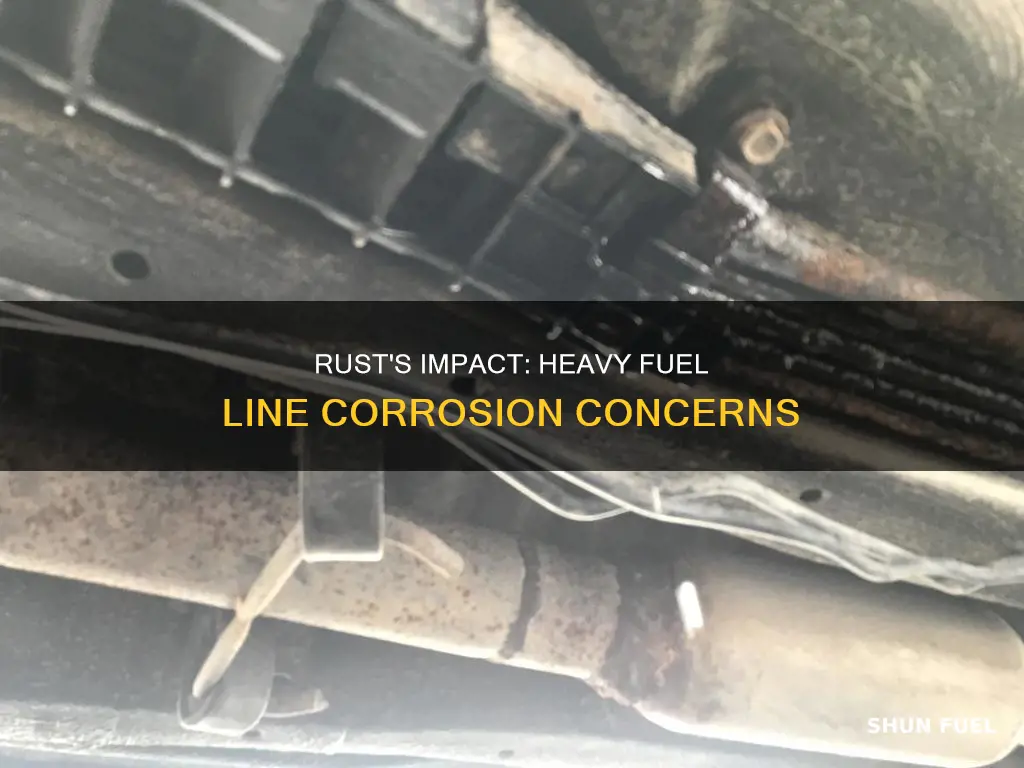
Heavy rust on fuel lines can be a serious issue for vehicle owners, as it can lead to a variety of problems. Rust can cause fuel leaks, which can be dangerous and costly to repair. It can also lead to reduced engine performance and fuel efficiency. In this article, we will explore the causes of heavy rust on fuel lines, the potential consequences, and how to prevent and treat this issue.
Characteristics | Values |
---|---|
Potential Causes | Corrosion, moisture, fuel contamination, old age of the vehicle |
Symptoms | Fuel leaks, engine misfires, reduced performance, hard starting, unusual noises |
Health Risks | Engine damage, fire hazard, environmental pollution |
Diagnosis | Visual inspection, pressure testing, fuel line replacement |
Prevention | Regular maintenance, fuel line coating, using fuel stabilizers |
Treatment | Cleaning, replacing affected sections, using rust inhibitors |
Cost | Varies; can range from minor repairs to major engine overhauls |
Legal Considerations | May require professional inspection and documentation |
What You'll Learn
- Fuel Line Material: Heavy rust on fuel lines is often caused by materials like steel or iron
- Corrosion Prevention: Regular maintenance and corrosion inhibitors can prevent heavy rust
- Fuel Quality: Contaminated fuel can accelerate rust formation on fuel lines
- Environmental Factors: Moisture and temperature changes can contribute to heavy rust
- Fuel System Design: Proper design and materials can reduce the risk of heavy rust
Fuel Line Material: Heavy rust on fuel lines is often caused by materials like steel or iron
Heavy rust on fuel lines is a common issue that can lead to significant problems for vehicle owners. This phenomenon is often associated with the material composition of the fuel lines themselves. When it comes to fuel lines, the primary materials used historically have been steel and iron. These metals, while durable, are susceptible to corrosion when exposed to certain environmental factors.
The presence of heavy rust on fuel lines is primarily due to the natural process of oxidation. When steel or iron fuel lines are exposed to moisture, especially in the presence of oxygen, they can undergo a chemical reaction that forms rust. This is a common occurrence in older vehicles or those that have been stored in humid environments. Over time, the rust can spread, leading to a buildup that may compromise the structural integrity of the fuel lines.
The impact of heavy rust on fuel lines can be detrimental. As the rust accumulates, it can create a layer of insulation around the fuel line, reducing its diameter and restricting the flow of fuel. This restriction can lead to reduced engine performance, as the engine may not receive the required amount of fuel. In some cases, the rust can also lead to fuel leaks, which can be dangerous and cause environmental damage.
To address this issue, it is essential to inspect and maintain fuel lines regularly. For older vehicles or those with a history of rust issues, it is recommended to use fuel lines made from alternative materials that are more resistant to corrosion. Modern vehicles often utilize materials like copper or synthetic compounds that are less prone to rust formation.
In summary, heavy rust on fuel lines is often a result of the material composition, particularly steel or iron. This issue can cause engine performance problems and potential fuel leaks. Regular maintenance and the use of more corrosion-resistant materials can help mitigate these risks and ensure the longevity of the vehicle's fuel system.
Optimizing Performance: Choosing the Right Fuel Line for Your Yamaha F225 Outboard
You may want to see also
Corrosion Prevention: Regular maintenance and corrosion inhibitors can prevent heavy rust
Corrosion, especially heavy rust, on fuel lines can be a significant issue for vehicle owners and operators. It is a common problem that can lead to various performance issues and even safety hazards. The presence of rust can cause blockages, reduce fuel flow, and even lead to fuel leaks, which can have detrimental effects on engine performance and overall vehicle safety. Therefore, implementing effective corrosion prevention measures is crucial to maintaining a reliable and safe fuel system.
Regular maintenance is a fundamental aspect of corrosion prevention. It involves routine inspections and checks to identify any signs of rust or corrosion on the fuel lines. During these inspections, it is essential to look for any discolouration, pitting, or flaking of the fuel line material. Over time, fuel lines can degrade due to the corrosive effects of fuel, especially in vehicles with older fuel systems. Regular maintenance allows for the early detection of these issues, enabling prompt action to prevent further corrosion.
One of the most effective methods to combat heavy rust is the use of corrosion inhibitors. These are specialized additives designed to protect metal surfaces from corrosion. When added to the fuel, these inhibitors create a protective layer on the fuel lines, preventing direct contact between the fuel and the metal. This barrier effect helps to inhibit the electrochemical corrosion process, which is the primary cause of rust formation. Corrosion inhibitors are particularly useful in older vehicles or those with fuel systems that are more susceptible to corrosion.
In addition to inhibitors, maintaining a clean fuel system is essential. Over time, fuel can accumulate contaminants, such as water, dirt, and debris, which can accelerate corrosion. Regular fuel filter changes and fuel system flushes help remove these contaminants, ensuring that the fuel lines remain free from corrosive substances. Keeping the fuel system clean not only prevents corrosion but also improves fuel efficiency and overall engine performance.
By combining regular maintenance and the use of corrosion inhibitors, vehicle owners can effectively prevent heavy rust on fuel lines. This proactive approach ensures that the fuel system remains in optimal condition, reducing the risk of performance issues and potential safety hazards. It is a simple yet crucial step in vehicle care, contributing to the longevity and reliability of the entire fuel system.
Unveiling the Power of 8AN Fuel Lines: A Comprehensive Guide
You may want to see also
Fuel Quality: Contaminated fuel can accelerate rust formation on fuel lines
Contaminated fuel is a common issue that can have detrimental effects on a vehicle's performance and longevity, especially when it comes to the fuel lines. Over time, fuel can degrade and become contaminated with various substances, including water, sediment, and even rust itself. This contamination is a significant concern as it directly impacts the quality of the fuel and, consequently, the health of the fuel lines.
When fuel lines are exposed to contaminated fuel, the presence of water and other impurities can lead to a process known as corrosion. Corrosion is the gradual deterioration of metal surfaces due to chemical reactions with the surrounding environment. In the case of fuel lines, the inner walls of the lines are typically made of metal, often steel or copper. When these metal surfaces come into contact with contaminated fuel, especially if it contains water, the water molecules can facilitate the formation of rust.
Rust formation on fuel lines is a serious problem because it can lead to several issues. Firstly, rust is an abrasive material that can wear down the fuel line walls over time. This wear and tear can result in small holes or leaks in the fuel lines, allowing contaminated fuel to seep into other engine components. Secondly, the presence of rust can restrict the flow of fuel, reducing the engine's performance and efficiency. As the rust accumulates, it can create a blockage, leading to difficult starting, poor acceleration, and even engine misfires.
The contamination of fuel often occurs due to various factors. One common cause is the aging of the fuel itself. Over time, fuel can absorb moisture from the air, leading to the formation of water droplets within the fuel tank. These droplets can then circulate throughout the fuel system, including the lines, causing rust and other contaminants. Additionally, fuel tanks may develop small leaks, allowing external contaminants to enter the fuel, further compromising its quality.
To prevent and mitigate the effects of contaminated fuel on fuel lines, regular maintenance is essential. This includes routine fuel filter changes to trap contaminants and ensure clean fuel delivery. It is also recommended to use fuel stabilizers, especially for long-term storage, to inhibit the absorption of moisture and maintain fuel quality. By addressing fuel quality and implementing preventive measures, vehicle owners can minimize the risk of rust formation on fuel lines and ensure the overall health and longevity of their engines.
Boat Fuel Line Removal: A Step-by-Step Guide
You may want to see also
Environmental Factors: Moisture and temperature changes can contribute to heavy rust
Moisture and temperature variations in the environment play a significant role in the development of heavy rust on fuel lines, especially in vehicles and machinery that operate in diverse weather conditions. When fuel lines are exposed to these environmental factors, they become susceptible to corrosion, which can lead to severe rust accumulation over time.
In humid environments, moisture tends to condense on the inner walls of fuel lines, creating a damp environment that encourages rust formation. This is particularly problematic in areas with high humidity levels, where the moisture content in the air is consistently elevated. Over time, the moisture can lead to the deterioration of the fuel line's internal surface, causing rust to form and accumulate.
Temperature changes, especially rapid fluctuations, can also accelerate the rusting process. When fuel lines are exposed to extreme cold, the fuel inside can freeze, leading to expansion and potential damage to the line. This expansion and contraction cycle, coupled with the moisture present, create an ideal environment for rust to form and spread. Similarly, in hot climates, the fuel can expand, causing pressure and potential damage to the fuel lines, which, when combined with moisture, accelerates rusting.
The impact of these environmental factors is further exacerbated by the presence of contaminants in the fuel. Fuel impurities, such as water, acids, and volatile organic compounds (VOCs), can accelerate corrosion when they come into contact with the fuel lines. These contaminants can penetrate the fuel line walls, creating a corrosive environment that promotes heavy rust formation.
To mitigate the effects of environmental factors on fuel lines, regular maintenance and inspections are crucial. This includes checking for leaks, replacing old or damaged fuel lines, and ensuring that fuel systems are properly sealed to prevent moisture intrusion. Additionally, using fuel stabilizers and maintaining a consistent fuel level can help reduce the impact of temperature changes and moisture, thus minimizing the risk of heavy rust on fuel lines.
Seafoam's Power: Can It Clean Fuel Lines?
You may want to see also
Fuel System Design: Proper design and materials can reduce the risk of heavy rust
The fuel system in vehicles is a critical component that requires careful design and material selection to prevent issues like heavy rust formation. Rust, a natural process of oxidation, can significantly impact the performance and longevity of fuel lines, leading to potential safety hazards. Proper design considerations and the use of appropriate materials are essential to mitigate these risks.
One key aspect of fuel system design is the choice of materials. Traditional steel fuel lines are susceptible to rust due to their iron content. Over time, exposure to moisture, especially in the presence of electrolytes in the fuel, can lead to rapid corrosion. To address this, modern fuel systems often utilize alternative materials such as stainless steel or high-density polyethylene (HDPE). Stainless steel, with its higher chromium content, forms a protective oxide layer that resists rusting. HDPE, a type of plastic, is also an excellent choice as it is non-corrosive and has a high resistance to moisture. These materials ensure that the fuel lines remain rust-free, even in harsh environments.
Designing the fuel system with proper geometry is another crucial factor. Fuel lines should be designed to minimize sharp bends and kinks, as these can create stress points where rust is more likely to initiate. Smooth, gradual bends and a well-planned route for the fuel lines can reduce the risk of localized corrosion. Additionally, the system should be designed to allow for proper ventilation, ensuring that any moisture in the fuel vaporizes and does not condense inside the lines.
The installation process also plays a significant role in preventing heavy rust. Fuel lines should be secured using appropriate clamps or brackets that provide even pressure and do not concentrate stress on specific areas. Proper sealing at connections and fittings is essential to prevent moisture intrusion. Regular maintenance, including inspections for any signs of corrosion or damage, is vital to identify and address issues early on.
In summary, fuel system design and material selection are critical in combating heavy rust formation. By choosing appropriate materials like stainless steel or HDPE, implementing thoughtful geometric designs, and ensuring proper installation and maintenance, the risk of rust-related issues can be significantly reduced. This approach not only enhances the reliability of the fuel system but also contributes to the overall safety and performance of the vehicle.
Mercury Verado Fuel Line Removal: A Step-by-Step Guide
You may want to see also
Frequently asked questions
Heavy rust on fuel lines refers to significant corrosion and deterioration of the metal surface of the fuel lines, often caused by prolonged exposure to moisture, fuel contaminants, or harsh environmental conditions. This can lead to a buildup of rust particles, which may block the fuel flow, reduce engine performance, and potentially cause engine damage over time.
Signs of heavy rust may include visible rust flakes or deposits inside the fuel lines, a noticeable decrease in fuel pressure, engine misfires, or a decrease in engine power. In some cases, you might be able to see rust-colored stains on the fuel lines or hear a rattling sound when the engine is running, indicating loose or damaged fuel line components.
If left untreated, heavy rust can lead to severe engine issues. Rust particles can restrict fuel flow, causing poor engine performance, hard starting, or even engine stalls. Over time, rust can erode the fuel lines, leading to leaks or complete fuel line failure. This may result in expensive engine repairs or the need for a complete fuel system replacement. Regular maintenance and inspection can help prevent and address rust-related problems.