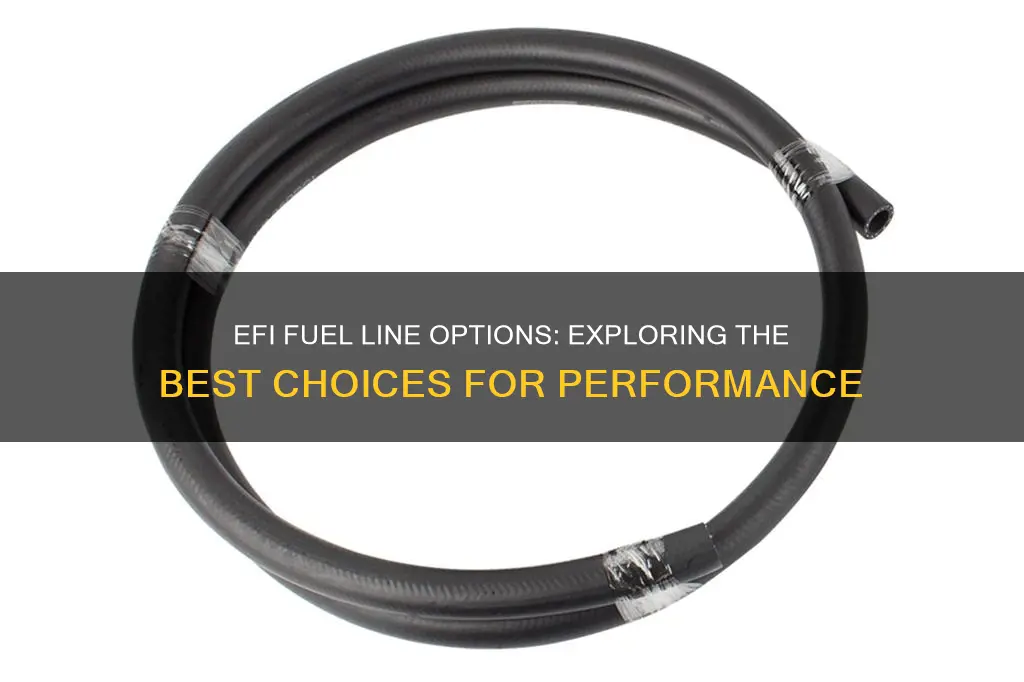
When it comes to fuel lines for EFI (Electronic Fuel Injection) systems, there are several options available, each with its own advantages and disadvantages. Some popular choices include braided steel fuel lines, which offer durability and resistance to heat and pressure, making them a common choice for high-performance applications. On the other hand, rubber fuel lines are more flexible and easier to install, but they may not be as durable as braided steel lines. Additionally, there are also silicone fuel lines, which provide excellent heat resistance and flexibility, making them suitable for a wide range of vehicles. The choice of fuel line material depends on factors such as the vehicle's performance requirements, climate conditions, and personal preferences.
What You'll Learn
- Material: Choose between rubber, silicone, or braided fuel lines
- Diameter: Select the appropriate size based on flow rate and pressure
- Compatibility: Ensure the fuel lines are compatible with the fuel type
- Routing: Plan the optimal path for fuel lines to avoid interference
- Connectors: Consider the type of connectors for easy installation and removal
Material: Choose between rubber, silicone, or braided fuel lines
When it comes to choosing the right material for fuel lines on an Electronic Fuel Injection (EFI) system, you have a few options to consider, each with its own advantages and use cases. The primary materials you'll come across are rubber, silicone, and braided fuel lines.
Rubber Fuel Lines:
Rubber has been a traditional choice for fuel lines due to its affordability and ease of installation. It is flexible and can withstand moderate temperatures, making it suitable for most automotive applications. Rubber fuel lines are known for their durability and resistance to fuel degradation. They are less prone to cracking and can handle the pressure of fuel injection systems. However, rubber may not be the best choice for high-performance vehicles or those operating in extreme temperatures. Over time, rubber can become brittle and may not perform as well as other materials under certain conditions.
Silicone Fuel Lines:
Silicone is a popular upgrade for fuel lines, especially in high-performance and modified vehicles. It offers superior flexibility and temperature resistance compared to rubber. Silicone fuel lines can handle extreme temperatures, making them ideal for racing or vehicles operating in harsh environments. This material is also known for its chemical resistance, ensuring that it remains stable even when exposed to various fuels. Silicone lines are more expensive than rubber but provide excellent long-term reliability and performance. They are less likely to become brittle and can withstand the high pressures associated with EFI systems.
Braided Fuel Lines:
Braided fuel lines are a premium option, often used in high-performance and racing applications. These lines consist of multiple layers of braided material, typically silicone or rubber, which provides exceptional flexibility and strength. Braided lines offer superior resistance to fuel degradation and can handle extremely high pressures. They are an excellent choice for vehicles that require precise fuel delivery and maximum performance. While braided lines are more expensive, they provide the best combination of flexibility, strength, and resistance to fuel-related degradation.
The choice between these materials depends on the specific requirements of your vehicle and the conditions it operates in. For everyday use, rubber or silicone lines can provide a cost-effective solution. However, for high-performance or modified vehicles, silicone or braided fuel lines are recommended to ensure optimal performance and longevity. It's essential to consider the temperature range, fuel type, and the overall performance expectations of your vehicle when making this decision.
Unveiling the Material Secrets of Metal Fuel Lines
You may want to see also
Diameter: Select the appropriate size based on flow rate and pressure
When it comes to selecting the appropriate diameter for fuel lines in an Electronic Fuel Injection (EFI) system, it's crucial to consider the flow rate and pressure requirements. The diameter of the fuel line plays a significant role in ensuring efficient and reliable fuel delivery to the engine. Here's a detailed guide on how to determine the right diameter:
Flow Rate and Pressure Considerations: The flow rate, which is the volume of fuel passing through the line per unit of time, and the pressure requirements are the primary factors in selecting the diameter. Higher flow rates typically demand larger diameters to accommodate the increased volume of fuel. This is because a larger pipe provides a greater cross-sectional area, allowing more fuel to pass through with each pulse. For instance, if your engine requires a high-performance fuel injection system, you'll need a larger diameter to handle the increased fuel flow. On the other hand, lower flow rates might allow for smaller diameters, but it's essential to ensure that the pressure drop across the line remains within acceptable limits.
Calculating the Required Diameter: To determine the appropriate diameter, you can use the Darcy-Weisbach equation, which relates the pressure drop across a pipe to the flow rate, pipe diameter, and other factors. This equation can be complex, but it provides a scientific approach to sizing the fuel lines. Alternatively, you can refer to industry standards and guidelines, which often provide recommended diameters based on specific flow rates and pressure differentials. These standards can be a valuable resource for ensuring optimal performance and safety.
Practical Experience and Testing: In practice, selecting the right diameter often involves a combination of theoretical calculations and practical experience. Many enthusiasts and professionals recommend testing different diameters to observe their performance in real-world conditions. This iterative process allows for adjustments until the desired balance between flow rate, pressure, and efficiency is achieved. It's also essential to consider the material of the fuel line, as different materials have varying flow characteristics and pressure tolerances.
Common Sizes and Considerations: Standard fuel line diameters for EFI systems often range from 3/8" to 1/2" (9.5 to 12.7 mm). However, these sizes can vary based on the specific application and engine requirements. For high-performance applications, larger diameters like 3/4" or even 1" (19.1 or 25.4 mm) might be used. It's crucial to remember that larger diameters offer better flow characteristics but may also increase the system's overall size and weight. Smaller diameters are more compact but might not handle high flow rates efficiently.
In summary, selecting the appropriate diameter for fuel lines in an EFI system is a critical aspect of engine performance and reliability. By carefully considering the flow rate and pressure requirements, and utilizing the right tools and guidelines, you can ensure that your fuel lines deliver the necessary fuel efficiently and effectively to your engine.
Unleash the Power: Breaking Fuel Lines: A Quarry Decision
You may want to see also
Compatibility: Ensure the fuel lines are compatible with the fuel type
When it comes to fuel lines for EFI (Electronic Fuel Injection) systems, compatibility is a critical factor to consider. The fuel lines play a vital role in delivering the correct fuel mixture to the engine, and using the right type of fuel lines ensures optimal performance and longevity of the vehicle. Here's a detailed guide on how to ensure compatibility:
Understanding Fuel Types: Different vehicles use various types of fuel, such as gasoline, diesel, or alternative fuels like ethanol blends. It's essential to know the specific fuel type your vehicle requires. For instance, gasoline engines typically use conventional gasoline, while some vehicles might utilize ethanol-blended fuels. Understanding the fuel type is the first step in selecting the appropriate fuel lines.
Checking Fuel Line Materials: Fuel lines are usually made from specific materials to withstand the properties of the fuel they carry. For gasoline applications, rubber or synthetic rubber-like materials are commonly used due to their flexibility and resistance to gasoline degradation. In contrast, diesel fuel lines often employ materials like nylon or braided steel to handle the higher pressure and temperature requirements. Always check the fuel line material to ensure it is compatible with the fuel type.
Considering Fuel Line Diameter: The diameter of the fuel line is another crucial aspect. EFI systems require precise fuel delivery, and the line's diameter should match the engine's requirements. Smaller diameters might be used for high-pressure applications, while larger diameters can handle lower pressure. Ensure that the chosen fuel line diameter aligns with the engine's specifications to maintain efficient fuel flow.
Checking for Compatibility with EFI System: EFI systems have specific requirements for fuel delivery, including pressure and flow rates. The fuel lines should be compatible with these parameters to ensure accurate fuel injection. Some vehicles might have unique EFI setups, so it's essential to consult the vehicle's manual or seek expert advice to determine the compatible fuel line specifications.
By carefully considering the fuel type, material, diameter, and EFI system compatibility, you can select the right fuel lines for your vehicle. This ensures that the engine receives the appropriate fuel mixture, leading to improved performance, fuel efficiency, and overall engine health. Always refer to the vehicle's manual or consult with professionals for the most accurate and compatible fuel line choices.
Braided Fuel Line Protection: Sealing the Deal
You may want to see also
Routing: Plan the optimal path for fuel lines to avoid interference
When planning the routing of fuel lines for an Electronic Fuel Injection (EFI) system, it's crucial to prioritize optimal flow and minimize potential interference. The goal is to ensure that the fuel lines are positioned in a way that allows for efficient delivery of fuel to the engine while avoiding any obstructions or complications. Here's a detailed guide on how to approach this task:
Understanding the Layout: Begin by thoroughly examining the engine bay and the layout of the vehicle's components. Identify the locations of the fuel tank, fuel pump, and the engine's fuel injectors. Understanding the spatial arrangement of these elements is key to planning an efficient route for the fuel lines. Look for any existing wiring harnesses, pipes, or other components that might interfere with the desired path.
Minimizing Twists and Turns: Fuel lines should be routed in a straight and direct manner whenever possible. Twists and turns can lead to reduced flow efficiency and potential fuel pressure drops. Aim to keep the lines as straight as the vehicle's structure allows. For example, if the fuel pump is located near the front of the engine bay, consider running the line along the firewall or towards the front of the vehicle to maintain a straight path.
Avoiding Interference: One of the critical aspects of routing is to prevent interference with other components. Fuel lines should not cross or rub against moving parts, such as engine components, exhaust systems, or suspension elements. Proper clearance is essential to avoid damage and ensure reliable operation. For instance, if the fuel line needs to cross a suspension arm, ensure there is sufficient space to prevent any potential damage during vehicle movement.
Using Appropriate Materials: Choose the right materials for the fuel lines to ensure durability and compatibility. High-quality rubber or synthetic materials are commonly used for their flexibility and resistance to fuel degradation. Ensure that the chosen material can withstand the temperature and pressure variations within the engine bay. Additionally, consider using protective sleeves or shielding to further safeguard the fuel lines from potential impacts or abrasions.
Organized Routing: Maintain a neat and organized routing system to facilitate future maintenance and troubleshooting. Labeling the fuel lines with their respective sources and destinations can be helpful. This practice ensures that any issues or adjustments can be made efficiently without causing unnecessary complications. Proper organization also contributes to a cleaner and more professional-looking engine bay.
By following these guidelines, you can effectively plan the routing of fuel lines for an EFI system, ensuring optimal performance, reliability, and longevity of the fuel delivery system. Remember, each vehicle may present unique challenges, so adapting these principles to the specific make and model is essential.
Unveiling the Material Secrets of Diesel Fuel Lines
You may want to see also
Connectors: Consider the type of connectors for easy installation and removal
When it comes to fuel lines on an Electronic Fuel Injection (EFI) system, the choice of connectors is an important consideration for any vehicle enthusiast or mechanic. The right connectors can make the installation process seamless and ensure optimal performance. Here's a detailed look at why connector selection is crucial:
Compatibility and Ease of Use: The primary goal is to ensure that the fuel lines are easily connected and disconnected for maintenance and repairs. Look for connectors that are designed specifically for fuel lines in EFI systems. These connectors often feature a quick-connect/quick-release mechanism, allowing for swift installation and removal without the need for specialized tools. This ease of use is particularly beneficial when dealing with time-sensitive repairs or when multiple fuel lines need to be connected or disconnected frequently.
Durability and Material Quality: Fuel lines are exposed to various environmental factors, including heat, vibration, and fuel contaminants. Therefore, the connectors should be made from durable materials that can withstand these conditions. High-quality connectors often use materials like brass, stainless steel, or reinforced rubber, ensuring longevity and resistance to corrosion. This durability is essential to prevent fuel leaks and maintain the integrity of the EFI system.
Sealing and Leak Prevention: Proper sealing is critical to prevent fuel leaks and ensure the system's reliability. Look for connectors with robust O-rings or gaskets that create a tight seal between the fuel line and the connector. This sealing mechanism should be able to withstand the pressure and temperature variations within the fuel system. Well-sealed connectors minimize the risk of fuel escaping, which could lead to engine performance issues and potential safety hazards.
Flexibility and Routing: Consider the flexibility of the connectors, especially when routing fuel lines through tight spaces or under the vehicle's body. Connectors that offer some flexibility will make it easier to navigate around obstacles without compromising the fuel line's integrity. This is particularly important in custom builds or when retrofitting older vehicles with EFI systems.
Standardization and Availability: Opt for connectors that are widely available and standardized across various vehicle makes and models. This ensures that replacement parts are easily accessible and cost-effective. Standardized connectors also simplify the installation process, as you won't need to source specific connectors for your vehicle, saving time and effort.
In summary, when dealing with fuel lines on an EFI system, the choice of connectors is a critical aspect. It directly impacts the ease of installation, durability, and overall performance of the fuel system. By considering the compatibility, durability, sealing properties, flexibility, and standardization of connectors, you can ensure a reliable and efficient fuel delivery system for your vehicle.
Unleash Your Engine's Potential: Understanding the 8AM Fuel Line
You may want to see also
Frequently asked questions
For EFI systems, the most common type of fuel lines used are braided steel fuel lines. These lines are known for their durability, flexibility, and resistance to fuel contamination. They are designed to withstand high pressure and temperature changes, making them ideal for fuel delivery in modern engines.
Yes, the material of the fuel line is crucial. Braided steel lines are preferred as they offer excellent protection against fuel contamination and can handle the high pressure and temperature variations in EFI systems. Some manufacturers also use rubber or silicone-coated lines, but these are less common and may not be suitable for high-performance applications.
The size of the fuel line depends on the engine's power output and the flow rate required. Typically, larger engines with higher horsepower output will require larger-diameter fuel lines to ensure sufficient fuel delivery. It's essential to consult the vehicle's manual or seek advice from an automotive specialist to determine the appropriate size.
It is not recommended to use regular fuel lines without modifications. Regular fuel lines may not have the same level of protection against fuel contamination and may not withstand the high pressure and temperature changes associated with EFI systems. Using the correct type of braided steel fuel lines is essential for optimal performance and longevity.
Fuel line filters are crucial components in EFI systems. They are installed between the fuel pump and the engine to prevent contaminants like dirt, water, and debris from entering the fuel system. These filters ensure clean fuel delivery, which is vital for maintaining engine performance and preventing potential damage to the fuel injectors.