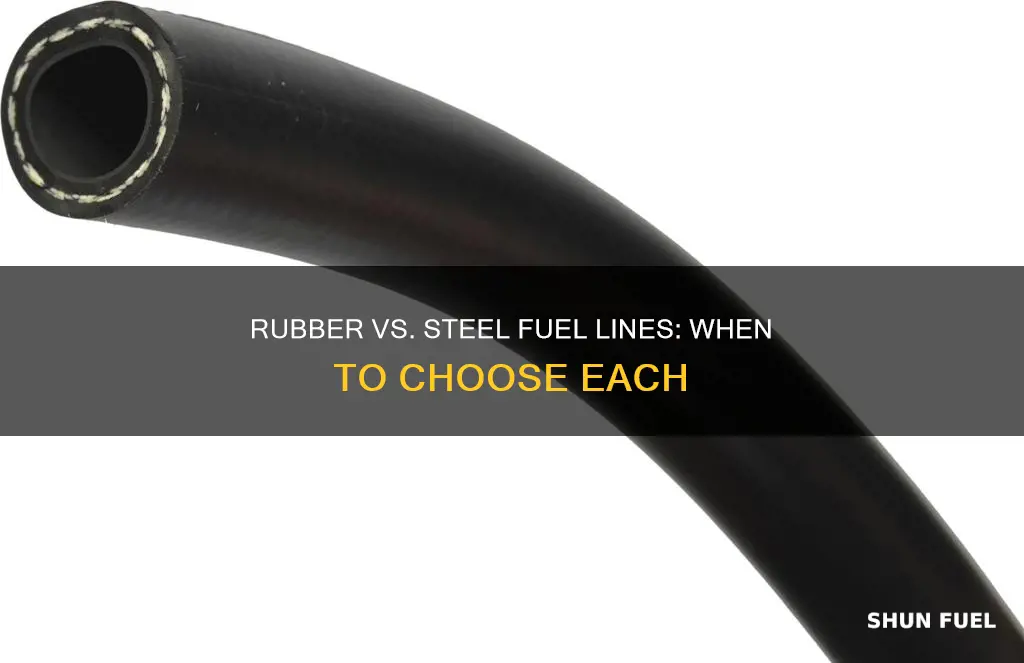
When it comes to choosing between rubber and steel fuel lines, the decision depends on various factors such as the application, environmental conditions, and performance requirements. Rubber fuel lines are commonly used in automotive applications due to their flexibility, ease of installation, and resistance to heat and vibration. They are ideal for high-performance engines and vehicles that require frequent starts and stops. On the other hand, steel fuel lines offer superior strength and durability, making them suitable for heavy-duty applications and environments with extreme temperatures or pressure. Understanding the specific needs of your project will help determine whether rubber or steel fuel lines are the best choice.
Characteristics | Values |
---|---|
Flexibility | Rubber fuel lines are more flexible and can bend around tight spaces, making them ideal for engine compartments with limited room. |
Durability | Steel fuel lines are more durable and less prone to damage from heat, oil, and fuel. They offer excellent resistance to corrosion and can handle higher pressure. |
Temperature Resistance | Rubber is generally better suited for lower temperature ranges, while steel can handle extreme temperatures, making it suitable for high-performance engines. |
Cost | Steel fuel lines tend to be more expensive due to their higher quality and durability. Rubber lines are often more affordable. |
Installation | Rubber lines are typically easier to install due to their flexibility, while steel lines may require more specialized tools and knowledge. |
Weight | Steel is heavier, which might be a consideration for certain vehicle applications. |
Noise | Rubber lines can be quieter, reducing engine noise. |
Maintenance | Steel lines may require less frequent maintenance due to their durability. |
Compatibility | Rubber is commonly used in older vehicles, while steel is often preferred in newer, high-performance models. |
What You'll Learn
- Flexibility: Rubber fuel lines offer flexibility, making them ideal for tight spaces and engine vibrations
- Durability: Steel fuel lines are more durable, resistant to corrosion, and suitable for high-pressure applications
- Temperature Range: Rubber handles extreme temperatures, while steel is best for cold climates
- Cost: Rubber is generally cheaper, but steel may be more cost-effective for long-term use
- Installation: Rubber lines are easier to install, while steel requires more specialized tools and expertise
Flexibility: Rubber fuel lines offer flexibility, making them ideal for tight spaces and engine vibrations
Flexibility is a key advantage of rubber fuel lines, especially in automotive applications. When compared to steel, rubber fuel lines offer a significant benefit in terms of adaptability and ease of installation. This characteristic is particularly important in modern vehicles, where engine compartments are often packed with various components, leaving little room for rigid metal lines. Rubber fuel lines can easily bend and conform to the available space, ensuring a secure and tight fit without causing any damage to the engine or surrounding parts. This flexibility is crucial for maintaining the integrity of the fuel system, especially in high-vibration environments where the engine and fuel lines are subjected to constant movement and stress.
The ability of rubber fuel lines to absorb and dampen vibrations is another advantage. Engine vibrations can cause metal fuel lines to rattle and potentially damage the fuel pump or injectors over time. Rubber, being a more elastic material, can effectively reduce these vibrations, providing a smoother and more reliable fuel supply. This is especially critical in high-performance vehicles or those with modified engines, where the increased power output can lead to more intense engine vibrations. By using rubber fuel lines, you create a buffer that protects the fuel system from the harsh conditions of the engine bay.
In addition to flexibility, rubber fuel lines also offer a level of durability that is often overlooked. While they may seem delicate, modern rubber compounds are designed to withstand the harsh chemicals in fuel and the extreme temperatures encountered in an engine bay. This durability ensures that the fuel lines remain pliable over time, even in the face of constant expansion and contraction due to temperature changes. As a result, rubber fuel lines can provide long-lasting performance without the risk of cracking or deteriorating, which is a common issue with steel lines over time.
The installation process also benefits from the flexibility of rubber fuel lines. When working in tight spaces, the ease of bending and shaping rubber lines allows mechanics to navigate around obstacles with greater ease. This simplifies the installation process, reducing the time and effort required to set up the fuel system. Furthermore, the flexibility of rubber lines can help minimize the number of brackets and supports needed to secure the lines, further simplifying the overall installation.
In summary, rubber fuel lines offer a unique combination of flexibility, durability, and ease of installation. Their ability to conform to tight spaces and absorb engine vibrations makes them an ideal choice for modern vehicles, ensuring a reliable and secure fuel supply. While steel fuel lines have their advantages, the flexibility of rubber lines is a critical factor in maintaining the performance and longevity of the fuel system, especially in demanding automotive environments. Understanding these differences can help engineers and mechanics make informed decisions when designing or maintaining fuel systems.
Optimizing Performance: Choosing the Right Fuel Line for Your 2001 Polaris Indy 500
You may want to see also
Durability: Steel fuel lines are more durable, resistant to corrosion, and suitable for high-pressure applications
When it comes to choosing the right fuel line for your vehicle, durability is a critical factor to consider, especially in high-pressure applications. Steel fuel lines offer a significant advantage in this regard, making them a preferred choice for many automotive enthusiasts and professionals.
One of the key benefits of steel fuel lines is their exceptional durability. Steel is a robust material known for its strength and resistance to wear and tear. Unlike rubber, which can degrade over time due to exposure to fuel, heat, and vibration, steel fuel lines are built to last. This durability ensures that the fuel lines can withstand the rigors of daily use, including high-pressure fuel delivery systems commonly found in performance vehicles. The strength of steel allows it to handle the stress of fuel transport without compromising its structural integrity, making it ideal for applications where reliability is paramount.
Corrosion resistance is another advantage of steel fuel lines. Steel is inherently resistant to corrosion, which means it can maintain its structural integrity even in the presence of fuel, moisture, and other corrosive elements. This is particularly important in high-temperature environments or when the fuel contains additives that can accelerate degradation. Rubber fuel lines, on the other hand, may deteriorate more quickly due to their susceptibility to corrosion, leading to potential leaks and performance issues. By choosing steel, you ensure that the fuel lines remain in optimal condition, providing a reliable and safe fuel supply.
In high-pressure applications, steel fuel lines excel. The material's strength and flexibility allow it to handle the increased pressure without compromising performance. This is crucial for vehicles with powerful engines that require precise and efficient fuel delivery. Steel's ability to withstand high pressure ensures that the fuel lines remain intact, preventing potential leaks and maintaining the overall efficiency of the fuel system. Whether it's a racing car or a high-performance truck, steel fuel lines provide the necessary durability and reliability to meet the demands of such applications.
In summary, when it comes to durability, steel fuel lines are the clear winner. Their resistance to corrosion and ability to handle high-pressure applications make them an excellent choice for vehicles that require a reliable and long-lasting fuel delivery system. While rubber fuel lines may be suitable for some applications, steel offers a more robust and dependable solution, ensuring that your vehicle's fuel system operates at its best.
Fram G3727 Inline Fuel Filter: Compatibility and Benefits
You may want to see also
Temperature Range: Rubber handles extreme temperatures, while steel is best for cold climates
When it comes to choosing between rubber and steel fuel lines, understanding the impact of temperature is crucial. Rubber fuel lines are an excellent choice for applications that involve extreme temperature variations. This is because rubber is known for its flexibility and ability to withstand a wide range of temperatures. It can handle the expansion and contraction that occurs with temperature fluctuations, making it ideal for environments where temperatures can vary drastically, such as in hot engines or outdoor settings. Rubber's resilience ensures that it can maintain its integrity and flexibility even when exposed to intense heat or cold.
In contrast, steel fuel lines are better suited for cold climates and environments with lower temperature extremes. Steel is a rigid material that becomes brittle when exposed to cold temperatures. While it can handle the cold, it may not be as flexible and can become more susceptible to cracking or breaking over time. Steel's strength and durability make it a reliable choice for applications where the fuel lines will be exposed to freezing temperatures, ensuring a secure and long-lasting connection.
The temperature range is a critical factor in determining the best material for fuel lines. Rubber's ability to handle extreme temperatures, both hot and cold, makes it a versatile option for various applications. It can accommodate the thermal expansion and contraction of the fuel, reducing the risk of leaks or damage. On the other hand, steel's performance in cold climates is advantageous, especially in regions with freezing temperatures, as it provides a robust and secure solution.
In summary, the choice between rubber and steel fuel lines depends on the specific temperature conditions of the environment. Rubber excels in handling extreme temperatures, making it suitable for a wide range of applications, while steel is the preferred material for cold climates, ensuring reliability and strength in freezing conditions. Understanding these temperature-related differences is essential for making informed decisions when selecting fuel lines for different automotive or industrial purposes.
Optimizing Performance: Choosing the Right Fuel Line for Your 3/8 ID Engine
You may want to see also
Cost: Rubber is generally cheaper, but steel may be more cost-effective for long-term use
When considering the choice between rubber and steel fuel lines, cost is a significant factor that can influence your decision. Rubber fuel lines are often the more affordable option, making them a popular choice for many applications. The lower cost of rubber is primarily due to its availability and ease of manufacturing. As a result, it is a cost-effective solution for those seeking a budget-friendly approach to fuel line installation.
However, while rubber is initially cheaper, it may not always be the most cost-effective choice in the long run. Rubber fuel lines have a tendency to degrade over time, especially when exposed to certain chemicals in fuel or when subjected to high temperatures. This degradation can lead to cracks, leaks, and eventually, the need for replacement. Over time, the recurring costs of replacing rubber fuel lines can accumulate, making steel a more economical choice in the long term.
Steel fuel lines, on the other hand, offer a different cost-benefit analysis. While they may have a higher upfront cost compared to rubber, steel is known for its durability and longevity. Steel lines are less susceptible to the same degradation issues as rubber, ensuring a longer lifespan. This means that, despite the higher initial investment, steel fuel lines can provide significant long-term savings by reducing the frequency of replacements and repairs.
In addition, the durability of steel fuel lines can contribute to overall cost savings. Steel is less prone to damage from fuel contaminants, extreme temperatures, and mechanical stress, ensuring a more reliable and consistent performance. This reliability can prevent potential issues and the associated costs that may arise from using less durable materials.
In summary, while rubber fuel lines offer a more affordable initial solution, steel may be the more cost-effective choice over time due to its durability and longevity. The decision should consider both short-term and long-term costs, ensuring that the chosen material aligns with the specific requirements and conditions of the fuel line application.
Perfect Fuel Line Size for 7kW Onan Generator
You may want to see also
Installation: Rubber lines are easier to install, while steel requires more specialized tools and expertise
When it comes to choosing between rubber fuel lines and steel fuel lines, the installation process is a significant factor to consider. Rubber fuel lines are generally more user-friendly and can be installed with relative ease, making them a popular choice for DIY enthusiasts and those with limited mechanical experience. The flexibility of rubber allows for easier maneuvering around engine components, and its natural resilience reduces the risk of damage during installation. This material is also less prone to kinking, which can be a common issue with rigid steel lines.
In contrast, installing steel fuel lines requires a higher level of skill and specialized tools. Steel is a rigid material, and its installation demands precise measurements and careful handling to avoid damage to the engine. The process often involves cutting and bending the lines, which can be challenging without the right equipment and experience. Additionally, steel lines may require the use of specialized connectors and fittings to ensure a secure and leak-free connection.
For those with limited mechanical knowledge or access to the necessary tools, rubber fuel lines offer a more accessible and straightforward installation process. They are less likely to cause damage during installation and can be easily routed around engine components. This ease of installation is particularly beneficial for retrofitting or modifying existing fuel systems, where the original setup may not be easily accessible or compatible with new lines.
On the other hand, steel fuel lines are typically reserved for high-performance applications or situations where durability and strength are paramount. The installation of steel lines often requires a more methodical approach, ensuring that the lines are properly secured and protected from potential engine vibrations. While steel may be more challenging to install, it offers superior resistance to fuel leaks and can withstand extreme conditions, making it an excellent choice for racing or heavy-duty vehicles.
In summary, the installation process plays a crucial role in determining the suitability of rubber or steel fuel lines. Rubber lines provide a simpler and more accessible installation, making them ideal for general use and DIY projects. Steel lines, while more demanding to install, offer enhanced durability and are preferred for high-performance or demanding applications. Understanding the installation requirements of each material is essential to ensure a successful and safe fuel system setup.
Understanding Rag Fuel Lines: A Comprehensive Guide
You may want to see also
Frequently asked questions
Rubber fuel lines are ideal for applications where flexibility and resistance to fuel-related chemicals are crucial. They are commonly used in fuel systems of cars, motorcycles, and small engines due to their ability to absorb vibrations and bend without kinking.
Steel fuel lines offer excellent strength and durability, making them suitable for high-pressure applications. They are less susceptible to damage from fuel-related chemicals and provide a more rigid structure, which can be beneficial in certain automotive setups.
Rubber fuel lines are preferred when the fuel system requires flexibility, such as in classic cars, racing applications, or where the fuel lines need to navigate tight spaces. They are also commonly used in marine environments due to their resistance to saltwater corrosion.
Rubber can be more susceptible to cracking and degradation over time, especially when exposed to certain fuels or extreme temperatures. It may also require more frequent inspections and maintenance to ensure its integrity.
Steel fuel lines are often chosen for high-performance applications, racing cars, or heavy-duty machinery where the fuel system operates under extreme conditions. They are also suitable for applications where flexibility is not a primary concern, and a rigid structure is desired.