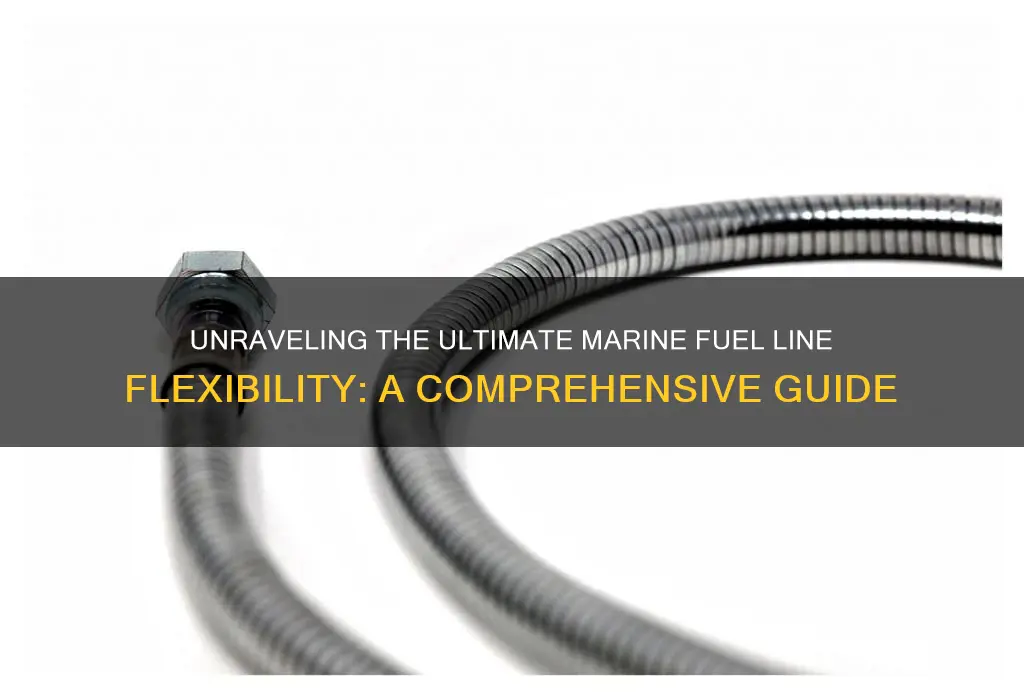
When it comes to marine fuel lines, flexibility is a crucial factor to consider, especially in the demanding environment of marine applications. The most flexible marine fuel line is designed to withstand the rigorous conditions of the sea, including vibrations, movements, and potential impacts. This type of fuel line is typically constructed with a high-quality, durable material that allows for easy bending and routing, ensuring a secure and reliable connection between the fuel tank and the engine. Its flexibility enables it to adapt to the various angles and configurations of marine vessels, providing an efficient and safe fuel supply while minimizing the risk of damage or leaks.
What You'll Learn
- Material Flexibility: Lines made from flexible materials like braided nylon or polyester offer superior bend radius and durability
- Temperature Resistance: Fuel lines with high-temperature resistance can withstand engine heat, ensuring long-lasting performance
- Vibration Damping: Lines with built-in vibration damping reduce engine noise and prevent damage from vibrations
- Chemical Compatibility: Choose lines compatible with marine fuels to prevent degradation and ensure long-term reliability
- Size and Routing: Flexible lines come in various sizes and can be easily routed to fit tight spaces and engine configurations
Material Flexibility: Lines made from flexible materials like braided nylon or polyester offer superior bend radius and durability
When it comes to choosing the most flexible marine fuel line, material flexibility is a key factor to consider. Lines made from flexible materials such as braided nylon or polyester offer several advantages that make them ideal for marine applications.
Braided nylon and polyester are known for their exceptional flexibility, allowing the fuel lines to withstand various bending and twisting motions without compromising their structural integrity. This flexibility is crucial in marine environments, where fuel lines need to navigate through tight spaces, sharp turns, and potential obstacles. By using these materials, the fuel lines can maintain their shape and resist kinking or bending excessively, ensuring a smooth and reliable flow of fuel.
One of the primary benefits of flexible materials is their ability to provide a superior bend radius. This means the fuel lines can be bent around corners and curves without experiencing excessive stress or strain. A larger bend radius reduces the risk of damage to the line and allows for easier installation and routing. For example, a braided nylon fuel line can be bent to a tighter radius compared to a rigid material, making it more adaptable to the unique challenges of marine environments.
Additionally, flexible materials like braided nylon and polyester offer excellent durability. These materials are designed to withstand the harsh conditions of marine environments, including exposure to sunlight, saltwater, and temperature fluctuations. The braiding technique used in their construction provides added strength and resistance to abrasion, ensuring that the fuel lines remain flexible yet robust. This durability is essential to prevent leaks, punctures, or damage that could occur during the operation and maintenance of marine vessels.
In summary, when selecting a marine fuel line, prioritizing material flexibility is essential. Lines made from braided nylon or polyester offer superior bend radius, allowing for easier installation and navigation through tight spaces. Their flexibility also ensures that the fuel lines can withstand various motions without compromising their structural integrity. Furthermore, the durability of these materials makes them well-suited to the demanding conditions of marine environments, providing long-lasting performance and reliability.
Choosing the Right Fuel Line: A Comprehensive Guide
You may want to see also
Temperature Resistance: Fuel lines with high-temperature resistance can withstand engine heat, ensuring long-lasting performance
When it comes to marine fuel lines, temperature resistance is a critical factor to consider, especially for those seeking the most flexible and durable solution. High-temperature resistance in fuel lines is essential to ensure the longevity and reliability of marine engines, which often operate in demanding environments. These fuel lines are designed to withstand the extreme heat generated by engines, whether it's the powerful diesel engines on large commercial vessels or the smaller inboard motors on recreational boats.
The ability to resist temperature changes is crucial for several reasons. Firstly, marine environments can expose fuel lines to intense heat, especially when engines are running at peak performance. This heat can cause traditional fuel lines to degrade, become brittle, or even melt, leading to potential fuel leaks and system failures. By using fuel lines with high-temperature resistance, you create a robust barrier between the fuel and the engine's heat, ensuring that the fuel remains stable and the lines remain intact.
These specialized fuel lines are typically made from advanced materials that can handle the rigors of marine environments. For instance, they may be constructed with a flexible yet sturdy inner layer, often made from high-density polyethylene (HDPE) or similar compounds, which provide excellent resistance to heat and chemical degradation. The outer covering could be a durable rubber or a specialized synthetic material, ensuring flexibility and protection against abrasion. This construction allows the fuel lines to bend and move with the vessel's motion while maintaining their structural integrity.
In addition to the materials used, the manufacturing process also plays a significant role in temperature resistance. Fuel lines with high-temperature resistance often undergo rigorous testing to ensure they can withstand extreme conditions. This includes exposing the lines to high temperatures and evaluating their performance over extended periods. By meeting these stringent standards, these fuel lines provide peace of mind, knowing that they can handle the challenges of marine environments.
In summary, when considering the most flexible marine fuel line, temperature resistance is a key differentiator. Fuel lines with this feature offer a reliable solution for marine applications, ensuring that engines can operate efficiently and safely, even in the most demanding conditions. By investing in high-quality, temperature-resistant fuel lines, boat owners and operators can minimize the risk of breakdowns and ensure their vessels are equipped to handle the unique challenges of marine environments.
E85 Fuel Line: Choosing the Right Option for Your Engine
You may want to see also
Vibration Damping: Lines with built-in vibration damping reduce engine noise and prevent damage from vibrations
When it comes to marine fuel lines, flexibility is a crucial factor, especially in the context of vibration damping. Vibration damping is an essential consideration for any marine application, as it directly impacts the performance and longevity of the engine and fuel system. Marine environments are inherently challenging due to the constant motion and vibrations experienced on the water. These vibrations can cause significant stress on fuel lines, leading to potential damage over time.
To address this issue, manufacturers have developed fuel lines with built-in vibration damping features. These lines are designed to absorb and dissipate the energy generated by engine vibrations, ensuring a smoother and more stable operation. The key to achieving this lies in the construction and material composition of the fuel lines. Traditional fuel lines often lack the necessary flexibility and resilience to withstand the harsh conditions of marine environments. They can become stiff and prone to cracking or breaking when exposed to continuous vibrations.
Vibration-damping fuel lines are engineered with specialized materials and designs. One common approach is to incorporate a layer of damping material within the fuel line itself. This damping layer can be made from various compounds, such as rubber or foam, which have inherent vibration-absorbing properties. When the engine operates, the vibrations cause the fuel line to flex and deform, but the damping material absorbs the energy, reducing the overall amplitude of the vibrations. This results in a quieter engine and minimizes the risk of damage to the fuel system.
The benefits of using vibration-damping fuel lines are significant. Firstly, they contribute to a quieter and more comfortable marine environment. By reducing engine noise, these lines make for a more pleasant experience for passengers and crew, especially during extended voyages. Secondly, the damping effect helps prevent premature wear and tear on the fuel system components. Without the constant vibration, the fuel lines, pumps, and injectors are less likely to develop cracks or leaks, ensuring a more reliable and efficient engine performance.
In summary, vibration damping is a critical aspect of marine fuel line design. By incorporating damping materials and flexible construction, these lines provide a robust solution to the challenges posed by engine vibrations. The result is a more durable and efficient marine fuel system, capable of withstanding the demanding conditions of the open sea. When selecting fuel lines for marine applications, considering vibration damping features is essential to ensure optimal performance and longevity.
Fuel Line Cleaning: How Much Does It Cost?
You may want to see also
Chemical Compatibility: Choose lines compatible with marine fuels to prevent degradation and ensure long-term reliability
When it comes to marine fuel lines, chemical compatibility is a critical factor to consider for the long-term reliability and performance of your vessel's fuel system. Marine fuels, such as diesel, gasoline, and biofuels, contain various additives and components that can interact with the materials used in fuel lines. If the fuel line material is not compatible with the fuel, it can lead to several issues, including fuel degradation, reduced performance, and even system failure.
The primary goal is to select fuel lines that are chemically compatible with the specific marine fuels being used. This means the materials used in the construction of the fuel line should not react with or be damaged by the components present in the fuel. For example, some marine fuels may contain antioxidants, detergents, or other additives designed to improve performance and prevent engine wear. If the fuel line is not compatible, these additives can potentially dissolve or degrade the fuel line material over time.
To ensure chemical compatibility, it is essential to refer to the manufacturer's specifications and guidelines for the chosen marine fuel. Different fuel types may have unique requirements and recommendations for fuel line materials. For instance, some marine diesel fuels might require fuel lines made from specific polymers or compounds that can withstand the fuel's chemical properties. By selecting the right material, you can prevent fuel degradation, maintain optimal engine performance, and extend the lifespan of your fuel system.
Common materials used for marine fuel lines include various types of rubber, such as natural or synthetic rubber compounds, and certain plastics like polyvinyl chloride (PVC) or fluoropolymers. These materials are chosen for their ability to resist fuel-related chemicals and provide flexibility, which is crucial for accommodating the movement and vibrations experienced during marine operations. It is crucial to avoid using materials that are known to be incompatible with the specific marine fuels in use, as this could lead to premature failure and potential safety hazards.
In summary, when selecting a marine fuel line, prioritize chemical compatibility to ensure the long-term reliability and performance of your vessel's fuel system. Research and consult the manufacturer's guidelines to choose materials that can withstand the specific marine fuels being used, preventing degradation and ensuring a consistent and safe fuel supply for your marine applications.
Understanding B1 Fuel Line: A Comprehensive Guide
You may want to see also
Size and Routing: Flexible lines come in various sizes and can be easily routed to fit tight spaces and engine configurations
When it comes to marine fuel lines, flexibility is a crucial factor, especially in the context of engine design and space constraints. The most flexible marine fuel lines are designed with a range of sizes to accommodate different vessel configurations and engine requirements. These lines are typically constructed with a durable yet pliable material, often a combination of rubber and synthetic compounds, allowing them to bend and adapt to various routes without compromising performance.
The variety in sizes is essential to ensure a proper fit for different engine compartments. Smaller vessels with compact engines may require thinner and more compact fuel lines, while larger ships with more extensive engine setups might need thicker and longer lines. This versatility in sizing enables marine engineers and technicians to optimize the fuel system's layout, ensuring efficient and safe operation.
Routing these flexible fuel lines is an art in itself. The lines are designed to be easily manipulated, allowing for intricate paths through tight spaces. This feature is particularly useful in engine rooms where space is limited, and traditional rigid lines would be cumbersome. By utilizing flexible lines, technicians can navigate around obstacles, such as bulkheads, pipes, and other equipment, creating a clean and efficient fuel supply system.
The ease of routing also simplifies the installation process. Technicians can quickly adapt the lines to the specific engine configuration, ensuring a secure and reliable connection. This flexibility in design not only saves time during installation but also reduces the risk of damage to the lines during the routing process.
In summary, the most flexible marine fuel lines offer a practical solution for engine room design and maintenance. Their adjustable nature, with various sizes and easy routing capabilities, ensures that fuel systems can be tailored to fit diverse vessel requirements. This adaptability is a key advantage in the marine industry, where space optimization and efficient fuel management are critical considerations.
The Ultimate Guide to Choosing the Best 1-2 Fuel Line
You may want to see also
Frequently asked questions
Flexibility in a marine fuel line is achieved through the use of specialized materials and construction techniques. Typically, these lines are made from high-quality, durable polymers or a combination of rubber and synthetic fibers, allowing them to bend and twist without kinking or damaging the fuel.
Flexible fuel lines are essential for marine applications due to the constant movement and vibrations experienced on boats. Their flexibility ensures that the lines can withstand the rigors of the marine environment, including engine vibrations, wave action, and the movement of the vessel, without compromising fuel delivery or causing damage to the engine.
It is crucial to use fuel lines specifically designed for marine applications. Standard automotive fuel lines may lack the necessary flexibility and durability for marine use, especially in harsh conditions. Marine-grade fuel lines are engineered to resist fuel degradation, UV exposure, and the corrosive effects of saltwater.
A flexible marine fuel line should be constructed with a smooth, flexible outer sheath, allowing it to bend around corners and navigate through tight spaces. It should also have a reinforced inner layer to prevent fuel leakage and maintain structural integrity. Look for lines with a clear or translucent outer cover to inspect the inner construction.
The lifespan of marine fuel lines depends on various factors, including the quality of the lines, the marine environment, and maintenance practices. As a general guideline, it is recommended to inspect and replace fuel lines every 5-10 years or sooner if signs of wear, damage, or fuel contamination are noticed. Regular maintenance and proper storage can help extend the life of these lines.