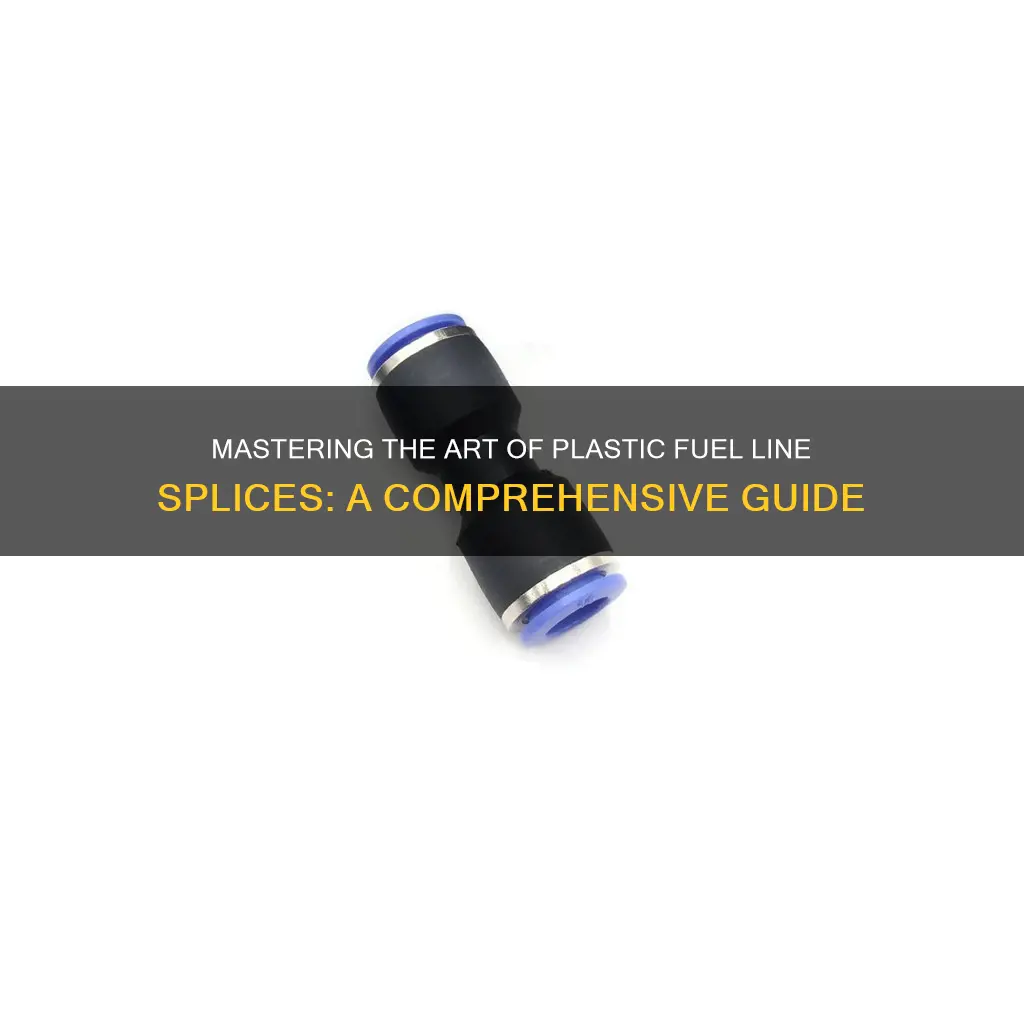
Splicing a plastic fuel line is a task that requires careful attention to detail and the right tools to ensure a secure and leak-free connection. This process involves joining two sections of plastic tubing together to create a continuous fuel line. It's important to prepare the ends of the lines by cleaning and deburring them to remove any debris or sharp edges. Then, you'll need to use a specialized adhesive or heat shrink sleeve to bond the lines together, ensuring a tight seal. Proper alignment and clamping are crucial to prevent any air bubbles or misalignment, which could lead to fuel leaks. With the right techniques and materials, you can effectively splice a plastic fuel line, ensuring the safety and efficiency of your vehicle's fuel system.
What You'll Learn
- Prepare Tools: Gather necessary tools: fuel line cutter, solvent cleaner, and heat shrink sleeves
- Clean Line: Remove dirt and debris from the fuel line using a solvent cleaner
- Cut and Prepare: Measure and cut the fuel line, ensuring a precise length
- Prepare Fittings: Clean and prepare the fittings for the new splice
- Solder and Test: Use a soldering iron to join the lines, then test for leaks
Prepare Tools: Gather necessary tools: fuel line cutter, solvent cleaner, and heat shrink sleeves
Before you begin the splicing process, it's crucial to gather the right tools to ensure a successful and secure repair. Here's a detailed guide on preparing the necessary equipment:
Fuel Line Cutter: This specialized tool is designed to cut through plastic fuel lines with precision. Look for a cutter that can handle the specific diameter of your fuel line. Having a sharp and accurate cutter is essential to make a clean cut, which will prevent any potential leaks or damage during the splicing process. Consider a manual or automatic cutter, depending on your preference and the complexity of the job.
Solvent Cleaner: Cleaning the fuel line is an often-overlooked but critical step. A solvent cleaner will help remove any dirt, debris, or old adhesive residue from the fuel line. Choose a cleaner specifically formulated for plastic to ensure it doesn't damage the material. Apply the cleaner generously to the area where the splice will take place, following the manufacturer's instructions for optimal results.
Heat Shrink Sleeves: These sleeves are an integral part of the splicing process, providing a protective barrier and ensuring a tight seal. Select heat shrink sleeves that are compatible with the diameter of your fuel line. The sleeves should be long enough to cover the entire splice area, providing a secure fit. Heat shrink technology offers a reliable and long-lasting solution for repairing fuel lines.
By gathering these tools, you'll be well-prepared to tackle the splicing of a plastic fuel line. Each item plays a specific role in ensuring a successful repair, so having them readily available is essential for a job well done. Remember, proper preparation leads to a more efficient and effective repair process.
Understanding Military-Grade Fuel Lines: Style, Durability, and Performance
You may want to see also
Clean Line: Remove dirt and debris from the fuel line using a solvent cleaner
To ensure a clean and functional fuel line, it's crucial to remove any dirt and debris that may have accumulated over time. This process is an essential step before attempting to splice a plastic fuel line, as it ensures optimal performance and longevity of the new connection. Here's a detailed guide on how to effectively clean the fuel line using a solvent cleaner:
Step 1: Prepare the Necessary Materials
Gather the required tools and materials before beginning the cleaning process. You will need a suitable solvent cleaner specifically designed for plastic fuel lines. These cleaners are typically available at automotive supply stores or online. Additionally, have a small brush or cleaning tool to scrub the interior of the fuel line and a container to hold the solvent cleaner.
Step 2: Locate the Fuel Line
Identify the fuel line that needs cleaning. It is usually a flexible tube connected to the fuel tank and running along the frame or under the vehicle. Ensure you have access to the entire length of the fuel line, as cleaning will be done from one end.
Step 3: Drain the Fuel Line (Optional but Recommended)
For optimal cleaning, it is advisable to drain the fuel line of any remaining fuel. This step ensures that you are cleaning the entire line, including the point where the fuel line connects to the engine. You can do this by disconnecting the fuel line from the engine and placing a container under it to catch any fuel that drips out. Allow the fuel to drain completely before proceeding.
Step 4: Apply the Solvent Cleaner
Pour a small amount of the solvent cleaner into the container. Follow the instructions on the cleaner's packaging to determine the appropriate amount. Carefully pour or squirt the cleaner into the fuel line, starting from the end closest to the fuel tank. Ensure an even distribution of the cleaner throughout the line.
Step 5: Scrub and Clean
Using the small brush or cleaning tool, gently scrub the interior of the fuel line to ensure the cleaner reaches all areas. Pay attention to any bends or kinks in the line, as these areas may accumulate more dirt and debris. Work the cleaner into the fuel line's surface to loosen and remove any built-up contaminants.
Step 6: Allow the Cleaner to Work
Let the solvent cleaner sit in the fuel line for the recommended time, which is typically specified on the cleaner's packaging. This allows the cleaner to penetrate and dissolve any stubborn deposits.
Step 7: Rinse and Dry
After the specified time has passed, rinse the fuel line with clean water to remove any remaining cleaner. Ensure that no traces of the solvent are left behind. Once rinsed, allow the fuel line to air dry completely before reinstalling it or proceeding with the splicing process.
By following these steps, you can effectively clean the fuel line, ensuring a smooth and debris-free connection when splicing the plastic fuel line. This preparation step is vital to guarantee the success and reliability of your fuel line repair or modification.
Unraveling the Mystery: Lines Attached to the Fuel Pump
You may want to see also
Cut and Prepare: Measure and cut the fuel line, ensuring a precise length
Before you begin the splicing process, it's crucial to measure and cut the fuel line with precision. This step ensures a seamless fit and prevents any potential leaks or damage. Here's a detailed guide on how to measure and cut the fuel line accurately:
Measuring the Fuel Line:
Start by identifying the length of the fuel line you need to splice. Carefully inspect the damaged section and measure it accurately. Use a flexible measuring tape or a ruler to get the exact length. Take note of the measurement in inches or centimeters, whichever is appropriate for your fuel line. It's essential to be precise here, as even a slight discrepancy can affect the overall fit and performance of the splice.
Cutting the Fuel Line:
Once you have the measurement, it's time to cut the fuel line. You can use a sharp utility knife or a specialized fuel line cutter for this task. Place the fuel line on a flat surface and align the measurement mark with the cutting edge of your tool. Apply steady pressure and make a clean cut. Ensure that the cut is straight and smooth to avoid any rough edges that could compromise the splice's integrity. If you're using a fuel line cutter, follow the manufacturer's instructions to ensure a precise cut.
Consider the following tips for a successful cut:
- Always cut slightly longer than needed, as you can trim the excess later if required.
- Take your time and be patient. A precise cut is essential to prevent any potential issues during the splicing process.
- If you're using a knife, ensure it is sharp to make a clean cut without damaging the fuel line material.
By carefully measuring and cutting the fuel line, you set the foundation for a successful splice. This attention to detail will contribute to a secure and leak-free connection, ensuring the reliability of your fuel system.
Optimal Fuel Line Size for 5-Horse Tecumseh Engine
You may want to see also
Prepare Fittings: Clean and prepare the fittings for the new splice
Before you begin the splicing process, it's crucial to ensure that the fittings are in optimal condition. Start by thoroughly cleaning the fittings to remove any dirt, debris, or old fuel residue. Use a mild detergent or a specialized cleaner designed for fuel lines to ensure a clean and safe environment for the splice. Rinse the fittings with clean water to eliminate any remaining cleaning agents. This step is essential to prevent contamination and ensure a secure connection.
Next, inspect the fittings for any signs of damage or wear. Look for cracks, brittleness, or any other defects that might compromise the integrity of the splice. If you notice any issues, it's best to replace the fittings to ensure a reliable and long-lasting repair. Smooth any rough surfaces on the fittings using a fine-grit sandpaper or a similar abrasive tool. This preparation ensures a better bond between the new splice and the existing fitting.
Additionally, consider applying a suitable lubricant to the fittings, especially if they are made of a harder plastic. A small amount of lubricant can make the fitting more pliable and easier to work with during the splicing process. However, be cautious not to use too much, as excess lubricant can lead to issues with the splice's strength. The goal is to create a clean, smooth, and well-prepared surface for the new splice.
Remember, taking the time to properly clean and prepare the fittings will significantly contribute to the success and longevity of the splice. It ensures a strong bond and reduces the risk of future issues. This attention to detail is a key aspect of mastering the art of splicing plastic fuel lines.
Mastering the Art of Fuel Line Clip Removal: A Step-by-Step Guide
You may want to see also
Solder and Test: Use a soldering iron to join the lines, then test for leaks
Splicing a plastic fuel line is a precise process that requires careful preparation and the right tools. Once you've gathered the necessary supplies and prepared the line, it's time to move on to the soldering step. This method ensures a strong and leak-free connection, which is crucial for maintaining the integrity of your fuel system.
Using a soldering iron is an effective way to join plastic fuel lines. Start by cleaning the surfaces of both the original line and the new section you're splicing in. Ensure there is no debris or contaminants that could interfere with the soldering process. Then, apply a small amount of flux to the inside of the line where the splice will occur. Flux helps to create a bond and ensures a clean connection. Allow the flux to dry slightly before proceeding.
Next, carefully cut the new section of the fuel line to the appropriate length, ensuring it matches the diameter of the original line. Use a sharp, clean knife or a specialized cutting tool designed for plastic fuel lines. Once the new section is cut, heat the soldering iron to the appropriate temperature for the type of solder you're using. Apply the solder to the heated tip of the iron, then quickly but carefully insert the new line into the original line, ensuring the solder melts and creates a strong bond. Hold the connection in place for a few seconds to allow the solder to cool and solidify.
After soldering, it's crucial to test the connection for any leaks. Turn on the fuel supply and observe for any signs of fuel escaping around the splice. You can use a soapy water solution to make the test more visible. If there are no leaks, your splice is successful. However, if any fuel is detected, carefully inspect the connection and re-solder if necessary, ensuring all steps are followed meticulously.
Remember, practicing this skill is essential to becoming proficient in splicing plastic fuel lines. Take your time, be patient, and always prioritize safety when working with fuel systems. With practice, you'll be able to create secure and reliable connections that will stand the test of time.
The Ultimate Guide to Choosing the Right Hose Clamp for Your 3/8" Outboard Fuel Line
You may want to see also
Frequently asked questions
To splice a plastic fuel line, you will need a few essential tools. Firstly, a pair of sharp scissors or a utility knife is crucial for cutting the line. Additionally, a heat source such as a heat gun or a hairdryer can be used to soften the plastic and create a secure bond. You might also consider using a plastic welder or a specialized adhesive designed for plastic fuel lines to ensure a strong and durable connection.
Proper preparation is key to a successful splice. Start by cleaning the ends of the fuel line to remove any dirt, debris, or old adhesive. You can use a cloth or a brush to wipe the surfaces. Then, cut the line at a 45-degree angle to create a smooth and precise edge. This step ensures better adhesion and a stronger bond when you join the two pieces together.
One common and effective method is the heat shrink technique. Begin by heating the ends of the fuel line until they become soft and pliable. Then, carefully align the two pieces and apply a layer of adhesive or a small amount of plastic welder along the length of the splice. Once the adhesive is set, use heat shrink tubing to cover the splice, ensuring a tight and secure fit. This method provides a reliable and long-lasting connection for your fuel line.