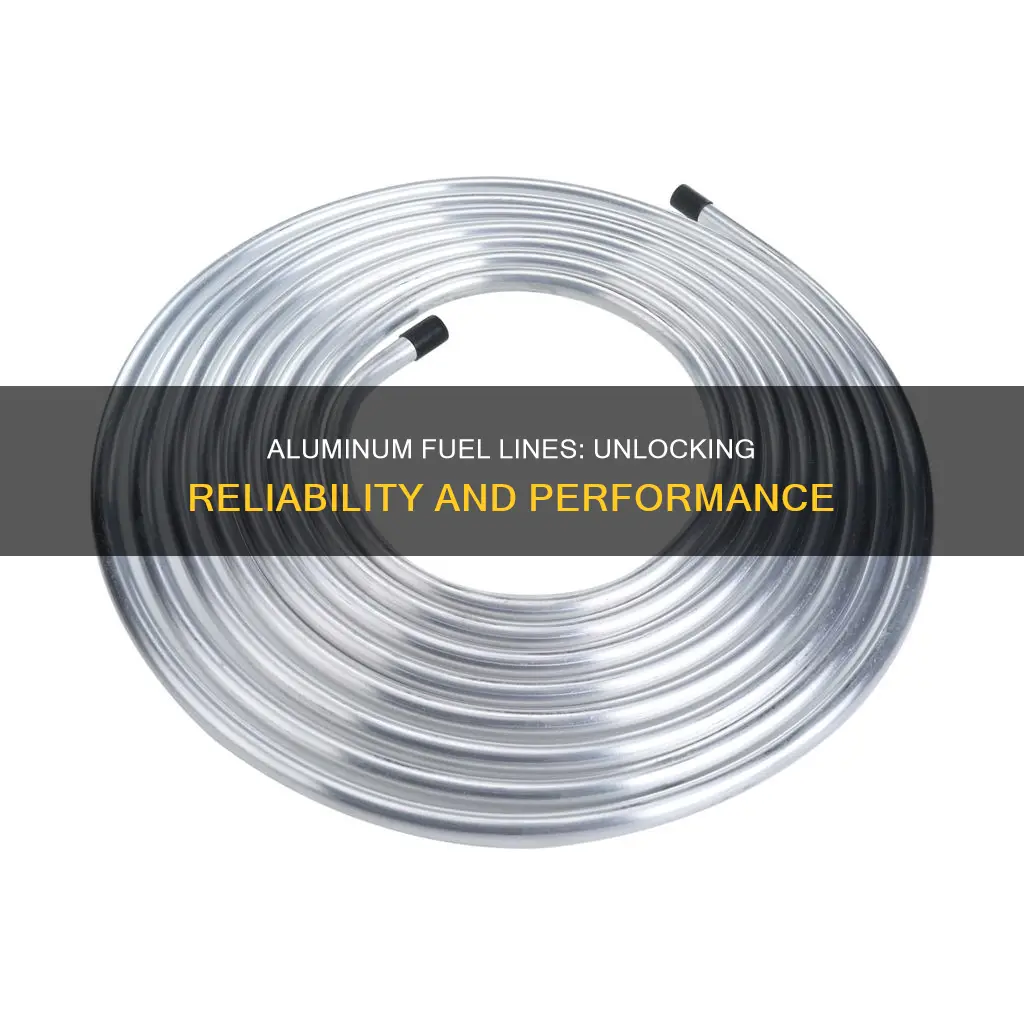
Aluminum fuel lines have become a popular choice for vehicle owners and mechanics alike due to their lightweight and corrosion-resistant properties. However, concerns about their reliability and longevity have often been raised. This paragraph aims to explore the reliability of aluminum fuel lines, examining their performance, durability, and potential maintenance requirements compared to traditional steel or rubber alternatives. By understanding the advantages and disadvantages, readers can make informed decisions about whether aluminum fuel lines are a suitable choice for their vehicles.
Characteristics | Values |
---|---|
Reliability | Aluminum fuel lines are generally considered reliable for fuel transport in vehicles, especially for non-critical applications. |
Corrosion Resistance | They offer good resistance to corrosion, which is beneficial for long-term use. |
Flexibility | These lines are flexible, allowing for easier installation and accommodating engine movements. |
Weight | Lighter than steel lines, reducing overall vehicle weight. |
Cost | Often more affordable compared to other materials. |
Availability | Widely available and easy to source. |
Temperature Tolerance | Can withstand moderate temperature variations but may not be suitable for extreme conditions. |
Compatibility | Compatible with various fuels, including gasoline and diesel. |
Maintenance | Requires minimal maintenance and is less prone to leaks. |
Durability | Less durable than some other materials but acceptable for standard use. |
Installation | Easy to install due to flexibility and lightweight. |
What You'll Learn
- Durability: Aluminum fuel lines are known for their resistance to corrosion and wear, ensuring long-lasting performance
- Flexibility: The material's flexibility allows it to withstand temperature changes without cracking, a key advantage over rigid lines
- Lightweight: Lighter than steel, aluminum lines reduce vehicle weight, improving fuel efficiency and handling
- Cost-Effective: Manufacturing and installation costs are lower, making it an affordable choice for many applications
- Maintenance: Easy to inspect and repair, aluminum lines require less maintenance over time compared to other materials
Durability: Aluminum fuel lines are known for their resistance to corrosion and wear, ensuring long-lasting performance
Aluminum fuel lines have earned a reputation for their exceptional durability, making them a reliable choice for various applications, especially in the automotive and marine industries. One of the key advantages of aluminum fuel lines is their inherent resistance to corrosion, which is a critical factor in maintaining the integrity of the fuel system over time. Unlike some other materials, aluminum does not readily corrode when exposed to fuel or the elements, ensuring that the fuel lines remain in optimal condition. This resistance to corrosion is particularly important in harsh environments or when using fuels with higher acidity levels, as it helps prevent the degradation of the fuel lines and the potential contamination of the fuel supply.
The durability of aluminum fuel lines is further enhanced by their ability to withstand wear and tear. These lines are designed to be flexible yet robust, allowing them to bend and move without compromising their structural integrity. This flexibility is especially beneficial in applications where the fuel lines need to navigate through tight spaces or accommodate the natural movement of vehicles or vessels. Despite their flexibility, aluminum fuel lines maintain their strength, ensuring that the fuel delivery system remains secure and reliable, even under constant stress.
In the automotive sector, where fuel lines are subjected to varying temperatures and road conditions, aluminum's durability is a significant advantage. The material's ability to resist wear and corrosion ensures that the fuel lines remain intact, preventing potential leaks or fuel contamination. This is crucial for maintaining engine performance and safety, as any compromise in the fuel system can lead to reduced power, increased emissions, or even engine failure.
For marine applications, the reliability of aluminum fuel lines is equally vital. In the harsh marine environment, where fuel lines are exposed to saltwater, UV radiation, and temperature fluctuations, aluminum's resistance to corrosion and wear becomes even more critical. Marine fuel lines made from aluminum can withstand the corrosive effects of saltwater, ensuring a consistent and reliable fuel supply to the engine, even in the most demanding conditions.
In summary, aluminum fuel lines are a reliable and durable solution for fuel delivery systems. Their resistance to corrosion and wear makes them an excellent choice for various industries, providing long-lasting performance and ensuring the safe and efficient operation of vehicles and marine vessels. With their ability to maintain structural integrity in challenging environments, aluminum fuel lines offer a cost-effective and dependable option for fuel line applications.
Understanding Trimmer Fuel Line Connections: A Guide to 358791580 Models
You may want to see also
Flexibility: The material's flexibility allows it to withstand temperature changes without cracking, a key advantage over rigid lines
The flexibility of aluminum fuel lines is a significant advantage over rigid alternatives, especially in applications where temperature variations are common. Aluminum, being a lightweight and highly malleable metal, offers a unique property that is crucial for the performance and longevity of fuel lines. This flexibility allows the lines to move and adapt to the natural expansion and contraction of the engine and surrounding components without the risk of cracking or breaking.
In automotive and marine environments, engines can experience rapid and significant temperature fluctuations. During operation, engines heat up, causing the engine block and associated components to expand. Conversely, when the engine is idling or off, these parts cool down, leading to contraction. Rigid fuel lines, typically made of steel or other less flexible materials, can become stressed and potentially crack under these temperature variations. This can result in fuel leaks, which are not only dangerous but can also lead to engine misfires and reduced performance.
Aluminum fuel lines, however, are designed to accommodate these changes. Their flexibility ensures that the lines remain intact and continue to deliver fuel efficiently, even when the engine is subjected to extreme temperatures. This is particularly important in high-performance vehicles or in climates where temperature extremes are common. The ability of aluminum lines to withstand these temperature changes without compromising their structural integrity is a key factor in their reliability and longevity.
Furthermore, the flexibility of aluminum fuel lines contributes to their overall durability. The material's ability to bend and move reduces the risk of damage from minor impacts or vibrations, which can occur during the normal operation of a vehicle. This added layer of protection ensures that the fuel lines remain in optimal condition, providing a consistent and reliable fuel supply to the engine.
In summary, the flexibility of aluminum fuel lines is a critical feature that enhances their reliability and performance. This property enables the lines to withstand temperature changes without cracking, ensuring a continuous and safe fuel supply to the engine. By choosing aluminum fuel lines, users can benefit from a more durable and efficient system, particularly in demanding environments where temperature variations are a constant challenge.
Understanding the 3/8 Fuel Line: A Comprehensive Guide
You may want to see also
Lightweight: Lighter than steel, aluminum lines reduce vehicle weight, improving fuel efficiency and handling
Aluminum fuel lines have gained popularity in the automotive industry due to their unique properties and advantages over traditional steel lines. One of the most significant benefits of aluminum is its lightweight nature, which plays a crucial role in enhancing vehicle performance and efficiency.
In the automotive world, weight reduction is a critical factor in improving overall vehicle dynamics. Aluminum fuel lines offer a substantial weight advantage over steel lines. Steel, being a denser material, contributes to a heavier vehicle, which can negatively impact fuel efficiency. By replacing steel with aluminum, vehicles can achieve a lighter overall weight, resulting in improved fuel efficiency. This is especially beneficial for high-performance cars and racing vehicles, where every pound saved can lead to better acceleration and handling. The reduced weight also allows for more responsive steering and improved cornering capabilities, making the vehicle more agile and enjoyable to drive.
The lightweight nature of aluminum fuel lines is a direct result of its lower density compared to steel. Aluminum's reduced weight translates to a more manageable and flexible fuel system, which can be particularly advantageous in tight spaces and under-the-hood configurations. This flexibility enables engineers to design more compact and efficient engine compartments, allowing for better engine cooling and improved overall aesthetics.
Furthermore, the weight reduction provided by aluminum lines contributes to better handling characteristics. Lighter fuel lines mean less unsprung weight, which directly affects the vehicle's suspension and overall ride quality. With reduced weight, the vehicle's suspension can react more quickly to road inputs, resulting in improved stability and responsiveness during cornering and acceleration. This enhanced handling performance is a significant advantage for both everyday driving and racing applications.
In summary, the lightweight nature of aluminum fuel lines is a key factor in their reliability and performance benefits. By reducing vehicle weight, aluminum lines contribute to improved fuel efficiency, handling, and overall driving experience. This makes aluminum fuel lines an attractive choice for automotive manufacturers seeking to optimize vehicle performance while maintaining reliability and safety.
Duramax Fuel Line Pressure: Testing and Troubleshooting Guide
You may want to see also
Cost-Effective: Manufacturing and installation costs are lower, making it an affordable choice for many applications
Aluminum fuel lines have gained popularity in various industries due to their cost-effectiveness and reliability. When compared to traditional fuel lines made of materials like steel or copper, aluminum offers significant advantages in terms of manufacturing and installation costs. This makes it an attractive option for a wide range of applications, especially in situations where budget constraints are a primary concern.
One of the primary reasons for the lower costs associated with aluminum fuel lines is the material itself. Aluminum is a lightweight and abundant metal, which makes it relatively inexpensive to produce. Its low density and ease of processing allow manufacturers to create fuel lines with minimal material waste, reducing production costs. Additionally, the manufacturing process for aluminum fuel lines is often more streamlined and less complex than that of other materials, further contributing to lower manufacturing expenses.
The cost-effectiveness of aluminum fuel lines extends to the installation process as well. Due to its lightweight nature, aluminum can be more easily manipulated and fitted into various systems, reducing the time and effort required for installation. This is particularly beneficial in applications where space is limited or access is challenging, as the flexibility and ease of installation of aluminum fuel lines can significantly impact project timelines and overall costs.
Furthermore, the affordability of aluminum fuel lines does not compromise their performance or durability. Despite being more cost-effective, aluminum fuel lines can still withstand the demands of their intended applications. They are resistant to corrosion, which is crucial for maintaining the integrity of the fuel system over time. Additionally, aluminum's lightweight nature can contribute to improved fuel efficiency in certain systems, offering a cost-saving benefit in the long run.
In summary, the cost-effectiveness of aluminum fuel lines is a result of the material's low production and installation costs, making it a practical choice for various projects. Its lightweight nature, ease of manufacturing, and installation, along with its durability and performance, ensure that it remains a reliable and affordable option for many applications, especially in industries where budget considerations are essential.
6AN 3/8 Stainless Braided Fuel Line: Ultimate Upgrade for Your Engine
You may want to see also
Maintenance: Easy to inspect and repair, aluminum lines require less maintenance over time compared to other materials
When it comes to the maintenance aspect of fuel lines, aluminum lines offer a significant advantage over their counterparts made from other materials. One of the primary reasons for this is their ease of inspection and repair. Aluminum fuel lines are designed with accessibility in mind, making it simpler for mechanics and vehicle owners to identify and address any potential issues.
The flexibility of aluminum is a key factor in its maintenance-friendly nature. Unlike rigid materials that may crack or become brittle over time, aluminum lines can bend and flex without compromising their structural integrity. This flexibility allows for easier installation and replacement, especially in tight spaces within an engine bay. When inspecting aluminum fuel lines, one can quickly identify any signs of damage or wear. The lines are less prone to developing leaks or cracks, which can be a common issue with other materials. A simple visual inspection can often reveal any potential problems, ensuring that maintenance tasks are swift and efficient.
Furthermore, the durability of aluminum contributes to its low-maintenance profile. Aluminum fuel lines are resistant to corrosion and oxidation, which are common causes of deterioration in other materials. This resistance means that aluminum lines can withstand the harsh conditions within an engine compartment, including exposure to heat, fuel vapors, and various chemicals. As a result, they require fewer replacements and repairs, saving both time and money in the long run.
In terms of repair, aluminum fuel lines are highly compatible with common automotive repair techniques. Mechanics can easily cut, bend, and join aluminum lines using standard tools and methods. This accessibility and ease of repair further emphasize the reliability and low-maintenance nature of aluminum fuel lines. Additionally, the availability of replacement parts and the expertise of mechanics in working with aluminum make it a convenient choice for vehicle owners.
In summary, the maintenance requirements for aluminum fuel lines are notably lower compared to other materials due to their ease of inspection and repair. The flexibility, durability, and compatibility with common repair techniques make aluminum lines a reliable and cost-effective choice for fuel line systems. This aspect of aluminum's reliability is particularly valuable for vehicle owners and mechanics seeking efficient and long-lasting solutions for their automotive needs.
Automotive Fuel Line: Unraveling the Mystery of ID vs. OD
You may want to see also
Frequently asked questions
Aluminum fuel lines are a popular choice for many vehicle owners due to their lightweight and corrosion-resistant properties. They are often used as an upgrade to the traditional steel fuel lines, offering improved flexibility and a longer lifespan. The material's ability to resist corrosion ensures that the fuel lines remain in good condition, even in harsh environments, making it a reliable option for both daily drivers and high-performance vehicles.
Aluminum fuel lines are generally considered more reliable than steel in many aspects. Steel lines can be prone to rust and corrosion, especially in areas with high humidity or salt exposure, which can lead to leaks and reduced fuel efficiency. Aluminum, being lighter and more resistant to corrosion, provides a longer-lasting solution, ensuring a consistent and reliable fuel supply to the engine.
Yes, aluminum fuel lines are versatile and can be used in a wide range of vehicles, from cars and trucks to motorcycles and boats. Their compatibility and ease of installation make them a preferred choice for many automotive enthusiasts and professionals. However, it's important to ensure that the vehicle's fuel system and engine components are designed to accommodate aluminum lines to avoid any potential issues.
While aluminum fuel lines offer numerous benefits, there might be a slight trade-off in terms of cost. Aluminum lines can be more expensive than steel alternatives, which may be a consideration for budget-conscious buyers. Additionally, in extremely cold climates, aluminum's lower melting point could be a concern, but this is typically mitigated by using thicker-walled lines or adding insulation. Overall, the reliability and performance advantages often outweigh these minor drawbacks.