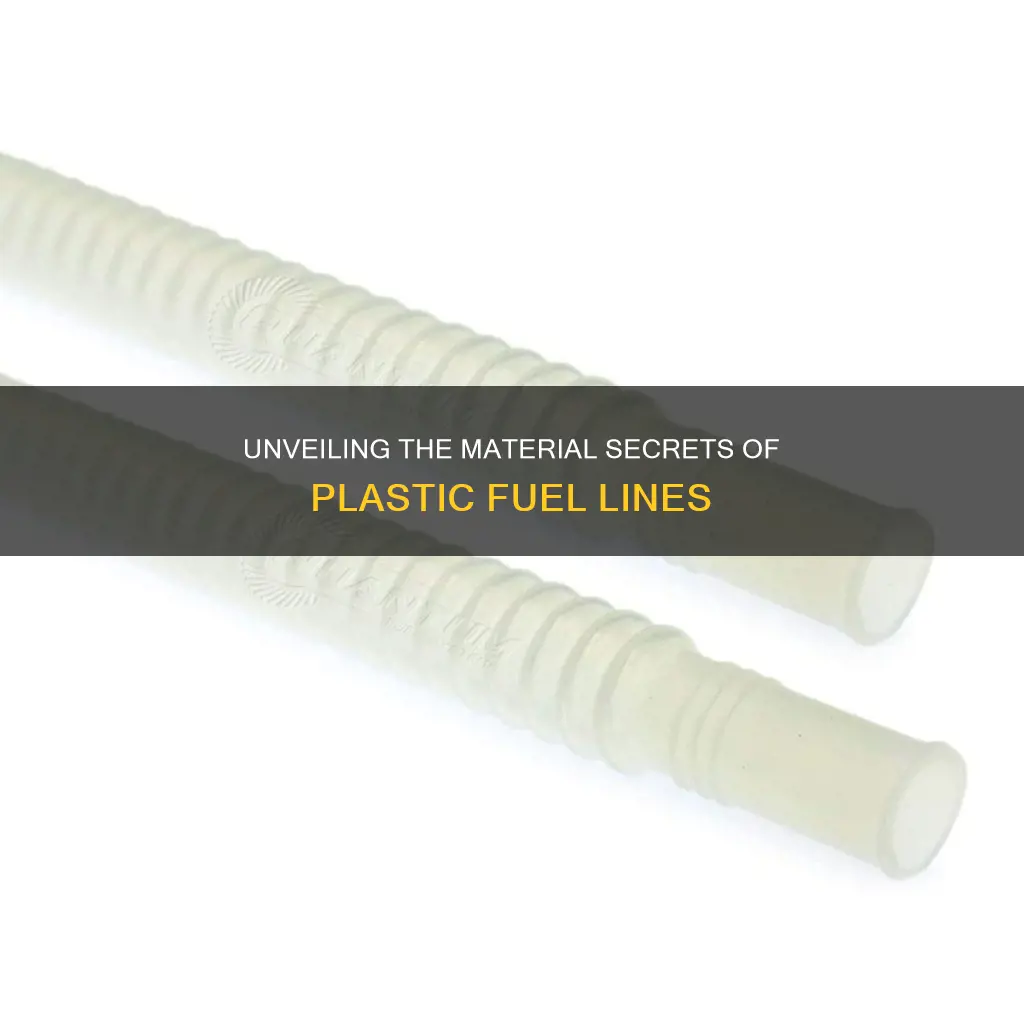
Plastic fuel lines, also known as fuel hoses, are an essential component in the fuel delivery system of vehicles. These lines are typically made from a variety of materials, including rubber, plastic, or a composite blend. The choice of material depends on factors such as the operating temperature, pressure, and chemical resistance required. Common materials used for plastic fuel lines include polyvinyl chloride (PVC), polyetheretherketone (PEEK), and nylon, each offering different levels of durability and flexibility. Understanding the composition of these fuel lines is crucial for ensuring their compatibility with the vehicle's fuel system and overall performance.
What You'll Learn
- Plastic fuel lines are typically made from materials like polyvinyl chloride (PVC) or polyethylene (PE)
- These materials are chosen for their durability, flexibility, and resistance to fuel degradation
- The production process involves extrusion and molding to create the desired shape and size
- Common additives include stabilizers to enhance longevity and prevent UV degradation
- Plastic fuel lines are often used in automotive applications due to their cost-effectiveness and ease of installation
Plastic fuel lines are typically made from materials like polyvinyl chloride (PVC) or polyethylene (PE)
Plastic fuel lines are an essential component in the automotive industry, serving as a critical link between the fuel tank and the engine. These lines are designed to transmit fuel efficiently while ensuring safety and reliability. The choice of material for these lines is crucial, as it directly impacts their performance, durability, and overall safety.
The primary materials used for manufacturing plastic fuel lines are polyvinyl chloride (PVC) and polyethylene (PE). Both materials offer unique advantages and are chosen based on the specific requirements of the application. PVC, a versatile and widely used plastic, is known for its excellent chemical resistance and durability. It can withstand the corrosive effects of fuels and oils, making it an ideal choice for fuel lines. PVC fuel lines are often preferred for their ability to resist cracking and aging, ensuring a long-lasting and reliable performance.
On the other hand, polyethylene (PE) is another popular choice for fuel line construction. PE is known for its flexibility and impact resistance, making it highly suitable for applications where flexibility is essential. It can accommodate slight movements and vibrations without compromising the integrity of the fuel line. PE fuel lines are often used in high-temperature environments, as they can withstand the heat generated by the engine without becoming brittle.
The choice between PVC and PE often depends on the specific needs of the vehicle and the fuel system. For instance, in high-performance engines or applications where temperature variations are significant, PE fuel lines might be preferred due to their flexibility and heat resistance. Conversely, in applications requiring maximum chemical resistance and durability, PVC fuel lines could be the better option.
In summary, plastic fuel lines are engineered to meet the demanding requirements of fuel transmission in vehicles. The materials used, such as PVC and PE, are carefully selected for their unique properties, ensuring that the fuel lines can withstand the harsh conditions of the engine compartment while providing reliable performance. Understanding the composition of these fuel lines is essential for maintaining the overall health and safety of a vehicle's fuel system.
Optimizing Performance: Choosing the Right Fuel Line for Your Waverunner
You may want to see also
These materials are chosen for their durability, flexibility, and resistance to fuel degradation
The choice of materials for plastic fuel lines is a critical aspect of automotive engineering, ensuring the safe and efficient delivery of fuel to an engine. The primary reason for selecting specific materials is to achieve a balance of durability, flexibility, and resistance to fuel degradation. These properties are essential to ensure the longevity and reliability of the fuel system, especially in the harsh environment of an engine compartment.
Durability is a key factor as fuel lines are exposed to various mechanical stresses, including vibrations, temperature fluctuations, and the constant movement of the vehicle. Materials that can withstand these conditions without cracking, breaking, or deteriorating over time are preferred. Common durable materials include high-density polyethylene (HDPE) and polypropylene, which have excellent impact resistance and can handle the rigors of everyday use. These plastics are known for their ability to retain their structural integrity even when subjected to extreme temperatures, making them ideal for fuel lines that must operate reliably in a wide range of climates.
Flexibility is another crucial attribute, as fuel lines need to accommodate the natural movement of the vehicle during operation. Rigid materials can lead to excessive stress on the fuel system, potentially causing leaks or damage over time. Materials like HDPE and polyetheretherketone (PEEK) offer the necessary flexibility to bend and twist without compromising strength. This flexibility is particularly important in areas where the fuel lines must navigate around engine components, providing a smooth and continuous path for fuel flow.
Resistance to fuel degradation is a unique challenge in fuel line design. Fuel contains various additives and can vary in composition, leading to potential degradation of the fuel line material over time. Materials that can resist this degradation ensure the long-term performance and safety of the fuel system. For instance, some plastics are formulated with additives that enhance their resistance to fuel-related chemicals, preventing swelling, softening, or disintegration. This resistance is vital to maintaining the structural integrity of the fuel lines and preventing fuel leaks, which could lead to engine misfires, reduced performance, or even dangerous situations.
In summary, the materials used in plastic fuel lines are carefully selected to meet the demanding requirements of automotive applications. By combining durability, flexibility, and resistance to fuel degradation, engineers can ensure that fuel lines provide a reliable and safe fuel supply to the engine. These materials play a critical role in maintaining the overall performance and longevity of the vehicle, contributing to a smooth and efficient driving experience.
Nylon Fuel Line Cleaning: Effective Methods and Tools
You may want to see also
The production process involves extrusion and molding to create the desired shape and size
The production of plastic fuel lines is a precise and intricate process that involves several key steps to ensure the final product meets the required specifications. One of the primary methods used in manufacturing these lines is extrusion, which is a process of pushing or drawing materials through a die or a small opening to create a continuous shape. In the context of fuel lines, the material, typically a type of plastic known as polyether ether ketone (PEEK) or a similar high-performance polymer, is heated and softened to a malleable state. This heated material is then forced through an extrusion die, which gives the fuel line its specific shape and size. The die is designed to create a seamless, smooth interior surface to ensure optimal fluid flow and prevent any potential leaks.
After the extrusion process, the fuel lines are often subjected to additional treatments to enhance their performance and durability. This can include cooling the lines to set the plastic's shape and hardness, a process known as 'curing'. Curing ensures that the material retains its structural integrity and can withstand the pressures and temperatures encountered in an engine environment. The lines are then inspected to verify their dimensions and overall quality.
Molding is another crucial step in the production process, especially when creating complex shapes or adding specific features to the fuel lines. This process involves placing the extruded material into a mold, which is a cavity or form that gives the desired shape. The mold can be made from various materials, but it is often designed with a release agent to ensure the plastic can be easily removed once cured. The molding process can be carried out through different methods, such as injection molding, which involves injecting the heated plastic into the mold under high pressure, or compression molding, where the material is compressed and heated within the mold.
In the case of fuel lines, molding can be used to create specific fittings, bends, or adapters that are essential for connecting the lines to the fuel tank, engine, and other components. This step allows for the customization of the fuel lines to fit various vehicle models and engine configurations. The molding process ensures that the final product has the required flexibility, strength, and resistance to chemicals and heat, making it suitable for its intended purpose.
The combination of extrusion and molding techniques allows manufacturers to produce plastic fuel lines that are not only lightweight and cost-effective but also highly reliable and efficient. These processes enable the creation of fuel lines with precise dimensions, ensuring a perfect fit and seamless integration into the vehicle's fuel system. Additionally, the ability to customize the shape and size through molding is crucial for accommodating different vehicle architectures and fuel system designs.
Fuel Pump Upgrade: Big Line Solutions for Your Chevy Yukon
You may want to see also
Common additives include stabilizers to enhance longevity and prevent UV degradation
Plastic fuel lines are an essential component in modern vehicles, responsible for transporting fuel from the tank to the engine. These lines are typically made from a variety of plastic materials, each chosen for its unique properties and ability to withstand the demanding conditions of an engine bay. One of the key considerations in the manufacturing of these lines is the inclusion of various additives, which play a crucial role in enhancing their performance and durability.
Stabilizers are among the most common additives used in plastic fuel lines. These additives are designed to improve the material's longevity and ensure its stability over time. The primary function of stabilizers is to prevent the degradation of the plastic caused by exposure to ultraviolet (UV) light from the sun. UV degradation can lead to a decrease in the material's strength and flexibility, making it more susceptible to cracking and failure. By incorporating stabilizers, manufacturers can ensure that the fuel lines remain intact and functional even when exposed to direct sunlight for extended periods.
The process of stabilizing plastic fuel lines involves a careful selection of specific chemicals that interact with the polymer chains. These additives create a protective barrier around the polymer, preventing it from breaking down under the influence of UV radiation. This is particularly important in outdoor applications where fuel lines are exposed to the elements. Over time, without stabilizers, the plastic can become brittle and crack, leading to fuel leaks and potential engine damage.
In addition to stabilizers, other additives such as antioxidants and heat stabilizers are often included to further enhance the material's performance. Antioxidants help to prevent oxidation, which can cause the plastic to become discolored and lose its structural integrity. Heat stabilizers, on the other hand, ensure that the material remains stable at high temperatures, which is crucial during engine operation. These additives work in conjunction with the base plastic material to create a robust and reliable fuel line system.
The use of these additives in plastic fuel lines is a critical aspect of automotive engineering, ensuring that vehicles can operate efficiently and safely over extended periods. By incorporating stabilizers and other performance-enhancing chemicals, manufacturers can provide a reliable solution for fuel transportation, contributing to the overall reliability and longevity of modern vehicles. Understanding the composition of these lines is essential for both manufacturers and vehicle owners, as it highlights the importance of proper maintenance and the role of these additives in ensuring optimal performance.
Unveiling the Secrets: Red Line Fuel System Explained
You may want to see also
Plastic fuel lines are often used in automotive applications due to their cost-effectiveness and ease of installation
Plastic fuel lines have become a popular choice for automotive applications, offering a range of benefits that make them an attractive option for vehicle manufacturers and enthusiasts alike. One of the primary reasons for their widespread use is their cost-effectiveness. Plastic is generally a more affordable material compared to traditional metal fuel lines, especially when considering the overall cost of the vehicle. This affordability factor allows manufacturers to equip vehicles with fuel lines without significantly increasing the overall price, making it an economically viable choice.
In addition to cost, the ease of installation is another significant advantage of plastic fuel lines. These lines are typically designed with flexibility in mind, allowing them to navigate through the engine compartment with relative ease. This flexibility reduces the time and effort required during the installation process, as technicians can quickly route the lines around various components without the need for extensive maneuvering. The lightweight nature of plastic also contributes to easier handling, making it a convenient choice for automotive assembly lines.
The manufacturing process of plastic fuel lines is efficient and streamlined. Plastic can be easily molded and shaped, allowing for precise customization to fit specific vehicle requirements. This adaptability ensures a perfect fit for various engine configurations, minimizing the risk of leaks and maximizing performance. Moreover, the production process is often faster and more cost-effective compared to metal fuel lines, further enhancing the economic benefits of using plastic.
Despite the advantages, it's important to note that plastic fuel lines may have some limitations. They are generally not as durable as metal lines, especially in extreme conditions. Over time, plastic can degrade due to factors like heat, UV radiation, and chemical exposure. However, modern advancements in plastic composition and additives have significantly improved their resistance to these environmental factors, making them suitable for a wide range of automotive applications.
In summary, plastic fuel lines offer a compelling combination of cost-effectiveness and ease of installation, making them a popular choice in the automotive industry. Their flexibility, lightweight nature, and efficient manufacturing process contribute to their widespread adoption. While there are some considerations regarding durability, ongoing improvements in plastic technology ensure that plastic fuel lines remain a reliable and practical solution for modern vehicles.
Essential Components: Building a Robust Fuel Line System
You may want to see also
Frequently asked questions
Plastic fuel lines are typically made from a type of synthetic material known as polyether ether ketone (PEEK). This material is chosen for its excellent chemical resistance, durability, and ability to withstand high temperatures, making it ideal for fuel line applications.
While PEEK is the most common material, some manufacturers might use a blend of PEEK and other polymers to enhance specific properties. For instance, adding a small amount of glass fiber can increase the material's strength and rigidity.
The PEEK material ensures that the fuel lines can resist the corrosive effects of gasoline, diesel, and other fuels. It also maintains flexibility even in low temperatures, preventing cracks and leaks. Additionally, PEEK has a low coefficient of friction, allowing for smooth fuel flow.
Absolutely! Plastic fuel lines are often preferred in high-performance applications due to their lightweight nature, which can improve a vehicle's overall performance. The material's ability to withstand high pressure and temperature changes also makes it suitable for racing or modified vehicles.
Plastic fuel lines generally require minimal maintenance. However, it's recommended to inspect them regularly for any signs of damage, cracks, or swelling, especially if the vehicle is exposed to extreme weather conditions or harsh chemicals. Proper maintenance ensures the longevity and reliability of the fuel system.