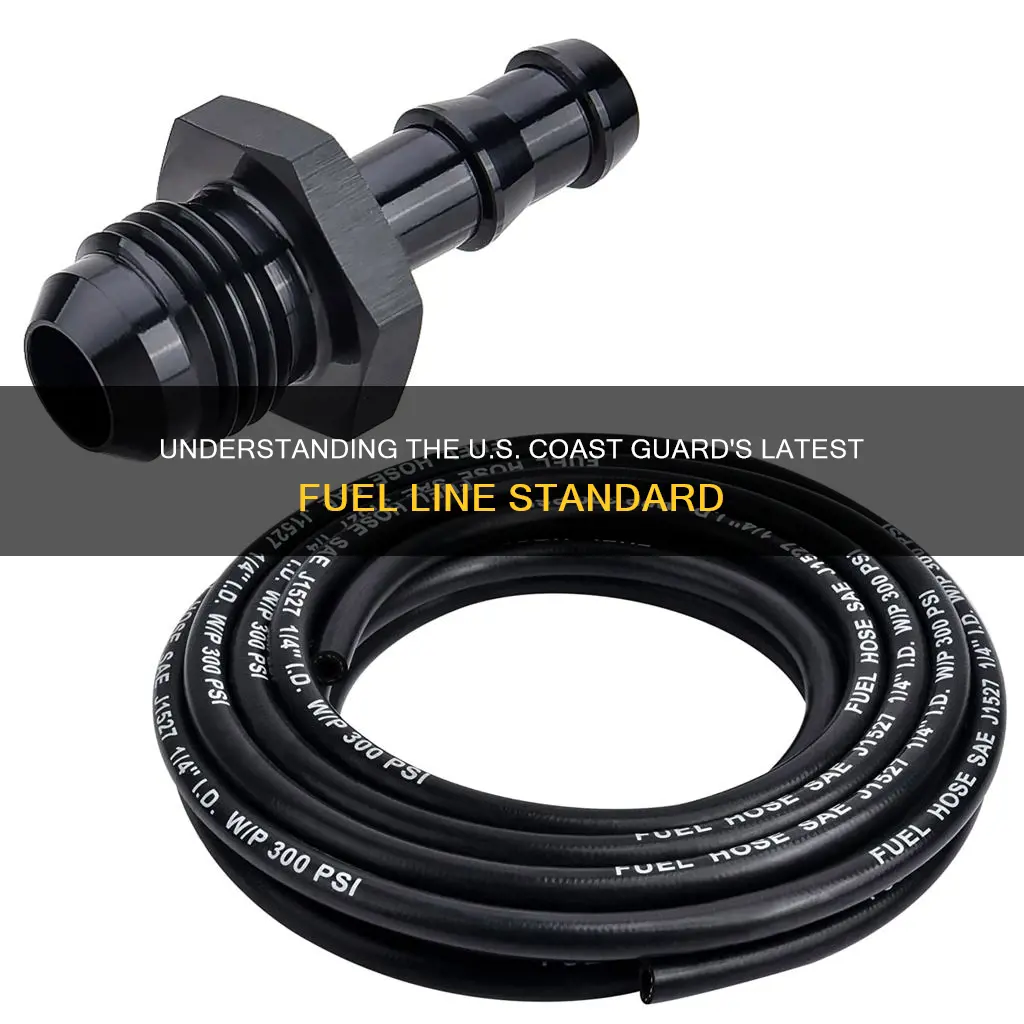
The U.S. Coast Guard (USCG) has recently introduced a new fuel line standard, the latest iteration of the SAE (Society of Automotive Engineers) fuel line specifications. This update is significant as it aims to enhance safety and performance in marine fuel systems. The new standard, designated as SAE J1928, provides detailed guidelines for the design, construction, and testing of fuel lines used in USCG vessels. It covers various aspects, including material requirements, pressure ratings, and installation procedures, ensuring that fuel lines meet the highest safety standards and can withstand the demanding conditions of marine environments.
What You'll Learn
- Fuel Line Material: The latest USCG-approved fuel lines are made from advanced materials like high-density polyethylene (HDPE)
- Sizing and Standards: USCG fuel lines adhere to specific SAE standards for diameters, pressure ratings, and compatibility
- Flexibility and Durability: These lines offer superior flexibility and durability, ensuring long-lasting performance in harsh marine environments
- Fire Resistance: The latest USCG fuel lines are designed with fire-resistant properties to meet safety regulations
- Compliance and Regulations: USCG fuel lines must comply with all relevant regulations and standards set by the Coast Guard
Fuel Line Material: The latest USCG-approved fuel lines are made from advanced materials like high-density polyethylene (HDPE)
The United States Coast Guard (USCG) has stringent requirements for fuel lines in marine applications, ensuring safety and reliability in the often-demanding marine environment. The latest USCG-approved fuel lines are crafted from cutting-edge materials, with high-density polyethylene (HDPE) emerging as a top choice. This advanced polymer offers a unique combination of strength, flexibility, and chemical resistance, making it ideal for the rigorous conditions encountered in marine settings.
HDPE fuel lines are designed to withstand the challenges posed by marine environments, including exposure to sunlight, temperature fluctuations, and the presence of various chemicals and fuels. The material's inherent flexibility allows for easy installation and routing, accommodating the often-complex layouts of marine vessels. Moreover, HDPE's resistance to abrasion and impact ensures that the fuel lines remain intact even in the face of potential hazards, such as rubbing against other components or accidental impacts.
One of the key advantages of HDPE fuel lines is their ability to maintain structural integrity over a wide temperature range. This is crucial in marine applications, where temperatures can vary significantly between hot summers and cold winters. HDPE's stability under these conditions ensures that the fuel lines remain reliable and functional throughout the year, providing consistent performance.
In addition to its mechanical properties, HDPE is also valued for its chemical compatibility with a wide range of fuels and solvents. This feature is essential in marine environments, where vessels often carry various types of fuels and may be exposed to cleaning agents or other chemicals. The HDPE fuel lines can withstand these substances without degradation, ensuring the safety and efficiency of the fuel system.
The USCG's approval of HDPE fuel lines reflects a commitment to safety and performance in marine applications. By utilizing advanced materials like HDPE, manufacturers can ensure that fuel lines meet the highest standards, providing a reliable and secure fuel supply for vessels operating in diverse and challenging environments. This attention to detail in material selection contributes to the overall safety and efficiency of marine operations.
Dodge Cummins Diesel Fuel Line Guide: 1997 Model
You may want to see also
Sizing and Standards: USCG fuel lines adhere to specific SAE standards for diameters, pressure ratings, and compatibility
The United States Coast Guard (USCG) has stringent requirements for fuel lines to ensure the safe and efficient operation of vessels. These specifications are outlined in the Society of Automotive Engineers (SAE) standards, which provide guidelines for fuel line diameters, pressure ratings, and compatibility. Adhering to these standards is crucial for maintaining the integrity of the fuel system and preventing potential hazards.
When it comes to sizing, USCG fuel lines are designed with precision. The SAE standards dictate the minimum and maximum allowable diameters for fuel lines based on the expected flow rates and pressure differentials. For instance, the latest SAE standard specifies that fuel lines should have an inside diameter of at least 3/8 inches for small vessels and 1/2 inch for larger ones. These dimensions ensure optimal fuel delivery while minimizing pressure drops, which can affect engine performance.
Pressure ratings are another critical aspect of USCG fuel line specifications. The SAE standards define the maximum pressure a fuel line can withstand without compromising its structural integrity. For USCG applications, the pressure rating should be at least 250 psi (pounds per square inch) to accommodate the demands of marine environments. This rating ensures that the fuel lines can handle the pressure fluctuations associated with vessel movement and engine operation.
Compatibility is also a key consideration in USCG fuel line standards. The SAE guidelines specify the materials and coatings that fuel lines should be made from to ensure compatibility with the fuel being transported. For instance, the fuel lines must be compatible with gasoline, diesel, or alternative fuels used in marine applications. This compatibility prevents fuel degradation, corrosion, and potential safety hazards.
In summary, USCG fuel lines are subject to rigorous SAE standards that define their diameters, pressure ratings, and compatibility. These standards are essential to guarantee the safe and efficient operation of vessels, ensuring that fuel lines can withstand the unique challenges of marine environments. By adhering to these specifications, the USCG can maintain the reliability and performance of fuel systems, contributing to the overall safety of maritime operations.
Understanding Snowmobile Fuel Lines: Inside the Gas Tank
You may want to see also
Flexibility and Durability: These lines offer superior flexibility and durability, ensuring long-lasting performance in harsh marine environments
The latest U.S. Coast Guard (USCG) fuel lines are designed with a focus on flexibility and durability, ensuring they can withstand the demanding conditions of marine environments. These fuel lines are an essential component of any vessel's fuel system, providing a reliable and safe way to transfer fuel from the tank to the engine. The superior flexibility of these lines is a key feature, allowing them to navigate through tight spaces and complex engine layouts without compromising performance. This flexibility is crucial for vessels with limited engine compartments, ensuring that the fuel lines can be routed efficiently without causing interference or damage.
In harsh marine environments, where fuel lines are exposed to constant movement, vibrations, and temperature fluctuations, durability becomes a critical factor. The latest USCG-approved fuel lines are constructed with high-quality materials that can resist wear and tear, ensuring long-lasting performance. These lines are often made from reinforced rubber or synthetic compounds, which provide excellent resistance to abrasion, chemicals, and UV radiation. The construction process involves layering and braiding techniques to enhance flexibility while maintaining structural integrity, ensuring that the lines can handle the rigors of marine operations.
Flexibility is achieved through the use of specialized materials and designs. The lines may feature a braided or spiral-wound construction, allowing them to bend and adjust to various angles without kinking or becoming stiff. This flexibility is particularly important when the vessel is in motion, as the fuel lines need to accommodate the movement of the vessel without restricting fuel flow. By offering superior flexibility, these lines ensure that the fuel supply remains consistent, even during challenging maneuvers or when the vessel is subjected to rough seas.
The durability of these fuel lines is further enhanced by their ability to withstand extreme conditions. Marine environments often expose fuel lines to saltwater, which can be corrosive, and fuel, which may contain additives that can degrade certain materials. The latest USCG fuel lines are treated with protective coatings or inhibitors to prevent corrosion and maintain their structural integrity. Additionally, the lines are designed to resist temperature extremes, ensuring they can operate effectively in both hot and cold marine climates.
In summary, the latest U.S. Coast Guard-approved fuel lines excel in flexibility and durability, making them ideal for harsh marine environments. Their superior flexibility allows for efficient routing in tight spaces, while their durable construction ensures long-lasting performance. By meeting the stringent requirements of the USCG, these fuel lines provide a reliable and safe solution for transferring fuel in various marine applications, contributing to the overall safety and efficiency of vessels operating in challenging conditions.
Understanding the Role of Fuel Line Pumps in Vehicles
You may want to see also
Fire Resistance: The latest USCG fuel lines are designed with fire-resistant properties to meet safety regulations
The United States Coast Guard (USCG) has implemented stringent safety measures for fuel lines, especially in the context of fire resistance, to ensure the safety of vessels and their crew. The latest USCG fuel lines are engineered with advanced materials and designs to withstand potential fire hazards, adhering to strict safety regulations. These fuel lines are a critical component in the overall safety strategy of marine vessels, particularly those operating in potentially hazardous environments.
Fire resistance is a critical aspect of fuel line design, especially for vessels that may encounter fire-related risks during their operations. The USCG has set specific standards and requirements for fuel lines to ensure they can withstand fire events without compromising the safety of the vessel and its occupants. These standards are designed to minimize the risk of fuel line failures that could lead to fires, explosions, or other catastrophic incidents.
The fire-resistant properties of the latest USCG fuel lines are achieved through the use of specialized materials and construction techniques. These fuel lines are typically made from high-temperature-resistant materials such as stainless steel or specialized polymers that can maintain their structural integrity even when exposed to intense heat. The construction process also involves reinforcing the fuel lines with fire-resistant coatings or braids to further enhance their ability to resist fire damage.
In addition to the use of fire-resistant materials, the design of the fuel lines also incorporates features that promote fire safety. For example, the fuel lines may have built-in fire barriers or protective sleeves that act as a barrier between the fuel and potential ignition sources. These design elements are carefully considered to ensure that the fuel lines can withstand the extreme conditions that may arise during a fire event.
By incorporating fire-resistant properties into the design of fuel lines, the USCG aims to significantly reduce the risk of fire-related incidents on marine vessels. This is particularly important for vessels operating in high-risk areas or those with specific safety requirements. The latest USCG fuel lines are a testament to the organization's commitment to enhancing maritime safety and ensuring that vessels are equipped with the necessary protective measures to safeguard their crew and cargo.
Unveiling the Material Mystery: What Fuels Clear Fuel Lines?
You may want to see also
Compliance and Regulations: USCG fuel lines must comply with all relevant regulations and standards set by the Coast Guard
The United States Coast Guard (USCG) has stringent regulations and standards in place to ensure the safety and reliability of fuel lines used in marine environments. These regulations are designed to prevent accidents, protect the environment, and maintain the integrity of the fuel systems on board vessels. When it comes to fuel lines, the USCG has specific requirements that must be met to ensure compliance.
One of the key aspects of compliance is the use of fuel lines that meet the latest SAE (Society of Automotive Engineers) standards. The SAE provides a comprehensive set of specifications and guidelines for various components of marine fuel systems, including fuel lines. The latest SAE standard for fuel lines is an essential reference for manufacturers, installers, and vessel owners to ensure that the fuel lines used are of the highest quality and meet the necessary performance criteria. This standard covers various factors such as material composition, dimensional tolerances, pressure ratings, and flexibility, ensuring that the fuel lines can withstand the demanding conditions of marine environments.
USCG regulations mandate that fuel lines must be made from approved materials that can withstand the corrosive effects of fuel, seawater, and other marine elements. The Coast Guard has established specific requirements for the construction and testing of fuel lines to ensure their durability and reliability. These requirements include the use of materials with appropriate tensile strength, flexibility, and resistance to abrasion and corrosion. For example, the USCG may specify that fuel lines must be constructed with a minimum number of layers, including an outer protective layer, to ensure their longevity and performance.
Compliance also involves regular inspections and maintenance to ensure that fuel lines remain in good condition throughout the vessel's operational life. The USCG provides guidelines for visual inspections, pressure testing, and replacement schedules to identify and address any potential issues. By adhering to these maintenance practices, vessel owners can ensure that their fuel lines continue to meet the required standards and minimize the risk of fuel leaks or system failures.
Furthermore, the USCG has established guidelines for the installation and routing of fuel lines to prevent damage and ensure proper functionality. These guidelines include recommendations for proper support, clearance from moving parts, and protection against mechanical stress. Proper installation and routing are crucial to maintaining the integrity of the fuel system and preventing potential hazards.
In summary, compliance with USCG regulations is essential for fuel lines used in marine applications. Manufacturers and vessel owners must adhere to the latest SAE standards and USCG guidelines to ensure the safety, reliability, and longevity of fuel lines. Regular maintenance, inspections, and adherence to installation practices are key components of maintaining compliance and minimizing the risks associated with fuel systems on board vessels.
Unveiling the Causes: Why Fuel Line Leaks Happen
You may want to see also
Frequently asked questions
The latest standard for fuel lines in the USCG is the SAE J1777, which was released in 2018. This standard provides specifications for fuel lines used in marine applications, ensuring they meet specific performance and safety criteria.
The USCG's fuel line standard is an adaptation of the SAE J1777, tailored to the unique requirements of the Coast Guard. It includes additional testing and inspection procedures to ensure the fuel lines can withstand the demanding conditions of marine environments, including exposure to saltwater and varying temperatures.
Using the latest standard is crucial for safety and compliance. The USCG fuel line specifications are designed to prevent fuel leaks, ensure proper fuel flow, and maintain the integrity of the fuel system. Adhering to these standards helps minimize the risk of fires, explosions, and other hazards associated with marine fuel systems.