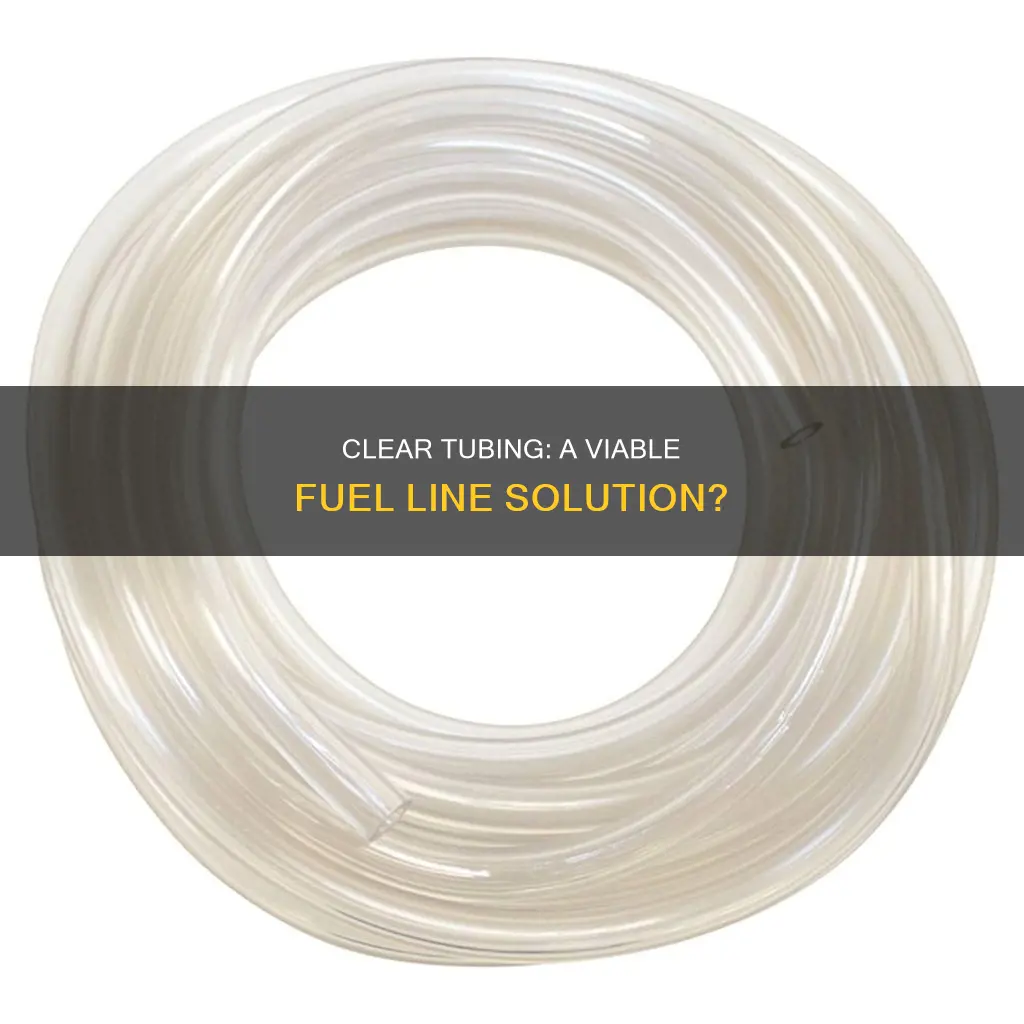
Clear tubing can be a viable alternative to traditional fuel lines in certain applications, but its effectiveness depends on various factors. While it may appear similar to fuel lines, clear tubing is not designed for the same purpose and may not withstand the corrosive effects of fuel over time. Factors such as the type of fuel, temperature, and pressure must be considered to ensure the tubing's compatibility and longevity. This introduction sets the stage for a discussion on the feasibility and limitations of using clear tubing as a fuel line.
Characteristics | Values |
---|---|
Material | Clear tubing can be made from various materials such as PVC, silicone, or rubber, depending on the specific application and requirements. |
Flexibility | It offers flexibility, allowing it to bend and move with the engine's vibrations, which is crucial for fuel lines. |
Chemical Resistance | Clear tubing should be resistant to the chemicals in fuel to prevent degradation and ensure long-term performance. |
Temperature Tolerance | It needs to withstand the temperature variations in the engine bay, including hot and cold conditions. |
Pressure Rating | The tubing must have an adequate pressure rating to handle the fuel pressure in the system. |
Compatibility | It should be compatible with the fuel type, ensuring no contamination or interaction with the fuel's properties. |
Transparency | Clear tubing allows for visual inspection of the fuel level and system health. |
Cost | The cost can vary depending on the material and thickness, but it is generally an affordable solution for fuel lines. |
Installation | It can be easily installed and routed through the engine bay, providing a neat and organized appearance. |
Maintenance | Regular maintenance and inspections are recommended to ensure the tubing remains in good condition. |
What You'll Learn
- Material Compatibility: Tubing must be compatible with fuel, resisting corrosion and degradation
- Pressure Rating: Tubing should withstand fuel pressure without bursting or leaking
- Flexibility: Fuel lines need flexibility to accommodate engine movement without cracking
- Temperature Tolerance: Tubing must handle fuel temperature extremes without becoming brittle or soft
- Vibration Resistance: Fuel lines should remain intact under engine vibration and movement
Material Compatibility: Tubing must be compatible with fuel, resisting corrosion and degradation
When considering the use of clear tubing as a fuel line, material compatibility is a critical factor to ensure the system's reliability and longevity. The tubing must be able to withstand the corrosive nature of fuels, which can vary widely in composition and properties. Different fuels, such as gasoline, diesel, or aviation fuel, have unique chemical characteristics that can lead to degradation of materials over time. For instance, gasoline contains additives like ethanol, which can cause swelling and softening of certain plastics, while diesel's higher sulfur content can accelerate corrosion. Therefore, the chosen tubing material should be resistant to these specific fuel components to prevent leaks, blockages, and system failures.
One approach to achieving material compatibility is to select tubing made from materials known for their resistance to fuel-related degradation. For example, some common materials used for fuel lines include high-density polyethylene (HDPE), polyvinyl chloride (PVC), and fluoropolymers like polytetrafluoroethylene (PTFE). HDPE is often preferred due to its excellent chemical resistance and ability to withstand various fuel types. It is also flexible, making it easy to route and install. PVC, while less flexible, is another suitable option, especially for its cost-effectiveness and durability. However, it's important to note that PVC may not be ideal for fuels containing ethanol due to its potential to cause swelling.
Fluoropolymers, such as PTFE, offer superior resistance to a wide range of chemicals, including fuels. This material is known for its non-stick properties, making it ideal for fuel lines as it reduces the risk of fuel accumulation and blockages. Additionally, PTFE is highly flexible and can withstand extreme temperatures, making it a versatile choice for various fuel applications. However, it is typically more expensive than other options.
In summary, when evaluating clear tubing for use as a fuel line, it is essential to consider the specific fuel type and its potential impact on material compatibility. The chosen tubing material should be resistant to corrosion, swelling, and degradation caused by the fuel's chemical properties. By selecting the appropriate material, you can ensure a reliable and long-lasting fuel delivery system, minimizing the risk of leaks and system failures.
Isuzu Diesel Fuel Line Sizes: A Comprehensive Guide
You may want to see also
Pressure Rating: Tubing should withstand fuel pressure without bursting or leaking
When considering the use of clear tubing as a fuel line, one of the critical factors to evaluate is the pressure rating. Fuel lines are designed to withstand the pressure generated by the fuel system, which can vary depending on the engine and operating conditions. The tubing must be able to handle this pressure without failing, as any burst or leak could lead to dangerous consequences, such as fuel spillage, engine damage, or even fire hazards.
The pressure rating of tubing is typically measured in pounds per square inch (PSI) or bars, and it indicates the maximum pressure the material can endure without permanent deformation or failure. For fuel lines, the pressure rating should be chosen based on the expected fuel pressure in the system. For instance, a typical car engine might operate at fuel pressures ranging from 50 to 100 PSI, while high-performance engines or those with turbochargers can reach much higher pressures.
To ensure the tubing can handle the required fuel pressure, it is essential to select a material with an appropriate pressure rating. Common materials used for fuel lines include rubber, silicone, and various types of plastics, each with its own pressure-withstanding capabilities. For example, rubber tubing might be suitable for lower-pressure applications, while high-temperature, high-pressure environments could benefit from silicone or specialized plastic compounds.
When specifying the tubing, it is crucial to consider the operating temperature as well, as this can affect the material's performance. Some materials may lose their structural integrity or become brittle at high temperatures, leading to potential failures. Therefore, selecting a tubing material that can withstand both the expected fuel pressure and operating temperature is vital for a safe and reliable fuel system.
In summary, when using clear tubing as a fuel line, the pressure rating is a critical consideration. The tubing must be able to withstand the fuel pressure without bursting or leaking, ensuring the safety and efficiency of the fuel system. Proper material selection, based on both pressure and temperature requirements, is essential to guarantee the long-term performance and reliability of the fuel line installation.
Optimizing Fuel Flow: Choosing the Right Fuel Line for Injection
You may want to see also
Flexibility: Fuel lines need flexibility to accommodate engine movement without cracking
Flexibility is a critical aspect of fuel lines, especially when considering their role in connecting the fuel tank to the engine. The engine's internal components are in constant motion, and the fuel lines must be able to move with the engine without compromising their structural integrity. This is particularly important to prevent fuel leaks, which can lead to dangerous situations and costly repairs.
The primary reason for this flexibility requirement is the engine's natural movement during operation. Engines experience a range of motions, including up and down, side to side, and even slight rotational movements. These motions can cause stress on the fuel lines, especially if they are rigid and inflexible. Over time, this stress can lead to cracks, tears, or even complete ruptures in the fuel lines, resulting in fuel leaks and potential engine damage.
To ensure adequate flexibility, fuel lines are typically constructed using materials that can bend and twist without breaking. Rubber, for example, is a common material for fuel lines due to its inherent flexibility. It can accommodate the engine's movements without cracking or becoming brittle over time. Additionally, the design of the fuel lines, including their diameter and wall thickness, plays a crucial role in their flexibility. Thinner walls and smaller diameters generally result in more flexible lines, allowing them to move with the engine more easily.
In some cases, fuel lines may also incorporate flexible materials like silicone or specialized rubber compounds. These materials offer excellent flexibility and resistance to heat and cold, ensuring that the fuel lines can withstand the varying temperatures encountered during engine operation. The use of flexible materials also helps to reduce the risk of fuel contamination, as the lines can move freely without trapping air or other contaminants.
When considering alternative materials like clear tubing, it is essential to evaluate their flexibility and suitability for the task. Clear tubing, while offering visibility into the fuel system, may not possess the same level of flexibility as dedicated fuel line materials. It is crucial to choose materials that can withstand the rigors of engine operation without compromising performance and safety.
Fuel Line Size for 1977 Suzuki KZ650: Essential Guide
You may want to see also
Temperature Tolerance: Tubing must handle fuel temperature extremes without becoming brittle or soft
When considering the use of clear tubing as a fuel line, one of the critical factors to evaluate is its temperature tolerance. Fuel lines are exposed to a wide range of temperatures, especially in automotive applications, where engines can operate in various climates. The tubing must be able to withstand these temperature extremes without compromising its structural integrity.
Extreme temperatures can cause materials to become brittle or soft, leading to potential issues. For instance, if the tubing is too rigid at low temperatures, it might become difficult to install and bend, while at high temperatures, it could become more susceptible to damage from engine vibrations or road debris. The ideal fuel line material should maintain its flexibility and strength across a broad temperature range.
Clear tubing, often made from materials like PVC or silicone, can offer good temperature resistance. PVC is known for its excellent durability and can handle a wide range of temperatures, making it a popular choice for fuel lines. However, it's important to note that even with these materials, there are limits. Prolonged exposure to very low temperatures can cause the tubing to become brittle, leading to cracks or even breaks. On the other hand, high temperatures can cause the material to degrade over time, affecting its performance and longevity.
To ensure optimal performance, it's recommended to choose tubing with a temperature rating that exceeds the expected operating temperatures of the fuel system. This provides a safety margin and helps prevent issues related to material degradation. Additionally, proper installation and regular maintenance can further enhance the tubing's ability to handle temperature extremes.
In summary, when using clear tubing as a fuel line, it is crucial to consider its temperature tolerance. Selecting a material with suitable temperature resistance and ensuring proper installation will contribute to a reliable and long-lasting fuel system. This attention to detail can help prevent potential issues and ensure the overall safety and efficiency of the vehicle's fuel delivery system.
Optimizing Performance: Choosing the Right Fuel Line for Your 1992 Johnson 115 V4 Outboard
You may want to see also
Vibration Resistance: Fuel lines should remain intact under engine vibration and movement
The integrity of fuel lines is crucial for the efficient and safe operation of any vehicle. When considering the use of clear tubing as a fuel line, one of the primary concerns is its ability to withstand the vibrations and movements inherent in an engine's operation. Vibration resistance is a critical factor in ensuring that the fuel line remains intact and functional over time.
Engine vibrations can be substantial, especially during acceleration, deceleration, and high-speed travel. These vibrations can cause the fuel line to flex and move, potentially leading to several issues. One of the most significant risks is the development of cracks or punctures in the tubing, which could result in fuel leaks. Fuel lines are designed to carry high-pressure fuel, and any breach in the line can lead to dangerous situations, including engine misfires, reduced performance, and even fire hazards.
To address this concern, clear tubing, often made from materials like PVC or polycarbonate, should be chosen for its inherent flexibility and durability. These materials can absorb and distribute the energy from vibrations, reducing the likelihood of damage. Additionally, the tubing should be properly secured to the vehicle's frame and other components to minimize movement. This can be achieved through the use of brackets, clamps, or ties, ensuring that the fuel line remains in place even under the most intense engine vibrations.
Furthermore, the design of the fuel line itself plays a vital role in vibration resistance. A well-designed line will have a smooth, flexible interior that allows for natural movement without kinking or restricting fuel flow. This flexibility is essential to prevent the line from becoming rigid and prone to damage. The outer layer of the tubing should also be robust and resistant to abrasion, ensuring it can withstand the harsh conditions inside the engine bay.
In summary, when using clear tubing as a fuel line, it is imperative to prioritize vibration resistance. This can be achieved through the selection of appropriate materials, proper securing methods, and careful design considerations. By ensuring the fuel line's ability to withstand engine vibrations, you can guarantee the reliable and safe operation of your vehicle's fuel system.
Locate the Fuel Injector Line on Your 2007 Impala SS
You may want to see also
Frequently asked questions
Clear tubing can be used as a fuel line, but it is important to consider the specific requirements and compatibility. Clear tubing, often made from materials like PVC or silicone, is generally flexible and resistant to fuel chemicals. However, it may not be as durable or heat-resistant as specialized fuel lines, so it's crucial to ensure the tubing can withstand the fuel's properties and the vehicle's operating conditions.
Clear tubing offers several benefits for fuel lines. Its transparency allows for easy inspection of the fuel flow, helping to identify any potential issues or blockages. Additionally, clear tubing is often more flexible, making installation and routing easier, especially in tight spaces. It is also relatively cost-effective and can be a good temporary or DIY solution for fuel line needs.
While clear tubing can work, there are some considerations. It may not be as long-lasting as dedicated fuel lines, especially in harsh environments or high-temperature conditions. Clear tubing might also be more susceptible to UV degradation over time, which could lead to cracking or leaks. Proper selection of tubing material and ensuring it meets fuel compatibility standards are essential to mitigate these risks.