied at high pressure, it creates a blue flame, which is a common visual indicator in oxy-fuel cutting applications.
Yes, the color can vary depending on several factors. The flame color can range from a bright blue to a darker shade, and it may also appear slightly yellow or orange at certain angles or in specific conditions. The intensity of the flame can also influence the perceived color.
The color of the oxygen line is an essential visual cue for operators. A bright blue flame indicates that the oxygen is being supplied correctly and the cutting parameters are optimized. Any deviation from the expected blue color may suggest issues with the oxygen supply, flame stability, or the overall cutting setup, requiring adjustments to ensure efficient and precise cutting.