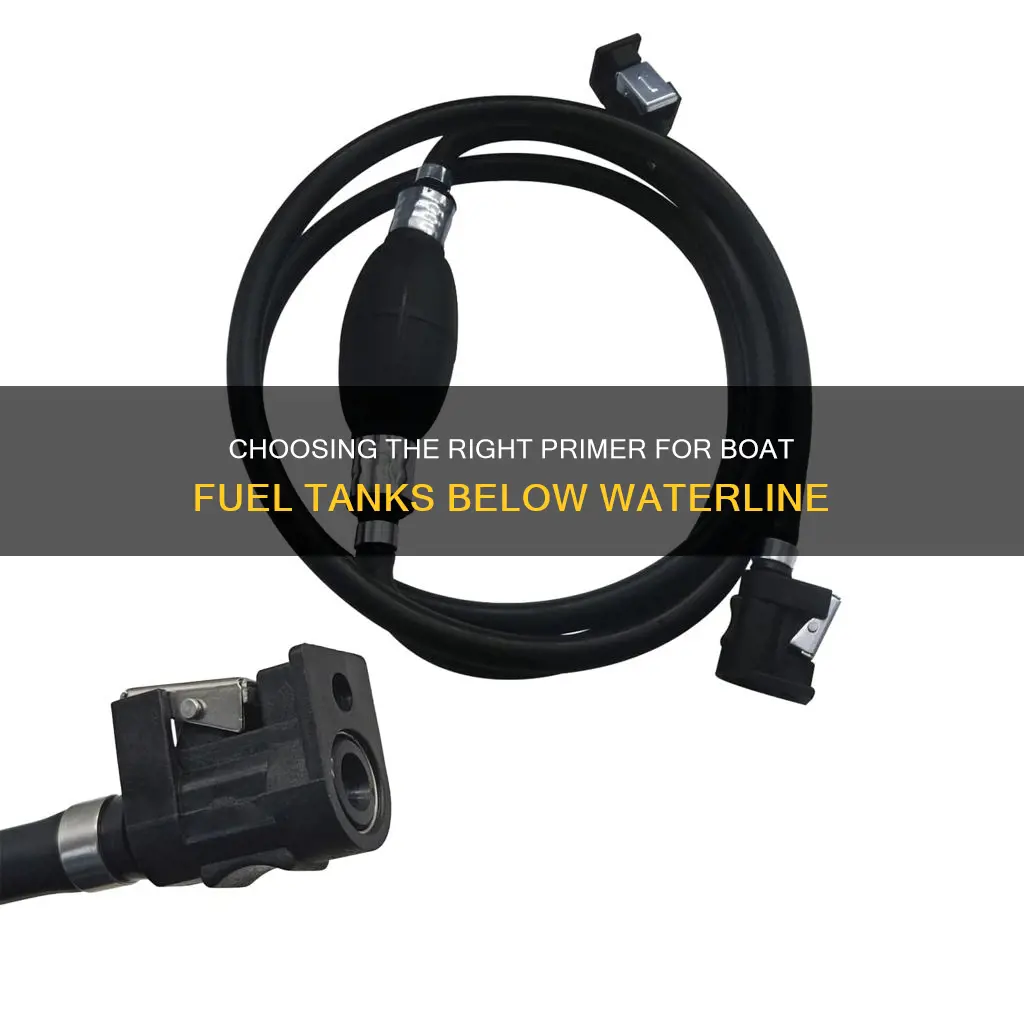
When it comes to maintaining the fuel tanks of boats below the waterline, choosing the right primer is crucial. The primer acts as a protective barrier, preventing corrosion and ensuring the longevity of the fuel system. This introduction aims to explore the various options available for primers specifically designed for boat fuel tanks, considering factors such as compatibility, durability, and environmental impact to help boat owners make informed decisions.
What You'll Learn
- Material Compatibility: Choose primer compatible with tank material (e.g., fiberglass, steel) to prevent corrosion
- Environmental Factors: Consider climate and water conditions to ensure primer durability and protection against corrosion
- Fuel Type: Select primer suitable for the type of fuel stored (e.g., gasoline, diesel) for optimal performance
- Application Method: Primers may be applied by brush, spray, or dip, each with its own advantages
- Regulatory Compliance: Ensure primer meets industry standards and regulations for marine fuel tank priming
Material Compatibility: Choose primer compatible with tank material (e.g., fiberglass, steel) to prevent corrosion
When preparing boat fuel tanks for below-waterline use, material compatibility is a critical factor to ensure the longevity and integrity of the tank. The choice of primer is essential as it forms the initial barrier between the tank material and the fuel, preventing corrosion and ensuring optimal performance.
For fiberglass tanks, a compatible primer is crucial to establish a strong bond and protect the composite structure. Fiberglass primers are specifically designed to adhere to the smooth surface of fiberglass, creating a seamless barrier against the corrosive effects of fuel and seawater. These primers often contain additives that enhance adhesion and provide additional protection against UV rays and chemical degradation. It is essential to choose a primer that is specifically formulated for fiberglass to ensure proper adhesion and long-term effectiveness.
On the other hand, steel tanks require a different approach due to the inherent reactivity of steel with fuel and moisture. Steel primers are formulated to inhibit rust and corrosion, providing a protective layer that safeguards the steel surface. These primers often contain zinc or other corrosion-inhibiting compounds to create a sacrificial layer, protecting the underlying steel. When selecting a primer for steel tanks, it is vital to consider the specific type of steel used and choose a primer that offers the necessary protection against corrosion in a marine environment.
In both cases, proper surface preparation is key. The tank's surface should be clean, smooth, and free of contaminants to ensure optimal primer adhesion. Any existing paint or old primer should be removed to create a fresh, bare surface for the new primer. This process ensures a strong bond and maximizes the primer's ability to prevent corrosion.
Additionally, it is worth noting that some primers are designed to be compatible with multiple materials, offering versatility for boat owners. These multi-purpose primers can be an excellent choice when dealing with tanks made from different materials, ensuring a consistent and effective barrier against corrosion. However, it is always advisable to consult the manufacturer's guidelines and recommendations to ensure the best results.
In summary, material compatibility is a critical aspect when choosing a primer for boat fuel tanks below the waterline. Whether dealing with fiberglass or steel, selecting the appropriate primer that matches the tank material will provide the necessary protection against corrosion, ensuring the fuel tank's longevity and reliability.
Understanding Military-Grade Fuel Lines: Style, Durability, and Performance
You may want to see also
Environmental Factors: Consider climate and water conditions to ensure primer durability and protection against corrosion
When preparing your boat's fuel tanks for the below-waterline environment, environmental factors play a crucial role in selecting the right primer. The durability and effectiveness of the primer are directly influenced by the climate and water conditions your vessel will encounter.
In regions with high humidity and frequent rainfall, it's essential to choose a primer that offers excellent moisture resistance. Look for primers designed to create a protective barrier against water absorption, preventing corrosion and ensuring the longevity of the fuel tank. Primers with a high degree of flexibility and adhesion properties can better withstand the expansion and contraction caused by temperature changes and humidity fluctuations.
For areas with extreme temperatures, whether hot or cold, the primer's ability to maintain its integrity is vital. In hot climates, opt for primers that can resist degradation caused by UV radiation and provide protection against the sun's harsh rays. Conversely, in colder regions, ensure the primer has good heat resistance to prevent cracking or peeling due to freezing temperatures and temperature fluctuations.
The type of water your boat will navigate is another critical consideration. Saltwater environments demand primers with superior corrosion resistance to protect against the electrochemical effects of saltwater. Look for primers containing zinc or other corrosion-inhibiting compounds to create a protective layer on the fuel tank's surface. In freshwater areas, while the risk of corrosion is lower, a primer with good moisture resistance and adhesion properties is still essential to maintain the tank's condition.
Additionally, consider the long-term exposure to sunlight and the potential for algae or marine growth in the water. Primers with UV stabilizers can help prevent fading and degradation over time. Regular maintenance and inspections are also recommended to identify and address any primer issues promptly, ensuring the fuel tank's protection remains effective in all environmental conditions.
Unveiling the Material Mystery: What Fuels Clear Fuel Lines?
You may want to see also
Fuel Type: Select primer suitable for the type of fuel stored (e.g., gasoline, diesel) for optimal performance
When it comes to maintaining the fuel tanks of boats, especially those located below the waterline, selecting the right primer is crucial for optimal performance and longevity. The primer acts as a protective layer, ensuring that the fuel remains stable and does not degrade over time. This is particularly important for boats, as they often operate in harsh marine environments.
For gasoline-powered boats, a suitable primer is one that is specifically designed for this fuel type. Gasoline primers are typically formulated to prevent the formation of harmful deposits and ensure efficient combustion. These primers often contain additives that help clean and protect the fuel system, including the tank and lines. Look for primers that are labeled as 'gasoline-safe' and ensure they meet the standards set by marine industry regulations.
In contrast, diesel fuel requires a different approach. Diesel primers are engineered to handle the unique properties of this fuel, which is generally less volatile than gasoline. These primers often have a higher flash point, ensuring they do not ignite easily, and they may contain antioxidants to prevent oxidation and degradation. It is essential to choose a primer that is compatible with diesel to avoid any potential issues with fuel stability.
The key to successful priming is understanding the specific requirements of the fuel type. For instance, gasoline primers might need to be more aggressive in their cleaning action to remove any contaminants, while diesel primers should focus on stability and long-term protection. Always refer to the manufacturer's guidelines and recommendations for the best results.
Additionally, consider the environmental factors and the specific conditions your boat operates in. Marine environments can be challenging due to saltwater exposure, which may require primers with added corrosion inhibitors. Always opt for primers that are designed for marine applications to ensure they meet the unique demands of boat fuel systems.
Mastering Fuel Injection: Hard Line Strategies for Optimal Performance
You may want to see also
Application Method: Primers may be applied by brush, spray, or dip, each with its own advantages
When it comes to preparing and priming boat fuel tanks, especially those located below the waterline, the choice of application method is crucial for achieving optimal results. The three primary methods for applying primers to these tanks are by brush, spray, or dip, each offering distinct advantages depending on the specific requirements and circumstances.
Brush Application: This traditional method involves using a brush to manually apply the primer to the surface of the fuel tank. It is a precise and controlled approach, allowing for easy coverage of small areas and intricate details. Brush application is ideal for tanks with complex shapes or those requiring a more delicate touch. The brush's ability to navigate tight spaces and provide a smooth, even coat makes it a preferred choice for intricate work. However, it is a time-consuming process and may not be as efficient for larger tanks.
Spray Application: Spraying is a faster and more efficient method, particularly for larger fuel tanks. It involves using an airbrush or a high-pressure spray gun to apply the primer uniformly across the surface. This technique provides excellent coverage and is known for its ability to create a smooth, even finish. Spray primers are often preferred for their speed and convenience, especially when dealing with extensive tank surfaces. The spray method is less likely to leave brush marks or visible strokes, resulting in a more professional appearance. However, it requires some skill to avoid overspray and ensure an even coat.
Dip Application: This method is a more hands-on approach, where the primer is applied by dipping a brush or roller into the primer can and then directly onto the tank surface. Dip application is straightforward and can be very effective for quick coverage. It is particularly useful for tanks with limited access or those that are already partially prepared. The dip method allows for easy control and is less messy compared to spraying. However, it may not provide the same level of coverage as spraying and could require more primer, especially for larger tanks.
Each application method has its own set of benefits, and the choice depends on factors such as the size of the tank, the complexity of the shape, the desired finish, and the available resources. For intricate work, the brush method is ideal, while spraying is efficient for larger areas. Dip application offers a simple and effective solution for quick priming tasks. Understanding these application methods will help ensure a successful and durable primer application for boat fuel tanks below the waterline.
Honda CR-V '98 Fuel Line Cut-Off: Causes and Fixes
You may want to see also
Regulatory Compliance: Ensure primer meets industry standards and regulations for marine fuel tank priming
When it comes to marine fuel tank priming, regulatory compliance is of utmost importance to ensure the safety and efficiency of your boat's fuel system. The primer used for below-waterline fuel tanks must adhere to specific industry standards and regulations to meet the unique challenges of marine environments. These standards are in place to prevent contamination, ensure proper fuel mixing, and maintain the integrity of the fuel system over time.
One of the key regulations to consider is the American Society of Testing and Materials (ASTM) standards, which provide guidelines for fuel system components, including primers. ASTM D4814 is a widely recognized standard that specifies the requirements for marine fuel system components. It ensures that the primer is compatible with the fuel, prevents corrosion, and maintains the fuel's quality. Compliance with ASTM D4814 is essential to guarantee that the primer will not degrade the fuel's performance or contribute to the formation of harmful deposits.
In addition to ASTM standards, marine fuel priming is also governed by regulations set by maritime authorities. For example, the International Maritime Organization (IMO) has established guidelines for the use of primers in marine fuel systems. These regulations often include specific requirements for primer composition, application methods, and performance standards. It is crucial to consult the relevant maritime regulations and ensure that the chosen primer meets or exceeds these standards to avoid potential legal issues and ensure the longevity of your boat's fuel system.
Furthermore, industry best practices and guidelines should be considered when selecting a primer. Many marine fuel system manufacturers provide recommendations or even specify certain primers for their products. Following these guidelines can help ensure compatibility and optimal performance. It is also advisable to choose primers that have been tested and approved by reputable marine testing laboratories to guarantee their effectiveness and compliance with industry standards.
In summary, regulatory compliance is a critical aspect of choosing the right primer for boat fuel tanks below the waterline. Adhering to industry standards such as ASTM D4814 and maritime regulations ensures that the primer is effective, compatible, and safe for marine environments. By selecting a primer that meets these standards, boat owners can maintain the integrity of their fuel system, prevent contamination, and ensure the overall reliability of their vessel's performance on the water.
Understanding Johnson 3HP Fuel Line Sizes: A Comprehensive Guide
You may want to see also
Frequently asked questions
For fuel tanks below the waterline, it is crucial to use a primer specifically designed for marine environments. Look for primers that are compatible with fuel and have excellent adhesion properties. Epoxy-based primers are commonly recommended for this application due to their ability to create a strong bond with the tank surface and provide a durable barrier against corrosion.
Priming the fuel tank is essential to ensure proper adhesion of the paint or coating. It helps to create a smooth surface, remove any contaminants, and provide a suitable base for the final finish. Primer also acts as a barrier, preventing corrosion and protecting the metal surface from the corrosive effects of fuel and moisture.
While general-purpose primers can be used, they may not provide the same level of protection and adhesion as marine-specific primers. Marine environments are harsh, and fuel tanks require a primer that can withstand the corrosive effects of fuel, moisture, and saltwater. Using a dedicated marine primer ensures better long-term performance and protection.
Proper preparation is key to a successful priming process. Start by thoroughly cleaning the tank to remove any dirt, rust, or old paint. Use a wire brush or sandpaper to create a rough surface, ensuring the primer has something to adhere to. Repair any holes or damage and ensure the tank is dry before applying the primer.
Yes, safety is crucial when working with fuel tanks. Always ensure proper ventilation in the work area to avoid inhaling fumes. Wear protective gear, including gloves and a respirator, to minimize contact with chemicals. Follow the manufacturer's instructions for the primer, including any specific application techniques and drying times.