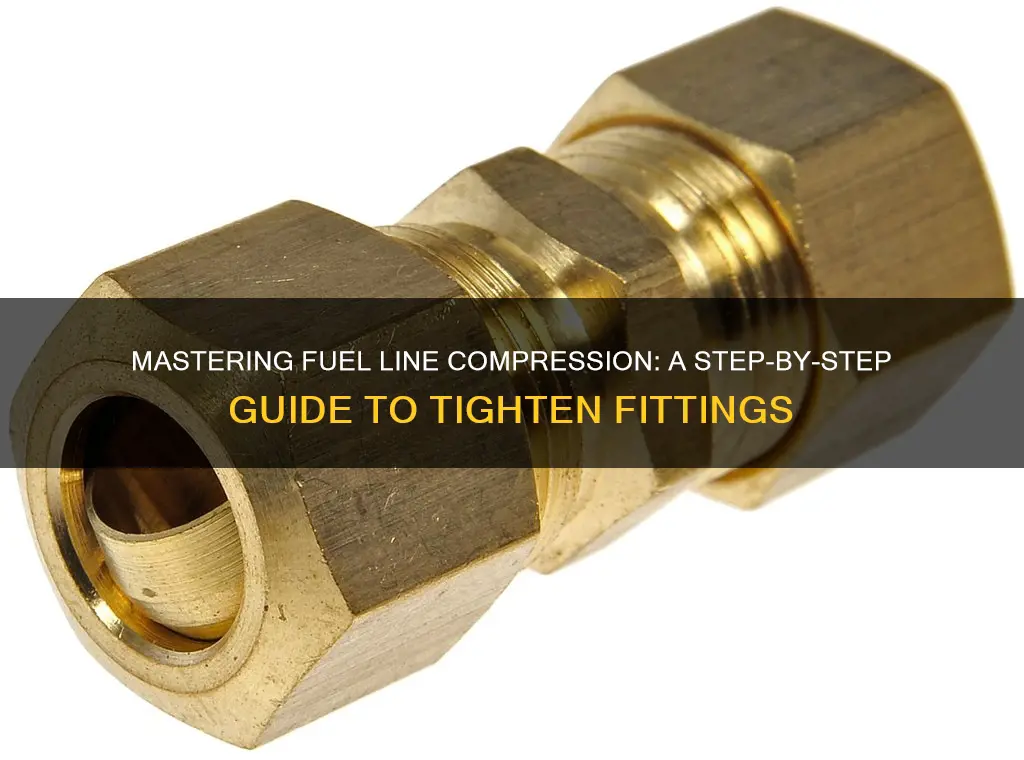
Tightening compression fittings for fuel lines is a crucial step in ensuring a secure and leak-free connection. This process involves using a specific technique to apply the right amount of force to the fitting, which can be achieved with the right tools and a systematic approach. By following these steps, you can effectively tighten the fitting, ensuring a reliable and safe fuel line system.
What You'll Learn
- Prepare Tools: Gather necessary tools: wrench, pliers, fuel line cleaner
- Clean Fitting: Use cleaner to remove dirt and corrosion from fitting and fuel line
- Tighten Securely: Apply firm, consistent pressure to tighten fitting without over-tightening
- Check Leaks: Inspect for leaks after tightening; ensure no fuel escapes
- Test Pressure: Apply pressure to ensure fitting holds fuel without leaks
Prepare Tools: Gather necessary tools: wrench, pliers, fuel line cleaner
To ensure a secure and reliable connection for your fuel line, it's essential to have the right tools and preparation. Here's a step-by-step guide on gathering the necessary equipment:
Wrench: A wrench is a fundamental tool for tightening compression fittings. You'll need a wrench that fits the size of the fitting you're working with. Common sizes include 1/4-inch, 3/8-inch, and 1/2-inch. Ensure it has a comfortable grip and consider using a wrench with a ratchet mechanism for added control during the tightening process.
Pliers: While a wrench is ideal, pliers can be a useful alternative, especially for smaller or more compact fittings. Pliers provide a firm grip and can help you apply force to tighten the fitting. Look for a pair with adjustable jaws to accommodate different sizes.
Fuel Line Cleaner: Cleaning the fuel line is a crucial step often overlooked. Over time, fuel lines can accumulate dirt, debris, and contaminants, leading to reduced performance and potential issues. Fuel line cleaner is designed to dissolve these deposits and ensure a clean, smooth interior for the fuel line. This step is essential to maintain the integrity of the fuel system and prevent any blockages.
Having these tools ready will ensure you can tackle the task of tightening compression fittings with confidence. It's always a good practice to inspect and maintain your fuel system regularly to prevent any potential issues and ensure optimal performance.
Harley Road King Fuel Line Size: Expert Guide
You may want to see also
Clean Fitting: Use cleaner to remove dirt and corrosion from fitting and fuel line
When preparing to tighten a compression fitting for a fuel line, it's crucial to ensure that the fitting and the fuel line are clean and free from any contaminants. This step is often overlooked but is essential for a secure and reliable connection. Start by gathering the necessary tools and materials, including a suitable fuel line cleaner, a small brush or wire brush, and a clean cloth.
The first step in the cleaning process is to disconnect the fuel line from the engine or the source it is currently connected to. This might require removing a few screws or bolts, depending on the setup. Once disconnected, use the fuel line cleaner as per the manufacturer's instructions. Typically, you'll apply the cleaner directly to the fitting and the fuel line, ensuring an even coating. Allow the cleaner to work for the recommended time, which usually ranges from a few minutes to an hour, depending on the product.
During this waiting period, you can use the small brush or wire brush to scrub away any stubborn dirt or corrosion. Pay close attention to the threads and the interior of the fitting, as these areas are prone to accumulation. After the specified time, wipe away the cleaner with a clean cloth, ensuring no residue remains. This step is vital as any remaining cleaner could attract dirt and moisture over time.
Once the fitting and fuel line are completely dry, you can proceed with reinstalling the fuel line. Ensure that the fitting is aligned correctly and that all connections are tight. Over-tightening should be avoided as it can damage the fitting or the fuel line. Instead, use a wrench or spanner to secure the fitting, applying gentle pressure until it is snug. This process ensures that the fitting is clean, free from corrosion, and properly installed, providing an efficient and safe fuel supply to your engine.
2004 Buick Rendezvous Fuel Line Leaks: Common Causes & Fixes
You may want to see also
Tighten Securely: Apply firm, consistent pressure to tighten fitting without over-tightening
When working with compression fittings for fuel lines, it's crucial to apply the right amount of force to ensure a secure and reliable connection. The goal is to tighten the fitting firmly without causing damage or compromising the integrity of the fuel line. Here's a step-by-step guide on how to achieve this:
Start by ensuring you have the correct tools for the job. A good quality wrench or spanner is essential, and it's important to choose the right size that fits the compression fitting. Place the wrench over the fitting, positioning it so that it aligns with the threads or the compression surface. Apply firm and consistent pressure, using a smooth, even motion. Avoid using excessive force, as this can lead to over-tightening, which may damage the fitting or the fuel line. The key is to apply pressure gradually and steadily, ensuring that the fitting is tightened evenly.
As you tighten the fitting, you should feel resistance, indicating that the threads are engaging. Continue applying pressure until you reach the desired tightness. A good rule of thumb is to tighten the fitting until it is snug, but not so tight that it becomes difficult to turn. Over-tightening can cause the fitting to crush or distort, leading to potential leaks or damage. It's important to use your judgment and rely on your sense of touch and feel for the right amount of pressure.
After tightening the fitting, give it a final check by hand to ensure it is secure. You can also use a tool like a thread seal tape or pipe compound to provide an additional layer of security, especially if the fuel line is exposed to vibrations or extreme conditions. This extra step can help prevent leaks and ensure the long-term reliability of your fuel line connection. Remember, the goal is to achieve a tight, secure fit without causing any harm to the components involved.
In summary, tightening compression fittings for fuel lines requires a careful and controlled approach. By applying firm, consistent pressure and using the right tools, you can ensure a reliable connection. Always be mindful of the potential risks associated with over-tightening, and take the time to inspect your work to guarantee a professional and safe installation.
Understanding Fuel Line Seals: A Comprehensive Guide
You may want to see also
Check Leaks: Inspect for leaks after tightening; ensure no fuel escapes
When working with fuel lines, ensuring a secure and leak-free connection is paramount. After tightening the compression fitting, it's crucial to inspect for any potential leaks to prevent fuel loss and potential hazards. Here's a step-by-step guide to effectively check for leaks:
Step 1: Gather the Necessary Tools: Before you begin, ensure you have the appropriate tools for the job. You'll need a fuel line inspection kit, which typically includes a small hand pump and a set of adapters. This kit allows you to create a controlled pressure environment to detect leaks.
Step 2: Prepare the System: Locate the fuel line and compression fitting you've just tightened. Ensure the system is not actively fueling the engine to avoid any accidental fuel release. If the vehicle is running, shut it off and disconnect the fuel source.
Step 3: Apply Pressure: Using the hand pump from your inspection kit, slowly apply pressure to the fuel line just before the compression fitting. Start with a low pressure and gradually increase it. Pay close attention to the fitting and the surrounding area.
Step 4: Inspect for Leaks: As you apply pressure, carefully observe the fuel line and the compression fitting. Look for any signs of fuel escaping, such as small droplets, mist, or a hissing sound. Feel the area around the fitting for any warmth or moisture, which could indicate a leak. Also, check for any visible damage or deformation around the fitting.
Step 5: Check for Fuel Escape: If you detect any fuel escaping, immediately release the pressure and tighten the fitting further. Repeat the process of applying pressure and inspecting until no leaks are found. Ensure that all connections are secure and tight.
Step 6: Final Inspection: After ensuring no leaks, perform a final visual inspection of the entire fuel line and fitting. Look for any signs of damage, corrosion, or wear that could compromise the integrity of the connection.
Remember, proper tightening and leak-checking are essential to maintaining a safe and efficient fuel system. Always follow manufacturer guidelines and best practices to ensure the longevity of your vehicle's fuel lines and overall performance.
Ford Fuel Line Fitting Removal: A Step-by-Step Guide
You may want to see also
Test Pressure: Apply pressure to ensure fitting holds fuel without leaks
When working with fuel lines, ensuring a secure and leak-free connection is crucial for the safe and efficient operation of your vehicle. Testing the pressure of compression fittings is a critical step in this process. Here's a detailed guide on how to perform this test effectively:
Start by gathering the necessary tools and materials. You'll need a fuel pressure gauge, which is specifically designed to measure the pressure of fuel. It should be compatible with the fuel line fittings in your system. Additionally, have a supply of compressed air or an air compressor ready to apply pressure to the fitting. It is also recommended to have a collection pan or rag to catch any potential fuel leaks during the test.
Locate the compression fitting you want to test. This fitting is typically found where the fuel line connects to an engine component or another fuel system component. Ensure that the fitting is accessible and that you have a clear view of the connection. If the fitting is part of a longer fuel line, consider removing a section to access the fitting for testing.
Now, it's time to apply pressure. Attach the fuel pressure gauge to the compression fitting. Make sure it is securely connected to avoid any potential leaks. Then, using the compressed air or air compressor, apply pressure to the fitting. Start with a low pressure and gradually increase it while monitoring the gauge. The goal is to reach a pressure that is within the recommended range for your specific fuel system. This pressure can vary depending on the manufacturer's specifications and the design of your fuel system.
As you increase the pressure, pay close attention to the gauge and the fitting. You should not observe any drops in pressure, indicating a potential leak. If you notice any fuel escaping or a drop in pressure, immediately release the pressure and inspect the fitting for any damage or loose connections. Tighten the fitting further if necessary, ensuring it is secure and free from any gaps that could cause leaks.
Once you've reached the desired pressure and confirmed that the fitting holds fuel without any leaks, you can safely release the pressure and disconnect the gauge. Repeat this process for each compression fitting in your fuel system to ensure comprehensive coverage. Remember, proper testing and tightening of these fittings are essential to prevent fuel leaks, which can lead to engine performance issues and potential safety hazards.
Vacuum Line Fuel Spill: Causes and Solutions
You may want to see also
Frequently asked questions
A secure compression fitting should not have any visible movement or play when you try to rock it back and forth. You can also use a wrench to apply gentle force and check for resistance. If the fitting remains firmly in place without any signs of looseness, it is likely tight enough.
The recommended torque value for compression fittings can vary depending on the specific application and manufacturer's guidelines. As a general rule, you should aim for a torque of around 50-100 in-pounds (in-lb) for most fuel line installations. Always refer to the product instructions or consult a professional for the exact torque requirements.
It is not recommended to reuse a compression fitting once it has been loosened. Over time, the threads or sealing surfaces of the fitting can be damaged, leading to potential leaks or reduced performance. It's best to replace the fitting if it becomes loose to ensure a secure and reliable connection.
You will typically need a few essential tools to tighten compression fittings. These include a wrench or spanner (depending on the fitting size and type), a torque wrench (if precise torque is required), and possibly a pair of pliers for any additional grip needed. Always choose the appropriate tool size that matches the fitting's dimensions.
Yes, there are a few techniques to ensure a secure connection. First, ensure that the fitting and fuel line are clean and free of any debris or contaminants. Apply a thin layer of thread sealant or pipe compound to the threads before inserting the fitting. Tighten the fitting by hand first, then use the wrench to apply the recommended torque. Finally, inspect the connection to ensure it is tight and there are no leaks.