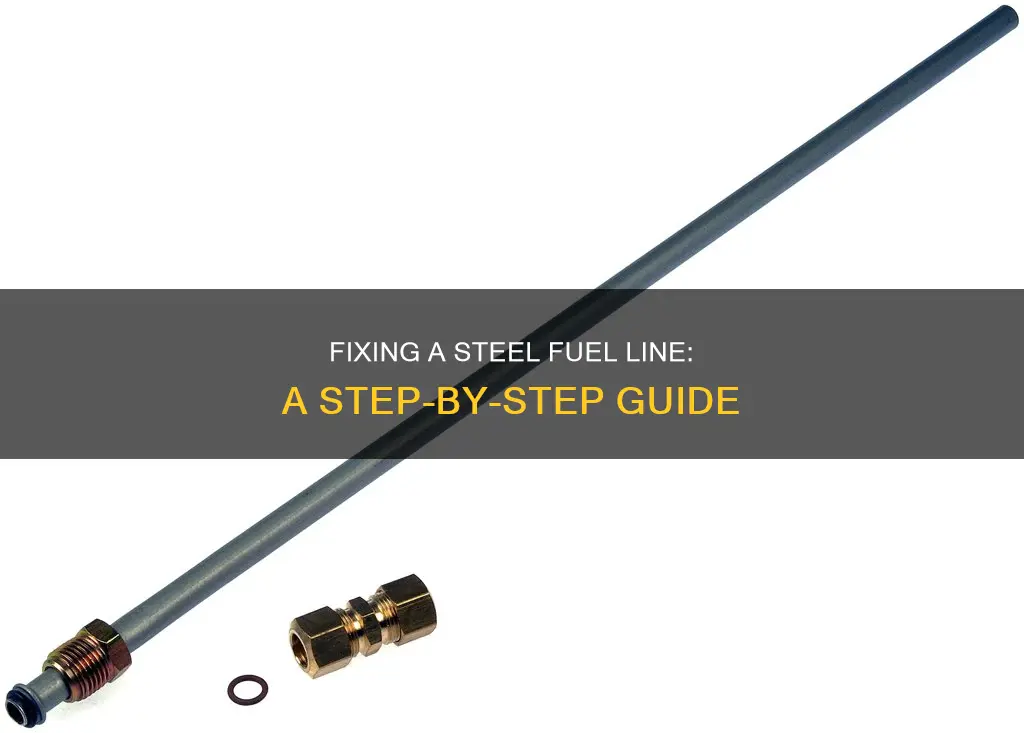
Repairing a steel fuel line is a crucial task for vehicle owners, as it ensures the safe and efficient operation of their engines. This process requires careful consideration of the specific steps to be taken, as steel fuel lines can be prone to damage from corrosion, punctures, or leaks. In this guide, we will explore the essential methods and tools needed to effectively fix a steel fuel line, covering everything from identifying the issue to ensuring a secure and long-lasting repair. By following these instructions, you can restore the integrity of your fuel system and maintain the performance of your vehicle.
What You'll Learn
- Identify the Issue: Inspect for cracks, corrosion, or damage
- Prepare the Line: Clean and deburr the damaged area
- Choose the Right Material: Select compatible steel or stainless steel
- Weld or Bond: Use proper welding techniques or adhesives for a strong bond
- Test and Inspect: Ensure the repair is leak-free and secure
Identify the Issue: Inspect for cracks, corrosion, or damage
When it comes to repairing a steel fuel line, the first step is to thoroughly inspect the line for any signs of damage or deterioration. This initial assessment is crucial to ensure you understand the extent of the problem and can proceed with the appropriate repairs. Start by visually examining the fuel line for any visible cracks, especially in areas where the line is most susceptible to wear and tear, such as bends, fittings, and connections. Look for any signs of corrosion, which can manifest as a white or reddish-brown powder-like substance on the surface of the steel. Corrosion is a common issue with fuel lines, especially in older vehicles or those exposed to harsh environmental conditions.
Pay close attention to the connections and fittings of the fuel line. Over time, these components can become loose or damaged, leading to fuel leaks. Check for any signs of damage, such as bends or kinks in the line, which could indicate a previous repair attempt or general wear. It's also important to inspect the fuel line for any signs of rust or oxidation, especially if the line has been exposed to moisture or fuel contaminants. Rust can weaken the structural integrity of the steel, making it more prone to cracks and leaks.
If you notice any cracks or corrosion, measure their length and width to determine the severity of the damage. Small cracks or minor corrosion may not require immediate repair but should be monitored. However, if the damage is significant, it's essential to address it promptly to prevent further deterioration and potential fuel leaks. Keep in mind that fuel lines are under constant pressure, so any damage can lead to hazardous situations if left unattended.
During your inspection, also check for any signs of fuel contamination, such as discoloration or a sweet odor, which could indicate the presence of water or other contaminants. Contaminated fuel can cause engine issues and further damage the fuel line. If you suspect contamination, it's best to consult a professional mechanic for advice on how to proceed.
Remember, a thorough inspection is key to identifying the issue and determining the necessary repairs. If you're unsure about any aspect of the inspection, it's always a good idea to seek professional assistance to ensure the job is done safely and effectively.
Choosing the Right Fuel Line Hose for Your 1969 Ford F100
You may want to see also
Prepare the Line: Clean and deburr the damaged area
Before you begin the repair process, it's crucial to ensure that the damaged area of the steel fuel line is thoroughly prepared. This initial step is essential to guarantee a successful and long-lasting fix. Here's a detailed guide on how to clean and deburr the affected section:
Cleaning the Damaged Area:
Start by thoroughly cleaning the damaged portion of the fuel line. Over time, fuel lines can accumulate dirt, rust, and debris, which can interfere with the repair process. Use a suitable cleaning agent, such as a fuel line cleaner or a mild detergent, and apply it directly to the affected area. Allow the cleaner to sit for a few minutes to loosen and dissolve any contaminants. Then, use a soft-bristled brush or a cleaning tool specifically designed for fuel lines to scrub the area gently. Ensure you remove all visible dirt and grime to create a clean surface for the repair.
Rinsing and Drying:
After cleaning, rinse the area thoroughly with clean water to remove any remaining cleaning agents. Make sure to flush out the entire length of the fuel line to ensure no residue is left behind. Once rinsed, allow the line to air dry completely. You can speed up the drying process by using a hairdryer on a low setting, ensuring it is held a safe distance from the line to avoid overheating. A completely dry fuel line is essential to prevent any further contamination during the deburring process.
Deburring Technique:
Deburring is a critical step to ensure a smooth and even surface for the repair. Use a fine-grit sandpaper or a deburring tool specifically designed for metal surfaces. Gently rub the sandpaper along the damaged area, following the direction of the metal's grain. The goal is to remove any sharp edges or burrs that could potentially cause further damage or interfere with the repair. Take your time and be meticulous in this step to achieve a clean and smooth finish.
Safety Precautions:
When cleaning and deburring, always wear appropriate personal protective equipment (PPE), such as gloves and safety goggles, to protect yourself from any potential hazards. Ensure you work in a well-ventilated area, especially when using cleaning agents or sandpaper, to avoid inhaling fumes or dust. Additionally, be cautious not to damage any surrounding components or create new imperfections during this process.
By following these steps, you'll create a prepared and refined surface for the subsequent repair work, ensuring a robust and reliable fix for your steel fuel line.
Duramax Fuel Line Diameter: 2003 Specs Revealed
You may want to see also
Choose the Right Material: Select compatible steel or stainless steel
When repairing a steel fuel line, choosing the right material is crucial to ensure the longevity and reliability of the fix. The primary goal is to select a material that is compatible with the existing fuel line and can withstand the corrosive effects of fuel over time. The two main options are steel and stainless steel, each with its own advantages and considerations.
Steel is a common choice for fuel lines due to its affordability and availability. However, it is important to choose the right type of steel. Regular carbon steel is not suitable for fuel lines as it is susceptible to corrosion and can degrade over time. Instead, opt for a steel alloy specifically designed for fuel line applications. These alloys often include a higher percentage of chromium, which provides excellent resistance to corrosion and oxidation. Look for specifications like ASTM A283 or ASTM A53, which indicate the steel's suitability for fuel line repairs.
Stainless steel is another excellent option for fuel line repairs, especially in environments with higher fuel temperatures or exposure to harsh chemicals. This material offers superior corrosion resistance compared to regular steel, making it ideal for long-term use. The most common type of stainless steel used in fuel lines is 304 stainless steel, known for its excellent mechanical properties and resistance to fuel degradation. It is important to ensure that the stainless steel used is of the appropriate grade and thickness to match the original fuel line for a secure and reliable repair.
When selecting the material, consider the specific conditions of your fuel line. If the line is exposed to high temperatures or contains fuels with corrosive properties, stainless steel might be the better choice. However, if cost is a significant factor and the fuel line is not subjected to extreme conditions, a properly chosen steel alloy can provide a viable and cost-effective solution.
In summary, the key to a successful fuel line repair is to choose the right material. Whether it's the corrosion-resistant stainless steel or a carefully selected steel alloy, the goal is to ensure compatibility and durability. Always refer to manufacturer guidelines and consult experts if needed to make an informed decision and ensure the safety and efficiency of your fuel system.
Cummins Fuel Injection Lines: Unraveling the Mystery of Uniform Lengths
You may want to see also
Weld or Bond: Use proper welding techniques or adhesives for a strong bond
When repairing a steel fuel line, the choice between welding and bonding depends on the specific circumstances and the condition of the line. Both methods can effectively address the issue, but each has its own set of advantages and considerations. Here's a detailed guide on how to approach welding and bonding for a strong and durable repair:
Welding:
Welding is a powerful method for repairing steel fuel lines, especially when dealing with significant damage or when a seamless connection is required. Here's a step-by-step process:
- Prepare the Materials: Ensure you have the necessary welding equipment, including a suitable welding rod for steel. Clean the fuel line section to be repaired, removing any dirt, rust, or debris.
- Positioning: Position the damaged section so that the surfaces to be joined are flush and aligned. This might involve clamping or using temporary supports to hold the parts in place.
- Welding Technique: Use a suitable welding technique for steel, such as gas welding or arc welding. Apply the welding rod in small, controlled passes, ensuring each pass overlaps the previous one to create a strong bond. Maintain a consistent heat input and a steady welding speed.
- Cooling and Inspection: Allow the welded joint to cool slowly. Inspect the weld for any defects like porosity, cracks, or insufficient fusion. If any issues are found, consider grinding and re-welding the affected area.
- Testing: After welding, test the fuel line for leaks and ensure the connection is secure.
Bonding (Using Adhesives):
Bonding with specialized adhesives is another viable option for repairing steel fuel lines, especially for smaller tears or punctures. Here's how to do it:
- Surface Preparation: Clean the fuel line and the adhesive application area thoroughly. Ensure the surface is free from oil, grease, and any contaminants.
- Choose the Right Adhesive: Select a high-temperature adhesive specifically designed for steel. Follow the manufacturer's instructions for the best results. Common adhesives used for metal bonding include epoxy resins and cyanoacrylate adhesives.
- Application: Apply the adhesive in a thin, even layer along the length of the tear or puncture. Ensure complete coverage and avoid air bubbles.
- Clamping and Curing: Use clamps or weights to apply pressure and ensure good contact between the adhesive and the metal. Follow the adhesive's curing time instructions, which may involve heating or specific environmental conditions.
- Testing: After curing, test the fuel line for leaks and ensure the bond is strong enough to handle the pressure and temperature of the fuel system.
Remember, when dealing with fuel lines, safety is paramount. Always work in a well-ventilated area, and consider wearing protective gear. It's crucial to follow the manufacturer's guidelines for both welding and bonding processes to ensure a successful and long-lasting repair.
VXR Pro 93 Fuel Line: Dimensions and Specifications
You may want to see also
Test and Inspect: Ensure the repair is leak-free and secure
When repairing a steel fuel line, the final step is crucial: thorough testing and inspection to ensure the repair is leak-free and secure. This process involves a series of checks to verify the integrity of the fixed line and prevent any potential issues. Here's a detailed guide on how to test and inspect the repair:
- Visual Inspection: Begin by conducting a visual inspection of the repaired area. Look for any visible signs of damage, such as cracks, bends, or corrosion. Ensure that all connections are tight and free from any debris or contaminants. Check for any residual fuel leaks around the repair site by applying a small amount of soapy water or a leak detection dye to the area. If a leak is detected, immediately address the issue and retest.
- Pressure Testing: After the visual inspection, perform a pressure test to ensure the line's integrity. Fill the fuel line with compressed air or a suitable testing fluid, ensuring it is at a pressure slightly above the normal operating pressure. Observe the line for any signs of leakage or pressure drops. Use a manometer or pressure gauge to measure and record the pressure at regular intervals. If any leaks are found, identify the source and make the necessary adjustments or re-weld the connection.
- Flow Testing: To further validate the repair, conduct a flow test. Attach a test gauge or flow meter to the fuel line and start the fuel pump. Measure the flow rate and pressure at different points along the line. Compare these readings with the original specifications to ensure they meet the required standards. If the flow rate or pressure is inconsistent, it may indicate a blockage or an issue with the repair.
- Ultrasonic Testing (Optional): For a more comprehensive inspection, consider using ultrasonic testing, especially if the fuel line is difficult to access or if there are concerns about hidden damage. This non-destructive testing method uses high-frequency sound waves to detect internal flaws or defects in the steel line. It can identify cracks, voids, or other imperfections that might not be visible during a visual inspection.
- Final Check: Once all the tests are completed and no leaks or issues are found, perform a final check to ensure everything is secure. Tighten any loose connections and double-check that all components are properly aligned. Verify that the fuel line is free from any obstructions and that the repair does not interfere with the normal operation of the fuel system.
Remember, proper testing and inspection are critical to the success of the repair. By following these steps, you can ensure that the steel fuel line is leak-free, secure, and ready for safe operation.
Powerful Engine Demands: Choosing the Right Fuel Line for 800 HP
You may want to see also
Frequently asked questions
For minor holes or punctures, you can use a steel fuel line repair kit. These kits typically include a sealing compound and a clamp. Clean the affected area, apply the compound, and then tighten the clamp to create a secure seal. This method is suitable for temporary repairs and can be used until a more permanent solution is implemented.
Steel fuel lines can develop leaks due to several factors. Over time, the lines may corrode or deteriorate due to exposure to fuel, heat, or vibration. Additionally, physical damage from accidents or impacts can lead to cracks or punctures. Regular inspections and maintenance are crucial to identify and address these issues promptly.
Replacing a damaged fuel line is a complex task and may require specialized tools and knowledge. It is generally recommended to have this work done by a professional mechanic to ensure a proper and safe installation. They will have the necessary skills to cut and install the new line, ensuring it is securely connected and free from leaks. DIY kits are available, but professional assistance is advised for optimal results.