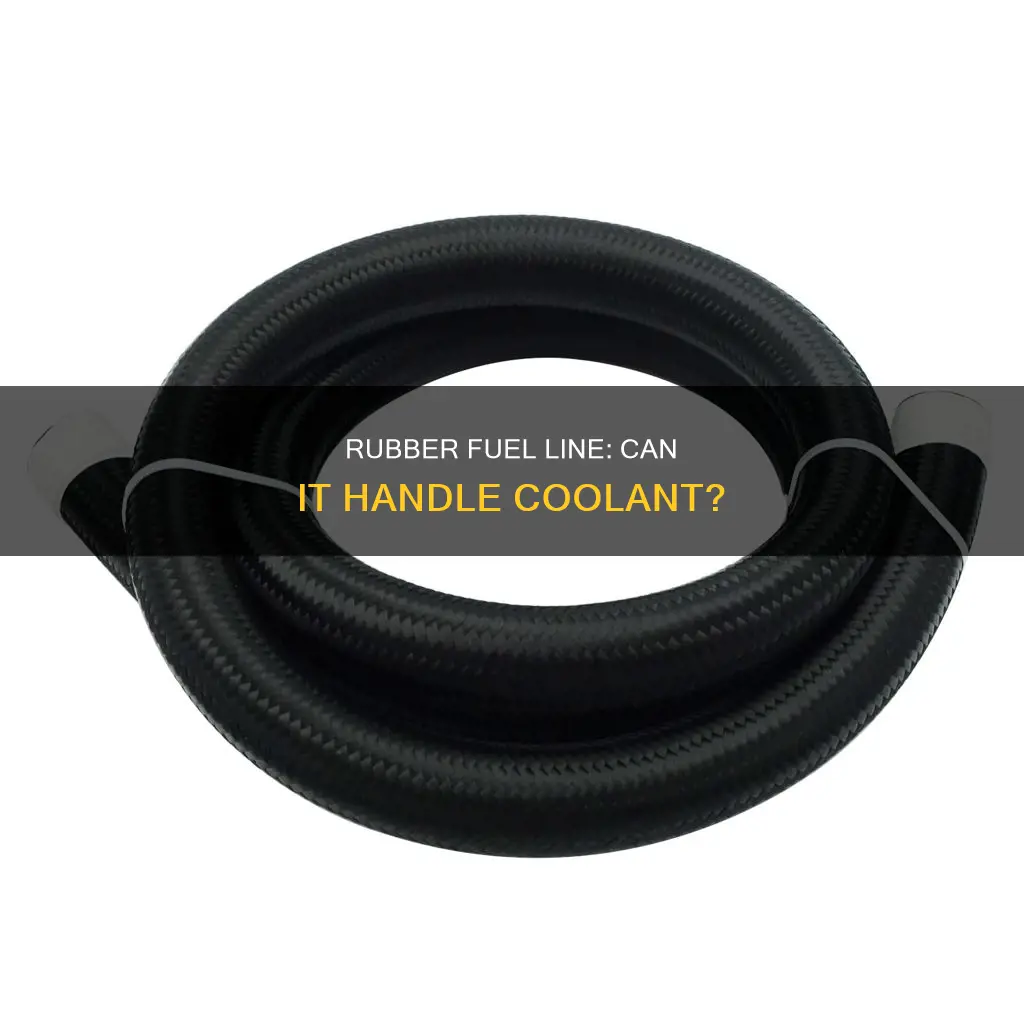
When it comes to vehicle maintenance, ensuring the compatibility of various components is crucial. One important aspect is the fuel system, particularly the fuel lines. Rubber fuel lines are commonly used in vehicles, but they may not be suitable for all substances they come into contact with. In this context, we explore whether rubber fuel lines are rated for coolant, considering the potential risks and benefits of using these materials in different automotive applications.
Characteristics | Values |
---|---|
Material | Rubber |
Temperature Range | -40°F to 250°F (-40°C to 121°C) |
Pressure Rating | Up to 250 psi (17.2 bar) |
Flexibility | High flexibility for easy installation |
Chemical Resistance | Resistant to coolant chemicals |
Durability | Long-lasting and resistant to aging |
Color | Typically black or blue |
Standard Sizes | Available in various diameters and lengths |
Compatibility | Suitable for use with most coolants |
Installation | Easy to install and connect |
What You'll Learn
- Material Compatibility: Rubber fuel lines must be compatible with coolant to prevent degradation
- Temperature Resistance: Coolant temperatures can affect rubber's flexibility and durability
- Chemical Stability: Rubber fuel lines should withstand coolant chemicals without cracking or leaking
- Pressure Handling: Rubber fuel lines must handle coolant pressure without failure
- Flexibility: Coolant's movement can cause rubber fuel lines to flex, requiring flexibility
Material Compatibility: Rubber fuel lines must be compatible with coolant to prevent degradation
The compatibility of rubber fuel lines with coolant is a critical aspect of vehicle maintenance that often goes overlooked. Coolant, also known as antifreeze, is a liquid mixture used to regulate the engine's temperature and prevent freezing in cold climates. When it comes to rubber fuel lines, the material's interaction with coolant is essential to ensure the longevity and reliability of the fuel system.
Rubber is a versatile material widely used in fuel lines due to its flexibility, durability, and cost-effectiveness. However, not all rubbers are created equal, and their compatibility with coolant can vary significantly. The primary concern is the potential for coolant to degrade the rubber over time, leading to a host of issues. Coolant contains various chemicals, including ethylene glycol, which can be corrosive to certain types of rubber. When exposed to coolant, some rubbers may become brittle, crack, or even disintegrate, compromising the integrity of the fuel system.
To ensure compatibility, it is crucial to select the right type of rubber for fuel lines. Natural rubber, for instance, is generally not recommended for coolant-carrying applications due to its susceptibility to degradation. On the other hand, synthetic rubbers, such as neoprene or butyl, offer improved resistance to coolant chemicals. These synthetic rubbers are specifically engineered to withstand the corrosive nature of coolant, making them ideal for fuel lines in vehicles that operate in diverse environmental conditions.
When choosing rubber fuel lines, it is essential to consider the specific coolant types used in the vehicle. Different coolants may have varying compositions and concentrations of chemicals, requiring different levels of compatibility. For example, some coolants contain additives that can accelerate the degradation process, making it even more critical to select the right rubber material. Consulting the vehicle manufacturer's guidelines or seeking expert advice can help in making an informed decision to ensure the fuel system's longevity.
In summary, material compatibility is a vital consideration when dealing with rubber fuel lines and coolant. The right choice of rubber material can prevent degradation, ensuring the fuel system's reliability and performance. By understanding the potential risks and selecting compatible materials, vehicle owners can maintain their fuel systems effectively and avoid costly repairs or replacements.
Heated Fuel Lines: Preventing Engine Cold Starts and Fuel Gel
You may want to see also
Temperature Resistance: Coolant temperatures can affect rubber's flexibility and durability
The performance and longevity of rubber fuel lines used in automotive applications are significantly influenced by their temperature resistance, particularly when exposed to coolant temperatures. Coolants, designed to regulate engine temperature, often contain additives that can impact the material properties of rubber. It is crucial to understand how these factors interact to ensure the fuel lines remain flexible, durable, and capable of withstanding the rigors of the automotive environment.
Rubber, a polymeric material, exhibits varying degrees of flexibility and strength depending on its composition and processing. When exposed to coolant temperatures, the rubber's molecular structure undergoes changes. Coolants, especially those with higher concentrations of ethylene glycol or propylene glycol, can cause the rubber to become stiffer and less pliable. This loss of flexibility can lead to increased stress on the fuel line during engine operation, potentially resulting in cracks, leaks, or even failure.
The durability of the rubber fuel line is also at stake. Prolonged exposure to coolant temperatures can accelerate the degradation of the rubber's cross-linking structure, leading to a phenomenon known as thermal aging. This process causes the rubber to become brittle and more susceptible to damage from mechanical stress. Over time, the fuel line may develop cracks or even rupture, causing fuel leaks, which can be hazardous and environmentally detrimental.
To address this issue, manufacturers often specify temperature ratings for their rubber fuel lines. These ratings indicate the maximum and minimum temperatures at which the fuel line can operate while maintaining its required performance characteristics. It is essential to select fuel lines that meet or exceed the engine's coolant temperature requirements to ensure optimal performance and longevity.
In summary, coolant temperatures play a critical role in the performance and durability of rubber fuel lines. Understanding the impact of coolants on rubber's flexibility and strength is vital for selecting the appropriate fuel line for a specific application. By considering temperature resistance, engineers and automotive professionals can ensure the reliability and safety of fuel systems, contributing to overall vehicle performance and longevity.
Effective Fuel Line Cleaning: Methods and Solutions
You may want to see also
Chemical Stability: Rubber fuel lines should withstand coolant chemicals without cracking or leaking
The chemical stability of rubber fuel lines is a critical aspect when considering their use in vehicle cooling systems. Coolant, a mixture of water, chemicals, and additives, is designed to regulate engine temperature and prevent corrosion. However, it can also be highly corrosive to certain materials, especially if the coolant contains ethylene glycol or other additives. Rubber, a common material for fuel lines, must be carefully selected to ensure it can withstand the chemical composition of the coolant without compromising its structural integrity.
Rubber fuel lines are typically made from synthetic rubbers that are formulated to resist the effects of various chemicals. These rubbers are engineered to have excellent resistance to ethylene glycol, which is a primary component of many coolants. The key to achieving this resistance lies in the molecular structure of the rubber. Natural rubbers, such as neoprene, have a relatively simple molecular structure that can be easily penetrated by coolant chemicals, leading to swelling, cracking, and eventual failure. In contrast, synthetic rubbers, like nitrile or butyl rubber, have more complex molecular chains that are less susceptible to chemical attack.
When selecting a rubber fuel line, it is essential to consider the specific coolant used in the vehicle. Different coolants may have varying chemical compositions, and some additives can be more aggressive than others. For instance, coolants with higher concentrations of silicates or phosphates might require rubber with enhanced chemical resistance to prevent degradation. Manufacturers often provide recommendations or specifications for the compatible coolants, ensuring that the fuel lines are rated for the specific coolant in use.
To ensure the chemical stability of rubber fuel lines, manufacturers employ various techniques during the production process. One common method is the use of specialized additives that enhance the rubber's resistance to coolant chemicals. These additives can include antioxidants, stabilizers, and reinforcing agents that improve the rubber's ability to withstand chemical exposure. Additionally, the manufacturing process may involve curing the rubber at specific temperatures and times to ensure optimal cross-linking, which is crucial for maintaining structural integrity under chemical stress.
In summary, the chemical stability of rubber fuel lines is vital to their performance in vehicle cooling systems. By selecting the right type of rubber and ensuring proper manufacturing techniques, engineers can produce fuel lines that withstand the corrosive effects of coolant chemicals. This is essential for maintaining the integrity of the fuel system, preventing leaks, and ensuring the vehicle's overall reliability and longevity. Proper selection and installation of rubber fuel lines rated for coolant are key to avoiding potential issues related to chemical degradation.
Unraveling the Mystery: 1971 Jeep Fuel Line Fitting Secrets
You may want to see also
Pressure Handling: Rubber fuel lines must handle coolant pressure without failure
The integrity of a vehicle's fuel system is crucial, and this is where rubber fuel lines come into play. These lines are a vital component in the fuel delivery process, connecting the fuel tank to the engine. When it comes to coolant, a common challenge arises: can rubber fuel lines withstand the pressure of coolant without compromising their functionality?
Coolant, also known as antifreeze, is essential for engine cooling and protection against freezing temperatures. It operates under high pressure within the engine block, creating a demanding environment for any component it comes into contact with. Rubber fuel lines, while flexible and durable, must be carefully selected to ensure they can handle this pressure effectively. The key factor here is the material's ability to resist coolant degradation and maintain its structural integrity.
Engineers and automotive professionals often recommend using rubber fuel lines specifically designed for coolant applications. These specialized lines are formulated to withstand the corrosive nature of coolant, which can erode regular rubber over time. The pressure-handling capacity of these lines is enhanced by their construction, often featuring multiple layers of rubber and reinforcement to ensure they can endure the forces exerted by the coolant system.
When selecting rubber fuel lines, it is imperative to consider the specific coolant types used in different vehicles. Different coolants have varying chemical compositions, and some may be more aggressive than others. For instance, ethylene glycol-based coolants are known for their potential to cause degradation in certain rubber compounds. Therefore, choosing the right rubber formula that is compatible with the coolant is essential to prevent leaks, cracks, or other forms of failure.
In summary, rubber fuel lines are a critical component in the fuel system, and their ability to handle coolant pressure is vital for the vehicle's performance and longevity. By understanding the specific requirements and selecting the appropriate rubber fuel lines, engineers can ensure that the fuel system operates efficiently and reliably, even in the presence of high-pressure coolant environments. This attention to detail contributes to the overall safety and efficiency of modern vehicles.
Leaky Fuel Line: Signs, Causes, and Repairs
You may want to see also
Flexibility: Coolant's movement can cause rubber fuel lines to flex, requiring flexibility
The movement of coolants within a vehicle's engine system can have a significant impact on the integrity and performance of various components, including rubber fuel lines. These fuel lines are crucial for delivering fuel from the tank to the engine, and their flexibility is essential to accommodate the dynamic nature of the engine's operation. Coolants play a vital role in maintaining engine temperature, and their circulation can lead to several challenges for rubber fuel lines.
One of the primary concerns is the expansion and contraction of the coolant as it heats up and cools down during the engine's operation. This thermal expansion and contraction can cause the fuel lines to flex and move, especially in areas where the lines are more exposed to temperature fluctuations. The flexibility of the rubber material is crucial here, as it allows the fuel lines to adjust and maintain a secure connection without compromising the flow of fuel. Over time, if the fuel lines lack sufficient flexibility, they may become brittle and prone to cracking, leading to potential fuel leaks and reduced engine performance.
In addition to thermal expansion, the mechanical movements of the engine can also impact the fuel lines. As the engine operates, various components move, including the engine block, pistons, and valves. These movements can cause the fuel lines to flex and twist, especially those that are routed through the engine compartment. The ability of the rubber fuel lines to flex and adapt to these mechanical motions is critical to ensuring a continuous and reliable fuel supply.
To address this requirement for flexibility, modern vehicles often employ rubber fuel lines with carefully designed construction and materials. The rubber compound used should have a suitable durometer, which is a measure of its hardness and flexibility. A softer rubber compound can provide better flexibility, allowing the fuel lines to accommodate the engine's movements without becoming brittle. Additionally, the fuel lines may feature protective layers or coatings to enhance their durability and resistance to coolant-related degradation.
In summary, the movement of coolants within the engine system necessitates the flexibility of rubber fuel lines. This flexibility ensures that the fuel lines can withstand the thermal expansion and contraction of coolants, as well as the mechanical movements of the engine. By using appropriately designed and constructed rubber fuel lines, vehicles can maintain a reliable fuel supply to the engine, even in the face of varying operating conditions. Regular inspection and maintenance of these fuel lines are essential to ensure their longevity and optimal performance.
Fuel Line Flaring: A Double-Edged Decision
You may want to see also
Frequently asked questions
Yes, rubber fuel lines can be used for coolant applications, but it's important to choose the right type of rubber and ensure compatibility with the specific coolant used. Some rubbers may degrade or become brittle when exposed to certain coolants, so proper selection is crucial.
When choosing a rubber fuel line for coolant, consider the temperature range of your coolant system, the chemical resistance of the rubber to the coolant, and the flexibility required for the application. Different rubbers have varying levels of resistance to abrasion, ozone, and UV radiation, which can affect their longevity.
It is generally not recommended to use a rubber fuel line rated for fuel only for coolant. Coolants often contain additives that can accelerate the degradation of rubber, leading to potential leaks or failure over time. It's best to use a line specifically designed for coolant applications.
Check the manufacturer's specifications and data sheets for the rubber fuel line. Look for information on the coolant compatibility of the rubber material. Some manufacturers provide guidelines on the types of coolants their products can withstand. If in doubt, consult the manufacturer or seek professional advice.
Yes, depending on the specific requirements of your coolant system, you might consider alternatives like braided stainless steel fuel lines or high-temperature plastic lines. These materials offer excellent chemical resistance and can handle higher temperatures, making them suitable for coolant-carrying applications.