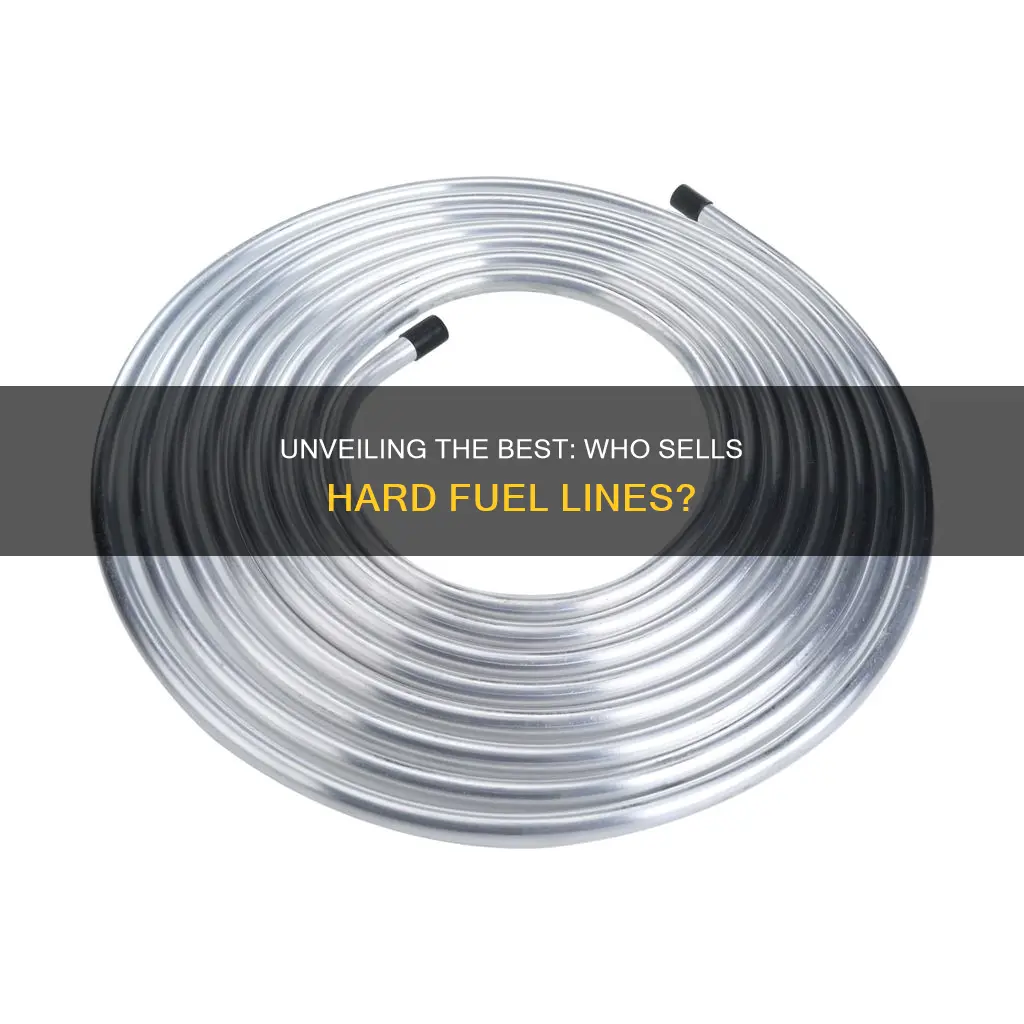
Sales of hard fuel lines, a critical component in the transportation and storage of fuels, are an essential aspect of the energy industry. These lines are designed to withstand high-pressure environments and are used to transport fuels over long distances, ensuring a reliable supply for various applications. The market for hard fuel lines is diverse, catering to industries such as aviation, marine, and land transportation. This introduction sets the stage for exploring the companies and suppliers that specialize in the sales and distribution of these specialized fuel lines, highlighting their importance in maintaining efficient and safe fuel management systems.
What You'll Learn
- Fuel Line Material: Different materials for fuel lines, such as rubber, plastic, or metal, offer varying durability and flexibility
- Fuel Line Sizes: Standardized fuel line sizes ensure compatibility with engines and fuel systems, preventing leaks and performance issues
- Fuel Line Routing: Proper routing techniques minimize stress and potential damage to fuel lines, enhancing engine performance and longevity
- Fuel Line Connections: Secure and leak-proof connections are crucial for maintaining fuel system integrity and preventing fuel leaks
- Fuel Line Maintenance: Regular inspection and cleaning of fuel lines prevent contamination and ensure optimal engine performance
Fuel Line Material: Different materials for fuel lines, such as rubber, plastic, or metal, offer varying durability and flexibility
When it comes to fuel lines, the choice of material is crucial as it directly impacts the performance and longevity of the system. Different materials offer unique advantages and are suited to specific applications. Here's an overview of the common materials used for fuel lines and their characteristics:
Rubber: Rubber fuel lines are a popular choice due to their flexibility and resilience. This material is ideal for applications where the fuel line needs to accommodate slight movements and vibrations. Rubber is known for its ability to absorb shocks and vibrations, making it less prone to damage from engine vibrations. It is also resistant to most fuels and oils, ensuring that the fuel line remains intact over time. However, rubber may not be the best option for high-temperature environments as it can become brittle and crack over extended periods.
Plastic: Plastic fuel lines are lightweight and offer excellent chemical resistance. They are often used in modern vehicles due to their ability to resist corrosion and provide a long-lasting solution. Plastic lines are flexible and can bend around tight spaces, making installation easier. This material is also less susceptible to damage from fuel leaks, as it doesn't absorb fuel as readily as rubber. However, plastic may not be as durable as other materials and can become brittle with age, especially in low-temperature conditions.
Metal: Metal fuel lines, typically made from stainless steel, are known for their exceptional strength and durability. These lines are rigid and provide excellent resistance to high temperatures and pressure. Metal is an excellent choice for high-performance vehicles or applications where the fuel line is subjected to extreme conditions. It offers a long-lasting solution and is less prone to degradation over time. However, metal lines are less flexible and may require more effort during installation, especially in confined spaces.
The choice of material depends on the specific requirements of the fuel system, including the type of fuel, operating conditions, and the overall design of the vehicle. Each material has its advantages and trade-offs, ensuring that there is a suitable option for every fuel line application. Understanding these differences is essential for ensuring the optimal performance and longevity of the fuel system.
The Ultimate Guide to Choosing the Right Hose Clamp for Your 3/8" Outboard Fuel Line
You may want to see also
Fuel Line Sizes: Standardized fuel line sizes ensure compatibility with engines and fuel systems, preventing leaks and performance issues
When it comes to fuel lines, standardized sizes are crucial for ensuring optimal performance and compatibility with various engines and fuel systems. These standardized dimensions play a vital role in preventing leaks, which can lead to costly repairs and potential safety hazards. By adhering to these specifications, you can ensure that the fuel lines are the correct length, diameter, and material for the specific application, resulting in a reliable and efficient fuel delivery system.
The importance of standardized fuel line sizes cannot be overstated. Engines and fuel systems are designed with specific requirements in mind, and using the wrong size can lead to a multitude of problems. For instance, a fuel line that is too small may restrict fuel flow, causing reduced engine performance and potential stalling. Conversely, a line that is too large might lead to excessive fuel pressure, which can cause engine damage over time. Therefore, it is essential to choose the appropriate size based on the engine's power output and the fuel system's design.
Standardization in fuel line sizes is achieved through various industry standards and regulations. These standards ensure that manufacturers and retailers provide consistent and reliable products. Common standards include those set by the Society of Automotive Engineers (SAE) and the International Organization for Standardization (ISO). These organizations establish guidelines for fuel line dimensions, materials, and testing procedures, ensuring that the lines meet specific quality and performance criteria.
When selecting fuel lines, it is imperative to consider the engine's specifications and the fuel system's requirements. Engine manuals and fuel system diagrams often provide detailed information on the recommended fuel line sizes. These specifications are typically based on extensive research and testing to ensure optimal performance and longevity. By matching the fuel line sizes to these recommendations, you can guarantee a seamless integration with the engine and fuel system.
In summary, standardized fuel line sizes are essential for maintaining the integrity of fuel systems and ensuring engines operate at their peak performance. By adhering to industry standards and considering the specific requirements of the engine and fuel system, you can prevent leaks, improve efficiency, and extend the lifespan of your vehicle's fuel delivery system. Always consult the manufacturer's guidelines and seek professional advice when selecting fuel lines to ensure a safe and reliable installation.
2000 Grand Prix GTP Fuel Line Size: Essential Guide
You may want to see also
Fuel Line Routing: Proper routing techniques minimize stress and potential damage to fuel lines, enhancing engine performance and longevity
When it comes to fuel line routing, proper techniques are essential to ensure optimal engine performance and longevity. Fuel lines are critical components that deliver fuel from the tank to the engine, and any damage or stress to these lines can lead to reduced engine efficiency and potential breakdowns. Here's an in-depth guide on how to route fuel lines effectively:
Understanding the Layout: Begin by thoroughly understanding the engine bay layout and the available space. Identify the locations of the fuel tank, fuel pump, and engine block. Visualize the path that the fuel lines must take to reach the engine, considering the natural flow of the fuel system. Proper planning at this stage is crucial to avoid any unnecessary complications during the installation process.
Minimizing Stress and Movement: The primary goal of fuel line routing is to minimize stress and movement on the lines. Excessive bending or twisting can lead to cracks, leaks, and reduced fuel pressure. Here are some techniques to achieve this:
- Keep the lines as straight as possible, especially when running along the engine's length. Avoid sharp bends and kinks by using straight runs and gentle curves.
- Utilize fuel line brackets or ties to secure the lines in place. These brackets should be positioned to distribute the line's weight evenly, preventing unnecessary strain.
- Route the lines away from high-temperature areas, such as the exhaust manifold or engine components that generate heat. Heat can cause fuel lines to degrade over time.
- Ensure that the lines are not pinched or compressed against other components, as this can restrict fuel flow and cause damage.
Using the Right Materials: Different types of fuel lines are available, each with unique characteristics. Choose the appropriate material based on the engine's requirements and operating conditions:
- For high-pressure applications, consider using braided fuel lines, which offer excellent flexibility and resistance to kinking.
- Rubber fuel lines are cost-effective and suitable for most applications, providing good flexibility and durability.
- For extreme conditions or high-performance engines, silicone or fluoropolymer fuel lines are ideal, as they can withstand extreme temperatures and fuel types.
Securing Connections: Properly securing fuel line connections is vital to prevent leaks and ensure a tight fit. Use fuel line connectors that are designed for the specific fuel line material. Tighten connections securely but avoid over-tightening, as this can damage the lines. Regularly inspect connections for any signs of wear or damage, especially after engine hours or during routine maintenance.
Regular Maintenance and Inspection: Fuel line routing is not a one-time task; it requires regular maintenance and inspection. Over time, fuel lines can degrade due to fuel contamination, heat, or mechanical stress. Implement the following practices:
- Check for any signs of damage, such as cracks, brittleness, or corrosion, during routine engine inspections.
- Inspect fuel lines for any leaks, especially at connections and bends.
- Consider using a fuel line cleaner to remove any contaminants and ensure optimal performance.
By following these proper routing techniques, you can significantly reduce the stress and potential damage to fuel lines, resulting in improved engine performance, increased fuel efficiency, and a longer lifespan for your vehicle's fuel system. Remember, proper maintenance and regular inspections are key to keeping your engine running smoothly.
Nylon Fuel Line: Safe Usage Guide for Your Vehicle
You may want to see also
Fuel Line Connections: Secure and leak-proof connections are crucial for maintaining fuel system integrity and preventing fuel leaks
Fuel line connections are a critical component of any fuel system, ensuring the safe and efficient delivery of fuel from the tank to the engine. These connections must be secure and leak-proof to maintain the integrity of the fuel system and prevent any potential hazards. Here's a detailed guide on why and how to achieve this:
The Importance of Secure Connections:
When fuel lines are connected, they form a path for the fuel to travel under pressure. Any loose or improper connections can lead to several issues. Firstly, it can cause fuel leaks, which are not only dangerous but also environmentally harmful. Fuel contains volatile compounds that can ignite easily, posing a fire hazard. Secondly, a poor connection can result in fuel loss, reducing engine performance and potentially causing it to stall. Therefore, ensuring a tight and secure fit is essential.
Materials and Design Considerations:
Fuel line connections should be made using materials that are compatible with the fuel type and resistant to corrosion and degradation. Common materials include stainless steel, brass, and high-density polyethylene (HDPE). The design of the connection should also be leak-proof, often featuring a compression or crimp style. Compression fittings use a ferrule that compresses around the fuel line, creating a tight seal. Crimp connections involve bending the fuel line to create a secure hold.
Step-by-Step Connection Process:
- Prepare the fuel line by cleaning it and ensuring it is free of any debris or contaminants.
- Measure and cut the fuel line to the appropriate length, allowing for a small overlap at the connection point.
- Apply a suitable fuel line compound or tape to the ends of the line to provide insulation and prevent leaks.
- For compression fittings, insert the fuel line into the fitting and tighten the nut securely, ensuring the ferrule is compressed evenly.
- In the case of crimp connections, carefully crimp the fuel line using specialized tools to create a secure hold.
- After making the connection, check for any signs of leakage by applying a small amount of fuel and observing for any seepage.
Regular Maintenance and Inspection:
Even the most secure connections require regular maintenance. Inspect fuel lines and connections periodically for any signs of damage, corrosion, or wear. Look for cracks, brittleness, or any signs of fuel leakage. If any issues are found, replace the affected sections promptly. Additionally, ensure that all connections are tight and secure, especially after any repairs or modifications to the fuel system.
By following these guidelines, you can ensure that fuel line connections are secure, leak-proof, and capable of withstanding the demands of the fuel system. This approach helps maintain the overall integrity of the vehicle's fuel system, ensuring optimal performance and safety.
Perfect Fuel Line Size for Suzuki DT 140
You may want to see also
Fuel Line Maintenance: Regular inspection and cleaning of fuel lines prevent contamination and ensure optimal engine performance
Fuel line maintenance is a critical aspect of vehicle care that often gets overlooked, but it plays a vital role in ensuring your engine operates at its best. Regular inspection and cleaning of the fuel lines are essential practices that can prevent contamination and maintain optimal engine performance. Over time, fuel lines can accumulate dirt, debris, moisture, and even microbial growth, which can lead to a range of issues.
The primary purpose of fuel lines is to transport gasoline or diesel from the fuel tank to the engine. When these lines become contaminated, it can result in reduced engine efficiency, poor fuel economy, and even engine misfires. Contaminants can cause blockages, leading to restricted fuel flow, which in turn affects the engine's ability to start and run smoothly. This is especially crucial for vehicles that rely on precise fuel injection systems, where even a small amount of contamination can have significant consequences.
To maintain your fuel lines, a regular inspection routine is recommended. Start by visually checking the lines for any signs of damage, cracks, or leaks. Look for discolored or cloudy fuel, which may indicate the presence of water or microbial growth. Pay attention to any unusual noises or vibrations while the engine is running, as these could be signs of restricted fuel flow. It's also a good practice to inspect the fuel tank for any signs of corrosion or leaks.
Cleaning the fuel lines is the next crucial step. This process involves removing contaminants and ensuring the lines are free from debris. One effective method is to use a fuel line cleaner, which can be purchased from automotive stores. These cleaners are designed to dissolve and remove built-up deposits and moisture. You can also use compressed air to blow out any loose debris. For more stubborn issues, a fuel line flush may be necessary, which involves running a cleaner through the entire fuel system.
In addition to cleaning, it's essential to address any underlying issues. If you notice any signs of contamination or damage, it's best to consult a professional mechanic. They can perform a thorough inspection and recommend appropriate repairs or replacements. Regular maintenance ensures that your fuel lines remain in good condition, providing clean, contaminant-free fuel to the engine, thus optimizing performance and longevity.
Understanding 3/8 Fuel Line Dimensions: Inside Diameter Explained
You may want to see also
Frequently asked questions
The primary manufacturers of hard fuel lines include companies like Hardline Systems, Hardline International, and various specialized automotive parts suppliers. These companies produce high-pressure fuel lines designed for heavy-duty applications and high-performance vehicles.
Yes, purchasing hard fuel lines typically requires considering factors such as vehicle compatibility, fuel type (e.g., diesel, gasoline), pressure ratings, and the specific make and model of the vehicle. It's essential to consult the vehicle's manual or seek professional advice to ensure the correct specifications are met.
While some basic fuel line installation tasks can be tackled by DIY enthusiasts, replacing hard fuel lines, especially in heavy-duty applications, often requires specialized knowledge and tools. It is recommended to have professional experience or consult a qualified mechanic to ensure proper installation and avoid potential hazards.
Hard fuel lines may need replacement due to various reasons, including wear and tear, damage from accidents or corrosion, leaks, or the need for an upgrade to meet higher performance requirements. Regular maintenance and inspections can help identify potential issues early on.
To ensure quality and authenticity, it is advisable to purchase fuel lines from reputable manufacturers or authorized dealers. Look for certifications, warranties, and reviews from previous customers. Checking for any signs of tampering or counterfeiting is also essential, especially when buying online.