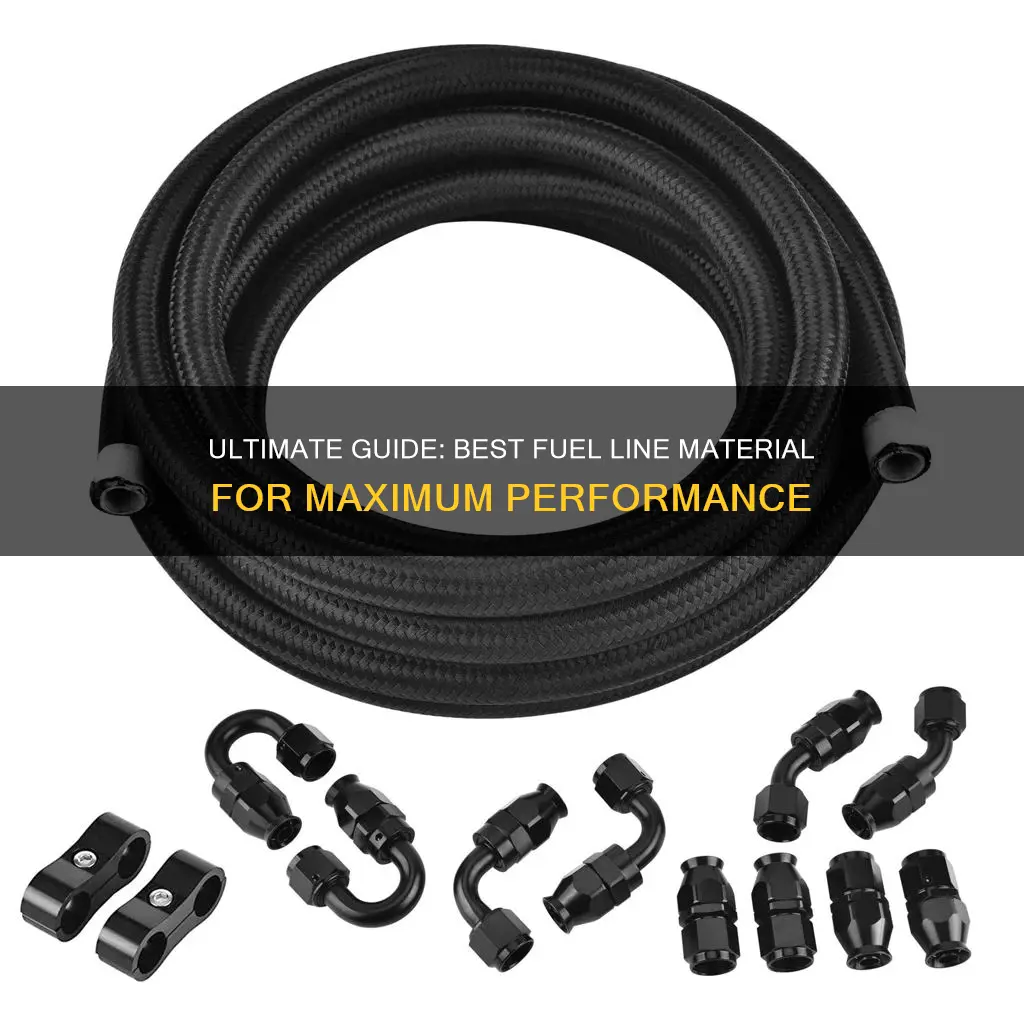
When it comes to choosing the best fuel line material, there are several factors to consider. The ideal material should be durable, flexible, and resistant to fuel degradation. Common options include rubber, silicone, and braided steel. Each material has its advantages and is suited to different applications. Rubber is cost-effective and flexible, making it suitable for most automotive uses. Silicone offers superior heat resistance and flexibility, ideal for high-temperature environments. Braided steel provides excellent durability and kink resistance, often used in high-pressure applications. The choice depends on the specific requirements of the fuel system, including temperature, pressure, and the type of fuel being used.
Characteristics | Values |
---|---|
Flexibility | High flexibility allows for easy installation and routing around engine components. |
Temperature Resistance | Materials like nylon, PVC, and EPDM rubber can withstand high temperatures, ensuring durability in various climates. |
Chemical Resistance | Fuel lines should be resistant to chemicals in fuel, such as ethanol and methanol, to prevent degradation. |
Pressure Rating | A suitable material should have a pressure rating that matches or exceeds the system's requirements to handle fuel pressure effectively. |
Corrosion Resistance | Materials like stainless steel and aluminum are preferred for their ability to resist corrosion from fuel and engine components. |
Cost | The cost of the material can vary, with some materials being more expensive but offering better performance and longevity. |
Availability | Common materials like nylon, PVC, and rubber are widely available, making them easily accessible for repairs and replacements. |
Ease of Installation | Materials that are easy to cut, bend, and install can save time and effort during vehicle maintenance. |
Longevity | High-quality materials with good reinforcement can provide long-lasting performance, reducing the need for frequent replacements. |
Compatibility | The material should be compatible with the fuel type and engine system to ensure optimal performance and safety. |
What You'll Learn
- Durability: Materials like stainless steel and braided stainless steel offer long-lasting performance
- Flexibility: Braided rubber or silicone provides flexibility for engine vibrations
- Temperature Resistance: Materials like nylon or PTFE withstand high temperatures
- Chemical Resistance: Materials like PVDF or FEP resist fuel chemicals
- Cost-Effectiveness: Standard rubber or PVC can be a budget-friendly option
Durability: Materials like stainless steel and braided stainless steel offer long-lasting performance
When it comes to choosing the best fuel line material, durability is a critical factor to consider, especially for those seeking long-lasting performance. In this regard, materials like stainless steel and braided stainless steel stand out as top choices. These materials are renowned for their exceptional strength and resistance to corrosion, making them ideal for withstanding the demanding conditions often encountered in automotive applications.
Stainless steel is a popular choice for fuel lines due to its inherent durability. It is known for its ability to resist oxidation and corrosion, ensuring that the fuel lines remain in excellent condition over an extended period. This material is particularly useful in high-temperature environments, as it can maintain its structural integrity without compromising performance. The inherent strength of stainless steel also makes it less susceptible to damage from fuel contaminants, ensuring a reliable and safe fuel delivery system.
Braided stainless steel takes the durability factor a step further. This material is created by braiding multiple strands of stainless steel together, forming a flexible yet robust structure. The braiding process provides excellent flexibility, allowing the fuel lines to navigate through tight spaces and engine compartments with ease. Despite its flexibility, braided stainless steel maintains its strength and durability, making it an excellent choice for applications where the fuel lines may be subjected to vibrations or extreme temperatures.
The combination of flexibility and strength in braided stainless steel makes it particularly advantageous in high-performance vehicles or those operating in harsh conditions. It can withstand the rigors of daily use, ensuring a consistent and reliable fuel supply. Additionally, the braided design often includes a protective outer layer, further enhancing its resistance to abrasion and external factors that could compromise its integrity.
In summary, when prioritizing durability, stainless steel and braided stainless steel are the go-to materials for fuel lines. Their ability to resist corrosion, maintain structural integrity, and offer flexibility makes them ideal for a wide range of applications, ensuring a long-lasting and reliable fuel delivery system. These materials are a testament to the importance of choosing the right components to ensure the overall performance and longevity of a vehicle's fuel system.
Understanding Fuel Crossovers: A Comprehensive Guide to Efficient Systems
You may want to see also
Flexibility: Braided rubber or silicone provides flexibility for engine vibrations
When it comes to choosing the best fuel line material, flexibility is a crucial factor to consider, especially in the context of engine vibrations. The fuel lines in your vehicle are responsible for transferring fuel from the tank to the engine, and they need to withstand the constant motion and vibrations that occur during operation. This is where the importance of flexibility comes into play.
Braided rubber and silicone are two popular materials known for their exceptional flexibility, making them ideal choices for fuel lines. These materials are designed to accommodate the natural movement and expansion of the engine components, ensuring a secure and reliable connection. Rubber and silicone are both elastic, allowing them to stretch and return to their original shape, which is essential when the engine vibrates or moves. This flexibility helps prevent fuel lines from becoming damaged or disconnected over time, ensuring a consistent and uninterrupted fuel supply.
Braided rubber fuel lines are a common choice due to their durability and flexibility. The rubber provides the necessary elasticity, while the braided design offers additional strength and kink resistance. This combination ensures that the fuel lines can handle the rigors of the engine environment without compromising their integrity. The braiding also helps to distribute the flexibility evenly, reducing the risk of localized wear and tear.
Silicone fuel lines are another excellent option, especially for high-performance or modified vehicles. Silicone is known for its superior flexibility and heat resistance, making it ideal for engines that generate significant heat. It can withstand extreme temperatures, ensuring that the fuel lines remain flexible even in challenging conditions. The flexibility of silicone also contributes to its durability, as it can absorb vibrations without permanent deformation.
In summary, flexibility is a critical aspect of fuel line performance, and braided rubber or silicone materials excel in this regard. Their ability to provide a secure connection while accommodating engine vibrations is essential for maintaining a reliable fuel supply. Whether you opt for rubber or silicone, the flexibility of these materials ensures that your fuel lines will remain intact and functional, even in the harshest of engine environments.
NHRA Fuel Line Routing: Engine Compartment Rules Explained
You may want to see also
Temperature Resistance: Materials like nylon or PTFE withstand high temperatures
When it comes to choosing the best material for fuel lines, temperature resistance is a critical factor to consider. Fuel lines are exposed to varying temperatures, especially in automotive applications, where engines can reach extremely high temperatures. Therefore, the material used for these lines must be able to withstand these harsh conditions without compromising performance or safety.
One of the key materials that excel in temperature resistance is nylon. Nylon is a synthetic polymer known for its excellent thermal stability. It can withstand temperatures ranging from -40°F to 212°F (-40°C to 100°C), making it highly suitable for fuel lines in a wide range of climates and engine operating conditions. Nylon's ability to maintain its structural integrity under high temperatures ensures that the fuel lines remain flexible and resistant to cracking or degradation over time.
Another material that offers exceptional temperature resistance is Polytetrafluoroethylene (PTFE). PTFE, commonly known as Teflon, is renowned for its non-stick properties and excellent thermal stability. It can withstand temperatures up to 500°F (260°C), making it ideal for high-performance applications. PTFE's resistance to heat and chemical corrosion ensures that fuel lines remain reliable and efficient, even in demanding environments.
The use of nylon and PTFE in fuel lines provides several advantages. Firstly, these materials are known for their flexibility, allowing the fuel lines to accommodate engine movement without becoming brittle or rigid. This flexibility is crucial for maintaining a secure and reliable connection between the fuel tank and the engine. Additionally, the temperature resistance of these materials helps prevent fuel leaks and ensures the longevity of the fuel system.
In summary, when selecting the best material for fuel lines, temperature resistance is a vital consideration. Materials like nylon and PTFE offer excellent thermal stability, ensuring that fuel lines can withstand the extreme temperatures encountered in various applications. Their flexibility and resistance to heat and chemical corrosion make them ideal choices for maintaining a reliable and efficient fuel system.
Unraveling the Mystery: Why Fuel Lines Break
You may want to see also
Chemical Resistance: Materials like PVDF or FEP resist fuel chemicals
When it comes to choosing the best material for fuel lines, chemical resistance is a critical factor to consider, especially in the context of automotive and aviation applications. The fuel lines in these industries are exposed to a variety of chemicals, including gasoline, diesel, jet fuel, and various additives, which can lead to degradation and failure over time. To combat this, engineers and manufacturers have turned to specialized materials that offer excellent resistance to these chemicals.
One such material is Polyvinylidene Fluoride (PVDF). PVDF is a synthetic polymer known for its exceptional chemical resistance. It can withstand exposure to a wide range of fuels and chemicals, making it an ideal choice for fuel lines. PVDF's resistance to chemicals is attributed to its unique molecular structure, which prevents the fuel from breaking down the material's polymer chains. This property ensures that the fuel lines remain intact and functional, even when exposed to harsh fuel environments.
Another material gaining popularity for fuel line applications is Fluorinated Ethylene Propylene (FEP). FEP is a fluoropolymer that offers excellent chemical resistance, including resistance to fuels and their derivatives. Its ability to resist chemical degradation makes it suitable for high-performance fuel systems. FEP's smooth surface also reduces the risk of fuel contamination and ensures a consistent flow of fuel, which is crucial for optimal engine performance.
The use of PVDF and FEP in fuel lines provides several advantages. Firstly, these materials significantly extend the lifespan of fuel lines by preventing chemical-induced degradation. This is particularly important in high-temperature and high-pressure environments, where traditional materials might fail. Secondly, their chemical resistance ensures that the fuel remains pure and free from contaminants, which is essential for engine efficiency and longevity.
In summary, when selecting the best material for fuel lines, chemical resistance is a key consideration. Materials like PVDF and FEP offer superior resistance to fuel chemicals, ensuring the durability and reliability of fuel lines in various industries. These materials' ability to withstand harsh fuel environments makes them indispensable in applications where engine performance and safety are paramount.
Understanding the Role of Fuel Line Hoses in the Evaporative Emissions System
You may want to see also
Cost-Effectiveness: Standard rubber or PVC can be a budget-friendly option
When it comes to choosing the best fuel line material, cost-effectiveness is a significant factor to consider, especially for DIY enthusiasts and those on a tight budget. Standard rubber and PVC (polyvinyl chloride) are two popular and affordable options that offer a balance between performance and price. These materials have been used for decades in various applications, including fuel lines, and have proven their reliability over time.
Rubber, in its various forms, is often the go-to choice for fuel lines due to its flexibility and ease of installation. Natural rubber, in particular, is known for its ability to withstand the corrosive effects of gasoline and diesel, making it a suitable long-term solution. It is also relatively inexpensive, which makes it an attractive option for those looking to save costs without compromising too much on quality. Additionally, rubber's flexibility allows it to conform to the shape of the vehicle's frame, ensuring a secure and snug fit.
PVC, on the other hand, offers a more rigid and lightweight alternative to rubber. It is often preferred for its durability and resistance to abrasion, which can be beneficial in certain automotive applications. PVC fuel lines are known for their ability to resist kinking and cracking, ensuring a reliable fuel supply even under demanding conditions. The cost of PVC is generally lower than that of high-quality rubber, making it an excellent choice for budget-conscious individuals without sacrificing performance.
Both rubber and PVC are readily available in hardware stores and automotive shops, making them easily accessible for those in need of a quick and affordable fuel line replacement or upgrade. Their widespread availability further contributes to their cost-effectiveness, as there is no need to search far and wide for specialized materials. Moreover, the simplicity of their installation process means that DIY enthusiasts can tackle the job themselves, potentially saving on labor costs.
In conclusion, for those seeking a cost-effective solution without sacrificing performance, standard rubber or PVC fuel lines are excellent choices. These materials offer a balance between affordability, durability, and ease of use, ensuring that you can get the job done without breaking the bank. With their widespread availability and proven track record, rubber and PVC are reliable options that cater to a variety of fuel line requirements.
Fads' Fuel Line: Unveiling the Secret to Their Success
You may want to see also
Frequently asked questions
The ideal material for fuel lines is typically a high-quality, flexible rubber compound, often referred to as fuel-grade rubber. This material is chosen for its ability to withstand the corrosive nature of gasoline and diesel, ensuring a long-lasting and reliable fuel supply to the engine.
Fuel lines are crucial for delivering fuel from the tank to the engine, and using the right material is essential for several reasons. The material must be compatible with the fuel type to prevent degradation and ensure optimal performance. Additionally, it should be flexible to accommodate engine movement and withstand temperature fluctuations without cracking or leaking.
Yes, some alternative materials are used, especially in high-performance or custom applications. Stainless steel is a popular choice for its durability and resistance to corrosion. It is often used for high-pressure fuel systems or in environments with extreme temperatures. Braided steel or copper fuel lines are also available, offering flexibility and strength.
When replacing or upgrading fuel lines, it's advisable to consult the vehicle's manual or seek professional advice. Original Equipment Manufacturer (OEM) parts are often the best choice, as they are designed specifically for your vehicle. High-quality aftermarket parts from reputable brands can also be a reliable option, ensuring compatibility and performance.