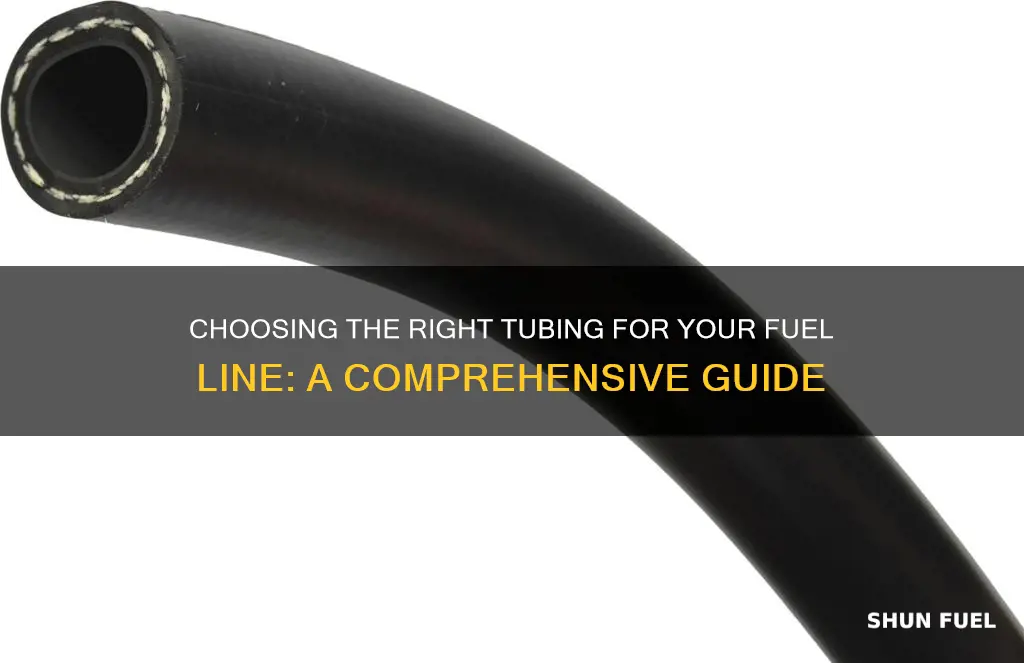
When it comes to choosing the right tubing for a fuel line, there are several factors to consider. The type of tubing you select will depend on the specific requirements of your fuel line, including the pressure and temperature of the fuel, the length of the line, and the compatibility with the fuel itself. Common materials used for fuel lines include steel, aluminum, and various types of plastic, each with its own advantages and disadvantages. In this guide, we will explore the different types of tubing available and help you make an informed decision to ensure the safety and efficiency of your fuel system.
What You'll Learn
- Fuel Line Material: Consider factors like temperature resistance and flexibility
- Diameter and Flow Rate: Choose tubing diameter based on fuel flow rate
- Compatibility: Ensure tubing is compatible with fuel type and vehicle system
- Length and Routing: Determine tubing length and routing for optimal installation
- Cost and Availability: Evaluate cost and availability of tubing options
Fuel Line Material: Consider factors like temperature resistance and flexibility
When it comes to choosing the right tubing for a fuel line, temperature resistance and flexibility are two critical factors that should be at the top of your list. These properties ensure the longevity and reliability of your fuel system, especially in demanding environments.
Temperature resistance is essential because fuel lines are exposed to varying temperatures, especially in automotive applications. The fuel lines need to withstand extreme cold, which can cause the fuel to thicken and flow poorly, as well as high temperatures, which can lead to fuel degradation and potential engine issues. For this reason, you should opt for materials that can handle a wide temperature range without compromising their structural integrity. Common materials like rubber, silicone, and certain types of plastic offer good temperature resistance, ensuring that the fuel lines remain flexible and functional under all conditions.
Flexibility is another crucial aspect, as fuel lines need to accommodate various movements and vibrations without breaking or becoming brittle. The tubing should be able to bend and twist without kinking or cracking, especially in areas with limited space or where the fuel lines are subject to mechanical stress. Materials like rubber and silicone are known for their inherent flexibility, making them ideal for fuel lines. These materials can absorb vibrations and reduce the risk of fuel leaks, ensuring a smooth and efficient fuel supply to the engine.
In addition to temperature and flexibility, consider the chemical resistance of the tubing material. Fuel lines should be able to resist the corrosive effects of gasoline, diesel, and other fuels to prevent degradation and ensure a long service life. Materials like stainless steel, brass, and certain types of plastic offer excellent chemical resistance, making them suitable for fuel line applications.
Lastly, the choice of tubing material should also consider factors like cost, availability, and ease of installation. Some materials may be more expensive but offer superior performance, while others might be more readily available and easier to install. It's important to balance these considerations with the specific requirements of your fuel system to make an informed decision.
Mastering the Art of Fuel Line Wrenching: A Comprehensive Guide
You may want to see also
Diameter and Flow Rate: Choose tubing diameter based on fuel flow rate
When selecting the appropriate tubing for a fuel line, one of the most critical factors to consider is the diameter of the tubing, which is directly related to the flow rate of the fuel. The flow rate, measured in gallons per minute (GPM) or liters per minute (LPM), determines the volume of fuel that needs to be transported through the line. This is a crucial consideration because it directly impacts the performance and efficiency of the fuel system.
The relationship between tubing diameter and flow rate is governed by the principles of fluid dynamics. As the diameter of the tubing increases, the cross-sectional area available for fuel flow also increases. This, in turn, allows for a higher flow rate, as more fuel can pass through the line at any given time. For example, a larger diameter tubing can handle a greater volume of fuel, ensuring that the engine receives the required amount of fuel for optimal performance, especially during high-load conditions.
To determine the appropriate diameter, one must consider the expected fuel flow rate in the system. This can be calculated by analyzing the engine's power output, fuel consumption rates, and the desired performance levels. For instance, a high-performance engine with a powerful fuel injection system will require a larger diameter tubing to accommodate the increased fuel flow rate, ensuring that the engine receives the necessary fuel for efficient operation.
It is essential to strike a balance between tubing diameter and material thickness. While a larger diameter tubing can handle higher flow rates, it may also increase the overall weight and cost of the system. Thicker walls can provide structural integrity but may restrict flow due to increased resistance. Therefore, engineers must carefully select the diameter and wall thickness to optimize flow rate, minimize pressure drops, and ensure the tubing can withstand the fuel's properties and system pressures.
In summary, when choosing the diameter of tubing for a fuel line, it is imperative to prioritize the flow rate to ensure the engine receives the required fuel for optimal performance. This involves considering the engine's specifications, fuel consumption rates, and the desired performance levels. By selecting the appropriate diameter, engineers can create a fuel system that operates efficiently, delivering the right amount of fuel to the engine at the right time.
Understanding the Role of the Diesel Fuel Return Line
You may want to see also
Compatibility: Ensure tubing is compatible with fuel type and vehicle system
When it comes to choosing the right tubing for a fuel line, compatibility is a critical factor that cannot be overlooked. The tubing must be compatible with the specific fuel type and the vehicle's fuel system to ensure optimal performance and safety. Here's a detailed guide on how to ensure compatibility:
Understand Fuel Types: Different fuels have distinct properties and requirements. For instance, gasoline and diesel have different octane levels, viscosities, and chemical compositions. Ethanol-blended fuels, such as E85, also require specific handling due to their higher alcohol content. Understanding the fuel type your vehicle uses is essential. Research the fuel's characteristics and any specific recommendations provided by the manufacturer. This knowledge will guide your tubing selection.
Consider Vehicle System Compatibility: The vehicle's fuel system design plays a significant role in tubing compatibility. Modern vehicles often have intricate fuel injection systems or electronic fuel pumps. These systems may require specific tubing materials and sizes to ensure efficient and reliable fuel delivery. Check the vehicle's manual or consult with automotive experts to identify the recommended tubing specifications for your particular make and model.
Material Selection: Tubing materials are a key aspect of compatibility. Common materials used for fuel lines include rubber, vinyl, and various types of plastic, such as PVC or polyurethane. Each material has its advantages and limitations. For example, rubber tubing is flexible and resistant to fuel degradation, but it may not be suitable for high-pressure systems. Vinyl tubing is cost-effective but less durable. Plastic tubing offers excellent chemical resistance and is often used in high-performance applications. Choose a material that aligns with the fuel type, vehicle system requirements, and environmental conditions.
Size and Diameter: The tubing's size and diameter are crucial for compatibility. Ensure that the tubing's inner diameter matches the fuel line's requirements to maintain optimal fuel flow. Smaller diameters may lead to reduced flow rates and potential pressure drops, while larger diameters can cause excessive fuel sloshing and noise. Refer to the vehicle's specifications or consult experts to determine the appropriate tubing size for your fuel line.
Testing and Verification: After selecting the tubing, it is essential to verify its compatibility through testing. This may involve pressure testing to ensure the tubing can withstand fuel system pressures and checking for any leaks. Additionally, consider the environmental conditions your vehicle will operate in. Extreme temperatures or exposure to sunlight can affect tubing performance. Choose materials that can withstand these conditions without compromising compatibility.
Choosing the Right Fuel Line: Size Matters!
You may want to see also
Length and Routing: Determine tubing length and routing for optimal installation
When it comes to installing a fuel line, determining the appropriate tubing length and routing is crucial for a safe and efficient system. The length of the tubing should be carefully calculated to ensure it can accommodate the fuel flow requirements without any unnecessary excess. A common rule of thumb is to allow for a slight overhang at each end of the line to facilitate easy connections and bends. This extra length can be calculated based on the diameter of the tubing and the desired bend radius, ensuring that the tubing can make the necessary turns without kinking or causing excessive stress on the material.
Routing the fuel line is an essential step to prevent potential hazards. The path should be carefully planned to avoid sharp bends or tight turns that could lead to kinking, which may result in fuel leaks or system failures. It is recommended to use a straight line as much as possible and to maintain a consistent diameter throughout the route. Consider the vehicle's structure and available space; the tubing should be routed away from hot surfaces, sharp edges, and moving parts to prevent damage and ensure longevity. Proper routing also includes avoiding areas where the line could be easily accessed or tampered with, especially in high-traffic areas.
For optimal installation, it is beneficial to use a tubing calculator or software that can provide precise measurements based on the specific fuel line requirements. These tools take into account factors such as the fuel flow rate, desired pressure, and the type of tubing material. By inputting these details, you can determine the exact length needed and the optimal routing path, ensuring a well-designed and safe fuel system. Additionally, considering the vehicle's layout and any existing plumbing or wiring can help in making informed decisions about the tubing's placement.
In some cases, flexible fuel lines might be preferred due to their ability to conform to various shapes and sizes. These lines are often made of materials like rubber or silicone, offering flexibility and durability. When using flexible tubing, it is essential to still plan the routing carefully, ensuring it can withstand the vehicle's movements and potential impacts. Proper support and securement methods should be employed to maintain the line's integrity.
In summary, determining the tubing length and routing is a critical aspect of fuel line installation. It requires careful consideration of the fuel flow, vehicle structure, and potential hazards. By following these guidelines and utilizing appropriate tools, you can ensure a well-installed fuel system that meets safety standards and provides efficient fuel delivery. Remember, proper planning and attention to detail will contribute to a reliable and long-lasting fuel line setup.
Understanding Fuel Injection Lines: A Comprehensive Guide
You may want to see also
Cost and Availability: Evaluate cost and availability of tubing options
When considering the appropriate tubing for a fuel line, it's essential to evaluate the cost and availability of different options to ensure you make an informed decision. The choice of tubing can significantly impact the overall performance and longevity of your fuel system. Here's a detailed breakdown of how to approach this aspect:
Research and Comparison: Begin by researching various types of tubing commonly used for fuel lines. This includes materials like steel, aluminum, and various plastics such as PVC, polypropylene, or fuel-grade rubber. Each material has its own advantages and disadvantages in terms of cost and availability. For instance, steel tubing is known for its durability but can be more expensive and less flexible. On the other hand, aluminum offers good corrosion resistance but may be less readily available compared to other materials. Understanding these variations will help you narrow down your choices.
Cost Analysis: Evaluate the cost of each tubing option. The price can vary depending on the material, thickness, and length required. For example, steel tubing might be more expensive upfront but could offer long-term savings due to its durability. In contrast, some plastic options, like PVC, are generally more affordable and widely available, making them a cost-effective choice for many applications. Consider the total cost, including any additional components like fittings and connectors, to get a comprehensive understanding of the financial implications.
Supplier and Market Availability: Assess the availability of the chosen tubing materials in the market. Some materials might be readily available from local suppliers or hardware stores, ensuring quick procurement and minimizing project delays. Others may require special ordering or sourcing from specialized suppliers, which could impact the timeline. Additionally, consider the lead time for ordering, especially if you're working on a tight schedule. Local suppliers often provide better accessibility and faster delivery, while online retailers might offer a wider range of options.
Long-Term Considerations: While initial cost is essential, it's also crucial to consider the long-term availability and maintenance requirements. Some tubing materials might be more susceptible to corrosion or degradation over time, leading to increased maintenance costs. Evaluate the expected lifespan of the fuel line and choose tubing that can withstand the operating conditions. This ensures that your investment in the tubing is justified and provides a reliable solution for your fuel line needs.
By carefully evaluating the cost and availability of different tubing options, you can make an informed decision that balances initial expenses with long-term performance and reliability. This approach ensures that your fuel line is equipped with the right tubing to handle the specific demands of your application.
Clogged Fuel Return Line: Engine Performance and Safety Risks
You may want to see also
Frequently asked questions
The most common type of tubing for fuel lines is fuel-grade rubber tubing, often made from materials like natural or synthetic rubber. This type of tubing is designed to withstand the corrosive nature of fuel and the varying temperatures it may encounter.
While PVC (polyvinyl chloride) tubing is commonly used for various plumbing and electrical applications, it is not ideal for fuel lines. PVC is not flexible enough to accommodate the movement of the fuel line and can become brittle over time, leading to potential cracks and fuel leaks.
The diameter of the tubing depends on several factors, including the volume of fuel your vehicle requires, the length of the line, and the pressure it needs to withstand. It's essential to consult your vehicle's manual or a professional mechanic to determine the appropriate diameter for your specific fuel line.
Different fuels have varying chemical compositions, and some materials may react with certain fuels, leading to degradation or contamination. For example, some rubber materials may not be suitable for fuels containing ethanol, as ethanol can dissolve the rubber over time. Always check the compatibility of the tubing material with your fuel type.
Yes, proper installation is crucial to ensure the safety and reliability of your fuel system. Fuel line tubing should be routed away from heat sources, sharp edges, and vibration-prone areas. It's recommended to use fuel-line clips or ties to secure the tubing and prevent damage or leaks. Additionally, ensure that all connections are tightened securely and sealed properly to maintain a leak-free system.