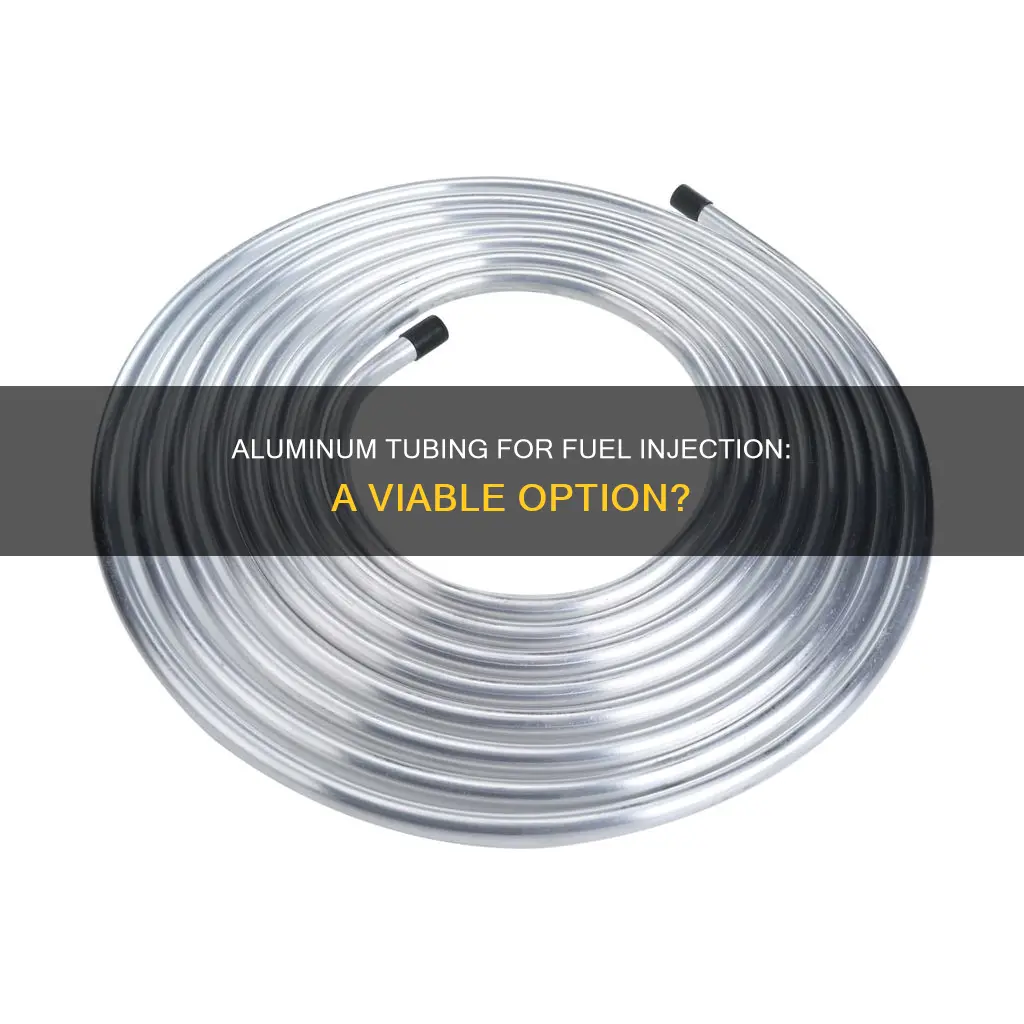
When it comes to fuel injection systems, the choice of material for fuel lines is crucial for optimal performance and safety. Aluminum tubing is a popular option for fuel lines due to its lightweight and corrosion-resistant properties. However, there are some considerations to keep in mind. In this paragraph, we will explore whether aluminum tubing is suitable for fuel injection fuel lines, examining its advantages, potential drawbacks, and the factors to consider when making this choice.
What You'll Learn
- Material Strength: Aluminum tubing offers lightweight, durable fuel lines for injection systems
- Corrosion Resistance: It resists corrosion, ensuring long-lasting performance in fuel injection systems
- Flexibility: Aluminum's flexibility allows for easy installation and routing in fuel lines
- Heat Dissipation: Its thermal properties help dissipate heat, preventing fuel line damage
- Cost-Effectiveness: Aluminum tubing provides an affordable, reliable solution for fuel injection fuel lines
Material Strength: Aluminum tubing offers lightweight, durable fuel lines for injection systems
Aluminum tubing is an excellent choice for fuel lines in injection systems, offering a unique combination of lightweight strength and durability. This material is an ideal candidate for fuel lines due to its inherent properties, which make it a reliable and efficient component in the automotive industry.
One of the key advantages of aluminum tubing is its lightweight nature. Fuel lines made from this material are significantly lighter than traditional steel or copper alternatives. This reduced weight is particularly beneficial in automotive applications, as it contributes to improved vehicle performance and fuel efficiency. The lightweight design of aluminum fuel lines allows for easier installation and reduced stress on the vehicle's overall structure, ensuring a more comfortable and responsive driving experience.
Despite its lightweight construction, aluminum tubing excels in durability. It possesses excellent resistance to corrosion, which is crucial for fuel lines as they are exposed to harsh environments and corrosive substances. The inherent corrosion resistance of aluminum ensures that the fuel lines remain intact and functional over extended periods, even in the presence of moisture, chemicals, and varying temperatures. This durability factor is essential for maintaining the integrity of the fuel injection system and ensuring optimal engine performance.
The strength of aluminum tubing is another critical aspect. It provides the necessary structural integrity to withstand the pressures and forces encountered in fuel injection systems. Aluminum fuel lines can handle the demands of high-pressure fuel delivery without compromising their structural integrity. This strength, combined with its lightweight nature, makes aluminum tubing an ideal solution for fuel lines, offering a balance between performance and reliability.
In summary, aluminum tubing is a superior material for fuel lines in injection systems. Its lightweight design reduces vehicle weight and improves fuel efficiency, while its durability and corrosion resistance ensure long-lasting performance. The strength of aluminum tubing allows it to handle the pressures and forces associated with fuel injection, making it a reliable and efficient choice for automotive applications. By utilizing aluminum tubing, engineers can create robust and lightweight fuel lines that contribute to enhanced vehicle performance and overall system efficiency.
Understanding Husqvarna Line Trimmer Fuel Mix: A Comprehensive Guide
You may want to see also
Corrosion Resistance: It resists corrosion, ensuring long-lasting performance in fuel injection systems
Aluminum tubing is indeed a suitable choice for fuel injection fuel lines, offering several advantages that make it a preferred material for this application. One of its key attributes is its excellent corrosion resistance, which is crucial for the longevity and reliability of fuel injection systems.
Corrosion, the deterioration of materials due to chemical reactions with their environment, can be detrimental to fuel lines, especially in the harsh conditions of an engine bay. Aluminum, with its inherent corrosion-resistant properties, forms a protective oxide layer on its surface when exposed to air, which acts as a barrier against further corrosion. This natural protection ensures that the aluminum tubing remains stable and free from rust and decay, even when in constant contact with fuel, which often contains corrosive elements.
The resistance to corrosion is particularly important in fuel injection systems as it helps prevent the degradation of the fuel lines over time. This means that the system can maintain its efficiency and performance without the risk of fuel leaks or reduced flow rates due to internal damage. As a result, the overall reliability and lifespan of the fuel injection system are significantly improved.
Furthermore, the lightweight nature of aluminum tubing is an added benefit. Its low weight allows for easier installation and flexibility, making it a practical choice for fuel lines that need to navigate through tight spaces within an engine compartment. This characteristic also contributes to the overall efficiency of the fuel injection system by reducing the strain on the engine and improving fuel delivery.
In summary, aluminum tubing's natural corrosion resistance, combined with its lightweight and flexible nature, makes it an ideal material for fuel injection fuel lines. This ensures that the system operates efficiently and reliably over an extended period, providing a cost-effective solution for fuel delivery in various engine applications.
2004 Buick Rendezvous Fuel Line Leaks: Common Causes & Fixes
You may want to see also
Flexibility: Aluminum's flexibility allows for easy installation and routing in fuel lines
Aluminum tubing is an excellent choice for fuel injection fuel lines due to its inherent flexibility, which offers several advantages during installation and maintenance. This property is particularly beneficial when dealing with the intricate network of fuel lines within an engine bay, where space is often limited and access can be challenging.
The flexibility of aluminum tubing allows for easy bending and manipulation, enabling technicians to navigate around various engine components with minimal effort. This characteristic is especially useful when connecting fuel lines to different parts of the engine, as it simplifies the routing process. Technicians can effortlessly adjust the tubing to fit the available space, ensuring a secure and reliable connection without causing any damage to the engine's internal components.
Furthermore, the flexibility of aluminum tubing contributes to the overall durability of the fuel line system. It can absorb minor vibrations and movements that occur during engine operation, reducing the risk of damage or disconnection. This is crucial for maintaining a consistent fuel supply and ensuring optimal engine performance.
In addition to its installation benefits, aluminum's flexibility also makes it easier to inspect and maintain the fuel lines over time. Technicians can access tight spaces and perform necessary repairs or replacements without the tubing becoming a hindrance. This ease of maintenance is essential for the long-term reliability of the fuel injection system.
When considering fuel injection fuel lines, the flexibility of aluminum tubing is a significant advantage. It simplifies the installation process, ensures a secure connection, and facilitates easy maintenance, making it an ideal material for this critical component of the fuel system.
Volvo C70 Fuel Line Removal: A Step-by-Step Guide
You may want to see also
Heat Dissipation: Its thermal properties help dissipate heat, preventing fuel line damage
Aluminum tubing is an excellent choice for fuel injection fuel lines due to its superior thermal properties, which play a crucial role in preventing fuel line damage. The material's ability to dissipate heat efficiently is a key advantage in the automotive industry, where fuel lines are constantly exposed to high temperatures.
When it comes to heat dissipation, aluminum excels. Its thermal conductivity is significantly higher than that of many other materials commonly used in fuel lines. This means that aluminum can quickly transfer heat away from the fuel line, ensuring that the temperature remains within safe limits. In fuel injection systems, where fuel is under high pressure and can reach elevated temperatures, this property is vital. By efficiently conducting heat, aluminum tubing prevents the fuel from overheating, which could lead to damage or even failure of the fuel line.
The thermal properties of aluminum also contribute to its lightweight nature, making it an ideal material for fuel lines. Lighter materials reduce the overall weight of the vehicle, which is a significant benefit in the automotive sector. Additionally, the lightweight nature of aluminum tubing allows for easier installation and flexibility, ensuring that the fuel lines can withstand the dynamic nature of vehicle movement without compromising performance.
Furthermore, aluminum's thermal stability is another critical factor. It maintains its structural integrity and heat dissipation capabilities over a wide temperature range. This stability ensures that the fuel line can handle the extreme temperatures encountered during vehicle operation, from idling to high-speed driving. As a result, aluminum tubing provides long-lasting performance and reliability, reducing the risk of fuel line damage or leaks.
In summary, aluminum tubing's thermal properties make it an ideal material for fuel injection fuel lines. Its high thermal conductivity and stability enable efficient heat dissipation, preventing fuel line damage and ensuring the longevity of the vehicle's fuel system. With its lightweight and flexible nature, aluminum offers a practical and effective solution for automotive fuel line applications.
Mastering the Art of Fuel Line Clamp Removal: A Step-by-Step Guide
You may want to see also
Cost-Effectiveness: Aluminum tubing provides an affordable, reliable solution for fuel injection fuel lines
Aluminum tubing offers a cost-effective and efficient solution for fuel injection fuel lines, making it an attractive option for both DIY enthusiasts and professionals in the automotive industry. When it comes to fuel lines, the primary concern is ensuring a reliable and safe delivery of fuel from the tank to the engine. Aluminum tubing provides an affordable alternative to traditional steel or stainless steel options, without compromising on performance or durability.
One of the key advantages of aluminum tubing is its lightweight nature. This characteristic reduces the overall weight of the fuel system, which can be beneficial for vehicles where weight is a critical factor, such as racing cars or aircraft. The lightweight design also contributes to better fuel efficiency, as less weight means less strain on the engine, resulting in improved performance and reduced fuel consumption.
In terms of cost, aluminum tubing is an economical choice. Its affordability makes it accessible to a wide range of users, including those on a budget. The material's price point is particularly appealing for fuel lines, as it allows for a more flexible and customizable approach to fuel system design. With aluminum tubing, you can create a tailored fuel line setup without breaking the bank. This cost-effectiveness is especially valuable for projects where multiple fuel lines need to be installed, as the savings can add up quickly.
Despite its cost-effectiveness, aluminum tubing is known for its durability. It possesses excellent resistance to corrosion, ensuring that the fuel lines remain reliable and long-lasting. This is crucial for fuel injection systems, where contaminants and fuel degradation are common concerns. Aluminum's natural resistance to corrosion helps prevent fuel line degradation, ensuring a consistent and clean fuel supply to the engine.
Furthermore, aluminum tubing's versatility allows for easy bending and shaping, making installation a straightforward process. Its flexibility enables technicians to navigate around engine components and tight spaces with ease, ensuring a precise and secure fit. This ease of installation contributes to the overall cost-effectiveness of the solution, as it reduces labor costs and minimizes the time required for fuel line assembly.
In summary, aluminum tubing is an ideal choice for fuel injection fuel lines due to its cost-effectiveness, lightweight design, durability, and ease of installation. It provides a reliable and affordable solution, making it a popular option for those seeking to upgrade or repair their fuel systems without incurring excessive expenses. With its combination of performance and price, aluminum tubing is a smart investment for anyone looking to optimize their fuel line setup.
John Deere LA105 Fuel Line: Size Guide and Tips
You may want to see also
Frequently asked questions
Yes, aluminum tubing can be used for fuel injection fuel lines, but it requires careful consideration. Aluminum has a lower melting point compared to steel, which might be a concern for high-temperature fuel systems. However, it is lightweight, corrosion-resistant, and can provide good thermal management, making it a viable option for certain applications.
Aluminum tubing offers several benefits. It is non-magnetic, which is essential for fuel systems as it won't interfere with magnetic sensors or components. Additionally, aluminum's natural corrosion resistance helps prevent fuel degradation and ensures a longer lifespan for the fuel lines. Its lightweight nature also reduces the overall weight of the fuel system.
One potential issue is that aluminum can be more susceptible to fatigue under constant pressure and vibration. This might require careful design and installation to ensure the tubing can withstand the stresses of the fuel system. Additionally, aluminum's lower strength compared to steel means it may not be suitable for high-pressure applications or in environments with extreme temperatures.
To ensure compatibility, it is crucial to select aluminum tubing with the appropriate thickness and diameter for your specific fuel system. Consulting the manufacturer's guidelines and specifications is essential. Additionally, consider the temperature and pressure requirements of your fuel system, and choose aluminum tubing that can withstand those conditions. Proper sealing and joining techniques are also vital to prevent fuel leaks.