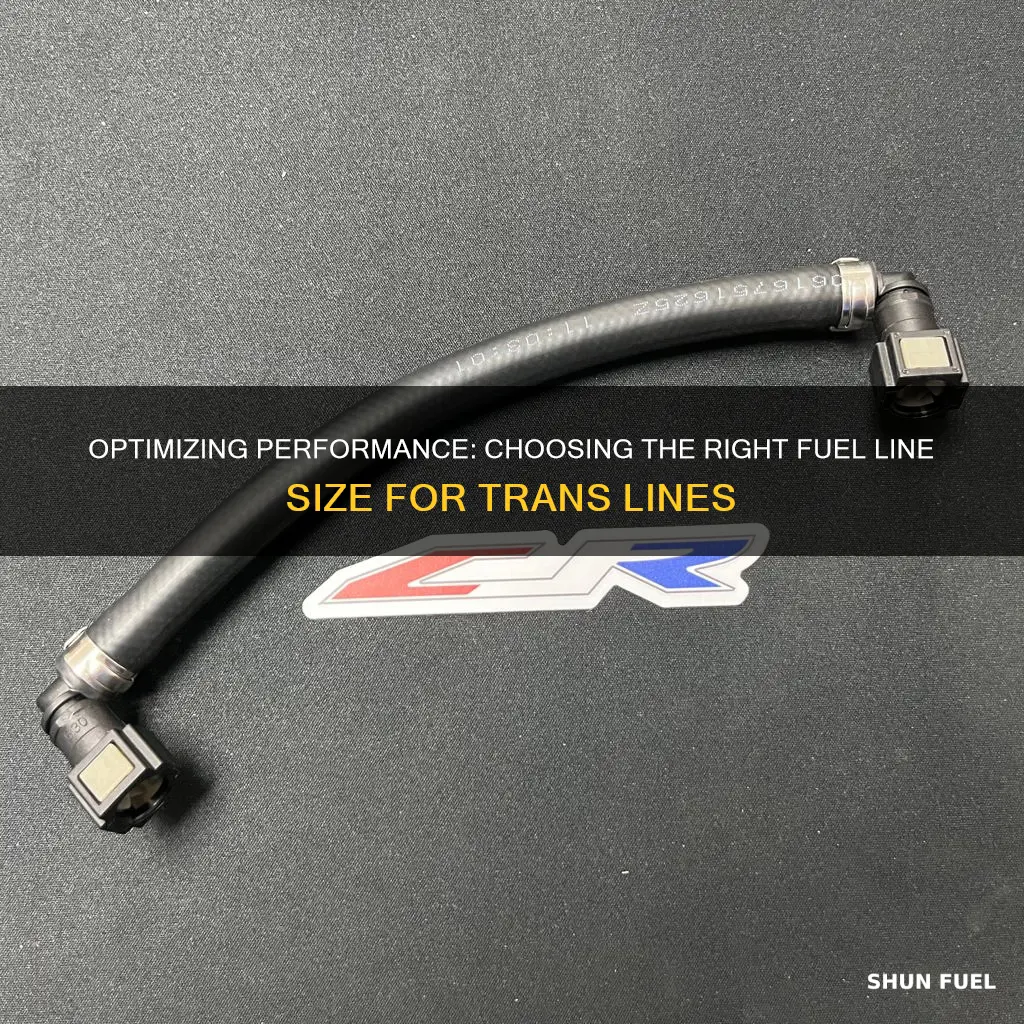
When it comes to choosing the right fuel line for your Trans Lines setup, it's crucial to consider the specific requirements of your vehicle and the performance you aim to achieve. The size of the fuel line plays a significant role in ensuring efficient fuel delivery and optimal engine performance. In this guide, we'll explore the factors that determine the appropriate fuel line size, including engine power, fuel flow rate, and installation considerations, to help you make an informed decision and optimize your Trans Lines setup.
What You'll Learn
- Fuel Line Diameter: Choose the right diameter based on engine power and flow rate
- Material Compatibility: Ensure the material is compatible with fuel type and temperature
- Length and Routing: Consider length and routing to avoid restrictions and damage
- Clamping Options: Select appropriate clamps for secure installation and vibration resistance
- Regulatory Compliance: Adhere to local regulations for fuel line installation and safety
Fuel Line Diameter: Choose the right diameter based on engine power and flow rate
When it comes to selecting the appropriate fuel line diameter for your transmission lines, it's crucial to consider the engine's power and the flow rate of fuel. The fuel line acts as a conduit, carrying the vital fuel from the tank to the engine, and its diameter directly impacts the efficiency and performance of the fuel delivery system. Here's a detailed guide to help you make the right choice:
Engine Power and Flow Rate: The primary factors to consider are the engine's power output and the required fuel flow rate. Higher-performance engines with increased displacement and power levels demand more fuel to meet their demands. As a rule of thumb, the fuel line diameter should be proportional to the engine's power. For instance, a high-performance V8 engine might require a larger diameter fuel line compared to a smaller, more compact engine. Similarly, the flow rate, which is the volume of fuel passing through the line per unit of time, also plays a significant role. Engines with higher flow rates need fuel lines that can accommodate the increased volume without causing pressure drops or restrictions.
Standard Sizes: Fuel lines are typically available in standard diameters, such as 3/8", 1/2", 5/8", or 3/4". These sizes are commonly used and provide a good balance between flow capacity and flexibility. For most standard engines, a 3/8" or 1/2" diameter fuel line is often sufficient. However, for high-performance applications, you might consider a 5/8" or even a 3/4" diameter to ensure optimal fuel delivery.
Calculating the Right Diameter: To determine the appropriate diameter, you can use a simple calculation. The formula is based on the principle of flow rate, which is flow rate = (pressure * diameter^2) / (viscosity * length). For your specific engine, measure or estimate the required flow rate and then use this formula to calculate the ideal diameter. Keep in mind that this calculation provides a theoretical value, and practical considerations might require adjustments based on real-world conditions.
Flexibility and Routing: Another essential aspect is the flexibility of the fuel line. The line should be able to bend and route around various engine components without kinking or restricting flow. Thicker fuel lines might offer more flexibility but can be bulkier. Consider the available space within the engine bay and choose a diameter that provides adequate flow while allowing for easy installation and routing.
In summary, selecting the right fuel line diameter involves a careful consideration of engine power and flow rate requirements. By matching the diameter to the engine's needs, you can ensure efficient fuel delivery, optimize performance, and maintain a reliable fuel system. Remember to consult manufacturer specifications and seek professional advice if needed to make an informed decision.
Fitech Fuel Line Fittings: A Comprehensive Guide
You may want to see also
Material Compatibility: Ensure the material is compatible with fuel type and temperature
When it comes to choosing the right fuel line for your transmission lines, material compatibility is a critical factor that cannot be overlooked. The fuel line's material must be carefully selected to ensure it can withstand the specific conditions of the fuel type and temperature variations it will encounter. Incompatible materials can lead to fuel degradation, leaks, and even system failures over time.
Different fuel types, such as gasoline, diesel, or even ethanol blends, have unique chemical compositions and properties. For instance, ethanol-blended fuels are more corrosive and can dissolve certain plastics and rubbers. Therefore, it is essential to choose a fuel line material that is resistant to the specific fuel's corrosive nature. Common materials used for fuel lines include rubber, vinyl, and various types of plastics like polyvinyl chloride (PVC) or polyethylene (PE). Each material has its advantages and limitations, so the choice depends on the specific fuel and operating conditions.
Temperature compatibility is another crucial aspect. Fuel lines must be able to handle the temperature extremes experienced in different climates and driving conditions. Extreme temperatures can cause materials to become brittle or soft, leading to cracks or leaks. For instance, in cold climates, the fuel line should be flexible enough to bend without becoming brittle, and in hot climates, it should resist heat degradation to maintain its structural integrity. Materials like silicone or certain types of rubber are often chosen for their temperature resistance.
To ensure compatibility, it is recommended to consult the vehicle's manual or seek advice from automotive experts. They can provide specific guidelines based on the vehicle's make and model, as well as the type of fuel it uses. Using the right material for the fuel line will not only ensure the longevity of your vehicle's fuel system but also contribute to better overall performance and reliability.
In summary, material compatibility is a key consideration when selecting fuel lines for transmission lines. The chosen material should be able to withstand the specific fuel's corrosive properties and temperature variations. By carefully selecting the right material, you can ensure a reliable and efficient fuel system, providing peace of mind and optimal vehicle performance.
Choosing the Right Fuel Line for Small Gas Engines: A Guide
You may want to see also
Length and Routing: Consider length and routing to avoid restrictions and damage
When it comes to choosing the right fuel line for your transmission lines, considering the length and routing is crucial to ensure optimal performance and prevent any potential issues. The fuel line should be long enough to reach the engine without any unnecessary tension or strain, as this can lead to restrictions and reduced fuel flow. A common rule of thumb is to allow for at least 6 inches of extra length to accommodate any potential movement or expansion of the engine components. This extra length also helps in case the fuel line needs to be adjusted during maintenance or repairs.
The routing of the fuel line is another critical aspect. It should be carefully planned to avoid any sharp bends or kinks that could restrict fuel flow and potentially cause damage over time. The line should be routed away from any moving parts, such as the engine's timing belt or pulleys, to prevent damage and ensure a smooth flow of fuel. It is recommended to use flexible fuel lines with a protective covering to withstand the heat and vibrations encountered in the engine compartment.
In some cases, the fuel line may need to pass through various engine compartments or under other components. In such scenarios, it is essential to consider the clearance and space available. The fuel line should be routed in a way that allows for easy access and maintenance, ensuring that it does not interfere with other parts or cause any obstructions. Proper routing will also help in maintaining the integrity of the fuel line and prevent any potential leaks or damage.
Additionally, when installing the fuel line, it is crucial to secure it properly. The line should be fastened using appropriate clamps or ties to prevent it from coming loose or causing damage to other components. Ensuring a secure and tight installation will contribute to the overall reliability and longevity of the fuel system.
By carefully considering the length and routing of the fuel line, you can avoid common issues such as restricted fuel flow, potential damage to the fuel line, and performance problems. It is always advisable to consult the vehicle's manual or seek professional guidance to determine the specific requirements for your transmission lines and ensure a proper installation.
Fuel Line Faults: Common Issues and Solutions
You may want to see also
Clamping Options: Select appropriate clamps for secure installation and vibration resistance
When it comes to installing fuel lines for transmission lines, clamping is a critical aspect that ensures a secure and reliable connection. The choice of clamps directly impacts the overall performance and longevity of the fuel system. Here's a detailed guide on selecting the appropriate clamps for your specific needs:
Understanding Clamp Requirements:
Before choosing clamps, it's essential to understand the specific requirements of your fuel line installation. Consider the following factors:
- Fuel Line Diameter: Different fuel lines have varying diameters, and clamps should be selected based on the size of the line. Standard fuel lines typically range from 3/8" to 1/2" in diameter, and corresponding clamp sizes are available.
- Vibration Resistance: Transmission lines are subject to vibrations during vehicle operation. Choose clamps that provide excellent vibration resistance to prevent fuel line movement and potential leaks.
- Environmental Conditions: Consider the operating environment. Outdoor installations may require clamps that can withstand UV exposure and temperature fluctuations.
Types of Clamps:
- Metal Clamps: These are durable and offer a tight grip. Metal clamps are ideal for heavy-duty applications and provide excellent vibration resistance. They are available in various sizes and are often used for larger fuel lines.
- Rubber Clamps: Rubber clamps are flexible and offer a secure grip without causing damage to the fuel line. They are commonly used for smaller lines and provide good vibration damping.
- Flanged Clamps: These clamps feature a flanged design, providing a larger contact area for a more secure hold. Flanged clamps are often used in high-pressure applications.
Installation Process:
- Measure and Cut: Ensure the fuel line is the correct length and cut it to size.
- Prepare the Clamps: Clean and inspect the clamps to ensure they are free of debris.
- Secure the Clamps: Place the clamp over the fuel line, ensuring it is centered. Use the appropriate tools to tighten the clamp securely, being careful not to overtighten.
- Test for Leaks: After clamping, check for any leaks at the connection points.
Vibration Resistance Techniques:
To enhance vibration resistance, consider the following:
- Use multiple clamps along the length of the fuel line to distribute the force and prevent movement.
- Opt for clamps with a longer reach to provide a more secure grip.
- For high-vibration applications, consider using vibration-damping materials or inserts within the clamp.
Remember, proper clamping is crucial for maintaining the integrity of your fuel system. Always refer to manufacturer guidelines and select clamps that match the fuel line specifications for a secure and long-lasting installation.
Unveiling Stihl Fuel Line Material: A Comprehensive Guide
You may want to see also
Regulatory Compliance: Adhere to local regulations for fuel line installation and safety
When it comes to fuel line installation, adhering to local regulations is of utmost importance to ensure safety and compliance. Each region has its own set of guidelines and standards that dictate the proper sizing and installation of fuel lines, especially in the context of transmission lines. These regulations are in place to prevent potential hazards such as fuel leaks, fires, and environmental contamination.
One key aspect of regulatory compliance is understanding the specific requirements for your area. Local authorities often provide detailed specifications regarding the diameter and material of fuel lines. For instance, certain areas may mandate the use of specific types of fuel lines, such as those made from high-temperature-resistant materials, to withstand the demands of transmission line applications. It is essential to consult the relevant codes and standards, such as those set by the International Fuel Gas Code (IFGC) or similar regional guidelines, to ensure you select the appropriate fuel line size.
The size of the fuel line is critical as it determines the flow rate and pressure capacity required for efficient and safe operation. Local regulations often specify the minimum and maximum allowable diameters for fuel lines to ensure they can handle the expected fuel volume and pressure. Insufficient line size may lead to reduced performance and potential safety risks, while oversized lines could be unnecessary and increase costs.
Additionally, regulatory compliance extends beyond the choice of fuel line size. Installation practices must adhere to local guidelines, including proper routing, support, and protection of the fuel lines. This ensures that the lines are not damaged, kinked, or subjected to excessive stress, which could compromise their integrity. Local regulations may also provide instructions on the use of specific connectors, fittings, and clamps to ensure a secure and leak-free installation.
Staying informed about local regulations is an ongoing process. It is advisable to regularly review and update your knowledge of the applicable codes and standards. This ensures that your fuel line installation practices remain compliant and up-to-date. By adhering to these regulations, you not only ensure the safety of your vehicle but also contribute to environmental protection and the overall well-being of the community.
Optimizing Performance: Choosing the Right Fuel Line for Your Johnson 200
You may want to see also
Frequently asked questions
The standard fuel line size for Trans Lines is usually 3/8 inch in diameter. This size is commonly used due to its balance between flow rate and flexibility, making it suitable for most applications.
While using a larger fuel line (e.g., 1/2 inch) can increase the flow rate, it is generally not recommended for Trans Lines. Larger lines may be more prone to vibration-induced leaks and can be less flexible, making installation more challenging.
The length of the fuel line depends on the specific vehicle and engine configuration. As a general rule, the line should be as short as possible to minimize the risk of fuel vaporization and ensure efficient delivery. It's best to consult the vehicle's manual or seek professional advice for accurate measurements.
Yes, the material is crucial. For Trans Lines, fuel-resistant materials like stainless steel or high-quality rubber compounds are ideal. These materials ensure durability, flexibility, and resistance to fuel degradation over time. Look for lines with a protective coating to enhance their performance and longevity.