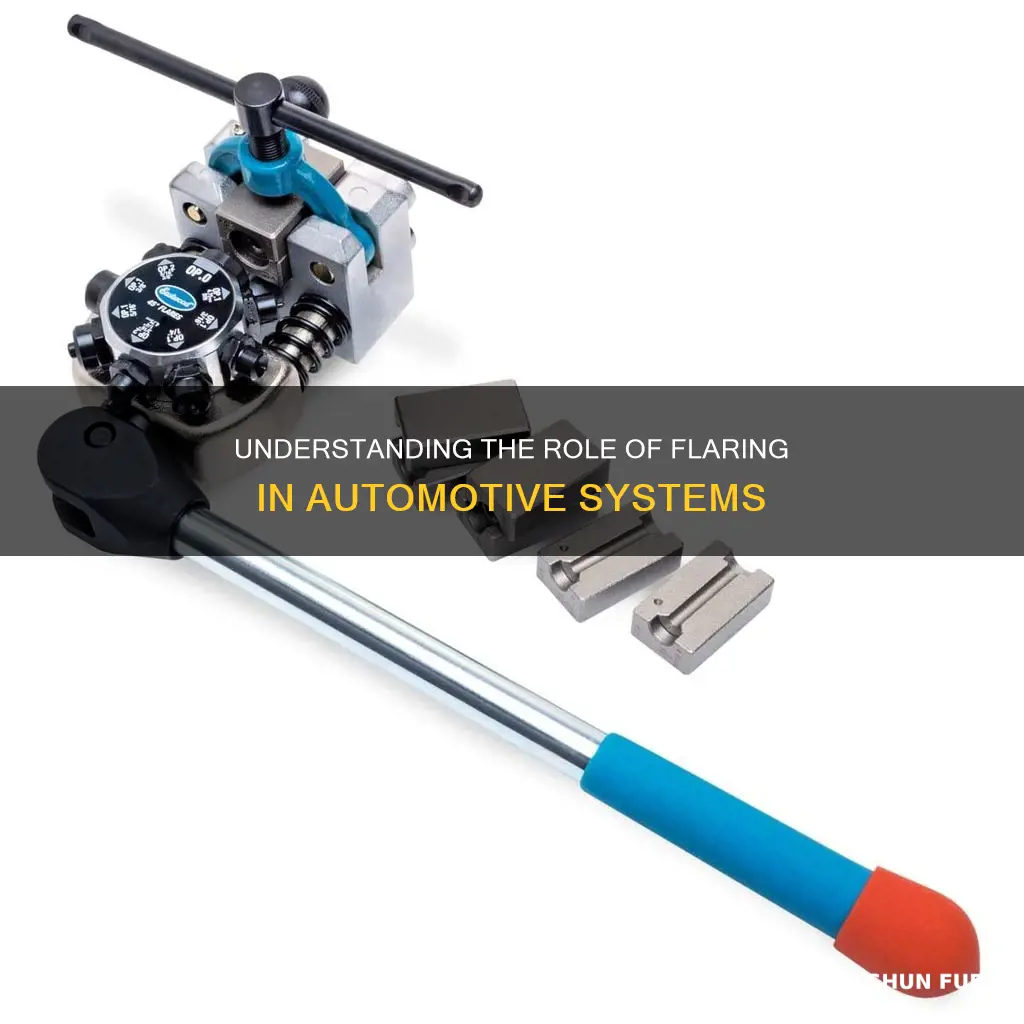
Flaring is a crucial process in the automotive industry, specifically in the assembly and maintenance of brake and fuel systems. It involves the precise bending and shaping of metal tubes to create a smooth, sealed connection between components. This technique is essential for ensuring the integrity and safety of brake and fuel lines, as it allows for a secure and leak-free attachment. The process of flaring is a critical step in the manufacturing and repair of these systems, where the right tools and techniques are employed to create a reliable and durable connection.
Characteristics | Values |
---|---|
Purpose | Flaring is a technique used to create a smooth, precise connection between brake and fuel lines. It involves bending and shaping the ends of the lines to fit together securely. |
Material Compatibility | Flaring can be applied to various materials commonly used in brake and fuel systems, such as steel, copper, and aluminum. |
Strength | The process ensures a strong and durable connection, preventing leaks and maintaining system integrity. |
Flexibility | Flared connections offer flexibility, allowing for slight movement and vibration without compromising the seal. |
Cost-Effectiveness | Compared to other joining methods, flaring is often more cost-effective for small-scale repairs and installations. |
Skill Requirement | Flaring requires skill and precision, typically performed by trained professionals to ensure a successful connection. |
Common Applications | This technique is widely used in automotive repair, especially for brake and fuel line installations, replacements, and repairs. |
Safety | Proper flaring ensures a safe and reliable system, reducing the risk of accidents caused by leaks or failures. |
Environmental Impact | Flaring can be an eco-friendly option as it minimizes material waste and promotes efficient use of resources. |
What You'll Learn
- Brake Line Flaring Tools: Specialized tools for creating flare connections on brake lines
- Fuel Line Flaring Techniques: Methods for flaring fuel lines to ensure tight seals
- Flaring Dies and Dies: Different types of dies used for brake and fuel line flaring
- Flaring Safety Precautions: Safety measures to prevent injuries during brake and fuel line flaring
- Flared Connection Inspection: Procedures for inspecting flared connections for leaks and proper fit
Brake Line Flaring Tools: Specialized tools for creating flare connections on brake lines
Brake line flaring is a critical process in automotive repair and maintenance, ensuring the safe and efficient operation of a vehicle's braking system. Flaring involves creating a flared or expanded end on a brake line to facilitate a secure connection with other components, such as calipers, master cylinders, or hydraulic reservoirs. This technique is essential for maintaining the integrity of the brake system, preventing leaks, and ensuring optimal performance. To achieve this, specialized tools known as brake line flaring tools are employed, which are designed to create precise flare connections.
These flaring tools are specifically engineered to handle the unique requirements of brake line installations. They typically consist of a mandrel, a die, and a handle. The mandrel, a central component, is a cylindrical shaft that rotates within the die, which is a shaped tool with a flared opening. When the tool is activated, the mandrel rotates, forcing the brake line material to expand and form a flare. This process requires precision and control to ensure the flare is of the correct size and shape, allowing for a tight and secure connection.
Brake line flaring tools come in various designs and sizes to accommodate different brake line diameters and applications. Some tools feature adjustable mandrels, allowing technicians to set the flare depth and angle according to the specific requirements of the job. This adjustability ensures versatility and accuracy, making it easier to work with various brake systems. Additionally, these tools often include safety features, such as guards or stops, to prevent over-tightening or damage to the brake lines during the flaring process.
Using specialized brake line flaring tools offers several advantages. Firstly, they provide consistent and repeatable results, ensuring that each flare connection is made to the same high standard. This consistency is crucial in maintaining the overall performance and safety of the braking system. Secondly, these tools are designed to minimize the risk of errors, reducing the chances of incorrect flare sizes or angles, which could lead to brake system failures. Properly flared connections also help prevent leaks, ensuring the brake fluid remains contained within the system.
In summary, brake line flaring tools are essential for creating secure and reliable flare connections on brake lines. Their specialized design and precision capabilities make them indispensable in automotive repair and maintenance, ensuring the braking system functions optimally and safely. With the right tools and proper technique, technicians can confidently create flare connections, contributing to the overall reliability and performance of the vehicle's braking system.
Maximizing Efficiency: The Role of Fuel Return Lines in Diesel Engines
You may want to see also
Fuel Line Flaring Techniques: Methods for flaring fuel lines to ensure tight seals
Flaring is a crucial technique used in the automotive industry to create a secure and leak-tight connection between fuel lines and other components. This process involves shaping the end of a fuel line to form a flare, which is then inserted into a corresponding fitting or adapter. The flare acts as a mechanical seal, ensuring that the fuel line is firmly attached and preventing any potential leaks. When it comes to brake lines, flaring is also employed to establish a reliable connection, although the process may vary slightly due to the different materials and requirements of brake systems.
The fuel line flaring process begins with the preparation of the fuel line itself. The end of the line is carefully cleaned and deburred to remove any sharp edges or contaminants that could interfere with the sealing process. This step is essential to ensure a smooth and precise flare. Next, the flaring tool is used to shape the end of the fuel line. This tool typically consists of a mandrel or die that is forced into the end of the line, creating a flare. The flare is designed to have a slightly larger diameter than the original fuel line, allowing it to form a tight seal within the fitting.
There are various methods and tools available for flaring fuel lines, each offering different levels of precision and control. One common technique is the use of a mechanical flaring tool, which applies pressure to the fuel line end, gradually forming the flare. This method requires skill and practice to achieve consistent results. Another approach is the use of a hydraulic flaring machine, which provides more power and speed, making it suitable for high-volume production environments. These machines often have adjustable settings to accommodate different fuel line sizes and materials.
For brake line flaring, specialized tools and techniques are employed due to the unique characteristics of brake systems. Brake lines often use different materials, such as stainless steel or brass, and may require specific flaring procedures. The flaring process for brake lines involves similar steps as fuel lines but may demand more precision and attention to detail. It is crucial to ensure that the flare is formed evenly and that the material is not damaged during the flaring process.
In summary, flaring is an essential skill for automotive technicians, enabling them to create secure connections for fuel and brake lines. By employing the right tools and techniques, technicians can ensure tight seals, preventing fuel leaks and maintaining the safety and performance of vehicles. Whether it's for fuel lines or brake lines, the flaring process requires practice, attention to detail, and the use of appropriate tools to achieve reliable and long-lasting connections.
Boat Fuel Line Maintenance: When to Inspect for Optimal Performance
You may want to see also
Flaring Dies and Dies: Different types of dies used for brake and fuel line flaring
Flaring is a crucial process in the automotive and plumbing industries, where metal tubes are bent or shaped to create a smooth, flared end. This technique is essential for creating secure connections for brake and fuel lines, ensuring optimal performance and safety. When it comes to flaring, the use of specialized dies is vital to achieving the desired shape and fit. These dies are designed to impress a specific flare profile onto the tube, allowing for a tight and reliable connection.
There are various types of flaring dies available, each tailored to different applications and materials. For brake lines, a common type of die is the 'Brake Line Flaring Die'. This die is specifically engineered to create a precise flare profile for brake hose connections. It typically features a curved or conical shape, which helps to form the tube's end into a smooth, rounded flare. The design ensures that the flare is consistent and uniform, providing a secure and leak-free connection for the brake system.
In the case of fuel lines, a different approach is often required due to the varying materials and sizes involved. Fuel line flaring dies are designed to accommodate the unique characteristics of fuel hoses, which may include different wall thicknesses and diameters. These dies often have adjustable features, allowing for customization to fit various fuel line sizes. The goal is to create a flare that provides a tight seal while also allowing for flexibility to accommodate potential movement within the fuel system.
Another type of die commonly used is the 'Universal Flaring Die', which, as the name suggests, can be adapted for multiple applications. These dies are versatile and can be adjusted to create different flare profiles. They are particularly useful when working with a variety of brake and fuel line sizes and materials. Universal flaring dies often feature a adjustable mandrel or a set of interchangeable dies, enabling the user to customize the flare shape as needed.
Additionally, some flaring dies incorporate a 'Stepped' or 'Progressive' design. This means the die has multiple stages or steps, each with a different flare profile. This design allows for a gradual flare formation, ensuring a more controlled and precise result. Such dies are especially useful when dealing with thicker or more rigid materials, as they provide a more gradual and controlled deformation process.
In summary, the choice of flaring die depends on the specific requirements of the brake or fuel line application. Each type of die is carefully designed to create the necessary flare profile, ensuring a secure and reliable connection. Whether it's a dedicated brake line die, a universal adjustable die, or a stepped design, these tools are essential for professionals in the automotive and plumbing fields to ensure the integrity and safety of their systems.
2006 Car Fuel Line Location: A Comprehensive Guide
You may want to see also
Flaring Safety Precautions: Safety measures to prevent injuries during brake and fuel line flaring
Flaring is a crucial process in automotive repair and maintenance, especially when it comes to connecting brake and fuel lines. It involves the precise bending and shaping of metal tubing to create a secure and leak-free connection. While flaring is a common and effective method, it requires careful attention to safety to prevent injuries and ensure the integrity of the system. Here are some essential safety precautions to follow when performing flaring operations:
Personal Protective Equipment (PPE): Before beginning any flaring task, it is imperative to wear appropriate personal protective equipment. This includes safety goggles to protect your eyes from sparks, flying debris, or any potential hazards during the process. Additionally, heat-resistant gloves should be worn to safeguard your hands from burns when using hot tools or working with heated components. A respirator or dust mask is also recommended to avoid inhaling any harmful fumes or particles that may be generated during the flaring process.
Work Area Preparation: Ensure that your work area is well-lit and organized. Keep the workspace clean and free from clutter to minimize the risk of accidents. Proper ventilation is crucial, especially when working with fuel lines, as it helps disperse any volatile substances and reduces the risk of fire. It is advisable to set up the work area near a fire extinguisher or have one readily available in case of emergencies.
Tool Inspection and Maintenance: Regularly inspect and maintain your flaring tools to ensure they are in good working condition. Check for any signs of damage, wear, or malfunction before starting the flaring process. Keep the tools clean and lubricated to facilitate smooth operations. Properly store and secure the tools when not in use to prevent accidents or damage.
Precision and Technique: Flaring requires precision and skill. Take your time to measure and mark the tubing accurately before beginning the flaring process. Use the correct flaring tools and apply the appropriate amount of force to avoid over-bending or damaging the material. Maintain a consistent technique throughout the operation to ensure a professional finish. Remember, rushing or using excessive force can lead to injuries and compromised connections.
Ventilation and Fire Safety: When working with fuel lines, always prioritize fire safety. Ensure that the work area is clear of any flammable materials or substances. Keep a fire extinguisher nearby and ensure that you know how to use it. Proper ventilation is crucial to disperse any fuel vapor and reduce the risk of ignition. Never use open flames or heat sources near fuel lines unless absolutely necessary and always follow safety protocols.
Training and Supervision: If you are new to flaring or working with brake and fuel lines, consider seeking guidance from an experienced professional. Proper training can significantly reduce the risk of errors and injuries. Supervision can help identify potential hazards and ensure that safety protocols are followed. Always follow the manufacturer's guidelines and recommendations for the specific vehicle or system you are working on.
By adhering to these safety precautions, you can minimize the risks associated with flaring brake and fuel lines, ensuring a safe working environment and high-quality connections. Remember, safety should always be the top priority in any automotive repair or maintenance task.
Fuel Line Fix: A Guide to Repairing Poulan Chainsaw Lines
You may want to see also
Flared Connection Inspection: Procedures for inspecting flared connections for leaks and proper fit
When it comes to inspecting flared connections, especially in the context of brake and fuel lines, a thorough examination is crucial to ensure the system's safety and performance. Flared connections are a common method for joining pipes or hoses, creating a robust and leak-resistant seal. Here's a step-by-step guide to inspecting these connections:
Preparation: Before beginning the inspection, ensure you have the necessary tools, including a torque wrench, a leak detection kit (which may include a soapy water solution or a specialized electronic leak detector), and a flashlight. It is essential to work in a well-ventilated area and wear appropriate personal protective equipment (PPE) to avoid any potential hazards.
Step-by-Step Inspection:
- Visual Inspection: Start by visually examining the flared connection. Look for any signs of damage, such as cracks, bends, or debris around the connection area. Check for proper alignment and ensure that the flare has been formed correctly, with no sharp edges or uneven surfaces.
- Leak Test: Use the leak detection kit to perform a thorough leak test. Start by applying a small amount of the leak detection solution or using the electronic detector around the connection. Allow a sufficient amount of time for the solution to dry or for the electronic detector to scan for leaks. Inspect the area carefully for any bubbles or changes in the solution's appearance, indicating a potential leak.
- Torque Check: If the connection is accessible, use the torque wrench to check the tightness of the flare nut. Refer to the manufacturer's specifications for the correct torque value. Ensure that the nut is tightened evenly and not over-tightened, as this can damage the threads or the flare connection.
- Functionality Test: After ensuring the connection is leak-free, test its functionality. For brake lines, this might involve checking the brake pedal feel and the responsiveness of the brakes. For fuel lines, inspect the flow of fuel through the line and ensure there are no blockages or leaks.
Additional Tips:
- Always follow the manufacturer's guidelines and recommendations for specific flare connection requirements.
- Keep a record of the inspections, including any issues found and the actions taken to rectify them.
- Regularly inspect flared connections, especially in critical systems like brakes and fuel lines, to maintain optimal performance and safety.
By following these procedures, you can effectively inspect flared connections, ensuring they are leak-free and properly fitted, which is vital for the overall reliability of brake and fuel line systems.
Fuel Line Blow-Off Filter: Causes, Fixes, and Prevention Tips
You may want to see also
Frequently asked questions
Flaring is a process used in the automotive industry to create a precise, cone-shaped end on metal tubes, such as brake and fuel lines. This technique ensures a secure and leak-free connection when joining these lines to other components.
In brake systems, flaring is employed to attach brake lines to various components like calipers, master cylinders, and wheel cylinders. The flared end of the brake line is inserted into a corresponding flared port, providing a tight seal and allowing for efficient transmission of hydraulic pressure to the brakes.
Flaring is also utilized for fuel lines to ensure a reliable connection to fuel tanks, injectors, and other fuel system components. By flaring the end of the fuel line, it creates a smooth, tapered surface that forms a secure seal when connected, preventing fuel leaks and ensuring proper fuel delivery.
Yes, flaring offers several benefits. It provides a strong, durable connection that can withstand the pressures and vibrations encountered during vehicle operation. Flared connections are also easier to assemble and disassemble, allowing for efficient maintenance and repairs. Additionally, the precise flare shape ensures a tight seal, preventing fuel or brake fluid leaks, which is crucial for safety and system performance.
Flaring is typically a specialized task that requires specific tools and expertise. While some basic flaring can be attempted at home with the right equipment, professional flaring ensures the highest quality and safety standards. Automotive repair shops and specialized flaring equipment manufacturers often provide this service to guarantee a reliable and secure connection for brake and fuel lines.