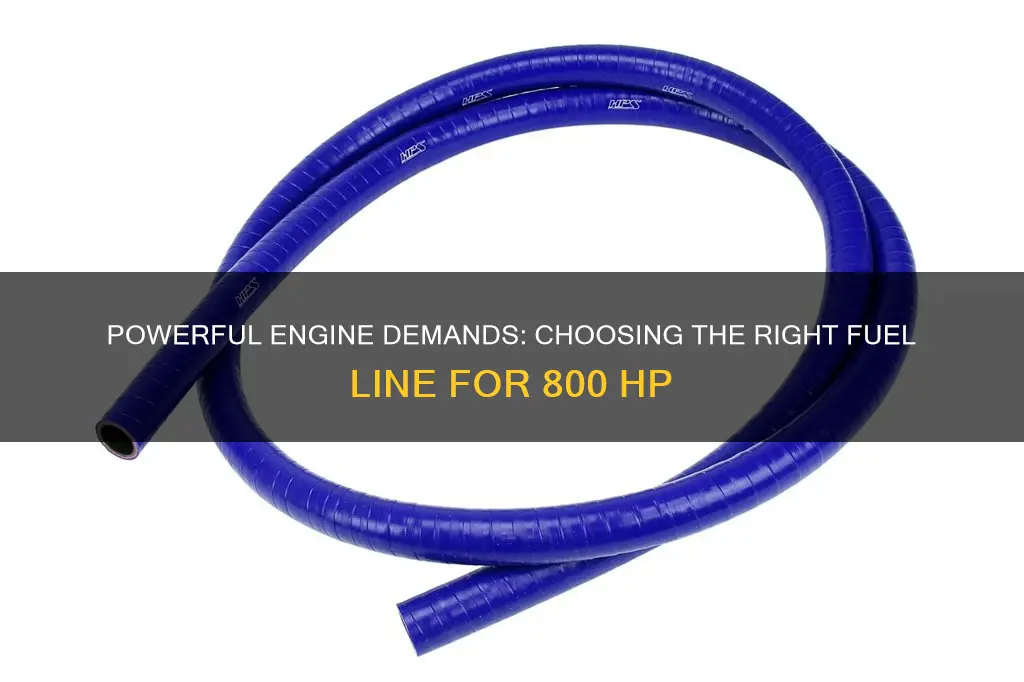
When building a high-performance vehicle capable of generating 800 horsepower, one of the critical aspects to consider is the fuel system. The fuel line plays a vital role in delivering the necessary fuel to the engine, and choosing the right size is crucial for optimal performance. This paragraph will explore the considerations and guidelines for selecting the appropriate fuel line size to ensure efficient and reliable fuel delivery to the wheels of such a powerful vehicle.
What You'll Learn
- Engine Power: Determine the required fuel flow rate for 800 hp
- Line Diameter: Choose a line diameter to handle the fuel pressure and flow
- Length: Calculate the optimal length for the fuel line
- Material: Select a suitable material for durability and performance
- Routing: Plan the fuel line route to avoid interference and ensure safety
Engine Power: Determine the required fuel flow rate for 800 hp
To determine the required fuel flow rate for an 800-horsepower engine, we need to consider several factors that influence the engine's performance and fuel consumption. Here's a detailed breakdown:
Engine Efficiency and Power Output: The first step is to understand the engine's efficiency and power output characteristics. Different engines have varying power curves, indicating how fuel is converted into horsepower. For an 800-hp engine, we need to refer to the manufacturer's data or conduct testing to determine the specific power output at different RPM (revolutions per minute) ranges. This data will help us establish a relationship between engine speed and fuel consumption.
Fuel Injection and Delivery System: The fuel injection system plays a critical role in delivering the required fuel to the engine. The system's design, including the type of injectors, fuel pumps, and pressure regulators, will impact the fuel flow rate. Modern engines often employ electronic fuel injection, which precisely controls the fuel-air mixture. Understanding the injection system's capabilities and limitations is essential to ensure the engine receives the correct amount of fuel for optimal performance.
Engine Load and Operating Conditions: Engine load and operating conditions significantly affect fuel consumption. During high-load situations, such as acceleration or climbing, the engine requires more fuel to meet the increased power demand. Conversely, during cruising or idling, the engine's fuel consumption decreases. To determine the required fuel flow rate, we must consider the typical operating conditions and loads the engine will experience. This includes accounting for factors like gear ratios, transmission efficiency, and the vehicle's overall design.
Fuel Line Sizing and Pressure: The size of the fuel line is crucial in ensuring the engine receives the necessary fuel flow rate. Fuel lines should be sized appropriately to handle the required fuel pressure and volume. Engineers often use fuel flow rate calculations, considering factors like fuel line diameter, length, and pressure drop, to determine the appropriate fuel line size. This calculation ensures that the fuel can be delivered efficiently to the engine, meeting its power requirements without excessive pressure drops or fuel degradation.
Testing and Calibration: In practice, determining the exact fuel flow rate for an 800-hp engine may require testing and calibration. This involves monitoring the engine's performance under various conditions and adjusting the fuel injection system accordingly. By comparing the measured fuel consumption with the desired power output, engineers can fine-tune the system to achieve the required fuel flow rate. This process ensures that the engine operates optimally and delivers the specified horsepower while maintaining efficiency and performance.
Choosing the Right B Nut for 3/4 Inch Fuel Lines
You may want to see also
Line Diameter: Choose a line diameter to handle the fuel pressure and flow
When dealing with high-performance vehicles, especially those producing 800 horsepower, the fuel system becomes a critical component. One of the most important aspects of this system is the fuel line diameter, which plays a crucial role in ensuring optimal performance and reliability. Choosing the right line diameter is essential to handle the increased fuel pressure and flow rates associated with powerful engines.
The fuel line diameter refers to the thickness or size of the fuel line, typically measured in inches or millimeters. It is a fundamental factor in determining the line's ability to manage fuel efficiently and effectively. For an 800-horsepower engine, a larger line diameter is generally recommended to accommodate the higher fuel requirements. A smaller diameter line may restrict fuel flow, leading to potential performance issues and reduced power output.
To determine the appropriate line diameter, consider the fuel pressure and flow rate. High-performance engines often operate at elevated fuel pressures to ensure efficient combustion. As the pressure increases, so does the required flow rate of fuel to meet the engine's demands. A larger diameter line can handle higher pressure and provide a smoother, more consistent fuel supply, which is crucial for maintaining power and preventing fuel-related issues.
A common rule of thumb is to use a fuel line diameter that is at least 1/4 inch (6.35 mm) for every 100 horsepower. For an 800-horsepower engine, this would translate to a line diameter of approximately 8 inches (203.2 mm) or larger. However, it's important to note that this is a general guideline, and the specific requirements may vary depending on the engine design, fuel pump specifications, and overall system setup. Consulting the vehicle's manual or seeking advice from experienced mechanics is essential to ensure the correct line diameter is chosen.
In summary, when dealing with an 800-horsepower engine, selecting an appropriate fuel line diameter is vital for optimal performance. A larger diameter line is necessary to handle the increased fuel pressure and flow, ensuring a reliable and efficient fuel supply to the engine. Properly sizing the fuel line is a critical aspect of building or modifying a high-performance vehicle to meet its full potential.
Choosing the Right Hose for Your 1.4-Inch Fuel Line
You may want to see also
Length: Calculate the optimal length for the fuel line
When dealing with high-performance vehicles, ensuring efficient and reliable fuel delivery is crucial, especially for those pushing the boundaries with 800 horsepower to the wheels. The fuel line, a critical component in this setup, plays a vital role in maintaining performance and safety. The length of the fuel line is a critical factor that can significantly impact the system's efficiency and reliability.
To calculate the optimal length, several factors need to be considered. Firstly, the distance between the fuel tank and the engine is a primary concern. For an 800-horsepower vehicle, the engine's power and the associated heat generation should be taken into account. Longer distances may require larger-diameter fuel lines to compensate for potential pressure drops, ensuring a consistent fuel supply. It is essential to strike a balance between the line's length and diameter to maintain optimal performance.
The fuel line's material is another critical aspect. High-performance applications often utilize materials like stainless steel or aluminum, which offer superior durability and resistance to heat and pressure. These materials can handle the demanding conditions associated with powerful engines, ensuring a long-lasting and reliable fuel supply. The choice of material should be based on the specific requirements of the vehicle and the expected operating environment.
Additionally, the fuel line's bend radius is a critical consideration. Bends and turns in the line should be minimized to avoid restrictions and potential fuel flow issues. The bend radius should be at least 1.5 times the diameter of the fuel line to ensure smooth and unobstructed fuel flow. Proper routing and support of the fuel line are essential to prevent damage and maintain optimal performance.
In summary, calculating the optimal length for the fuel line involves considering the distance between the fuel source and the engine, selecting appropriate materials, and ensuring proper bend radii. By carefully evaluating these factors, enthusiasts and professionals can design a fuel system that meets the demands of an 800-horsepower vehicle, ensuring efficient power delivery and a reliable fuel supply. This attention to detail is crucial for maximizing performance and minimizing potential issues in high-performance automotive applications.
Mastering Fuel Injection: Hard Line Strategies for Optimal Performance
You may want to see also
Material: Select a suitable material for durability and performance
When it comes to selecting the right material for fuel lines in a high-performance vehicle, such as one generating 800 horsepower to the wheels, durability and performance are paramount. The material choice will significantly impact the fuel line's ability to withstand the rigors of high-performance driving, including extreme temperatures, pressure, and vibrations.
One of the most commonly used materials for fuel lines in racing and high-performance applications is stainless steel. This material offers exceptional strength and corrosion resistance, making it ideal for withstanding the harsh conditions of high-horsepower engines. Stainless steel fuel lines are known for their flexibility, allowing them to navigate through tight spaces and engine compartments without becoming brittle or prone to cracking. Additionally, the material's inherent durability ensures that the fuel lines can handle the high-pressure fuel environment without compromising performance or safety.
Another excellent option for high-performance fuel lines is braided stainless steel. This material combines the flexibility of a synthetic braid with the strength and corrosion resistance of stainless steel. The braided construction provides excellent flexibility, making it easy to route the fuel lines through the engine bay. The stainless steel core ensures that the fuel lines can handle high-pressure fuel without any loss of performance. This combination of flexibility and strength is crucial for maintaining a reliable fuel supply to the engine, especially in high-performance applications.
For those seeking a more lightweight option, aluminum fuel lines can be a viable choice. Aluminum offers a significant weight reduction compared to stainless steel, which is beneficial for high-performance vehicles where weight is a critical factor. However, it's important to note that aluminum fuel lines may require additional protection to prevent corrosion, as the material is more susceptible to oxidation. Proper coating or the use of aluminum-specific sealants can help mitigate this issue.
In summary, when selecting the material for fuel lines in a high-performance vehicle, it is essential to prioritize durability and performance. Stainless steel and braided stainless steel are excellent choices due to their strength, flexibility, and resistance to corrosion. For those seeking a lightweight option, aluminum can be considered, but with the necessary precautions to ensure long-term reliability. The right material choice will ensure a consistent and reliable fuel supply to the engine, contributing to the overall performance and success of the vehicle.
Chevy 49 Fuel Line: Size and Compatibility Guide
You may want to see also
Routing: Plan the fuel line route to avoid interference and ensure safety
When designing the fuel line routing for a high-performance vehicle with an 800-horsepower engine, careful planning is essential to ensure optimal performance and safety. The primary goal is to minimize fuel pressure drop and maintain a consistent fuel supply to the engine while avoiding potential hazards. Here's a detailed guide on how to approach this:
Understanding the Basics: Begin by familiarizing yourself with the vehicle's fuel system specifications. This includes knowing the fuel pump's capacity, the required fuel pressure, and the type of fuel injectors used. Different engines may have unique requirements, so it's crucial to consult the vehicle's manual or seek expert advice. For instance, a high-performance engine might demand a specific fuel line diameter to handle the increased power output without compromising efficiency.
Route Planning: The fuel line route should be carefully planned to avoid any potential interference with other components. Here are some key considerations:
- Clearance from Moving Parts: Ensure the fuel line is positioned away from areas where it could be damaged by moving engine parts. This is especially important for high-performance vehicles with aggressive engine mounts and suspension systems.
- Heat Management: Keep the fuel line away from hot engine components to prevent fuel degradation and potential safety hazards. Consider using heat shields or insulation if necessary.
- Underbody Routing: If the fuel tank is located under the vehicle, plan the route to avoid sharp bends or kinks that could lead to fuel contamination or reduced flow.
- Access and Maintenance: Design the route to allow easy access for maintenance and fuel filter changes. This is crucial for regular servicing and ensuring the long-term health of the fuel system.
Material Selection: Choosing the right material for the fuel line is vital. High-performance applications often require fuel lines with a higher pressure rating and flexibility. Consider materials like stainless steel or braided rubber hoses that can withstand the demands of a powerful engine.
Safety Considerations: Safety should always be a top priority. Ensure that the fuel line routing does not pose a fire hazard or interfere with emergency equipment. In high-performance vehicles, it's common to use fuel line protectors or shields to safeguard against potential impacts or road debris.
By meticulously planning the fuel line route, you can ensure that the 800-horsepower engine receives the necessary fuel supply while maintaining a safe and efficient system. This level of detail is crucial for any high-performance vehicle owner or mechanic to optimize performance and longevity.
Understanding Rubber Fuel Line Sizes for CJ7s
You may want to see also
Frequently asked questions
The fuel line size depends on various factors, including the engine's power output, fuel pump capacity, and desired flow rate. For an 800-hp engine, a fuel line diameter of 1/2 inch to 3/4 inch is often recommended to handle the high fuel pressure and volume required for optimal performance.
The length of the fuel line should be sufficient to reach from the fuel pump to the engine's fuel injectors or carburetor without excessive bends or restrictions. A general rule of thumb is to keep the fuel line as straight as possible and limit the total length to 10-15 feet. Consider the engine's mounting position and the vehicle's design to ensure a clean and efficient route for the fuel line.
Yes, high-performance fuel lines often use materials like stainless steel or braided nylon to withstand high pressure and temperature. Some manufacturers also offer fuel lines with a protective coating or inner lining to reduce fuel evaporation and improve overall efficiency. These specialized materials can enhance the fuel line's durability and performance in demanding applications.
Using an undersized fuel line can lead to several issues, including reduced fuel flow, engine misfires, and decreased power output. The engine may not receive the required amount of fuel at the right pressure, resulting in poor performance and potential damage over time. It is crucial to select the appropriate fuel line size to ensure the engine operates efficiently and reliably.