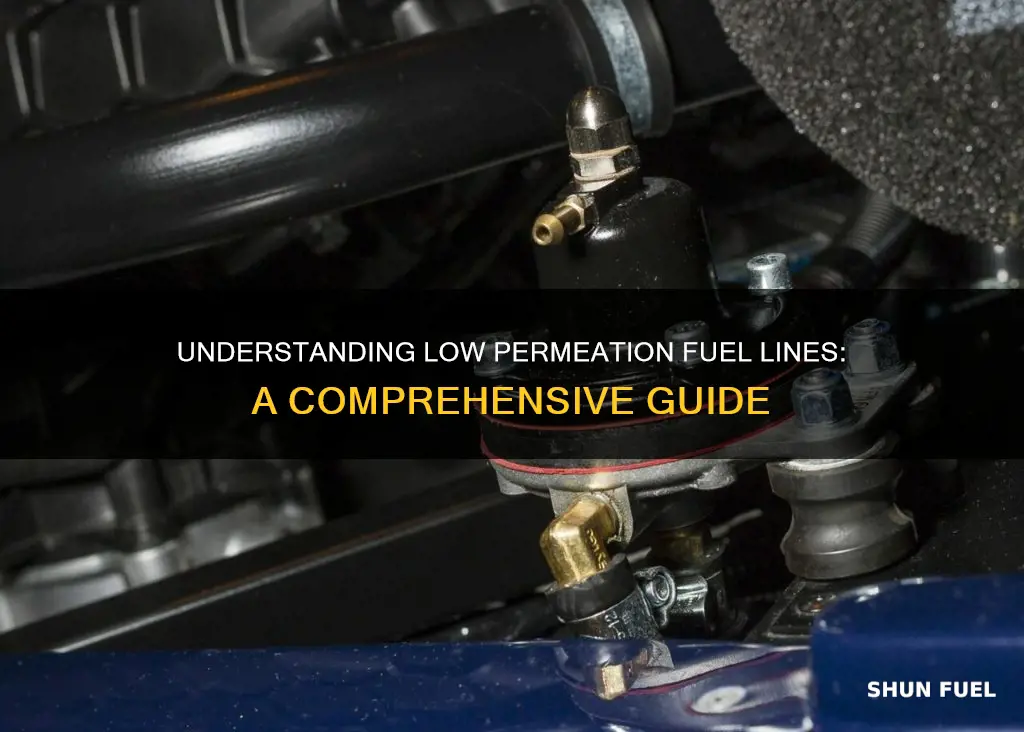
Low permeation fuel lines are an essential component in the design and operation of fuel systems, particularly in the automotive and aviation industries. These specialized lines are designed to transport fuel efficiently while minimizing the release of volatile organic compounds (VOCs) and other harmful substances into the environment. The term low permeation refers to the material's ability to resist the diffusion of fuel through its walls, ensuring that the fuel remains contained within the line and does not evaporate or leak into the surrounding air. This feature is crucial for maintaining fuel efficiency, reducing emissions, and ensuring the safety of fuel-handling systems. Understanding the concept of low permeation fuel lines is vital for engineers and technicians working on fuel systems, as it directly impacts the performance and environmental impact of these systems.
Characteristics | Values |
---|---|
Definition | A fuel line with low permeation allows fuel to pass through it with minimal loss or evaporation. |
Material | Typically made from materials like stainless steel, aluminum, or specialized polymers. |
Permeation Rate | Low permeation fuel lines are designed to have a very low rate of fuel permeation, often measured in grams per square meter per day. |
Temperature Resistance | They can withstand a wide range of temperatures, ensuring fuel stability. |
Compatibility | Compatible with various fuel types, including gasoline, diesel, and biofuels. |
Durability | Built to last, withstanding mechanical stress, vibrations, and environmental factors. |
Flexibility | Often flexible to accommodate engine movement and provide a secure connection. |
Installation | Easy to install and connect to the fuel system. |
Maintenance | Low maintenance required, with no special care needed. |
Safety | Reduces the risk of fuel leaks and potential engine damage. |
Efficiency | Helps maintain engine performance by ensuring a consistent fuel supply. |
What You'll Learn
- Fuel Line Material: Low permeation lines are made from materials that resist fuel evaporation
- Pressure Resistance: These lines can withstand fuel pressure without leaking
- Temperature Tolerance: They maintain integrity across a wide temperature range
- Corrosion Inhibition: Special coatings prevent fuel-induced corrosion
- Flexibility: Low permeation lines are flexible for easy installation and routing
Fuel Line Material: Low permeation lines are made from materials that resist fuel evaporation
Low permeation fuel lines are an essential component in the automotive industry, particularly for vehicles that rely on fuel efficiency and performance. These fuel lines are designed with a specific purpose: to minimize the evaporation of fuel, especially volatile organic compounds (VOCs), from the fuel system. The concept of low permeation is crucial as it directly impacts the overall efficiency and environmental friendliness of a vehicle's fuel delivery system.
The primary challenge with fuel lines is their potential to allow fuel to evaporate, which can lead to several issues. Firstly, fuel evaporation contributes to increased emissions, as the evaporated fuel releases VOCs into the atmosphere. This is a significant concern for environmental regulations, as it can negatively impact air quality. Secondly, fuel evaporation can result in a loss of fuel efficiency, as the engine may not receive the precise amount of fuel required for optimal performance. This can lead to reduced power output and increased fuel consumption.
To address this problem, engineers and manufacturers have developed fuel lines made from specialized materials. These materials are carefully selected to possess low permeation properties, meaning they resist the evaporation of fuel. One common material used for this purpose is stainless steel, known for its excellent resistance to corrosion and its ability to maintain structural integrity even in the presence of fuel. Stainless steel fuel lines are designed to be durable and long-lasting, ensuring that the fuel remains contained within the system without excessive evaporation.
Another material often employed in low permeation fuel lines is a composite material, which can be a blend of various polymers and additives. These composites are engineered to have a low permeability to fuel, making them ideal for fuel delivery systems. The use of composite materials allows for flexibility in design, enabling the creation of fuel lines that can conform to the vehicle's engine bay while still maintaining their structural integrity.
In summary, low permeation fuel lines are a critical innovation in the automotive industry, aiming to reduce fuel evaporation and its associated environmental and performance impacts. By utilizing materials with excellent resistance to fuel permeation, such as stainless steel and composite materials, these fuel lines ensure that the fuel remains contained, leading to improved engine efficiency and reduced emissions. This technology is a testament to the ongoing efforts to make vehicles more environmentally friendly and efficient.
VXR Pro 93 Fuel Line: Dimensions and Specifications
You may want to see also
Pressure Resistance: These lines can withstand fuel pressure without leaking
Low permeation fuel lines are an essential component in the fuel delivery system of vehicles, particularly those with high-performance engines. These lines are designed to transport fuel efficiently while ensuring that it remains contained and secure within the system. One of the critical aspects of these fuel lines is their ability to withstand fuel pressure without any leakage, which is a feature often referred to as 'pressure resistance'.
The pressure resistance of low permeation fuel lines is a crucial factor in maintaining the integrity of the fuel system. Fuel lines are typically subjected to varying levels of pressure, especially in high-performance vehicles, where engines operate at higher RPMs and produce more power. The pressure resistance ensures that the fuel lines can handle these forces without compromising the safety and efficiency of the system. This feature is vital to prevent fuel leaks, which could lead to dangerous situations, such as fires or explosions, especially in high-temperature environments.
These fuel lines are constructed using specialized materials that are engineered to resist fuel permeation and maintain structural integrity under pressure. The materials used are carefully selected to ensure they can withstand the corrosive nature of fuel, especially over extended periods. This resistance to permeation is achieved through the use of advanced polymers and synthetic compounds that form a protective barrier around the fuel, preventing it from seeping through the line walls.
In addition to the material composition, the design of these fuel lines also plays a significant role in their pressure resistance. The lines are often designed with a flexible yet robust structure, allowing them to accommodate slight movements and vibrations without compromising their integrity. This flexibility, combined with the material's strength, ensures that the fuel lines can withstand the mechanical stresses imposed by the fuel pressure and the vehicle's operation.
Furthermore, the manufacturing process of these fuel lines involves rigorous quality control measures to ensure they meet the required standards for pressure resistance. This includes testing the lines under simulated fuel pressure conditions to assess their performance and durability. By adhering to these strict manufacturing practices, the fuel lines can provide reliable and safe fuel delivery, even in demanding automotive applications.
Scooter Fuel Lines: Powering the Engine's Heart
You may want to see also
Temperature Tolerance: They maintain integrity across a wide temperature range
Temperature tolerance is a critical aspect of fuel lines, especially in automotive and industrial applications where fuel lines are exposed to varying environmental conditions. These lines are designed to withstand a wide range of temperatures, from extreme cold to scorching heat, without compromising their structural integrity or performance. This feature is essential to ensure the safe and efficient operation of fuel systems.
In cold environments, fuel lines must remain flexible and resistant to brittleness. Low permeation fuel lines are engineered to maintain their shape and functionality even when temperatures drop significantly. This is crucial to prevent fuel leaks and ensure that the fuel system operates optimally, even in freezing conditions. The material composition and construction of these lines play a vital role in achieving this temperature tolerance.
When temperatures rise, the fuel lines must endure without degrading or becoming susceptible to heat-induced damage. High-quality fuel lines are constructed with materials that can withstand elevated temperatures without softening or losing their structural strength. This is particularly important in applications where engines operate at high temperatures, such as racing cars or industrial machinery. The ability to maintain integrity across a wide temperature range ensures that the fuel lines can handle the demands of various operating environments.
The design and manufacturing processes of low permeation fuel lines also contribute to their temperature tolerance. These lines often feature reinforced construction, using materials like steel braids or woven fibers to provide additional strength and flexibility. This reinforcement helps prevent cracking or kinking, ensuring that the fuel lines remain intact and functional even when subjected to extreme temperature fluctuations.
Furthermore, the use of specialized coatings or protective layers can enhance temperature tolerance. These coatings may include rubber, plastic, or other materials applied to the inner and outer surfaces of the fuel lines. Such coatings act as a barrier, protecting the inner components from direct exposure to harsh temperatures and preventing degradation or corrosion. This additional layer of protection ensures the long-term reliability and performance of the fuel lines.
Fuel Line Clog Symptoms: Engine Issues Revealed
You may want to see also
Corrosion Inhibition: Special coatings prevent fuel-induced corrosion
Corrosion is a natural process that occurs when a material reacts with its environment, leading to deterioration and potential failure. In the context of fuel systems, corrosion can be particularly detrimental, as it can compromise the integrity of fuel lines, tanks, and other components, leading to leaks, contamination, and even system failure. One of the primary causes of corrosion in fuel systems is the presence of corrosive substances in the fuel itself, such as water, acids, and volatile organic compounds (VOCs). These substances can accelerate the breakdown of metal surfaces, leading to pitting, galvanic corrosion, and other forms of degradation.
To combat this issue, engineers have developed specialized coatings and inhibitors that can be applied to fuel lines and other components to prevent corrosion. These coatings act as a protective barrier, shielding the metal surface from the corrosive effects of the fuel. They work by forming a non-reactive layer on the metal surface, which prevents the corrosive substances from coming into direct contact with the metal. This layer can be made from various materials, including polymers, ceramics, and metallic oxides, each with its own unique properties and advantages.
One common type of corrosion inhibitor is a zinc phosphate coating. This coating is applied to the inner surface of fuel lines and tanks, creating a protective layer that resists corrosion. Zinc phosphate provides excellent adhesion to the metal surface and forms a dense, non-porous layer that prevents the penetration of corrosive substances. It is particularly effective in preventing galvanic corrosion, where different metals in contact with each other experience accelerated corrosion due to the flow of electricity.
Another approach to corrosion inhibition is the use of silicate-based coatings. These coatings are often applied to aluminum and other lightweight metals commonly used in fuel systems. Silicate coatings form a stable, non-reactive layer that resists the corrosive effects of water and acids. They are particularly useful in preventing pitting corrosion, which can occur when small, localized areas of the metal surface are attacked by corrosive substances.
In addition to these coatings, some fuel systems incorporate corrosion inhibitors in the fuel itself. These inhibitors are added in small quantities to the fuel during the manufacturing process or can be injected directly into the fuel tank. They work by adsorbing onto the metal surface and forming a protective layer, similar to the coatings mentioned above. Common fuel inhibitors include polyphosphates, polycarboxylates, and amine-based compounds, each with its own specific mechanism of action.
By employing these corrosion-inhibiting techniques, fuel systems can be designed to withstand the corrosive effects of the fuel they contain. This ensures the longevity and reliability of the system, reducing the risk of leaks, contamination, and other performance issues caused by corrosion. Proper maintenance, including regular inspections and the use of high-quality, corrosion-resistant materials, further enhances the overall durability of fuel systems.
E85 Fuel Line Maintenance: What to Flush and Why
You may want to see also
Flexibility: Low permeation lines are flexible for easy installation and routing
Low permeation fuel lines are designed with a specific focus on flexibility, making them an ideal choice for various fuel delivery systems. This flexibility is a key feature that sets these lines apart and offers numerous advantages during installation and maintenance. The ability to easily bend and route these lines allows for a more efficient and adaptable setup, ensuring that the fuel system can be tailored to fit the unique requirements of different vehicles and applications.
When it comes to installation, the flexibility of low permeation lines simplifies the process. These lines can be effortlessly maneuvered around tight spaces, complex engine compartments, and various obstacles without compromising their structural integrity. This ease of installation not only saves time but also reduces the risk of damage to the fuel lines during the setup process. The flexibility ensures that the lines can be securely fastened and positioned without the need for excessive force, making the entire installation process smoother and safer.
In terms of routing, the flexibility of these fuel lines provides designers and mechanics with the freedom to choose the most optimal path for the fuel supply. This is particularly beneficial in high-performance vehicles or custom builds, where the fuel lines need to be strategically placed to ensure efficient fuel delivery while maintaining a clean and organized engine bay. The ability to route the lines around specific components or through different angles allows for a more aesthetically pleasing and functional fuel system.
Furthermore, the flexibility of low permeation fuel lines contributes to their durability. The lines can absorb vibrations and movements without breaking or kinking, which is essential in dynamic environments such as racing or off-road adventures. This flexibility ensures that the fuel lines remain intact and functional even when subjected to extreme conditions, providing a reliable fuel supply to the engine.
In summary, the flexibility of low permeation fuel lines is a significant advantage that simplifies installation, allows for creative routing, and enhances the overall durability of the fuel system. This feature makes these lines a preferred choice for professionals and enthusiasts alike, ensuring a reliable and efficient fuel delivery solution for a wide range of applications.
Choosing the Right Color Fuel Line for Your Mower
You may want to see also
Frequently asked questions
Low permeation fuel lines are an essential component in the design of fuel systems, especially in vehicles and industrial applications. These lines are designed to minimize the release of volatile organic compounds (VOCs) and other harmful substances from the fuel into the surrounding environment. The term "low permeation" refers to the material's ability to resist the diffusion of fuel through its walls, ensuring that the fuel remains contained and does not evaporate or leak.
Regular fuel lines, often made of rubber or plastic, may allow fuel to permeate and evaporate over time, leading to potential health and environmental concerns. In contrast, low permeation fuel lines are constructed using specialized materials like metal braids or composite materials that act as a barrier. This construction method significantly reduces the rate of fuel permeation, ensuring a safer and more controlled fuel delivery system.
In the automotive industry, low permeation fuel lines are crucial for maintaining the integrity of the fuel system and ensuring optimal engine performance. These lines help prevent fuel leaks, reduce emissions, and improve overall fuel efficiency. By minimizing fuel evaporation, they contribute to a cleaner environment and enhance the longevity of the vehicle's fuel system components.